The Maintenance Method Of Die Casting Mold
Die casting die belongs to a kind of casting liquid die forging and special die casting die forging machine. For die casting, die casting material, die casting machine and die are indispensable. In order to improve the production efficiency, brand quality and high economic benefits, and to extend the service life of die casting die, the use and maintenance of die casting die is very important.
Correct use and maintenance of die casting die
1. The rapid cooling and heating of the mould should be reduced as far as possible, and continuous production should be carried out as far as possible. High speed injection is strictly prohibited in the cold mold state.
In the process of die-casting, the die-casting die has been in the reciprocating fatigue state of hot expansion and cold shrinkage, and the temperature of the mold cavity has been changing from 160 ℃ to 350 ℃. The die is rapidly cooled and hot, and the hot expansion and contraction are not stopped, resulting in the fatigue damage of the die. However, when the production starts in the cold mold state, the mold temperature starts to rise from the low temperature, the temperature difference increases, the mold expansion and contraction increases, and the mold fatigue increases correspondingly, which will accelerate the mold damage and shorten the mold life. Therefore, continuous production should be carried out as far as possible in die-casting production to reduce the rapid cooling and heating of the die as far as possible, so as to prolong the life of the die.
In addition, in the cold mold state, the mold does not reach the normal production temperature, and the gap between the parts of the mold is relatively large. In this case, it is strictly forbidden to open high-speed injection and pressurization. Otherwise, the clearance parts of the die, including slide block, ejector pin hole and so on, are easy to enter the aluminum sheet, thus damaging the mold and affecting the die life.
2. Try to reduce the injection speed, specific pressure and die impact.
In die casting production, the injection speed not only affects the filling speed and gate speed, but also increases the impact peak value when the injection speed is high. Therefore, the injection speed is high, the injection gate speed is fast, the erosion of the mold will be intensified, the impact peak value will be increased, the impact force of the mold will be increased, and the mold life will be greatly reduced. Therefore, when we adjust the die-casting process, we should reduce the injection speed as far as possible under the condition of ensuring the product quality, which is very important to improve the die life and the economic benefits of die-casting enterprises. At present, the advanced die-casting machine is equipped with injection brake device, which is very beneficial to reduce the impact peak value, reduce the impact force borne by the mold, and improve the die life.
The injection specific pressure is also an important parameter in the die casting process. According to the quality requirements and characteristics of the casting, the injection specific pressure is generally in the range of 400-900 kg / cm2. When the temperature exceeds 900 kg / cm2, it has little effect on the internal quality of castings. However, if the injection pressure is too high, it will not only increase the mold expansion force, but also make the expansion force exceed the locking force of the machine tool, resulting in aluminum channeling. At the same time, if the die bears large bulging force, it will also damage the mold or shorten the mold life. Therefore, in die-casting production, we should pay more attention to the injection rate than to the injection rate. As the injection rate is not easy to observe, it is often ignored. In fact, the specific pressure of injection is an important parameter in the die casting process, which not only affects the quality of the casting, but also has a great impact on the die life. This point should be paid more attention by die casting enterprises.
3. In the process of using the mould, the blister and aluminum skin should be cleaned up in time to prevent the mold from being damaged.
In the use of the mold, the mold often appears wrappings and aluminum skin due to various reasons. At this time, it must be cleaned in time, otherwise the mold will be damaged if the production continues. Especially in the sliding block, if the slide enters into the aluminum sheet, the sliding block will collapse and be damaged due to the large clamping force of the die casting machine. Therefore, in case of such problems, it is necessary to clean the mold in time, find out the causes and repair the mold in time. Otherwise, the service life of the die will be seriously affected if the die is damaged.
4. The pouring temperature of molten aluminum should be reduced as much as possible to improve the service life of the die.
The pouring temperature of liquid aluminum in die casting not only affects the quality of casting, but also affects the service life of die casting die. In general, the pouring temperature of liquid aluminum is 630-720 degrees. For different parts, we should choose lower pouring temperature as far as possible, which can not only save energy, but also prolong the service life of die casting die. Because the higher the temperature of liquid aluminum, the greater the erosion of the mold, the greater the range of temperature field changes, the greater the thermal expansion and contraction, the greater the fatigue of the mold, the more easily damaged. Therefore, it is beneficial to prolong the service life of die casting die by properly reducing the pouring temperature of molten aluminum.
5. Strengthen the maintenance of the mold, regular maintenance, regular tempering of the mold cavity stress treatment.
Die casting die has been in high pressure, high speed, high temperature continuous production, the use conditions are relatively bad. In the process of using, the mold will produce damage or hidden trouble. Therefore, it is very important to strengthen the maintenance of the mold, regularly maintain the mold, replace the damaged parts, replace the vulnerable parts, clean the slide way, ejector pin hole, etc. it is very important to ensure the reliability of the mold in the die-casting production, and also can extend the service life of the mold.
At the same time, because the die-casting die is constantly impacted, expanding and shrinking continuously, new internal stress will be produced. If it is not eliminated in time, the die surface is easy to crack or crack. Therefore, it is also an important means to prolong the life of the die by means of stress relief tempering regularly. Generally, the first tempering should be carried out after 3000-5000 mold times after the mold is put into use. In the future, according to the use of the situation, generally every 10000 mold production, the mold cavity to carry out stress tempering, which can greatly extend the service life of the mold.
Please keep the source and address of this article for reprinting:The Maintenance Method Of Die Casting Mold
Minghe Die Casting Company are dedicated to manufacture and provide quality and high performance Casting Parts(metal die casting parts range mainly include Thin-Wall Die Casting,Hot Chamber Die Casting,Cold Chamber Die Casting),Round Service(Die Casting Service,Cnc Machining,Mold Making,Surface Treatment).Any custom Aluminum die casting, magnesium or Zamak/zinc die casting and other castings requirements are welcome to contact us.
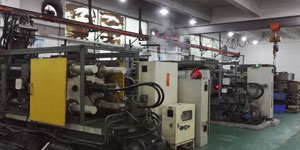
Under the control of ISO9001 and TS 16949,All processes are carried out through hundreds of advanced die casting machines, 5-axis machines, and other facilities, ranging from blasters to Ultra Sonic washing machines.Minghe not only has advanced equipment but also have professional team of experienced engineers,operators and inspectors to make the customer’s design come true.
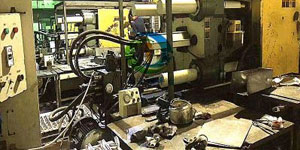
Contract manufacturer of die castings. Capabilities include cold chamber aluminum die casting parts from 0.15 lbs. to 6 lbs., quick change set up, and machining. Value-added services include polishing, vibrating, deburring, shot blasting, painting, plating, coating, assembly, and tooling. Materials worked with include alloys such as 360, 380, 383, and 413.
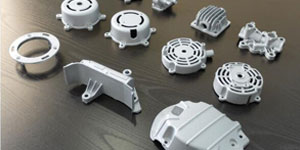
Zinc die casting design assistance/concurrent engineering services. Custom manufacturer of precision zinc die castings. Miniature castings, high pressure die castings, multi-slide mold castings, conventional mold castings, unit die and independent die castings and cavity sealed castings can be manufactured. Castings can be manufactured in lengths and widths up to 24 in. in +/-0.0005 in. tolerance.
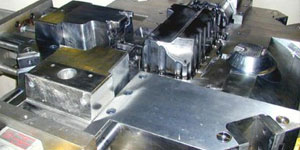
ISO 9001: 2015 certified manufacturer of die cast magnesium, Capabilities include high-pressure magnesium die casting up to 200 ton hot chamber & 3000 ton cold chamber, tooling design, polishing, molding, machining, powder & liquid painting, full QA with CMM capabilities, assembly, packaging & delivery.
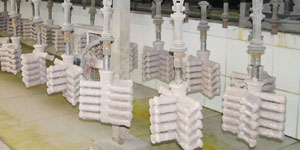
ITAF16949 certified. Additional Casting Service Include investment casting,sand casting,Gravity Casting, Lost Foam Casting,Centrifugal Casting,Vacuum Casting,Permanent Mold Casting,.Capabilities include EDI, engineering assistance, solid modeling and secondary processing.
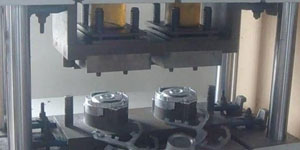
Casting Industries Parts Case Studies for: Cars, Bikes, Aircraft, Musical instruments, Watercraft, Optical devices, Sensors, Models, Electronic devices, Enclosures, Clocks, Machinery, Engines, Furniture, Jewelry, Jigs, Telecom, Lighting, Medical devices, Photographic devices, Robots, Sculptures, Sound equipment, Sporting equipment, Tooling, Toys and more.
What Can we help you do next?
∇ Go To Homepage For Die Casting China
→Casting Parts-Find out what we have done.
→Ralated Tips About Die Casting Services
By Minghe Die Casting Manufacturer |Categories: Helpful Articles |Material Tags: Aluminum Casting, Zinc Casting, Magnesium Casting, Titanium Casting, Stainless Steel Casting, Brass Casting,Bronze Casting,Casting Video,Company History,Aluminum Die Casting |Comments Off