The Internal Quality Inspection Of Aluminum Alloy Castings
In recent years, the casting technology of aluminum alloy castings has been greatly developed, and the output of aluminum castings has been increasing year by year. Now it has been more and more widely used in the fields of weapons, aviation, aerospace, textiles, etc., and the quality requirements of castings are also increasing. strict. Among all the characteristics of casting quality, internal quality is the key factor that determines the overall quality of castings. At the same time, the internal quality of castings also reflects the pros and cons of casting technology. Therefore, the control of the internal quality defects of castings is the goal that casting technicians must always solve and improve.
1. The concept of internal quality
The internal quality of aluminum alloy castings generally refers to the degree to which the internal defects of the casting meet the requirements of relevant standards. These defects generally include cracks, pinholes, pores, shrinkage holes, porosity, segregation and inclusions. Due to the existence of these defects, the physical properties, mechanical properties and metallographic structure of the castings will often change, which will bring about the use of castings. Serious hidden danger. Therefore, internal quality is the primary control factor for casting production and inspection.
2. Characteristics of internal quality defects
- (1) Internal quality defects are often hidden inside the castings, which cannot be inspected by ordinary visual methods, and often require special methods and equipment to complete.
- (2) For the judgment of internal quality defects, the inspectors need to have professional knowledge training and have certain practical work experience.
3. Current standards implemented in my country
At present, there are two standards for the inspection of cast alloy castings in my country, one is GB/T9438—1999 (aluminum
The national standard for alloy castings, one is the HB963-2005 (aluminum alloy castings) aviation standard. The requirements for internal defects of the two standards are similar and different, mainly due to different industries and different usage requirements, but the basic requirements and inspection methods are the same, which are described separately below.
4. Classification of castings
The two standards divide the castings into three categories according to their importance in the use process.
Type Ⅰ castings: bear heavy loads, complex working conditions, used in key parts, damage to castings will be dangerous
And the safe operation of the whole machine.
Class Ⅱ castings: bear medium load, used in important parts, the damage of castings will affect the normal of the parts
Work and cause accidents.
Class Ⅲ castings: castings that bear light loads and are used for general parts.
5. GB/T9438—1999 requirements
(1) Casting inspection type This standard stipulates that the internal quality inspection must be carried out for Type I castings; for Type II and Type III castings, the internal quality inspection shall be carried out only when the user requires inspection.
(2) Several standards cited in the internal quality inspection of this standard
- ①GB/T11346-1989 Aluminum alloy castings X-ray photography inspection pinhole (circular) classification. The standard stipulates the classification of round pinholes in aluminum alloy castings, which are divided into two groups A and B according to the thickness of the transillumination. The A component grade is suitable for castings with a transilluminated thickness of <13mm, and the B component grade is suitable for transillumination. For castings with a thickness of 13-50mm, each group has 8 grades of reference film.
- ②HB6578-1992 standard reference radiograph for inspection of aluminum and magnesium alloy castings. The standard has a more detailed classification of internal quality defects, mainly including 6 categories of pores, pinholes, shrinkage, porosity, inclusions and segregation. Each category is divided into 8 grades of reference film.
- ③JB/T7946.3—1999 cast aluminum alloy pinhole. This standard specifies the grading principle and evaluation method for the low-magnification pinhole degree of cast aluminum alloy. The standard divides the pinhole degree into 5 levels.
(3) Inspection methods X-ray non-destructive testing; low power test inspection.
(4) Specific requirements for testing
- ① The internal quality of the casting is first inspected according to the technical requirements of the casting drawing.
- ② No crack defects are allowed inside the casting.
- ③If there are no clear regulations, for pinhole defects, Class I castings, hydraulic parts, and pneumatic parts should be accepted in accordance with the level 2 in the GB/T11346-1989 standard. Partial level 4 pinholes are allowed, but generally they should not exceed the inspected area. 25% of it. When the air-tightness test meets the design requirements, acceptance according to level 3 is allowed. Class Ⅱ castings shall be accepted according to level 3 pinholes.
- ④The internal porosity, shrinkage cavity, looseness and inclusion defects of various castings shall be implemented as specified in Table 1.
6. HB963-2005 requirements
Several standards cited in the internal quality inspection of this standard:
- (1) GB/T11346-1989 aluminum alloy castings X-ray photography inspection pinhole (circular) classification, the standard explanation is the same as above.
- (2) JB/T7946.3-1999 cast aluminum alloy pinhole, the standard explanation is the same as above.
- (3) HB5395—1988 Aluminum alloy X-ray photography inspection long pinhole classification standard. The standard is divided into 3 groups according to the thickness of castings. The first group is suitable for castings smaller than 13mm, the second group is suitable for castings larger than 13-25mm, and the third group is suitable for castings larger than 25-50mm. Each group has 1, There are 5 levels in 2, 3, 4, and 5.
- (4) HB5396-1988 aluminum alloy X-ray radiography inspection spongy porosity classification standard; HB5397-1988 aluminum alloy X-ray radiography inspection scattered porosity classification standard. These two standards are divided into 2 groups according to the thickness of the castings. The first group is suitable for castings smaller than 13mm, and the second group is suitable for castings larger than 13-50mm. Each group has 1, 2, 3, 4, and 5 in total. All levels.
Various internal porosity, shrinkage cavity, porosity and inclusion defects of various castings shall be implemented as specified in Table 2.
7. JB/T7946.3-1999 (cast aluminum alloy pinhole) requirements
(1) When the internal pinholes of castings are inspected by the low power test method, the Class I castings or hydraulic and pneumatic parts shall be accepted according to the second level of the standard, and the third level of pinholes is allowed, but generally shall not exceed the inspected area. 250u. When the air-tightness test meets the design requirements, acceptance according to level 3 is allowed. Class Ⅱ castings shall be accepted according to level 3 pinholes.
(2) Preparation method of low-magnification samples
- ①Metal samples shall be sampled according to the requirements of the drawings. Generally, the thick parts of the castings shall be taken.
- ②Surface roughness Ra≤1.6μm after sample processing.
- ③First clean the sample with gasoline, alcohol or acetone, and then etch the sample with 10%-15% sodium hydroxide aqueous solution at a humidity of (25±5)°C, and the etching time is 7-10min.
- ④ After the sample is etched, clean it with water, then remove the corrosion film on the surface of the sample with 20% to 25% nitric acid, then clean it with water and dry it.
- ⑤ Judge the sample against the standard level.
8. Other requirements for internal quality inspection
- (1) The above inspection contents and methods are not applicable to die castings.
- (2) When the internal quality is inspected by the low power method, because the location of the defect is difficult to accurately determine, the sampling location of the prepared sample is not necessarily the most serious location of the casting defect. Therefore, the reliability of low-power method inspection is poor. Generally, X-ray non-destructive inspection is the first choice for internal quality inspection, and low-power method inspection is used as a supplement.
- (3) The preparation of radiographic film should be carried out in accordance with the requirements of JB/T9217-1999 radiographic flaw detection method, and the blackness of the film should be 1.5-2.0.
- (4) Personnel engaged in radiographic evaluation must hold a level 2 or higher qualification certificate issued by the relevant competent authority of the country and suitable for their work.
- (5) When the pinhole (circular) defect shown on the X-ray film of the casting is between two adjacent levels, it shall be evaluated according to the severity level.
9. Work experience
- (1) Inspectors must learn more about casting process knowledge, fully understand the causes and physical forms of various defects, and improve their own judgment ability in order to make correct judgments on various defects.
- (2) The above inspection standards are only a guiding document, and they should be used flexibly in the actual application process. The function and stress of each part of each part are different, and the tolerance to defects is also different. Inspectors should be familiar with the actual application of each part during use, so that they can better use the standard.
- (3) Although high-quality parts have good performance, the casting process is more difficult, the cost is also high, and the yield is low, which will cause cost waste. Therefore, we must establish a sense of unity of opposites between quality and cost in our work. The basic performance must be guaranteed, and the casting cost must also be considered.
Please keep the source and address of this article for reprinting: The Internal Quality Inspection Of Aluminum Alloy Castings
Minghe Die Casting Company are dedicated to manufacture and provide quality and high performance Casting Parts(metal die casting parts range mainly include Thin-Wall Die Casting,Hot Chamber Die Casting,Cold Chamber Die Casting),Round Service(Die Casting Service,Cnc Machining,Mold Making,Surface Treatment).Any custom Aluminum die casting, magnesium or Zamak/zinc die casting and other castings requirements are welcome to contact us.
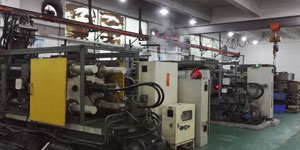
Under the control of ISO9001 and TS 16949,All processes are carried out through hundreds of advanced die casting machines, 5-axis machines, and other facilities, ranging from blasters to Ultra Sonic washing machines.Minghe not only has advanced equipment but also have professional team of experienced engineers,operators and inspectors to make the customer’s design come true.
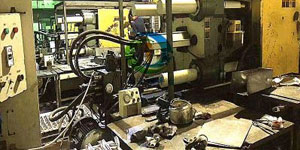
Contract manufacturer of die castings. Capabilities include cold chamber aluminum die casting parts from 0.15 lbs. to 6 lbs., quick change set up, and machining. Value-added services include polishing, vibrating, deburring, shot blasting, painting, plating, coating, assembly, and tooling. Materials worked with include alloys such as 360, 380, 383, and 413.
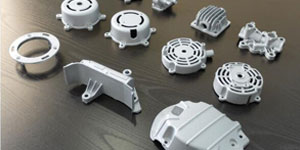
Zinc die casting design assistance/concurrent engineering services. Custom manufacturer of precision zinc die castings. Miniature castings, high pressure die castings, multi-slide mold castings, conventional mold castings, unit die and independent die castings and cavity sealed castings can be manufactured. Castings can be manufactured in lengths and widths up to 24 in. in +/-0.0005 in. tolerance.
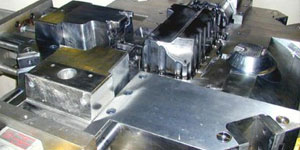
ISO 9001: 2015 certified manufacturer of die cast magnesium, Capabilities include high-pressure magnesium die casting up to 200 ton hot chamber & 3000 ton cold chamber, tooling design, polishing, molding, machining, powder & liquid painting, full QA with CMM capabilities, assembly, packaging & delivery.
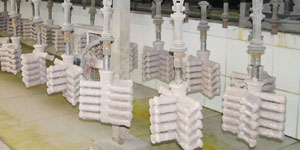
ITAF16949 certified. Additional Casting Service Include investment casting,sand casting,Gravity Casting, Lost Foam Casting,Centrifugal Casting,Vacuum Casting,Permanent Mold Casting,.Capabilities include EDI, engineering assistance, solid modeling and secondary processing.
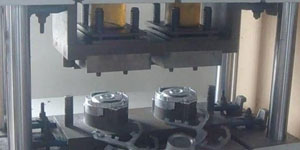
Casting Industries Parts Case Studies for: Cars, Bikes, Aircraft, Musical instruments, Watercraft, Optical devices, Sensors, Models, Electronic devices, Enclosures, Clocks, Machinery, Engines, Furniture, Jewelry, Jigs, Telecom, Lighting, Medical devices, Photographic devices, Robots, Sculptures, Sound equipment, Sporting equipment, Tooling, Toys and more.
What Can we help you do next?
∇ Go To Homepage For Die Casting China
→Casting Parts-Find out what we have done.
→Ralated Tips About Die Casting Services
By Minghe Die Casting Manufacturer |Categories: Helpful Articles |Material Tags: Aluminum Casting, Zinc Casting, Magnesium Casting, Titanium Casting, Stainless Steel Casting, Brass Casting,Bronze Casting,Casting Video,Company History,Aluminum Die Casting |Comments Off