The Influence Of Refractory Fillers On Casting Coatings Quality
Casting coating affects the internal and surface quality of castings, especially the lost foam coating is one of the key factors to control and ensure the quality of lost foam casting. As we all know, foundry coatings are composed of five basic components: carrier, refractory filler, suspending agent, binder and auxiliary additives, among which refractory filler is the main component, which determines the refractoriness, chemical stability, and thermal insulation of the coating. It also has an important influence on the air permeability and sintering peelability of the coating. Therefore, it can be said that the quality of refractory filler is a key factor in the quality of casting coatings.
In lost foam casting, how to choose refractory fillers for coatings mainly consider the following properties of the fillers:
- (1) Refractoriness;
- (2) Density;
- (3) Thermal expansion coefficient;
- (4) Grain type and particle size distribution;
- (5) Chemical reactivity with molten metal;
- (6) Gas volume;
- (7) The compatibility with other ingredients in the coating;
- (8) Whether it will affect the health of the operators and the environment.
Bauxite powder
Bauxite has been widely used in common cast steel coatings and cast iron coatings in recent years due to its high refractoriness, good chemical stability, small expansion coefficient, abundant sources, and low price.
1 Chemical composition
The content of Al2O3 in the bauxite, the sintering temperature, and the content of impurities such as Ti02 and FeO3 have a greater impact on the coating. Therefore, the ore with high Al2O3 content is selected and calcined at 1450℃-1500℃, and then the clinker is selected and ground into fine powder. After that, pickling treatment is still a key step. In addition to the higher content of Ti02 and FeO3 in bauxite without pickling treatment, the dust and mechanical iron mixed in the calcination and grinding process increase. (Currently, the amount of fine bauxite powder Most of the processing is based on the Raymond mill, and most of the wear-resistant parts are high-strength steel castings, and the mixed mechanical iron is difficult to remove with magnetic separation.) The prepared coating is affected by the refractoriness, and the increase in floating and sediment Paint brushability, suspension and storage time.
1.2 Granularity
The particle size and particle size distribution of bauxite are important factors affecting the density and air permeability of the coating, especially the lost foam coating. Whether the pyrolysis products of the foam pattern during the sintering process can be smoothly discharged through the coating, the loss of the foam coating Air permeability is a major feature that distinguishes it from other sand casting coatings. According to different needs, Minghe Die Casting Company has divided the particle size of bauxite into two different specifications for use in sand casting coatings and lost foam coatings.
The particle size distribution of bauxite powder used in sand casting coatings is:
- -270 mesh to 320 mesh, the concentration rate is 96%
- +270 mesh not more than 1%
The particle size distribution of bauxite used in lost foam coatings is:
- -270 mesh to -320 mesh 78%
- -200 mesh to -270 mesh 15%
- -100 mesh to -200 mesh 5%
- +100 mesh not more than 2%
The above particle size distribution is also applicable to the gradation of other refractory fillers.
Zircon powder and N-3 powder
Zircon powder is processed from zircon sand, with low linear expansion coefficient, good thermal shock stability, high refractoriness and no chemical effect on most alloys at high temperatures. It is a good refractory filler, mostly used for stainless steel , High-alloy steel castings, imported zirconium powder is mostly used abroad for jet mill grinding, the content of Zr02 is greater than 65%, and the impurity content is low. The zirconium powder processed in China is mostly ground by Raymond mill, and the impurity content is relatively high. In recent years, zirconium The source of powder powder is relatively complicated, and the price is rising all the way. Many coating manufacturers are looking for alternative products of zircon powder to reduce the cost of cast steel coating. Xiangyu Company has successfully developed a new synthetic refractory filler N-3 powder. Widely used in cast steel coatings.
N-3 powder is synthesized from several natural refractory materials in proportion, fused, crushed, and acid-washed. The refractoriness, linear expansion coefficient, and chemical stability are close to zircon powder, and it does not interact with alkaline oxidation such as FeO3. The material reacts, which is conducive to the anti-sticking of the coating, and the price is only one-third of the zircon powder
Magnesia powder and forsterite powder
Magnesia powder and forsterite powder are usually used as the first choice refractory materials for the preparation of coatings for alkaline steel castings. The main component of magnesia large sea powder is the agglomerates obtained by calcining natural magnesite ore (MgCO2), which is processed by crushing, grinding, and magnetic separation. It is worth paying special attention to the following points:
- (1) The sintered block must be a so-called burnt block calcined at 1500℃-1600℃, the particles are dense and hard, and the MgO content is greater than 90%, otherwise the coating is easy to crack during high temperature pouring.
- (2) The sintered block contains high magnetic materials such as iron and iron oxide. Xiangyu Company uses 5000 high-magnetic double-roll magnetic separator to perform magnetic separation twice, and the magnetic materials are selected as high as about 25%. Therefore, to obtain high-quality magnesia powder, magnetic separation is a key step.
- (3) Magnesia powder is easy to absorb water and become damp, so special attention should be paid to the water content in the powder.
The iron oxide content in forsterite powder should be mainly controlled, not more than 10%, the smaller the serpentine (hydrous magnesium silicate) content, the better, generally not more than 20%, otherwise the refractoriness will decrease, the ignition loss and the gas evolution will increase Big.
Brown corundum powder and white corundum powder
Brown corundum is made of bauxite as raw material and processed by high temperature smelting at 2000°C-2400°C. White corundum is made of alumina powder and recrystallized by electrofusion. Its basic mineral is a-Al2O3, and the former is greater than 94%. , The latter is greater than 97%, the corundum has high hardness, high melting point, high thermal conductivity, good thermal stability, not easy to crack, good acid and alkali resistance, brown corundum powder is suitable for the preparation of ordinary cast steel and alloy steel coatings, white Because of its high price, corundum powder is often used as a composite filler for coatings for large steel castings. It should be noted that the particle size distribution and label of the corundum powder for abrasives and the corundum powder for casting coatings are inconsistent, and should be graded according to the particle size composition of the refractory filler for coatings. In addition, there are waste sand wheels grinding to produce corundum powder on the market, which has high impurity content, so pay special attention to it when purchasing.
Quartz powder and fused silica powder
Quartz powder is one of the traditionally used refractory fillers. Because of its low price and abundant resources, it is still used by many manufacturers. However, its low refractoriness and large linear expansion coefficient are only suitable for casting coatings and small steel castings. Fused silica powder and ordinary quartz powder can be used in combination, and used in lost foam cast steel and cast iron coatings, effectively sending out the cracking and peeling of the coating caused by the phase transformation and expansion of the quartz powder, and the effect is very good. The characteristics of fused silica powder are: low thermal expansion rate, good thermal stability, strong creep resistance at high temperature, especially suitable for lost foam coatings.
Other refractory fillers
In addition to the above-mentioned refractory fillers, there are also mullite powder, chromite powder, high-aluminum steel jade powder, diatomite powder, talc powder, mica powder, feldspar powder, etc. According to the functional requirements of the coating, it can be It can be used as a refractory filler if it is selected alone or compounded. It will not be described in detail here. Xiangyu Company can supply it. In short, the refractory filler is the main part of the coating, which plays a decisive role in the effect of the coating. The selection of refractory filler should focus on the main indicators such as mineral composition, purity, impurity content, and particle size composition of the refractory filler.
Please keep the source and address of this article for reprinting:The Influence Of Refractory Fillers On Casting Coatings Quality
Minghe Die Casting Company are dedicated to manufacture and provide quality and high performance Casting Parts(metal die casting parts range mainly include Thin-Wall Die Casting,Hot Chamber Die Casting,Cold Chamber Die Casting),Round Service(Die Casting Service,Cnc Machining,Mold Making,Surface Treatment).Any custom Aluminum die casting, magnesium or Zamak/zinc die casting and other castings requirements are welcome to contact us.
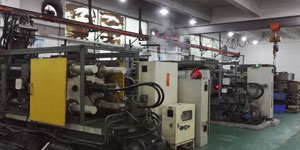
Under the control of ISO9001 and TS 16949,All processes are carried out through hundreds of advanced die casting machines, 5-axis machines, and other facilities, ranging from blasters to Ultra Sonic washing machines.Minghe not only has advanced equipment but also have professional team of experienced engineers,operators and inspectors to make the customer’s design come true.
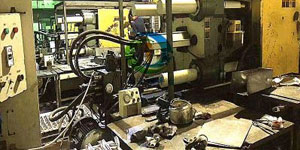
Contract manufacturer of die castings. Capabilities include cold chamber aluminum die casting parts from 0.15 lbs. to 6 lbs., quick change set up, and machining. Value-added services include polishing, vibrating, deburring, shot blasting, painting, plating, coating, assembly, and tooling. Materials worked with include alloys such as 360, 380, 383, and 413.
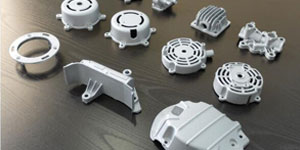
Zinc die casting design assistance/concurrent engineering services. Custom manufacturer of precision zinc die castings. Miniature castings, high pressure die castings, multi-slide mold castings, conventional mold castings, unit die and independent die castings and cavity sealed castings can be manufactured. Castings can be manufactured in lengths and widths up to 24 in. in +/-0.0005 in. tolerance.
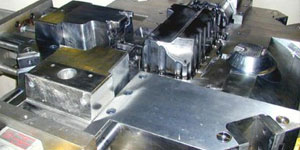
ISO 9001: 2015 certified manufacturer of die cast magnesium, Capabilities include high-pressure magnesium die casting up to 200 ton hot chamber & 3000 ton cold chamber, tooling design, polishing, molding, machining, powder & liquid painting, full QA with CMM capabilities, assembly, packaging & delivery.
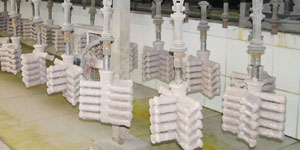
ITAF16949 certified. Additional Casting Service Include investment casting,sand casting,Gravity Casting, Lost Foam Casting,Centrifugal Casting,Vacuum Casting,Permanent Mold Casting,.Capabilities include EDI, engineering assistance, solid modeling and secondary processing.
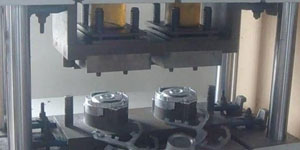
Casting Industries Parts Case Studies for: Cars, Bikes, Aircraft, Musical instruments, Watercraft, Optical devices, Sensors, Models, Electronic devices, Enclosures, Clocks, Machinery, Engines, Furniture, Jewelry, Jigs, Telecom, Lighting, Medical devices, Photographic devices, Robots, Sculptures, Sound equipment, Sporting equipment, Tooling, Toys and more.
What Can we help you do next?
∇ Go To Homepage For Die Casting China
→Casting Parts-Find out what we have done.
→Ralated Tips About Die Casting Services
By Minghe Die Casting Manufacturer |Categories: Helpful Articles |Material Tags: Aluminum Casting, Zinc Casting, Magnesium Casting, Titanium Casting, Stainless Steel Casting, Brass Casting,Bronze Casting,Casting Video,Company History,Aluminum Die Casting |Comments Off