The Material Forming Process Of Custom Mechanical Parts
With the advancement of science and technology, in the aerospace and computer fields, some parts that require particularly high machining accuracy and surface roughness require precision machining and super finishing. The dimensional accuracy achieved by precision and ultra-precision machining can reach sub-micron or even nanometer level. The machining methods of these mechanical parts include ultra-precision turning and ultra-precision grinding.
Machining parts machining material forming manufacturing process mostly uses models to make raw materials into parts or blanks. During the material forming process, the shape, size, organizational state, and even the combined state of the raw materials will change. Since the forming accuracy is generally not high, the material forming manufacturing process is often used to manufacture the blank. It can also be used to manufacture parts with complex shapes but not very demanding precision. The production efficiency of the material forming process is high. Commonly used forming processes include casting, forging, powder metallurgy and so on.
Casting is a process in which liquid metal is poured into a mold cavity suitable for the shape and size of the part, and the blank or part is obtained after cooling and solidification. The basic technological process is modeling, smelting, pouring, cleaning and so on. Due to the mold filling ability, shrinkage and other factors during alloy casting, the castings may have defects such as uneven structure, shrinkage, thermal stress, and deformation, making the accuracy, surface quality, and mechanical properties of the castings poor. Nevertheless, due to strong adaptability and low production cost, casting machining is still widely used. The shape is complex, especially the rough part with complex inner cavity is often used for casting.
At present, the commonly used casting methods in production include ordinary sand casting, investment casting, metal mold casting, pressure casting, low pressure casting, centrifugal casting, etc. Among them, ordinary sand casting is the most widely used.
Forging of mechanical parts machining and sheet metal stamping are collectively referred to as forging. Forging is the use of forging equipment to apply external force to the heated metal for plastic deformation to form a part blank with a certain shape, size and structure. The internal structure of the forged blank is dense and uniform. The metal streamline distribution is reasonable, which improves the strength of the parts. Therefore, forging is often used to manufacture blanks for parts that require high comprehensive mechanical properties.
Forging can be divided into free forging, model forging and tire die forging.
Free forging is to place the metal between the upper and lower abutment irons to plastically deform the metal, and use the law of free flow to form. The forming efficiency is low and the precision is low. Generally used to produce forgings with small batch sizes and simple shapes.
Model forging is to place metal in the die cavity of a forging die to deform. The plastic flow of the metal is restricted by the die cavity. The forming efficiency is high, the precision is high, and the metal streamline distribution is more reasonable. However, due to the high cost of mold manufacturing, it is usually used for mass production. Compared with free forging, model forging requires a large forging force and cannot be used for forging large forgings.
Tire mold forging is to forge metal using tire molds on free forging equipment. Tire molds are simple to manufacture, low cost, and convenient to form, but they have low forming accuracy. They are often used to produce small forgings with low accuracy requirements.
Machine parts machining sheet metal stamping is to use a die on a press to punch the sheet metal into parts of various shapes and sizes. Stamping machining has extremely high productivity and high machining accuracy, and its machining forms include punching, bending, deep drawing, forming and so on. Blanking is to punch the sheet into various flat parts. Bending, deep drawing and other forming processes stamp the sheet metal into various three-dimensional parts. Sheet metal stamping is widely used in electrical products, light industrial products, and automobile manufacturing.
Powder metallurgy is a process in which metal powder or a mixture of metal and non-metal powder is used as a raw material to produce certain metal products or metal materials through mold pressing and sintering processes. It can not only produce special metal materials, but also produce metal parts with little and no cutting machining. The material utilization rate of powder metallurgy products can reach 95%, which can greatly reduce the input of cutting machining and reduce the production cost. Therefore, it is increasingly widely used in mechanical manufacturing. Due to the high price of the powder raw materials used in powder metallurgy, the powder has poor fluidity during forming, and the shape and size of the parts are subject to certain restrictions. There are a certain amount of tiny pores in the powder metallurgy parts, the strength of which is about 20%-30% lower than that of castings or forgings, and the plasticity and toughness are also poor.
The technological process of powder metallurgy production includes powder preparation, compounding, pressing and forming, sintering, shaping and so on. Among them, the powder preparation and mixing process are usually completed by the manufacturer that provides the powder.
Please keep the source and address of this article for reprinting:The Material Forming Process Of Custom Mechanical Parts
Minghe Die Casting Company are dedicated to manufacture and provide quality and high performance Casting Parts(metal die casting parts range mainly include Thin-Wall Die Casting,Hot Chamber Die Casting,Cold Chamber Die Casting),Round Service(Die Casting Service,Cnc Machining,Mold Making,Surface Treatment).Any custom Aluminum die casting, magnesium or Zamak/zinc die casting and other castings requirements are welcome to contact us.
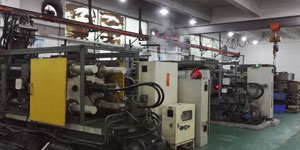
Under the control of ISO9001 and TS 16949,All processes are carried out through hundreds of advanced die casting machines, 5-axis machines, and other facilities, ranging from blasters to Ultra Sonic washing machines.Minghe not only has advanced equipment but also have professional team of experienced engineers,operators and inspectors to make the customer’s design come true.
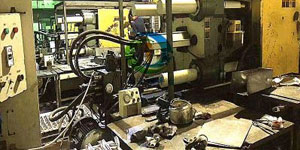
Contract manufacturer of die castings. Capabilities include cold chamber aluminum die casting parts from 0.15 lbs. to 6 lbs., quick change set up, and machining. Value-added services include polishing, vibrating, deburring, shot blasting, painting, plating, coating, assembly, and tooling. Materials worked with include alloys such as 360, 380, 383, and 413.
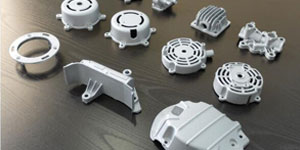
Zinc die casting design assistance/concurrent engineering services. Custom manufacturer of precision zinc die castings. Miniature castings, high pressure die castings, multi-slide mold castings, conventional mold castings, unit die and independent die castings and cavity sealed castings can be manufactured. Castings can be manufactured in lengths and widths up to 24 in. in +/-0.0005 in. tolerance.
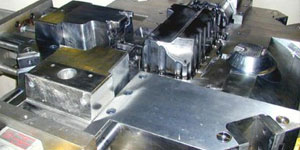
ISO 9001: 2015 certified manufacturer of die cast magnesium, Capabilities include high-pressure magnesium die casting up to 200 ton hot chamber & 3000 ton cold chamber, tooling design, polishing, molding, machining, powder & liquid painting, full QA with CMM capabilities, assembly, packaging & delivery.
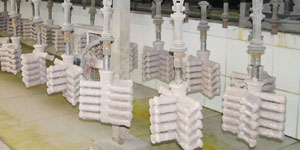
ITAF16949 certified. Additional Casting Service Include investment casting,sand casting,Gravity Casting, Lost Foam Casting,Centrifugal Casting,Vacuum Casting,Permanent Mold Casting,.Capabilities include EDI, engineering assistance, solid modeling and secondary processing.
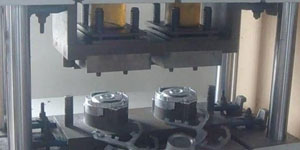
Casting Industries Parts Case Studies for: Cars, Bikes, Aircraft, Musical instruments, Watercraft, Optical devices, Sensors, Models, Electronic devices, Enclosures, Clocks, Machinery, Engines, Furniture, Jewelry, Jigs, Telecom, Lighting, Medical devices, Photographic devices, Robots, Sculptures, Sound equipment, Sporting equipment, Tooling, Toys and more.
What Can we help you do next?
∇ Go To Homepage For Die Casting China
→Casting Parts-Find out what we have done.
→Ralated Tips About Die Casting Services
By Minghe Die Casting Manufacturer |Categories: Helpful Articles |Material Tags: Aluminum Casting, Zinc Casting, Magnesium Casting, Titanium Casting, Stainless Steel Casting, Brass Casting,Bronze Casting,Casting Video,Company History,Aluminum Die Casting |Comments Off