The Influencing Factors Of Metal Forgings Heat Treatment
In forging production, in addition to ensuring the required shape and size of the forging, it must also meet the performance requirements of the part during use. Using reasonable forging technology and process parameters, the organization and structure of raw materials can be improved through the following aspects performance:
- Break the columnar crystals, improve the macrosegregation, change the as-cast structure into the forged structure, and under the appropriate temperature and stress conditions, weld the internal voids to increase the density of the material;
- The ingot is forged to form a fiber structure, and further rolling, extrusion, and die forging are used to obtain a reasonable fiber direction distribution for the forging;
- Control the size and uniformity of crystal grains;
- Improve the distribution of the second phase (such as alloy carbides in ledeburite rigid);
- The structure is strengthened by deformation or deformation-phase transformation.
Due to the improvement of the above-mentioned structure, the plasticity, impact toughness, fatigue strength and durability of forgings have also been improved, and then through the final heat treatment of the parts, a good combination of hardness, strength and plasticity required by the parts can be obtained. performance.
If the used forging process is unreasonable, it may produce forging defects, including surface defects, internal defects or unqualified performance, which will affect the processing quality of subsequent processes, and some will seriously affect the performance of forgings and reduce the quality of finished products. The service life of the battery may even endanger safety.
The influence of the forging structure on the structure and properties after the final heat treatment is mainly manifested in the following aspects:
- Unimprovable structural defects: austenitic and ferritic heat-resistant stainless steels, high-temperature alloys, aluminum alloys, magnesium alloys, etc., materials that have no isomeric transformation during heating and cooling, as well as some copper alloys and For titanium alloys, the structural defects generated during the forging process cannot be improved by heat treatment.
- Organizational defects that can be improved: coarse-grained and Widmanstatten structure in general overheated structural steel forgings, slight network carbides caused by improper cooling of hypereutectoid steels and bearing steels during post-forging heat treatment , Satisfactory structure and performance can be obtained after the final heat treatment of the forging (3) Organizational defects that are difficult to eliminate by normal heat treatment: such as low-magnification coarse-grained, 9Cr18 stainless steel, twin carbides of H13, etc., require high-temperature normalizing, repeated normalizing, low-temperature decomposition, high-temperature diffusion annealing and other measures to be improved .
- Organizational defects that cannot be eliminated by the general heat treatment process: serious stone fractures and ridge fractures, overburning, ferrite bands in stainless steel, carbide meshes and bands in ledeburite alloy tool steel, etc. The performance of the forgings after heat treatment declines or even fails.
- Microstructure defects that will further develop during the final heat treatment: For example, the coarse-grained structure in the alloy structural steel forgings, if the heat treatment after forging is not improved, often causes martensite after carbon, nitriding and quenching The needle is thick and the performance is unqualified; the thick banded carbides in high-speed steel often cause cracking during quenching.
- If the heating is improper, for example, the heating temperature is too high and the heating time is too long, it will cause defects such as decarburization, overheating, and overburning.
- During the cooling process after forging, if the process is improper, it may cause cooling cracks, white spots, etc., which may crack during the heat treatment.
What are the effects of cutting on the quality of heat-treated workpieces?
- In the state of quenching and tempering, annealing and normalizing of the workpiece, the hardness is lower than 45HRC, and the quality of the workpiece including surface finish, residual stress, machining allowance, and removal of the surface decarburization carbon-depleted layer is not affected by the cutting process. Obviously, it will not cause a change in the potential performance of the workpiece.
- The processing of workpieces of hardened steel or workpieces is also called hard processing. The hardness of the workpieces is as high as 50~65HRC. The materials mainly include ordinary quenched steel, quenched die steel, bearing steel, rolled steel and high-speed steel, etc. The impact of cutting is more obvious. Factors such as the generation and conduction of cutting heat, high-speed friction and wear during the cutting process will cause a certain degree of damage to the machined surface. The integrity of the machined surface during hard cutting mainly includes the surface texture, hardness, surface roughness, dimensional accuracy, residual stress distribution and white layer generation.
The hardness of the machined surface increases with the increase of the cutting speed, and decreases with the increase of the feed rate and the cutting amount. And the higher the hardness of the machined surface, the greater the depth of the hardened layer. The results show that the uniform residual compressive stress on the surface of the workpiece after hard cutting, while the maximum compressive stress of the workpiece after grinding is mainly concentrated on the surface of the workpiece.
The larger the obtuse angle radius of the tool, the greater the value of residual compressive stress; the higher the hardness of the workpiece, the larger the value of residual compressive stress. The hardness of the workpiece has a great influence on the surface integrity of the workpiece. The greater the hardness of the workpiece, the more conducive to the formation of residual compressive stress.
Another important factor that affects the surface quality of hard cutting is the formation of white layers. The white layer is a structure formed by the hard cutting process. It has unique wear characteristics: on the one hand, it has high hardness and good corrosion resistance; on the other hand, it shows high brittleness, which is easy to cause early spalling failure. It may even crack after being placed for a stage after processing. When cutting hardened AISIE52100 bearing steel with ceramic and PCBN tools on a high-rigidity CNC lathe, it was found that the surface and sub-surface layers of the workpiece have changed in their microstructure. The microstructure is composed of a white untempered layer and a black over-tempered layer.
At present, the view that the white layer is regarded as a martensite structure has been unanimously recognized, and the main dispute lies in the fine structure of the white layer. One view is that the white layer is the result of phase change and is composed of fine-grained martensite formed by rapid heating and sudden cooling of the material during the cutting process. Another view is that the formation of the white layer is only a term of deformation mechanism, which is just an unconventional martensite obtained by plastic deformation.
Please keep the source and address of this article for reprinting:The Influencing Factors Of Metal Forgings Heat Treatment
Minghe Die Casting Company are dedicated to manufacture and provide quality and high performance Casting Parts(metal die casting parts range mainly include Thin-Wall Die Casting,Hot Chamber Die Casting,Cold Chamber Die Casting),Round Service(Die Casting Service,Cnc Machining,Mold Making,Surface Treatment).Any custom Aluminum die casting, magnesium or Zamak/zinc die casting and other castings requirements are welcome to contact us.
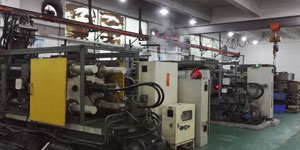
Under the control of ISO9001 and TS 16949,All processes are carried out through hundreds of advanced die casting machines, 5-axis machines, and other facilities, ranging from blasters to Ultra Sonic washing machines.Minghe not only has advanced equipment but also have professional team of experienced engineers,operators and inspectors to make the customer’s design come true.
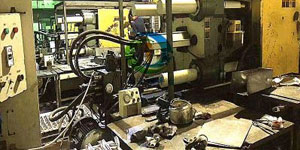
Contract manufacturer of die castings. Capabilities include cold chamber aluminum die casting parts from 0.15 lbs. to 6 lbs., quick change set up, and machining. Value-added services include polishing, vibrating, deburring, shot blasting, painting, plating, coating, assembly, and tooling. Materials worked with include alloys such as 360, 380, 383, and 413.
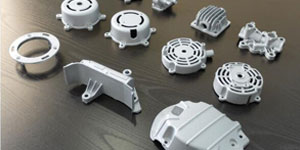
Zinc die casting design assistance/concurrent engineering services. Custom manufacturer of precision zinc die castings. Miniature castings, high pressure die castings, multi-slide mold castings, conventional mold castings, unit die and independent die castings and cavity sealed castings can be manufactured. Castings can be manufactured in lengths and widths up to 24 in. in +/-0.0005 in. tolerance.
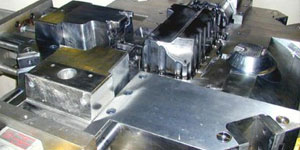
ISO 9001: 2015 certified manufacturer of die cast magnesium, Capabilities include high-pressure magnesium die casting up to 200 ton hot chamber & 3000 ton cold chamber, tooling design, polishing, molding, machining, powder & liquid painting, full QA with CMM capabilities, assembly, packaging & delivery.
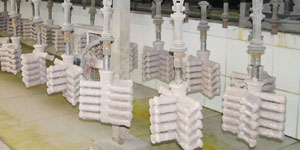
ITAF16949 certified. Additional Casting Service Include investment casting,sand casting,Gravity Casting, Lost Foam Casting,Centrifugal Casting,Vacuum Casting,Permanent Mold Casting,.Capabilities include EDI, engineering assistance, solid modeling and secondary processing.
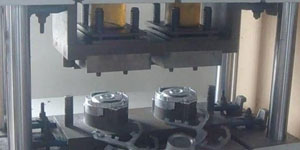
Casting Industries Parts Case Studies for: Cars, Bikes, Aircraft, Musical instruments, Watercraft, Optical devices, Sensors, Models, Electronic devices, Enclosures, Clocks, Machinery, Engines, Furniture, Jewelry, Jigs, Telecom, Lighting, Medical devices, Photographic devices, Robots, Sculptures, Sound equipment, Sporting equipment, Tooling, Toys and more.
What Can we help you do next?
∇ Go To Homepage For Die Casting China
→Casting Parts-Find out what we have done.
→Ralated Tips About Die Casting Services
By Minghe Die Casting Manufacturer |Categories: Helpful Articles |Material Tags: Aluminum Casting, Zinc Casting, Magnesium Casting, Titanium Casting, Stainless Steel Casting, Brass Casting,Bronze Casting,Casting Video,Company History,Aluminum Die Casting |Comments Off