The Main Technical Measures Of Low Cost Ironmaking
Introduction
With the rapid development of China's iron and steel industry, China's annual pig iron production reached 660 million tons in 2012, accounting for nearly 60% of the world's annual production. On the one hand, the supply of mineral resources is increasingly tight, and the prices of raw materials and fuels continue to rise; On the other hand, the contradiction of overcapacity is becoming increasingly prominent, and the market competition is becoming increasingly fierce. The profit space of iron and steel enterprises is gradually shrinking, and the situation of operation and development is becoming increasingly severe. Iron and steel enterprises rely on scientific management means and scientific and technological means to tap internal potential, optimize product structure, reduce system cost and improve enterprise efficiency. Scientific and technological means must be reflected by technological progress and technological innovation. Advanced technology is the guarantee of low-cost ironmaking.
Optimization of raw and fuel structure
The quality of raw material and fuel is the premise of blast furnace ironmaking production and the essence of concentrate technology; The cost of raw materials and fuels accounts for 2 / 3 of the cost of ironmaking. Therefore, it is necessary to rely on technological progress and innovation, adopt advanced technical means, optimize the composition and process technology of raw materials and fuels, and comprehensively analyze the cost performance of physicochemical properties, metallurgical properties, blast furnace operation and other factors of different composition of raw materials and fuels through relevant experiments and practices, so as to ensure and improve the level of concentrate, To achieve low cost ironmaking and obtain maximum economic benefits.
1.Optimization of coke blending structure
The role of coke in blast furnace smelting is charge skeleton, reducing agent, heating agent and carburizing. In today's large-scale blast furnace, high coal injection ratio smelting conditions, the role of coke skeleton is particularly important, not only to meet the requirements of cold mechanical strength, but also to meet the requirements of blast furnace for coke hot performance. The quality of coke is guaranteed by the amount of main coking coal, and the cost of coke is mainly reflected in coal blending. Therefore, relying on advanced technical means, optimizing coal preparation, coal blending and coking technology, and on the premise of ensuring the coke quality of blast furnace, it is an effective technical measure to reduce the coke cost by purchasing inferior coal or reducing the proportion of coking coal in coal blending.
2.Optimization of coal injection structure
Blast furnace coal injection technology has been widely used in modern blast furnace ironmaking to save coke and increase iron, reduce cost and increase efficiency, improve smelting process and promote smooth operation of blast furnace. With the shortage of traditional anthracite resources and high price, high volatile and explosive bituminous coal injection technology develops rapidly, and more and more blast furnaces begin to inject bituminous coal, lignite and other coal. Through mixing and matching of bituminous coal, lignite, lean coal, anthracite, Lantan and other coals, we can scientifically evaluate the cost performance of blended coal with various proportions, optimize the structure of coal injection and blending, improve the smelting process of blast furnace, and reduce the coke ratio, so as to achieve the purpose of reducing costs and improving technical and economic indicators.
3.Optimization of sinter blending structure
With the development of China's iron and steel industry, China's iron ore resources are increasingly scarce. There are many kinds of imported ores and Chinese minerals, with different prices and quality. Scientific and comprehensive evaluation of sintering performance and economic value of various iron ores, rational utilization of various iron ore resources at home and abroad, optimization of sinter mix structure, increase of consumption proportion of inferior low price ores, and improvement of sinter performance while reducing sinter cost are important technical issues we are facing.
In addition, in order to produce high-quality sinter with low slag ratio under the condition of low ore ratio, foreign iron and steel enterprises have proposed mebios (mosaic iron ore sintering) technology, carried out a large number of laboratory basic research, and achieved certain results. At present, there are industrial production examples at home and abroad.
Optimization of operation index parameters of blast furnace
With the development of blast furnace ironmaking technology and equipment, blast furnace operators, on the basis of concentrate technology, make full use of advanced technologies such as oxygen enrichment, high pressure, coal injection and high blast temperature, adjust stable and reasonable operation system, optimize blast furnace operation index parameters, maintain reasonable operation type of blast furnace, maintain stable and smooth operation of blast furnace, and improve technical and economic indexes of blast furnace, In order to realize the technical policy of "high efficiency, high quality, low consumption, long life and environmental protection" of modern blast furnace. In order to fully realize the technical policy of modern blast furnace, blast furnace operation must be changed from extensive type to fine type, scientific smelting concept must be established, operation concept must be changed, evaluation index must be optimized, low fuel ratio and low cost smelting must be realized, and both economic and social benefits can be obtained.
1. Optimization of smelting intensity index
Smelting intensity is an evaluation index of smelting intensity of blast furnace. Practice shows that it has a U-shaped curve relationship with coke ratio (or fuel ratio). The lowest point of the curve corresponds to the suitable smelting intensity under the lowest coke ratio. Increasing or decreasing smelting intensity will make coke ratio increase. However, with the improvement of the application level of advanced technologies such as concentrate, oxygen enrichment, high pressure, coal injection and high blast temperature, and the improvement of smelting conditions, the curve will move down to the right in varying degrees, the minimum coke ratio will gradually decrease, and the suitable smelting intensity will gradually increase (see Figure 1), and the utilization coefficient of blast furnace will be further improved. This is the reason why most people in the industry have long advocated adopting medium smelting intensity and adapting to smelting conditions.
Smelting intensity is a strengthening index based on volume utilization coefficient, which was introduced by China from the former Soviet Union in 1950s. It measures the strengthening degree of blast furnace by volume combustion intensity. To a certain extent, it misleads people to adopt extensive operation mode, and only uses more blast, more coke and more tapping as the index to measure the productivity of blast furnace; At the same time, due to historical reasons, in the period of strong demand for iron and steel, insufficient production capacity and large profit margin for iron and steel products, one-sided pursuit of high smelting intensity in order to achieve high volume utilization coefficient, mostly focusing on output, light energy consumption, heavy coefficient and light coke ratio, resulting in high fuel ratio for a long time. With the development of China's economic transformation, higher requirements are put forward for the iron and steel industry, and the corresponding evaluation standards also need to change.
Therefore, the method proposed by academician Xiang Zhongyong, which is based on the utilization coefficient of hearth area, is more scientific and in line with the essence of blast furnace smelting. The practice of Baosteel blast furnace strengthening by reducing the amount of gas per ton of iron belly shows that reducing fuel is the most effective way to reduce cost and increase efficiency. Increasing oxygen enrichment rate and top pressure is the right choice for strengthening blast furnace.
2. Optimization of coal injection ratio index
Coal injection is an important technical measure for energy saving and cost reduction in blast furnace ironmaking. The significance for blast furnace ironmaking lies in replacing coke with coal, reducing coke ratio, saving investment and energy consumption in coke production, and alleviating the contradiction of lack of main coking coal; At the same time, it can improve the smelting operation of blast furnace and promote the stable and smooth operation of blast furnace. Therefore, some enterprises blindly pursue high coal injection ratio regardless of their own wind temperature and concentrate level, resulting in excessive injection, reduction of replacement ratio and increase of fuel ratio, so that the carbon content in furnace dust even exceeds 50%.
According to the theory of economic coal injection ratio put forward by Professor Xu manxing, the economic coal injection ratio of a certain stage of the blast furnace should be calculated according to the lowest coke ratio, the lowest fuel ratio and the highest utilization coefficient. The premise of economic coal injection ratio is that the increase of coal injection ratio does not cause the increase of fuel ratio and carbon content of blast furnace dust (normally ≤ 20%).
Concluding remarks
Low cost ironmaking is an inevitable way for iron and steel enterprises to survive and develop under the situation of increasingly tense raw and fuel resources, obvious overcapacity and severe requirements for energy conservation and emission reduction. The specific measures are: relying on advanced technology, optimizing the structure of raw and fuel, improving the level of concentrate, reducing the cost of raw and fuel; Optimize the operation index parameters of blast furnace, establish a scientific concept of smelting intensification, overcome the one-sided pursuit of high production index (high smelting intensity, high utilization coefficient, high coal injection ratio, etc.), maintain the bosh gas volume suitable for smelting conditions, achieve the high efficiency of blast furnace, maintain the economic coal injection ratio suitable for smelting conditions, and achieve the purpose of increasing replacement ratio and reducing fuel ratio.
Please keep the source and address of this article for reprinting: The Main Technical Measures Of Low Cost Ironmaking
Minghe Die Casting Company are dedicated to manufacture and provide quality and high performance Casting Parts(metal die casting parts range mainly include Thin-Wall Die Casting,Hot Chamber Die Casting,Cold Chamber Die Casting),Round Service(Die Casting Service,Cnc Machining,Mold Making,Surface Treatment).Any custom Aluminum die casting, magnesium or Zamak/zinc die casting and other castings requirements are welcome to contact us.
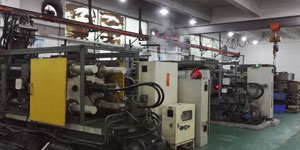
Under the control of ISO9001 and TS 16949,All processes are carried out through hundreds of advanced die casting machines, 5-axis machines, and other facilities, ranging from blasters to Ultra Sonic washing machines.Minghe not only has advanced equipment but also have professional team of experienced engineers,operators and inspectors to make the customer’s design come true.
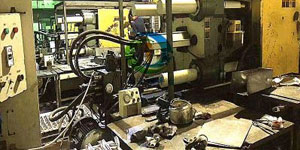
Contract manufacturer of die castings. Capabilities include cold chamber aluminum die casting parts from 0.15 lbs. to 6 lbs., quick change set up, and machining. Value-added services include polishing, vibrating, deburring, shot blasting, painting, plating, coating, assembly, and tooling. Materials worked with include alloys such as 360, 380, 383, and 413.
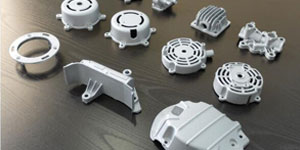
Zinc die casting design assistance/concurrent engineering services. Custom manufacturer of precision zinc die castings. Miniature castings, high pressure die castings, multi-slide mold castings, conventional mold castings, unit die and independent die castings and cavity sealed castings can be manufactured. Castings can be manufactured in lengths and widths up to 24 in. in +/-0.0005 in. tolerance.
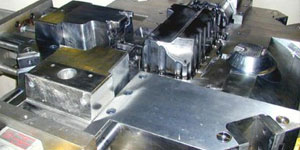
ISO 9001: 2015 certified manufacturer of die cast magnesium, Capabilities include high-pressure magnesium die casting up to 200 ton hot chamber & 3000 ton cold chamber, tooling design, polishing, molding, machining, powder & liquid painting, full QA with CMM capabilities, assembly, packaging & delivery.
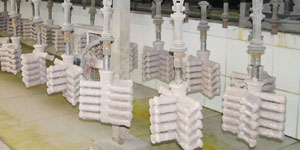
ITAF16949 certified. Additional Casting Service Include investment casting,sand casting,Gravity Casting, Lost Foam Casting,Centrifugal Casting,Vacuum Casting,Permanent Mold Casting,.Capabilities include EDI, engineering assistance, solid modeling and secondary processing.
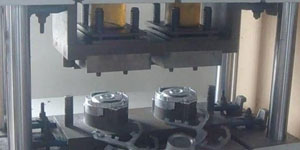
Casting Industries Parts Case Studies for: Cars, Bikes, Aircraft, Musical instruments, Watercraft, Optical devices, Sensors, Models, Electronic devices, Enclosures, Clocks, Machinery, Engines, Furniture, Jewelry, Jigs, Telecom, Lighting, Medical devices, Photographic devices, Robots, Sculptures, Sound equipment, Sporting equipment, Tooling, Toys and more.
What Can we help you do next?
∇ Go To Homepage For Die Casting China
→Casting Parts-Find out what we have done.
→Ralated Tips About Die Casting Services
By Minghe Die Casting Manufacturer |Categories: Helpful Articles |Material Tags: Aluminum Casting, Zinc Casting, Magnesium Casting, Titanium Casting, Stainless Steel Casting, Brass Casting,Bronze Casting,Casting Video,Company History,Aluminum Die Casting |Comments Off