The Maintenance Of Automobile Molds
The first-level maintenance of the mold refers to the operation and daily maintenance of the mold during the production, and the main content is cleaning, lubrication and inspection.
1. Maintenance During Mold Loading
The upper and lower surfaces of the mold should be cleaned before the mold is installed to ensure that the mold mounting surface and the press working table are not crushed and the parallelism of the upper and lower mounting surfaces of the mold manufacturing during production.
After the mold is installed, the mold is opened, and all parts of the mold are cleaned, especially the guide mechanism. For the surface mold, the surface of the mold is cleaned to ensure the quality of the part. Lubricate the sliding parts of the mold and apply grease. Inspection of all parts of the mold, especially safety parts. Such as: safety side pins, safety screws, side guards, punching waste passages, etc.
2. Maintenance In Production
During production, oil the corresponding parts of the mold regularly. Such as: the pressing ring and fillet of the drawing die; the knife edge of the trimming die; the flanging knife block part, etc.
The small hole waste channel of the trimming punching die is cleaned up regularly.
3.Maintenance After Production
- After the production is over, a comprehensive inspection of the mold is required.
- The mold is thoroughly cleaned to ensure the cleanliness of the mold.
- Clean up the waste in the mold to ensure that there is no waste in the waste box.
- The use status of the mold and the situation after use are truthfully reported to the mold voucher.
Secondary Maintenance Of Mold
The secondary maintenance of the mold refers to the regular systematic maintenance of the mold based on the technical status and complexity of the mold. This maintenance work is completed by mold repair personnel, and records are made according to the maintenance situation. The following describes the requirements and methods of the second warranty for different parts.
- Convex and concave molds of drawing die: The main problem of the convex and concave dies of the drawing die is the roughening and the pressing pits of the molding surface. During maintenance, the rounded corners of the mold are mainly polished. If there is a crater, repair the mold and then repair it.
- Guide parts (guide posts, guide sleeves and guide plates, etc.): the mold will have pull marks during work. The main causes are dirty lubricating oil and guide gap deviation. The pulling marks of the guide parts are eliminated by polishing after smoothing with oilstone.
- Trimming edge: The edge part of the mold is prone to chipping and edge collapse during the use of the mold. At this time, the damaged knife edge of the mold should be repaired and repaired.
- Springs and other elastic parts: During use, the spring is one of the most vulnerable parts of the mold, and it usually breaks and deforms. The method adopted is to replace, but during the replacement process, you must pay attention to the specifications and models of the springs. The specifications and models of the springs are determined by the three items of color, outer diameter and length. Only when these three items are the same can they be replaced.
- Punches and sleeves: most of the punches and sleeves used on the mold are made of standard parts, and the punches are prone to breakage, bend and gnaw during the use of the mold. Cushioning is generally broken. The damage of the punch and sleeve is generally replaced with parts of the same specification. The parameters of the punch mainly include the size of the working part, the size of the installation part, and the length dimension.
- Fastening parts: Check whether the fastening parts are loose or damaged. The method adopted is to find parts of the same specification for replacement.
- Pressing and unloading parts: pressing parts such as pressing plates, uniglue, etc., unloading parts such as unloading plates, pneumatic ejector devices, etc. During maintenance, check the assembly relationship of each part and whether there is damage, and repair the damaged part.
Please keep the source and address of this article for reprinting: The Maintenance Of Automobile Molds
Minghe Die Casting Company are dedicated to manufacture and provide quality and high performance Casting Parts(metal die casting parts range mainly include Thin-Wall Die Casting,Hot Chamber Die Casting,Cold Chamber Die Casting),Round Service(Die Casting Service,Cnc Machining,Mold Making,Surface Treatment).Any custom Aluminum die casting, magnesium or Zamak/zinc die casting and other castings requirements are welcome to contact us.
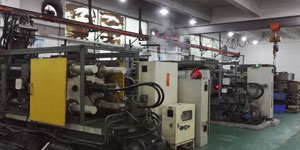
Under the control of ISO9001 and TS 16949,All processes are carried out through hundreds of advanced die casting machines, 5-axis machines, and other facilities, ranging from blasters to Ultra Sonic washing machines.Minghe not only has advanced equipment but also have professional team of experienced engineers,operators and inspectors to make the customer’s design come true.
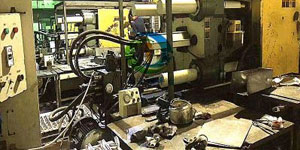
Contract manufacturer of die castings. Capabilities include cold chamber aluminum die casting parts from 0.15 lbs. to 6 lbs., quick change set up, and machining. Value-added services include polishing, vibrating, deburring, shot blasting, painting, plating, coating, assembly, and tooling. Materials worked with include alloys such as 360, 380, 383, and 413.
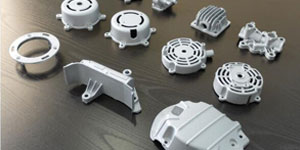
Zinc die casting design assistance/concurrent engineering services. Custom manufacturer of precision zinc die castings. Miniature castings, high pressure die castings, multi-slide mold castings, conventional mold castings, unit die and independent die castings and cavity sealed castings can be manufactured. Castings can be manufactured in lengths and widths up to 24 in. in +/-0.0005 in. tolerance.
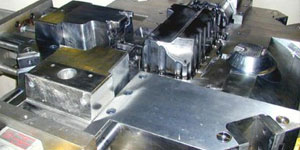
ISO 9001: 2015 certified manufacturer of die cast magnesium, Capabilities include high-pressure magnesium die casting up to 200 ton hot chamber & 3000 ton cold chamber, tooling design, polishing, molding, machining, powder & liquid painting, full QA with CMM capabilities, assembly, packaging & delivery.
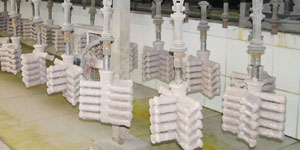
ITAF16949 certified. Additional Casting Service Include investment casting,sand casting,Gravity Casting, Lost Foam Casting,Centrifugal Casting,Vacuum Casting,Permanent Mold Casting,.Capabilities include EDI, engineering assistance, solid modeling and secondary processing.
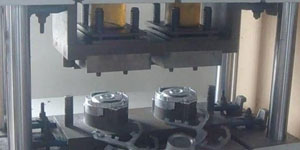
Casting Industries Parts Case Studies for: Cars, Bikes, Aircraft, Musical instruments, Watercraft, Optical devices, Sensors, Models, Electronic devices, Enclosures, Clocks, Machinery, Engines, Furniture, Jewelry, Jigs, Telecom, Lighting, Medical devices, Photographic devices, Robots, Sculptures, Sound equipment, Sporting equipment, Tooling, Toys and more.
What Can we help you do next?
∇ Go To Homepage For Die Casting China
→Casting Parts-Find out what we have done.
→Ralated Tips About Die Casting Services
By Minghe Die Casting Manufacturer |Categories: Helpful Articles |Material Tags: Aluminum Casting, Zinc Casting, Magnesium Casting, Titanium Casting, Stainless Steel Casting, Brass Casting,Bronze Casting,Casting Video,Company History,Aluminum Die Casting |Comments Off