The Main Points Of Stamping Die Overhaul
The purpose of mold maintenance is to quickly find out the problem points and solve them, so that the mold can be restored to its original state and can continue to produce products that meet the standards.
Products made from the same mold have the same size and shape, that is, part or all of the size and shape are completed after each process. Therefore, when the product has a variation, the processing station can be found according to the variation part. And repair it to restore it to its original state. If the result of the judgment is a design error, the design must be changed. Mold maintenance is based on this principle.
The following points can be used as reference for maintenance:
1. Measure the final product punched out, check the inspection standards to determine the variation, and check the LAYOUT to measure whether the size of the project is the same as the mold drawing, and whether the size is different. If necessary, measure the related projects before and after to be accurate. Determine the place and cause of the variation, and then implement countermeasures to solve it.
2. When you are unable to determine or propose countermeasures by yourself, you should ask others for advice, and don't act arbitrarily.
3. Too big hair
- Knife edge wear: re-grind
- The gap is too large: most of the sides are polished belts, and the brightness is low, so reduce the gap.
- The gap is too small: the secondary shear surface increases the gap.
- Conjunction cut: change the degree of joint or make a difference or reduce the gap.
- Too sharp à: The product à degree is less than 75 degrees to change the engineering or gap.
- The material is too hard: replace the material or increase the gap.
- Mold collapse à: Re-grind.
- Improper mold shell: local hairs or scratches. Re-calibrate or modify the mold.
4. Bite the mold
- Mould is loose: the movement of the punch or die exceeds the unilateral gap. Adjust the combination gap.
- Die tilt: The straightness of the punch or die is not correct, or there is foreign matter between the templates, which prevents the template from being flat. Reorganization or grinding correction.
- Template deformation: The template is not rigid or thick, or deformed by external force. Replace with a new template or correct the method of disassembly.
- Deformation of the mold base: the thickness of the mold base is not uniform or the force is uneven, and the straightness of the guide post and the guide sleeve varies. Grinding and correcting or refilling plastic steel or replacing the mold base or equalizing the force.
- Die interference: Whether the size of the punch or die is correct, whether the position is correct, whether the upper and lower die positioning is deviated, whether it will loosen after assembly, the accuracy of the punch is not correct, and the die frame is not correct.
- Punching shear deflection: The punch strength is not ì, the big and small punches are too close, the lateral force is not balanced, and the punch is semi-oblique. Strengthen the guiding and protection function of the peeling sloping board or increase the punch, short the small punch, increase the heel and heel length, and support and guide early. Pay attention to the length of the feed.
5. Size variation
- Knife edge wear: The hair is too large or the size becomes larger (cut shape); becomes smaller (punching); flatness is not good. Re-grind or replace the die.
- No guidance: The guiding pin or other positioning devices are not working, the feeder is not loosened or the guiding pin diameter is not correct, and the guiding cannot be corrected. The positioning block is worn and the feed distance is too long.
- The die is too short: the bend becomes larger, the inversion is not, and the forming is incomplete.
- No escape hole ì: Squeezed or injured or deformed. Clear the escape hole or increase the escape hole and depth.
- Ejection failure ì: poor feeding, bent strips, poor stripping, upper die pulling, extended ejection.
- Improper ejection: improper preparation of ejector pins, improper spring force or excessive ejection. Adjust the elastic force or change the position or the number of pins; pin grinding is short to match.
- Poor guide material: the length of the guide plate is not too large or the guide gap is too large, or the mold and the feeder are skewed or the distance between the mold and the feeder is too long.
- Blanking deformation: Some bending parts cannot allow the material to overlap and must be dropped every time, or the disc strain can be overcome by pressure pad or shearing à.
- Bending deformation: Extrusion at the upper bend; the proximal hole is deformed by tensile force, and the force is unevenly bent à the inclined punch is not long enough.
- Punching shear deformation: the material is distorted and uneven, the size increases or the eccentricity is asymmetrical.
- Impact deformation: The product blows out and the air pressure is too strong or the gravity falls and impacts deformation.
- Extrusion of floating chips: the extruding variation of waste materials floating up or fine chips remaining on the mold surface or foreign bodies.
- Improper material: Material width or thickness, improper material or material hardness, will also produce defects.
- Poor design: poor engineering arrangements and poor clearance settings are difficult to overcome unless the design is changed.
6. Mold damage
- Hot buried: The quenching temperature is too high or not, the tempering frequency and time are inappropriate, and the quenching method time cannot be grasped; the problem does not appear until after a period of use.
- Stamping and stacking: the material overlaps and continues to be stamped, usually because the stripping board is broken.
- Waste blockage: The blanking hole is not drilled or the size is not consistent, or it falls on the bed and is not cleaned in time. The punch and the lower template are more damaged.
- The punch is dropped: it is not sufficiently fixed or suspended, or the screw is too thin and the strength is not strong, or the punch is broken.
- No escape hole: The size or depth of the escape hole of the punch press plate is not enough, and the escape part of the punch and stripping plate is usually damaged because the stripping plate is damaged.
- Foreign matter entering: the product bounces back, the mold parts collapse and fall, the screw protrudes from the mold surface or other items enter the mold, which may damage the lower mold, the stripping plate or the punch, and the guide post.
- Assembling error: the parts are damaged due to the wrong position and direction.
- Spring factor: Insufficient spring force or breakage or unequal height sleeves make the stripping plate tilt, or the spring is not regularly configured, causing overlapping punching and damaging parts.
- Improper stamping: the working height is adjusted too low, the guide post loses oil, the strip is misfeed or half-filled, the peripheral equipment such as the feeding, unloading, and rewinding machine is damaged, the air pipe is not installed or not opened, the punch is abnormal, etc. The damage caused.
- Improper maintenance: The above-mentioned points have occurred due to the replacement but not replacement, or the screw is not tightened or restored to the original state.
Please keep the source and address of this article for reprinting:The Main Points Of Stamping Die Overhaul
Minghe Die Casting Company are dedicated to manufacture and provide quality and high performance Casting Parts(metal die casting parts range mainly include Thin-Wall Die Casting,Hot Chamber Die Casting,Cold Chamber Die Casting),Round Service(Die Casting Service,Cnc Machining,Mold Making,Surface Treatment).Any custom Aluminum die casting, magnesium or Zamak/zinc die casting and other castings requirements are welcome to contact us.
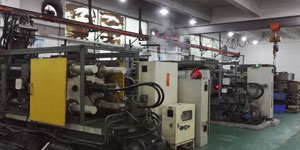
Under the control of ISO9001 and TS 16949,All processes are carried out through hundreds of advanced die casting machines, 5-axis machines, and other facilities, ranging from blasters to Ultra Sonic washing machines.Minghe not only has advanced equipment but also have professional team of experienced engineers,operators and inspectors to make the customer’s design come true.
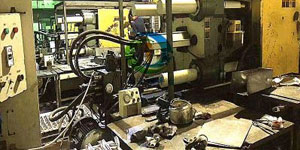
Contract manufacturer of die castings. Capabilities include cold chamber aluminum die casting parts from 0.15 lbs. to 6 lbs., quick change set up, and machining. Value-added services include polishing, vibrating, deburring, shot blasting, painting, plating, coating, assembly, and tooling. Materials worked with include alloys such as 360, 380, 383, and 413.
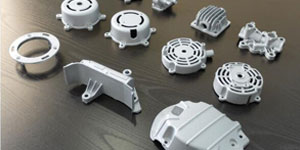
Zinc die casting design assistance/concurrent engineering services. Custom manufacturer of precision zinc die castings. Miniature castings, high pressure die castings, multi-slide mold castings, conventional mold castings, unit die and independent die castings and cavity sealed castings can be manufactured. Castings can be manufactured in lengths and widths up to 24 in. in +/-0.0005 in. tolerance.
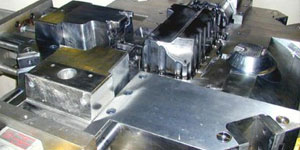
ISO 9001: 2015 certified manufacturer of die cast magnesium, Capabilities include high-pressure magnesium die casting up to 200 ton hot chamber & 3000 ton cold chamber, tooling design, polishing, molding, machining, powder & liquid painting, full QA with CMM capabilities, assembly, packaging & delivery.
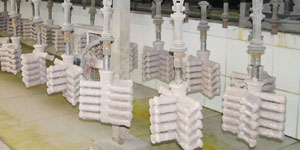
ITAF16949 certified. Additional Casting Service Include investment casting,sand casting,Gravity Casting, Lost Foam Casting,Centrifugal Casting,Vacuum Casting,Permanent Mold Casting,.Capabilities include EDI, engineering assistance, solid modeling and secondary processing.
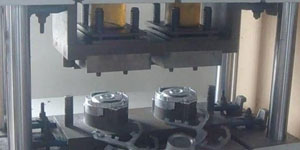
Casting Industries Parts Case Studies for: Cars, Bikes, Aircraft, Musical instruments, Watercraft, Optical devices, Sensors, Models, Electronic devices, Enclosures, Clocks, Machinery, Engines, Furniture, Jewelry, Jigs, Telecom, Lighting, Medical devices, Photographic devices, Robots, Sculptures, Sound equipment, Sporting equipment, Tooling, Toys and more.
What Can we help you do next?
∇ Go To Homepage For Die Casting China
→Casting Parts-Find out what we have done.
→Ralated Tips About Die Casting Services
By Minghe Die Casting Manufacturer |Categories: Helpful Articles |Material Tags: Aluminum Casting, Zinc Casting, Magnesium Casting, Titanium Casting, Stainless Steel Casting, Brass Casting,Bronze Casting,Casting Video,Company History,Aluminum Die Casting |Comments Off