The Matters Needing Attention When Designing Casting Structure
Since the casting cools and solidifies faster in the metal mold than in the sand mold, and the metal mold has no tolerance, when the metal mold is cast, the casting stress generated in the casting is larger than that in the sand casting. Defects such as insufficient pouring, cold barrier, white mouth (for castings), etc. usually:
Attention should be paid to the following structural issues in preventing cracks in metal mold castings:
- A. The requirements for uniform wall thickness, gentle transition and connection between walls, proper fillet at relatively corners, etc. should be stricter than sand casting castings;
- B The vertically connected walls should be changed to obliquely connected;
- C The weaker parts of the structure should be reinforced with ribs, bosses, etc. to prevent casting cracks;
- D Try to reduce the protrusions, ribs, flanges and other protruding parts that hinder the free shrinkage of the casting;
- E When arranging the reinforcing rib on the casting, its influence on the shrinkage of the casting should also be considered.
Attention should be paid to the following structural problems in preventing insufficient pouring and cold isolation of metal mold castings:
- A. The wall thickness of the casting should be appropriate and not too thin, especially when the contour size of the casting is large;
- B. A large horizontal surface should be avoided, because it makes the molten metal rise very slowly during casting, and the surface in contact with the air is large, which is easy to oxidize. At the same time, due to the rapid heat dissipation of the metal mold, the molten metal quickly loses fluidity and is easy to cause pouring. Insufficiency, cold barrier, slag inclusion and other defects;
- C. The shape of the casting should be streamlined as much as possible to avoid sharp edges and corners and sharply changing connections to facilitate the flow of molten metal.
When designing metal castings with more complex shapes, if the production process has greater difficulties, try to make the castings simple in appearance and strong structure changes without affecting the use conditions of the castings to facilitate the removal of the castings from the metal mold.
When designing the basic structural units of metal mold castings and selecting their parameters, it is usually necessary to pay attention to:
- (1) Due to the fast heat dissipation of the metal mold, the minimum wall thickness of the metal mold casting should be larger than that of the sand casting casting;
- (2) The thickness of the inner wall and the inner rib of the casting should generally be 0.6-0.7 of the thickness of the connected outer wall, otherwise the inner wall (rib) will cool slowly, cracks will easily occur at the junction of the inner and outer walls when the casting shrinks;
- (3) In order to prevent the gray cast iron parts from producing white holes, in addition to the measures taken from the process, the wall thickness must not be too thin (some materials indicate that when the wall thickness is more than 15mm, the corners of the castings must be cast with metal molds. Use rounded corners, and the rounded corners of aluminum alloy and magnesium alloy metal mold castings should not be less than 3~4m;
- (4) Due to the inconsistency of the metal mold and the core, in order to facilitate the removal of the casting and the extraction of the mold, the casting slope of the metal mold casting should be appropriately larger than that of the sand casting, generally 30%-50% larger. It should be pointed out: In addition to the alloy type and the height of the wall, the casting slope is related to the position of the surface of the casting. The surface of the casting that has a tendency to separate from the surface of the metal mold when the casting is cooled and shrinks can be designed with a smaller slope. The surface of the casting, which tends to be pressed against the metal mold during shrinkage, should be given a larger slope.
Please keep the source and address of this article for reprinting: The Matters Needing Attention When Designing Casting Structure
Minghe Die Casting Company are dedicated to manufacture and provide quality and high performance Casting Parts(metal die casting parts range mainly include Thin-Wall Die Casting,Hot Chamber Die Casting,Cold Chamber Die Casting),Round Service(Die Casting Service,Cnc Machining,Mold Making,Surface Treatment).Any custom Aluminum die casting, magnesium or Zamak/zinc die casting and other castings requirements are welcome to contact us.
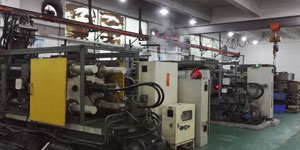
Under the control of ISO9001 and TS 16949,All processes are carried out through hundreds of advanced die casting machines, 5-axis machines, and other facilities, ranging from blasters to Ultra Sonic washing machines.Minghe not only has advanced equipment but also have professional team of experienced engineers,operators and inspectors to make the customer’s design come true.
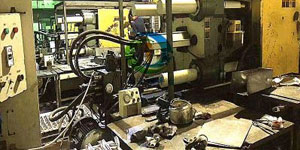
Contract manufacturer of die castings. Capabilities include cold chamber aluminum die casting parts from 0.15 lbs. to 6 lbs., quick change set up, and machining. Value-added services include polishing, vibrating, deburring, shot blasting, painting, plating, coating, assembly, and tooling. Materials worked with include alloys such as 360, 380, 383, and 413.
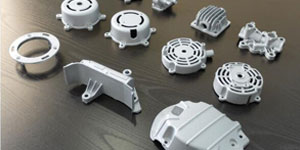
Zinc die casting design assistance/concurrent engineering services. Custom manufacturer of precision zinc die castings. Miniature castings, high pressure die castings, multi-slide mold castings, conventional mold castings, unit die and independent die castings and cavity sealed castings can be manufactured. Castings can be manufactured in lengths and widths up to 24 in. in +/-0.0005 in. tolerance.
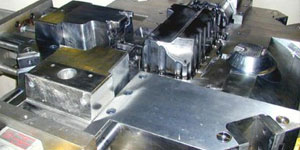
ISO 9001: 2015 certified manufacturer of die cast magnesium, Capabilities include high-pressure magnesium die casting up to 200 ton hot chamber & 3000 ton cold chamber, tooling design, polishing, molding, machining, powder & liquid painting, full QA with CMM capabilities, assembly, packaging & delivery.
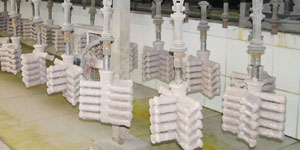
ITAF16949 certified. Additional Casting Service Include investment casting,sand casting,Gravity Casting, Lost Foam Casting,Centrifugal Casting,Vacuum Casting,Permanent Mold Casting,.Capabilities include EDI, engineering assistance, solid modeling and secondary processing.
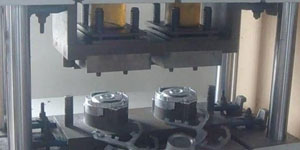
Casting Industries Parts Case Studies for: Cars, Bikes, Aircraft, Musical instruments, Watercraft, Optical devices, Sensors, Models, Electronic devices, Enclosures, Clocks, Machinery, Engines, Furniture, Jewelry, Jigs, Telecom, Lighting, Medical devices, Photographic devices, Robots, Sculptures, Sound equipment, Sporting equipment, Tooling, Toys and more.
What Can we help you do next?
∇ Go To Homepage For Die Casting China
→Casting Parts-Find out what we have done.
→Ralated Tips About Die Casting Services
By Minghe Die Casting Manufacturer |Categories: Helpful Articles |Material Tags: Aluminum Casting, Zinc Casting, Magnesium Casting, Titanium Casting, Stainless Steel Casting, Brass Casting,Bronze Casting,Casting Video,Company History,Aluminum Die Casting |Comments Off