The Impurity Removal Technology For Secondary Aluminum Smelting Process
The production process of secondary aluminum alloy can be divided into three stages: pretreatment, smelting (including refining), and ingot casting. The smelting process is to add scrap aluminum into the smelting furnace and heat it to melt into a liquid state. After slagging, temperature measurement and composition The inspection and other processes are transferred to the refining furnace, where elements such as silicon and copper are added, and the process of degassing, slag removal and refining is carried out. Harmful metal elements in the secondary aluminum melt mainly include Fe, Mg, Zn, Pb, etc. For different harmful metal elements, different removal methods need to be adopted.
1. Iron Removal Technology
Iron is a common magazine in the production of secondary aluminum, which has an extremely adverse effect on the quality and performance of aluminum and aluminum alloys. Therefore, in addition to the pretreatment of the scrap aluminum to remove iron, the inclusion of iron should be removed as much as possible during the smelting process to prevent it from being slightly dissolved in the aluminum and aluminum alloy melt. Generally, the following methods are used to remove iron inclusions.
1.1 Manganese And Iron Removal Method
Manganese can effectively form a high melting point iron-rich phase compound in the aluminum alloy solution and deposit on the bottom of the furnace to achieve the purpose of iron removal. The reactions that occur are as follows:
Al9Fe2Si2+Mn→AlSiMnFe
The amount of manganese used to remove 1kg of iron is 6.7-8.3kg, and it can transform the remaining coarse, flaky, hard and brittle Al9Fe2Si2 phase into the flaky AlSiMnFe phase, thereby weakening the harmful effects of iron. However, the method of adding manganese to remove iron will increase the manganese content of the aluminum alloy. Aluminum alloys with limited manganese content should not be used, and the cost of the method of adding manganese to remove iron is relatively high.
1.2 Adding Beryllium To Iron Removal Method
Beryllium reacts with the Al9Fe2Si2 phase in the aluminum alloy melt, thereby reducing the harmful effects of iron. The reaction is as follows: Al9Fe2Si2+Be→Al5BeFeSi
Adding 0.05%—0.1% of beryllium to aluminum and aluminum alloy melts can promote the transformation of the coarse flake Al9Fe2Si2 phase into dot-shaped Al5BeFeSi, which obviously eliminates the brittleness of aluminum alloy. However, the price of beryllium is relatively high, and beryllium vapor is toxic, harmful to the human body, and pollutes the working environment. Therefore, the method of adding beryllium to iron should be used with caution.
1.3 Settling Iron Removal Method
The sedimentation iron removal method is the comprehensive effect of a multi-element master alloy prepared with four substances of Mn, Cr, Ni and Zr, which interacts with the coarse iron-rich compound in the aluminum alloy melt to form a new multi-element iron-rich compound. The multi-element iron-rich compound gradually grows up as the temperature decreases. When it grows large enough to overcome the settlement resistance, it will settle and remove iron. When the amounts of Mn, Cr, Ni, and Zr are 2.0%, 0.8%, 1.2%, and 0.6%, respectively, the iron content in the aluminum and aluminum alloy melts treated by the sedimentation iron removal method can be reduced from 1% To 0.2%. Manganese plays a major role in removing iron in the sedimentation method. Although chromium is not as good as manganese in removing iron, it has better resistance to oxidation and burnout. The main purpose of adding nickel is to reduce the brittleness caused by manganese and chromium residues. The addition of zirconium can not only play the role of iron, but also has the role of grain refinement.
1.4 Filtration And Iron Removal Method
The filtering method of iron removal is based on the principle that the iron-rich phase impurities in the aluminum alloy melt segregate at a lower temperature and a longer holding time, and mechanical filtration is used to remove the aggregated iron-rich phase materials. The filtering iron removal method is generally carried out when the melt is poured. It can not only remove large iron-rich phase substances, but also can remove other large-sized inclusions in aluminum and aluminum alloy melts. The filtering iron removal method usually uses foam Ceramic filter plate.
1.5 Smelting Direct Iron Removal Method
The direct iron removal method by smelting has been widely used in the secondary aluminum industry due to its low cost and simple operation. The method is briefly described as follows:
- (1) Strictly control the melting temperature, use the difference between the melting points of aluminum and iron to melt aluminum, and iron and other high melting point metal impurities settle to the bottom of the furnace, thereby removing iron. The inclined rotary kiln can efficiently process various waste aluminum Smelting furnace for processing.
- (2) During smelting, the iron debris should be removed before each stirring, and the iron mixed in the aluminum slag should be taken out during the slag removal.
- (3) According to the actual conditions of the selected smelting equipment and technology, in principle, for every batch of aluminum waste smelted, the slag and iron that settle on the bottom of the furnace should be pulled out.
- (4) When a secondary aluminum enterprise uses a smelting furnace-a holding furnace for production, after each furnace is melted, the molten aluminum in the furnace is dispatched to remove the iron in a hot state.
- (5) Use rapid melting and low temperature aluminum tapping. During smelting, the recycled aluminum scrap is quickly smelted under the protection of the solvent, and the entire melting process is about 2-3 hours. When the recycled aluminum scrap is melted, the temperature of the melt at this time is about 650°C. At this temperature, the solubility of iron in aluminum and aluminum alloy melts is extremely small. At this time, the iron contained in the recycled aluminum scrap is left in the slag and is clear with the slag.
2. Magnesium Removal Technology
Magnesium is also a common impurity in the production of secondary aluminum. The following methods are usually used to remove magnesium in the waste aluminum melt.
2.1 Magnesium Removal Method By Oxidation
Magnesium removal by oxidation is based on the principle that the affinity of magnesium and oxygen is greater than that of other metals. During the smelting process, magnesium first reacts strongly with oxygen, and its oxides are insoluble in aluminum and aluminum alloy melts and float up, and then rise from aluminum and aluminum alloys. The surface of the melt is skimmed off. In order to accelerate the oxidation process of magnesium, tools can be used to stir aluminum and aluminum alloy melts. The effect of the oxidation method to remove magnesium increases with the extension of the stirring time, but this method also causes the combustion and oxidation loss of aluminum, silicon and other elements while removing magnesium, and it is generally not suitable to be used.
2.2 Magnesium Chloride Removal Method
In the removal of magnesium from secondary aluminum melt, chlorine is often used as an oxidant to react with active metals such as magnesium in the melt to form chlorides. Because magnesium has a greater affinity for chlorine than aluminum, when chlorine passes into aluminum and aluminum alloy melts, the following chemical reactions occur:
- Mg+Cl2==MgCl2
- 2Al+3Cl2==2AlCl3
- 3Mg+2AlCl3==3MgCl2+2Al
The generated magnesium chloride is dissolved in the solvent layer, and the reaction of magnesium and chlorine gas emits a large amount of heat, which heats the aluminum and aluminum alloy melt.
The magnesium removal effect of the chlorination magnesium removal method is more obvious, which can reduce the magnesium content in the aluminum and aluminum alloy melts to 0.3%—0.4%, and it is easy to operate. At the same time, it has the functions of degassing and slag removal, but chlorine is Highly toxic substances, the damage to human health and the environment is great, and the aluminum and aluminum alloy melts after the removal of magnesium by chlorine gas have coarse grains, and the mechanical properties are reduced.
2.3 Chlorine Salt Removal Of Magnesium Method
Most commonly used chloride salts for magnesium removal from secondary aluminum melts are aluminum chloride. This method uses a certain pressure of nitrogen to spray aluminum chloride into aluminum and aluminum alloy melts, so that aluminum chloride and magnesium react as follows:
2AlCl3+3Mg==3MgCl2+Al
According to this method, chlorine does not escape into the atmosphere, and unreacted aluminum chloride is absorbed by the above sodium chloride and potassium chloride solvents. This method can reduce the magnesium content of aluminum and aluminum alloy melts by 0.1-0.2%.
2.4 Cryolite Magnesium Removal Method
Cryolite reacts with magnesium to generate compounds that are insoluble in aluminum and aluminum alloy melts and remove magnesium. Cryolite is relatively cheap and easy to obtain, so that the method for removing magnesium from cryolite has been widely used in the secondary aluminum industry. Cryolite and magnesium undergo the following chemical reactions in aluminum and aluminum alloy melts:
3Na3AlF6+3Mg==2Al+6NaF+3MgF2
The theoretical consumption of cryolite is 6kg/kg-Mg, and the actual consumption is 1.5-2 times of the theoretical consumption. The reaction temperature is 850-900℃, which can reduce the magnesium content to 0.05%. In order to reduce the temperature for removing magnesium from cryolite, cryolite containing 40% NaCl and 20% KCl is sprinkled on the surface of the melt.
3. Technology For Removing Zinc, Lead, Etc
The chlorination and zinc removal method can be used to remove zinc from aluminum and aluminum alloy melts. This method uses the principle that zinc has a greater affinity for oxygen than aluminum. During the smelting process, tools are used to stir aluminum and aluminum alloy melts to promote the reaction of zinc with oxygen, thereby achieving the purpose of zinc removal. The effect is very limited, and during the process of removing zinc, it is easy to cause oxidative burning of aluminum and other elements. It will also cause aluminum and aluminum alloy melt to get gas and produce a large number of inclusions. Generally, it is not recommended to use oxidizing zinc removal.
The sedimentation method is used to remove heavy metal impurities such as zinc and lead in aluminum and aluminum alloy melts. The sedimentation method is to prolong the standing time of aluminum and aluminum alloy melts, using the principle of greater density of zinc and lead, so that zinc and lead can sink to the bottom of the furnace during smelting; stable liquid flow during discharge can make heavy metals such as zinc and lead First, it flows out and adheres to the first few ingots that are poured, and these ingots can be selected for additional treatment.
The elution crystallization method can also be used to remove non-aluminum metal inclusions. This method refining aluminum and aluminum alloy melts is based on the principle that the solubility of non-aluminum metal inclusions in molten aluminum changes during cooling. However, the dissolution crystallization method has high cost and complicated operation, and it is rarely used in the large-scale secondary aluminum industry.
No matter which method is used to remove non-aluminum metal inclusions in aluminum and aluminum alloy melts, it will increase the production cost of secondary aluminum. Improving the direct utilization rate of aluminum and aluminum alloy scrap, making full and reasonable utilization of valuable elements in aluminum and aluminum alloy scrap, and selecting the aforementioned advanced and efficient pretreatment process has very important practical significance for the production of recycled aluminum.
4. Technology For Removing Sodium, Potassium, Hydrogen, Calcium, etc.
Foreign countries have developed the "LARS" melt online technology, which can produce high-quality aluminum ingots for aerospace and aviation with high purity requirements. This technology is in a leading position in the world. Its important characteristics are:
- (1) The outgassing rate is high. The use of this equipment can reduce the online hydrogen content of the melt from 0.39mL/100×10-6 to below 0.1mL/100g, and the outgassing rate can reach more than 75%.
- (2) Effectively remove metal and non-metal impurities.
- (3) Effectively remove alkali metals, make K+, Ca+, Li+, Na+ ions and other alkali metal ions less than 1×10-6 after use; effectively remove various compounds.
After use, the product has passed the American aerospace industry Class A or AA and flaw detection. For example, 7075 alloy only has a Class A flaw control rate of 97%, and a Class AA flaw control rate of 92%.
Minghe Die Casting Company Is Custom manufacturer of precision & non-ferrous die castings. Products include aluminum & zinc die castings. Aluminum die castings are available in alloys including 380 & 383. Specifications include plus /- 0.0025 tolerances & maximum molding weight of 10 lbs. Zinc die casting parts are available in standard alloys such as Zamak no. 3, Zamak no. 5 & Zamak no. 7 & hybrid alloys such as ZA-8 & ZA-27. Specifications include plus /- 0.001 tolerances & maximum molding weight of 4.5 lbs.
Please keep the source and address of this article for reprinting: The Impurity Removal Technology For Secondary Aluminum Smelting Process
Minghe Die Casting Company are dedicated to manufacture and provide quality and high performance Casting Parts(metal die casting parts range mainly include Thin-Wall Die Casting,Hot Chamber Die Casting,Cold Chamber Die Casting),Round Service(Die Casting Service,Cnc Machining,Mold Making,Surface Treatment).Any custom Aluminum die casting, magnesium or Zamak/zinc die casting and other castings requirements are welcome to contact us.
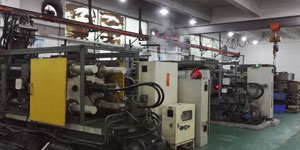
Under the control of ISO9001 and TS 16949,All processes are carried out through hundreds of advanced die casting machines, 5-axis machines, and other facilities, ranging from blasters to Ultra Sonic washing machines.Minghe not only has advanced equipment but also have professional team of experienced engineers,operators and inspectors to make the customer’s design come true.
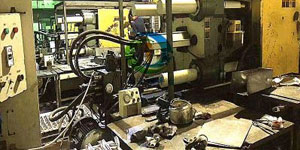
Contract manufacturer of die castings. Capabilities include cold chamber aluminum die casting parts from 0.15 lbs. to 6 lbs., quick change set up, and machining. Value-added services include polishing, vibrating, deburring, shot blasting, painting, plating, coating, assembly, and tooling. Materials worked with include alloys such as 360, 380, 383, and 413.
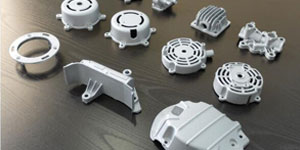
Zinc die casting design assistance/concurrent engineering services. Custom manufacturer of precision zinc die castings. Miniature castings, high pressure die castings, multi-slide mold castings, conventional mold castings, unit die and independent die castings and cavity sealed castings can be manufactured. Castings can be manufactured in lengths and widths up to 24 in. in +/-0.0005 in. tolerance.
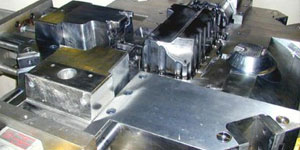
ISO 9001: 2015 certified manufacturer of die cast magnesium, Capabilities include high-pressure magnesium die casting up to 200 ton hot chamber & 3000 ton cold chamber, tooling design, polishing, molding, machining, powder & liquid painting, full QA with CMM capabilities, assembly, packaging & delivery.
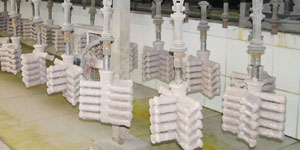
ITAF16949 certified. Additional Casting Service Include investment casting,sand casting,Gravity Casting, Lost Foam Casting,Centrifugal Casting,Vacuum Casting,Permanent Mold Casting,.Capabilities include EDI, engineering assistance, solid modeling and secondary processing.
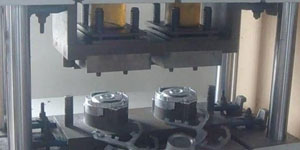
Casting Industries Parts Case Studies for: Cars, Bikes, Aircraft, Musical instruments, Watercraft, Optical devices, Sensors, Models, Electronic devices, Enclosures, Clocks, Machinery, Engines, Furniture, Jewelry, Jigs, Telecom, Lighting, Medical devices, Photographic devices, Robots, Sculptures, Sound equipment, Sporting equipment, Tooling, Toys and more.
What Can we help you do next?
∇ Go To Homepage For Die Casting China
→Casting Parts-Find out what we have done.
→Ralated Tips About Die Casting Services
By Minghe Die Casting Manufacturer |Categories: Helpful Articles |Material Tags: Aluminum Casting, Zinc Casting, Magnesium Casting, Titanium Casting, Stainless Steel Casting, Brass Casting,Bronze Casting,Casting Video,Company History,Aluminum Die Casting |Comments Off