The Key Points Of Aluminum Alloy Die Casting Design
Aluminum die castings have the advantages of high production efficiency, low processing costs, easy mechanical automation in the production process, high dimensional accuracy of the castings, good surface quality, and good overall mechanical properties; but it is easy to produce pores, flow marks, and scratches during the casting process. Defects such as flaws, dents, cracks, under-casting, etc., which make the appearance quality and mechanical properties of die-castings deteriorate. In order to avoid the above problems in the die-casting molding process, the structural designer needs to evaluate the plan in advance in the structural design of the die-casting part, and make a reasonable layout in the structural design of the parts, and reduce the defects to a minimum by optimizing the structure.
The Forming Principle Of Aluminum Alloy Die Casting
Aluminum alloy die-casting parts must be formed by molds, combined with die-casting machines and aluminum alloys for comprehensive use. The principle of die-casting process is to use high pressure to flow molten metal into a precision metal mold cavity at high speed, and the molten metal is cooled and solidified under pressure to form a casting. Cold and hot chamber die casting are two basic methods of die casting process. In the cold chamber die-casting, the molten metal is poured into the press chamber by manual or automatic pouring device, and then the injection punch advances to hydraulically press the metal into the cavity. In the hot chamber die casting process, the pressure chamber is perpendicular to the crucible, and the molten metal flows into the pressure chamber automatically through the feed port on the pressure chamber. The injection punch moves downwards to push the molten metal into the cavity through the gooseneck. After the molten metal is solidified, the die-casting mold is opened and the casting is taken out to complete the entire die-casting forming process.
Die casting wall thickness | Reinforcement Thickness |
0.8-2.5 | 1.5-3.5 |
2.0-3.5 | 2.5-3.5 |
Relation between rib thickness and die casting wall thickness (mm)
Design points of aluminum alloy die castings
The rationality of die-casting design is related to the entire die-casting molding process. When designing die-casting parts, the structural characteristics of die-casting parts and the process requirements of die-casting should be fully considered to minimize the defects of the designed die-casting parts in the process of die-casting molding process. Occurred, the quality of die-casting parts is improved to the greatest extent with the optimal design plan.
Alloy type | Zinc alloy | Aluminum alloy | Copper alloy |
Casting cavity | 0’20' | 0’32' | 0’45' |
Outer cavity of casting | 0’10' | 0’15' | 0’30' |
Min. Die Casting Slope
2.1 Reasonable design of the wall thickness of die castings
Wall thickness should be fully considered when designing aluminum alloy die casting structure. Wall thickness is a factor of special significance in the die casting process. Wall thickness has a close relationship with the entire process specification, such as the calculation of filling time and the selection of internal gate speed. , Calculation of solidification time, analysis of mold temperature gradient, the effect of pressure (final specific pressure), the length of mold retention time, the level of casting ejection temperature and operating efficiency; if the design wall thickness is too thick, shrinkage holes, sand holes, and pores will appear , External surface defects such as coarse internal grains, which reduce the mechanical properties, increase the quality of parts and increase the cost; too thin design wall thickness will cause poor aluminum liquid filling, difficult molding, poor aluminum alloy dissolution, and difficulty in filling the surface of castings. , Lack of material and other defects, and bring difficulties to the die casting process; with the increase of pores, the internal pores, shrinkage and other defects of die castings increase. Therefore, under the premise of ensuring sufficient strength and rigidity of the casting, the casting wall should be minimized Thick and keep the thickness of the cross-section uniform.
2.2 Reasonable design of reinforcement ribs for die castings
For large-plane or thin-walled die-casting parts, their strength and rigidity are poor, and they are easy to deform. At this time, the use of stiffeners can effectively prevent the die-casting from shrinking and breaking, eliminating deformation, and enhancing the strength and rigidity of the die-casting. For structures such as, platform, reinforcement ribs can be used to improve the stress distribution and prevent root fracture. At the same time, the reinforcement ribs can assist the flow of molten metal and improve the filling performance of the casting. The thickness of the root of the stiffener is not greater than the thickness of the wall here, and the thickness is generally designed to be 0.8~2.0mm; the draft angle of the stiffener is generally designed to be 1°~3°, the higher the height, the smaller the draft angle; A fillet should be added to the root of the rib to avoid sharp changes in the section of the part, and at the same time to assist the flow of molten metal, reduce the stress concentration of the part, and increase the strength of the part. The fillet is generally close to the wall thickness here; the height of the rib generally does not exceed 5 of its thickness. The thickness of stiffeners is generally required to be uniform. If the design is too thin, the stiffener itself is easy to break, and if it is too thick, defects such as depressions and pores are easy to occur. Table 1 shows the relationship between the thickness of the rib and the wall thickness of the die casting.
2.3 Reasonable design of the angle of die casting
The role of the die casting slope is to reduce the friction between the casting and the mold cavity, making it easy to take out the casting; to ensure that the die casting surface is not strained, and it can extend the life of the mold. The inclination of the die is related to the height of the die casting. The greater the height, the smaller the inclination of the die. Under normal circumstances, the exit angle of the outer surface of the die-casting part is about 1/2 of the inner cavity exit angle, but in actual design, the inner and outer surface of the die-casting part can be designed to be the same in order to maintain the wall thickness. Uniformity, simplifying the structural design. For example, Table 2 is the reference value of the minimum draft angle of various alloy die castings, and Table 3 shows the relationship between the draft angle and depth of each die casting cavity.
Casting cavity depth/casting material | <6mm | 6-8mm | 8-10mm | 10-15mm | 15-20mm | 20-30mm | 30-60mm |
Zinc Alloy | 2°30’ | 2° | 1°45’ | 1°30’ | 1°15’ | 1° | 0°45’ |
Aluminum Alloy | 4° | 3°30’ | 3° | 2°30’ | 2° | 1°30’ | 1°15’ |
Copper Alloy | 5° | 4° | 3°30’ | 3° | 2°30’ | 2° | 1°30’ |
The relationship between the inclination of the cavity and the depth of the mold
2.4 Reasonable design of machining allowance
When designing die-casting parts, machining should be avoided as much as possible. Machining will destroy the dense layer on the surface of the part and affect the mechanical properties of the part; it will expose the internal pores of the die-casting part, affect the surface quality, and increase the cost of the part. When machining of die-casting parts cannot be avoided, the design with larger cutting volume should be avoided as much as possible, and the structure design should be as easy as possible for machining or reduce the machining area and reduce the machining cost.
The upper part of the die-casting part requires high dimensional accuracy, or some flat surface roughness requirements are high, and the die-casting process is difficult to meet the requirements. At this time, subsequent processing is required. For this part of the structure, the machining allowance should be reserved as much as possible when designing. The surface strength and hardness of die-casting parts are higher than that of the inside. Pay attention to keeping the surface density during machining, so the machining allowance should not be excessive. Excessive machining may cause pores and external surface defects. Table 4 is reserved for reference for machine plus margin.
Nominal size | 0-30 | 30-50 | 50-80 | 80-120 | 120-180 | 180-260 |
Margin per side | 0.3 | 0.4 | 0.5 | 0.6 | 0.7 | 0.8 |
2.5 Spraying design of aluminum alloy die castings
The surface spraying design of die-casting parts generally adopts the powder spraying process, the principle of which is electrostatic spraying: the paint is mainly polarized by the electrode, and then the object to be sprayed is charged with the opposite charge, and the powder is uniformly attached to the surface of the object under the action of the electric field force. . The characteristics of powder spraying process: powder electrostatic spraying will not cause air pollution, powder can be recycled to reduce the cost of material consumption, and the coating film has good acid, alkali and corrosion resistance.
Please keep the source and address of this article for reprinting: The Key Points Of Aluminum Alloy Die Casting Design
Minghe Casting Company are dedicated to manufacture and provide quality and high performance Casting Parts(metal die casting parts range mainly include Thin-Wall Die Casting,Hot Chamber Die Casting,Cold Chamber Die Casting),Round Service(Die Casting Service,Cnc Machining,Mold Making,Surface Treatment).Any custom Aluminum die casting, magnesium or Zamak/zinc die casting and other castings requirements are welcome to contact us.
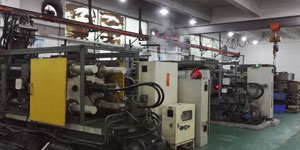
Under the control of ISO9001 and TS 16949,All processes are carried out through hundreds of advanced die casting machines, 5-axis machines, and other facilities, ranging from blasters to Ultra Sonic washing machines.Minghe not only has advanced equipment but also have professional team of experienced engineers,operators and inspectors to make the customer’s design come true.
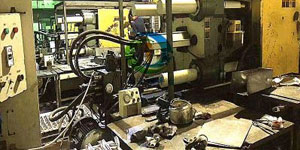
Contract manufacturer of die castings. Capabilities include cold chamber aluminum die casting parts from 0.15 lbs. to 6 lbs., quick change set up, and machining. Value-added services include polishing, vibrating, deburring, shot blasting, painting, plating, coating, assembly, and tooling. Materials worked with include alloys such as 360, 380, 383, and 413.
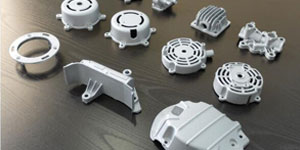
Zinc die casting design assistance/concurrent engineering services. Custom manufacturer of precision zinc die castings. Miniature castings, high pressure die castings, multi-slide mold castings, conventional mold castings, unit die and independent die castings and cavity sealed castings can be manufactured. Castings can be manufactured in lengths and widths up to 24 in. in +/-0.0005 in. tolerance.
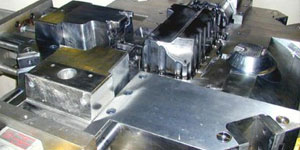
ISO 9001: 2015 certified manufacturer of die cast magnesium, Capabilities include high-pressure magnesium die casting up to 200 ton hot chamber & 3000 ton cold chamber, tooling design, polishing, molding, machining, powder & liquid painting, full QA with CMM capabilities, assembly, packaging & delivery.
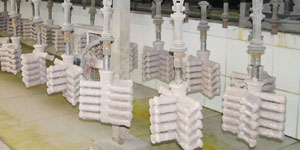
ITAF16949 certified. Additional Casting Service Include investment casting,sand casting,Gravity Casting, Lost Foam Casting,Centrifugal Casting,Vacuum Casting,Permanent Mold Casting,.Capabilities include EDI, engineering assistance, solid modeling and secondary processing.
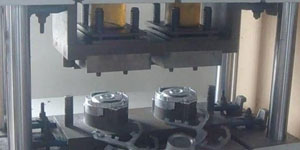
Casting Industries Parts Case Studies for: Cars, Bikes, Aircraft, Musical instruments, Watercraft, Optical devices, Sensors, Models, Electronic devices, Enclosures, Clocks, Machinery, Engines, Furniture, Jewelry, Jigs, Telecom, Lighting, Medical devices, Photographic devices, Robots, Sculptures, Sound equipment, Sporting equipment, Tooling, Toys and more.
What Can we help you do next?
∇ Go To Homepage For Die Casting China
→Casting Parts-Find out what we have done.
→Ralated Tips About Die Casting Services
By Minghe Die Casting Manufacturer |Categories: Helpful Articles |Material Tags: Aluminum Casting, Zinc Casting, Magnesium Casting, Titanium Casting, Stainless Steel Casting, Brass Casting,Bronze Casting,Casting Video,Company History,Aluminum Die Casting |Comments Off