The Influence Of Three Cutting Elements On Machining Efficiency
Everyone knows that when improving machining efficiency, increasing the three elements of cutting (cutting speed, cutting depth, and feed rate) is the simplest and most direct method. However, the improvement of the three elements of tool cutting is generally limited by the existing machine tool design conditions. So the cheapest way is to choose a good tool material.
The determination rule of the three elements of cutting
Determine the depth of the knife, the amount of feed and the linear cutting speed.
Cutting depth: generally determined according to the machining allowance;
Feed rate: The rough machining feed rate is determined by the power of the machine tool, and the finishing feed rate is determined by the surface roughness;
Cutting speed: Determined according to the material of the tool and the spindle speed of the machine tool.
From the perspective of improving cnc machining efficiency, increasing the depth of cut is probably a method worth considering. One of the important reasons is that experiments have shown that once the cutting depth is equal to 10 times the feed, increasing the cutting depth will have minimal impact on tool durability. If the cutting speed is increased, changing the cutting speed will cause the tool durability to change at nearly twice the speed; if the feed is changed, the tool durability can also be changed roughly the same. Therefore, when the so-called "net size" cannot be achieved for the blanks of our mass production mode, increasing the depth of cut is a choice that can achieve high-efficiency production cycle without causing significant increase in tool costs.
Tool selection
Cemented carbide tools are the mainstream tools in the current tool market. Everyone is familiar with this tool. You can adjust the three cutting elements of cemented carbide tools according to the actual processing site conditions, so as to maximize the tool life and processing efficiency. However, cubic nitrogen The development of boron-based tools has not been long, and many people have never touched such tools. However, with the emergence of hard materials and difficult-to-machine materials, cubic boron nitride tools have gradually appeared in everyone's field of vision. But many people often think that cubic boron nitride tools are limited to high-speed cutting and finishing processes.
In fact, with the continuous R&D and innovation of the superhard material tool industry, cubic boron nitride tools have been widely used in rough machining processes and intermittent cutting conditions. The selection of cubic boron nitride tools is the same as that of cemented carbide tools. According to different workpiece materials, different tool grades and tool structures are selected.
The composite welding cubic boron nitride blade is generally used for the finishing process. It has only the cutting edge part of the cubic boron nitride material, and the matrix is a cemented carbide matrix. The depth of the knife is controlled within 0.5mm, so it can only be used For finishing processes, for those with large margins and irregular surfaces, choose the integral cubic boron nitride blade. The whole body is made of cubic boron nitride. The cutting depth is 1-10mm, and the tool life is generally 3 hours/ Cutting edge.
With the research progress of cubic boron nitride tools and the actual needs in processing, the original high-speed finishing has developed to intermittent, rough and semi-finish, and can also be used in ordinary machine tools; the use cost is also More economical.
Further Reading
The machining ranges of cubic boron nitride tools and cemented carbide tools overlap. For example, gray cast iron, cemented carbide tools and cubic boron nitride tools can all be processed. You can choose a more economical and cost-effective tool material, cemented carbide according to the needs of the enterprise. Due to its own performance limitations, the maximum linear speed of the tool can reach 350m/min, while the cubic boron nitride tool can reach 1500m/min. At the same time, the durability of the cubic boron nitride tool is 30-50 times that of ordinary cemented carbide tools. 5-15 times the life of the layered carbide tool.
However, companies do not blindly choose cubic boron nitride tools to process gray cast iron. After all, the price of cubic boron nitride tools is higher than that of cemented carbide tools. Therefore, it is recommended to choose for mass production and high processing efficiency requirements. For cubic boron nitride cutting tools, if the processing efficiency is not high and there are few jobs, it is more economical and cost-effective to choose cemented carbide cutting tools.
Please keep the source and address of this article for reprinting:The Influence Of Three Cutting Elements On Machining Efficiency
Minghe Die Casting Company are dedicated to manufacture and provide quality and high performance Casting Parts(metal die casting parts range mainly include Thin-Wall Die Casting,Hot Chamber Die Casting,Cold Chamber Die Casting),Round Service(Die Casting Service,Cnc Machining,Mold Making,Surface Treatment).Any custom Aluminum die casting, magnesium or Zamak/zinc die casting and other castings requirements are welcome to contact us.
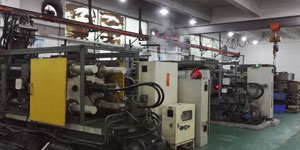
Under the control of ISO9001 and TS 16949,All processes are carried out through hundreds of advanced die casting machines, 5-axis machines, and other facilities, ranging from blasters to Ultra Sonic washing machines.Minghe not only has advanced equipment but also have professional team of experienced engineers,operators and inspectors to make the customer’s design come true.
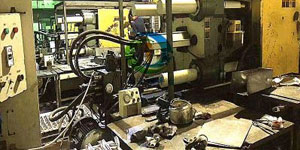
Contract manufacturer of die castings. Capabilities include cold chamber aluminum die casting parts from 0.15 lbs. to 6 lbs., quick change set up, and machining. Value-added services include polishing, vibrating, deburring, shot blasting, painting, plating, coating, assembly, and tooling. Materials worked with include alloys such as 360, 380, 383, and 413.
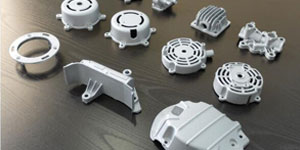
Zinc die casting design assistance/concurrent engineering services. Custom manufacturer of precision zinc die castings. Miniature castings, high pressure die castings, multi-slide mold castings, conventional mold castings, unit die and independent die castings and cavity sealed castings can be manufactured. Castings can be manufactured in lengths and widths up to 24 in. in +/-0.0005 in. tolerance.
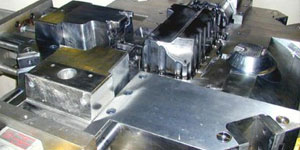
ISO 9001: 2015 certified manufacturer of die cast magnesium, Capabilities include high-pressure magnesium die casting up to 200 ton hot chamber & 3000 ton cold chamber, tooling design, polishing, molding, machining, powder & liquid painting, full QA with CMM capabilities, assembly, packaging & delivery.
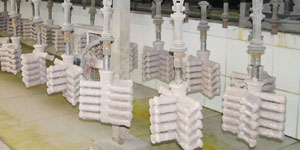
ITAF16949 certified. Additional Casting Service Include investment casting,sand casting,Gravity Casting, Lost Foam Casting,Centrifugal Casting,Vacuum Casting,Permanent Mold Casting,.Capabilities include EDI, engineering assistance, solid modeling and secondary processing.
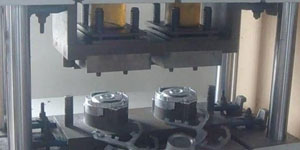
Casting Industries Parts Case Studies for: Cars, Bikes, Aircraft, Musical instruments, Watercraft, Optical devices, Sensors, Models, Electronic devices, Enclosures, Clocks, Machinery, Engines, Furniture, Jewelry, Jigs, Telecom, Lighting, Medical devices, Photographic devices, Robots, Sculptures, Sound equipment, Sporting equipment, Tooling, Toys and more.
What Can we help you do next?
∇ Go To Homepage For Die Casting China
→Casting Parts-Find out what we have done.
→Ralated Tips About Die Casting Services
By Minghe Die Casting Manufacturer |Categories: Helpful Articles |Material Tags: Aluminum Casting, Zinc Casting, Magnesium Casting, Titanium Casting, Stainless Steel Casting, Brass Casting,Bronze Casting,Casting Video,Company History,Aluminum Die Casting |Comments Off