The Introduction To Automobile Lightweight Process
At present, with the adjustment of energy structure and the improvement of environmental protection requirements, the automobile industry is developing in the direction of light weight. Data shows that for every 10% decrease in automobile quality, fuel consumption decreases by about 3% to 5%. Car lightweighting can not only effectively reduce energy consumption and increase car use functions, but also reduce production costs and improve car quality. It has become an important direction for car manufacturing to reduce car weight.
An important way to realize automobile lightweight
Of course, car lightweighting is not just a simple matter of reducing the weight of the car, but to ensure the quality of the car, using more new materials in the functional and structural parts of the car to make the performance of the car parts more excellent. At the same time, the weight is lighter, which ensures that the energy consumption of the car is reduced during the driving process, and achieves multiple effects.
Corresponding to the decline in the quality of the car itself, the lightweight technology of the car is mainly achieved through the following ways: the proportion of light materials continues to rise, aluminum alloys, magnesium alloys, titanium alloys, high-strength steels, plastics, powder metallurgy, and ecological composite materials And the application of ceramics, etc.; structural optimization and the level of modular design of parts and components continue to improve, such as the use of front-wheel drive, high-rigidity structure and ultra-light suspension structure to achieve the purpose of lightweight, computer-aided integration technology (including CAD/ The development of technologies such as CAE/CAO) and structural analysis has promoted continuous innovation in the forming method and connection technology of the automobile manufacturing industry.
In the above three ways to realize the lightweight of automobiles, the processing of new materials, the design and formation methods of automobile structuring and modularization, and the progress of connection technology all require corresponding technological innovations to achieve. Among these three approaches, laser cutting and laser welding have their unique advantages and become important technical means to realize the lightweight of automobiles.
Laser welding and laser cutting innovative lightweight technology
Automobile manufacturing is a huge system engineering that requires a series of processes and technologies to complete. In recent years, advanced technologies represented by laser cutting, industrial robots, and digital control are continuously promoting the upgrading of the automobile manufacturing industry. As an advanced processing method, laser is destined to bring revolutionary breakthroughs to the development of the automobile manufacturing industry. . At present, laser technology in the field of automobile manufacturing mainly focuses on applications such as laser welding, laser cutting, laser weakening, laser marking, laser trimming, and laser remanufacturing.
The most important advantage of laser in automobile manufacturing is its advanced non-contact processing method, which plays an important role in the innovation of processing technology in the fields of automobile body-in-white, automobile electronics, steel processing and so on. In the application of new materials such as aluminum alloys, magnesium alloys, titanium alloys, laser cutting is faster and more precise than previous cutting methods. For these difficult-to-process materials, laser cutting is easier to achieve. The advancement of technology has also turned the application of these new materials from ideal to reality, so that new materials can be realized in the lightweight of automobiles.
Structure and modularization are the integration of the scattered parts and components in traditional automobile manufacturing to realize the original functions of the automobile as a whole, thereby reducing weight and realizing light weight. The realization of structuring and modularization depends to a large extent on the progress of connection technology. Some of the traditional production methods are fastened by screws, and some are connected by glue. The traditional methods cannot meet the requirements of precision and robustness in modern automobile manufacturing, and the application of new materials also makes the traditional methods slightly disadvantageous. Laser welding is non-contact. During the processing, precision welding can be achieved without touching the product. It has achieved leap-forward progress in the robustness, seamlessness, precision and cleanliness of the connection. Become an important molding method in the future.
Laser technology has played an important role in the lightweight of automobiles, thereby greatly improving the performance and safety of automobiles. In the future, laser technology has broad application prospects in the automotive field.
Please keep the source and address of this article for reprinting: The Introduction To Automobile Lightweight Process
Minghe Die Casting Company are dedicated to manufacture and provide quality and high performance Casting Parts(metal die casting parts range mainly include Thin-Wall Die Casting,Hot Chamber Die Casting,Cold Chamber Die Casting),Round Service(Die Casting Service,Cnc Machining,Mold Making,Surface Treatment).Any custom Aluminum die casting, magnesium or Zamak/zinc die casting and other castings requirements are welcome to contact us.
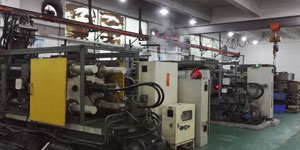
Under the control of ISO9001 and TS 16949,All processes are carried out through hundreds of advanced die casting machines, 5-axis machines, and other facilities, ranging from blasters to Ultra Sonic washing machines.Minghe not only has advanced equipment but also have professional team of experienced engineers,operators and inspectors to make the customer’s design come true.
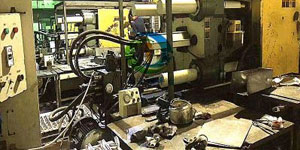
Contract manufacturer of die castings. Capabilities include cold chamber aluminum die casting parts from 0.15 lbs. to 6 lbs., quick change set up, and machining. Value-added services include polishing, vibrating, deburring, shot blasting, painting, plating, coating, assembly, and tooling. Materials worked with include alloys such as 360, 380, 383, and 413.
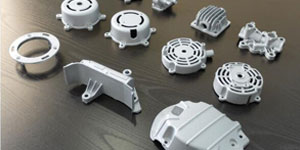
Zinc die casting design assistance/concurrent engineering services. Custom manufacturer of precision zinc die castings. Miniature castings, high pressure die castings, multi-slide mold castings, conventional mold castings, unit die and independent die castings and cavity sealed castings can be manufactured. Castings can be manufactured in lengths and widths up to 24 in. in +/-0.0005 in. tolerance.
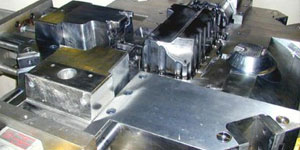
ISO 9001: 2015 certified manufacturer of die cast magnesium, Capabilities include high-pressure magnesium die casting up to 200 ton hot chamber & 3000 ton cold chamber, tooling design, polishing, molding, machining, powder & liquid painting, full QA with CMM capabilities, assembly, packaging & delivery.
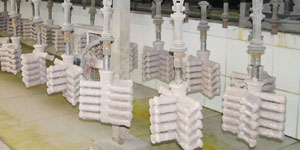
ITAF16949 certified. Additional Casting Service Include investment casting,sand casting,Gravity Casting, Lost Foam Casting,Centrifugal Casting,Vacuum Casting,Permanent Mold Casting,.Capabilities include EDI, engineering assistance, solid modeling and secondary processing.
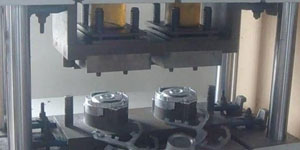
Casting Industries Parts Case Studies for: Cars, Bikes, Aircraft, Musical instruments, Watercraft, Optical devices, Sensors, Models, Electronic devices, Enclosures, Clocks, Machinery, Engines, Furniture, Jewelry, Jigs, Telecom, Lighting, Medical devices, Photographic devices, Robots, Sculptures, Sound equipment, Sporting equipment, Tooling, Toys and more.
What Can we help you do next?
∇ Go To Homepage For Die Casting China
→Casting Parts-Find out what we have done.
→Ralated Tips About Die Casting Services
By Minghe Die Casting Manufacturer |Categories: Helpful Articles |Material Tags: Aluminum Casting, Zinc Casting, Magnesium Casting, Titanium Casting, Stainless Steel Casting, Brass Casting,Bronze Casting,Casting Video,Company History,Aluminum Die Casting |Comments Off