The Manufacturing Technology Of Steel Castings
For machine parts requiring higher strength, plasticity and toughness, steel castings are required. The output of steel castings is second only to cast iron, accounting for about 15% of the total output of castings.
According to chemical composition, cast steel can be divided into two categories: carbon cast steel and alloy cast steel. Among them, carbon cast steel is the most widely used, accounting for more than 80% of the total output of cast steel.
1.Carbon Cast Steel
Generally, low-carbon steel ZG15 has a higher melting point and poor casting performance, and is only used to manufacture motor parts or carburized parts; medium-carbon steel ZG25~ZG45 have comprehensive properties higher than all kinds of cast iron, that is, high strength and excellent performance. Due to its plasticity and toughness, it is suitable for manufacturing parts with complex shapes, high strength and toughness requirements, such as train wheels, forging hammer stands and anvils, rolls and high-pressure valves. It is the most widely used type of carbon cast steel; The high-carbon steel ZG55 has a low melting point, and its casting performance is better than that of medium-carbon steel, but its plasticity and toughness are poor, and it is only used to manufacture a few wear-resistant parts.
2.Alloy Cast Steel
According to the total amount of alloying elements, alloy cast steel can be divided into two categories: low alloy steel and high alloy steel.
- Low-alloy cast steel, our country mainly uses manganese series, manganese silicon series and chromium series. Such as ZG40Mn, ZG30MnSi1, ZG30Cr1MnSi1, etc. It is used to manufacture parts such as gears, hydraulic press working cylinders and hydraulic turbine rotors, and ZG40Cr1 is commonly used to manufacture important stress parts such as high-strength gears and high-strength shafts.
- High alloy cast steel, with special properties such as wear resistance, heat resistance or corrosion resistance. For example, high manganese steel ZGMn13 is a kind of anti-wear steel, mainly used to manufacture parts used under dry friction working conditions, such as the front wall and grab teeth of excavators, crawlers of tractors and tanks, etc.; chromium-nickel stainless steel ZG1Cr18Ni9 and chromium stainless steel ZG1Cr13 and ZGCr28, etc., have high corrosion resistance to nitric acid, and are mainly used to manufacture chemical, petroleum, chemical fiber and food equipment parts.
Casting process characteristics of cast steel
The mechanical properties of cast steel are higher than cast iron, but its casting properties are worse than cast iron. Because of the high melting point of cast steel, the molten steel is easy to oxidize, the fluidity of molten steel is poor, and the shrinkage is large. Its body shrinkage rate is 10-14% and linear shrinkage is 1.8-2.5%. In order to prevent defects such as insufficient pouring, cold separation, shrinkage and porosity, cracks and sand sticking of steel castings, more complicated process measures than cast iron must be adopted:
- 1. Due to the poor fluidity of molten steel, in order to prevent cold barriers and insufficient pouring of steel castings, the wall thickness of steel castings should not be less than 8mm; the structure of the pouring system should be simple and the cross-sectional size should be larger than that of cast iron; dry casting is used Or hot mold; appropriately increase the pouring temperature, generally 1520°~1600°C, because the pouring temperature is high, the molten steel has a high degree of overheating, and the liquid state is maintained for a long time, and the fluidity can be improved. However, if the pouring temperature is too high, it will cause defects such as coarse grains, thermal cracks, pores and sand sticking. Therefore, the casting temperature of small, thin-walled and complex-shaped castings is about the melting point temperature of steel + 150°C; the casting temperature of large, thick-walled castings is about 100°C higher than its melting point.
- 2. As the shrinkage of cast steel greatly exceeds that of cast iron, in order to prevent shrinkage cavities and shrinkage defects in castings, most of the casting processes adopt measures such as risers, chilled iron, and subsidies to achieve sequential solidification.In addition, in order to prevent the occurrence of shrinkage cavities, shrinkage porosity, pores and cracks in steel castings, the wall thickness should be uniform, sharp corners and right-angle structures should be avoided, sawdust is added to the casting sand, coke is added to the core, and Hollow cores and oil sand cores are used to improve the retreatability and air permeability of sand molds or cores. The melting point of cast steel is high, and its casting temperature is correspondingly high. The interaction between molten steel and mold material at high temperature can easily produce sticky sand defects. Therefore, artificial quartz sand with higher refractoriness should be used as the mold, and the surface of the mold should be brushed with a coating made of quartz powder or zirconium sand powder. In order to reduce the gas source, improve the fluidity of molten steel and the strength of the mold, most of the steel castings are cast in dry or quick-drying molds, such as CO2 hardened sodium silicate sand molds.
- 3. Heat treatment of steel castings:All steel castings should be used after heat treatment. Because there are casting defects such as porosity, cracks, shrinkage cavity and shrinkage porosity, coarse grains, uneven structure and residual internal stress in the steel castings in the as-cast state, the strength, especially the plasticity and toughness of the steel castings are greatly reduced.In order to refine the grain, uniform structure and eliminate internal stress, steel castings must be normalized or annealed. Normalized steel has higher mechanical properties and lower cost than annealed steel, so it has more applications. However, because normalizing treatment will cause larger internal stress than annealing, it is only suitable for steel castings with a carbon content of less than 0.35%. Because low-carbon steel castings have good plasticity, they are not easy to crack during cooling. In order to reduce internal stress, steel castings should be tempered at high temperature after normalizing. For steel castings with carbon content ≥ 0.35%, complex structure and easy to crack, only annealing treatment can be carried out. Steel castings should not be quenched, otherwise they will easily crack.
- 4. the melting of cast steel:The smelting of cast steel generally uses open hearth furnaces, electric arc furnaces and induction furnaces. The open hearth is characterized by its large capacity, the use of scrap steel as raw material, the ability to accurately control the composition of steel and the ability to smelt high-quality steel and low-alloy steel. It is mostly used for smelting molten steel for large steel castings with high quality requirements.
The three-phase electric arc furnace is easy to start and stop the furnace, can ensure the composition and quality of the molten steel, the requirements for the charge are not very strict, and it is easy to heat up, so it can make high-quality steel, high-grade alloy steel and special steel, etc. It is a production molding Common equipment for steel castings.
In addition, the power frequency or intermediate frequency induction furnace can be used to smelt various high-grade alloy steels and steels with extremely low carbon content. The induction furnace has fast smelting speed, low alloy element burning loss, low energy consumption, and high quality of molten steel, that is, low impurity content and few inclusions. It is suitable for small steel casting workshops.
Please keep the source and address of this article for reprinting:The Manufacturing Technology Of Steel Castings
Minghe Die Casting Company are dedicated to manufacture and provide quality and high performance Casting Parts(metal die casting parts range mainly include Thin-Wall Die Casting,Hot Chamber Die Casting,Cold Chamber Die Casting),Round Service(Die Casting Service,Cnc Machining,Mold Making,Surface Treatment).Any custom Aluminum die casting, magnesium or Zamak/zinc die casting and other castings requirements are welcome to contact us.
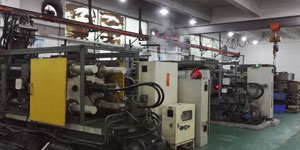
Under the control of ISO9001 and TS 16949,All processes are carried out through hundreds of advanced die casting machines, 5-axis machines, and other facilities, ranging from blasters to Ultra Sonic washing machines.Minghe not only has advanced equipment but also have professional team of experienced engineers,operators and inspectors to make the customer’s design come true.
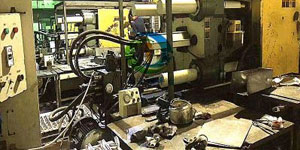
Contract manufacturer of die castings. Capabilities include cold chamber aluminum die casting parts from 0.15 lbs. to 6 lbs., quick change set up, and machining. Value-added services include polishing, vibrating, deburring, shot blasting, painting, plating, coating, assembly, and tooling. Materials worked with include alloys such as 360, 380, 383, and 413.
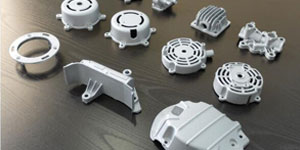
Zinc die casting design assistance/concurrent engineering services. Custom manufacturer of precision zinc die castings. Miniature castings, high pressure die castings, multi-slide mold castings, conventional mold castings, unit die and independent die castings and cavity sealed castings can be manufactured. Castings can be manufactured in lengths and widths up to 24 in. in +/-0.0005 in. tolerance.
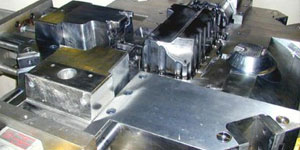
ISO 9001: 2015 certified manufacturer of die cast magnesium, Capabilities include high-pressure magnesium die casting up to 200 ton hot chamber & 3000 ton cold chamber, tooling design, polishing, molding, machining, powder & liquid painting, full QA with CMM capabilities, assembly, packaging & delivery.
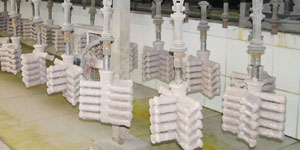
ITAF16949 certified. Additional Casting Service Include investment casting,sand casting,Gravity Casting, Lost Foam Casting,Centrifugal Casting,Vacuum Casting,Permanent Mold Casting,.Capabilities include EDI, engineering assistance, solid modeling and secondary processing.
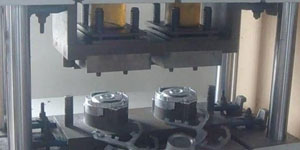
Casting Industries Parts Case Studies for: Cars, Bikes, Aircraft, Musical instruments, Watercraft, Optical devices, Sensors, Models, Electronic devices, Enclosures, Clocks, Machinery, Engines, Furniture, Jewelry, Jigs, Telecom, Lighting, Medical devices, Photographic devices, Robots, Sculptures, Sound equipment, Sporting equipment, Tooling, Toys and more.
What Can we help you do next?
∇ Go To Homepage For Die Casting China
→Casting Parts-Find out what we have done.
→Ralated Tips About Die Casting Services
By Minghe Die Casting Manufacturer |Categories: Helpful Articles |Material Tags: Aluminum Casting, Zinc Casting, Magnesium Casting, Titanium Casting, Stainless Steel Casting, Brass Casting,Bronze Casting,Casting Video,Company History,Aluminum Die Casting |Comments Off