The Measures To Prevent Coarse Grains Of Castings
Coarse crystal grains of castings refer to defects that show excessively coarse grain structure and unsuitable for application after mechanical engineering or fracture inspection. This coarse grain structure may be spread throughout the entire casting or may occur in the casting.
In essence, the coarse grain defect is a metallurgical defect. Based on years of production practice and refer to relevant materials, the author talks about the causes and preventive measures of coarse casting defects.
1. Casting structure and process design
- (1) If the cross-section difference of the casting is too large, the thicker cross-section will cool slowly and cause the coarse grains there. Metals, such as gray cast iron, which are very sensitive to cross-sectional changes, are more likely to produce such defects.An effective way to prevent such defects is to avoid excessive disparity in the cross-sectional dimensions of castings, but this approach is sometimes beyond the reach of foundry workers. Therefore, as far as casting itself is concerned, it is possible to reduce the occurrence of such problems and the severity of such defects by setting cold iron, controlling the pouring temperature, or selecting a suitable pouring system. The use of cold iron can speed up the cooling rate of the thicker section of the casting; too high pouring temperature will make this kind of problem more serious and should be avoided; by adjusting and revising the pouring system design, the lower temperature of the molten metal is located at the lower section of the casting. Thick parts, and design the most effective riser at the thick section of the casting to reduce the size of the riser as much as possible.
- (2) For castings with holes, process designers sometimes do not use cores that help reduce the effective cross-sectional size, and make the cross-sections without cores too thick to cause this defect. Therefore, in process design, it should be as small as possible. A sand core is set in the thick section.
- (3) In some cases, the section of the casting is not too thick, but because a narrow recess or core forms a heat sink section in the casting, the result is the same as the thick section. E.g. It may be necessary to set a core at a columnar umbilicus in the deeper part of the casting, and this will cause slow cooling. In the case that the design cannot be modified, unless the metal temperature can be lowered, or the gate can be relocated, the best solution is to install cold iron at the core or mold section.
- (4) The machining allowance is too large in the process design, which not only increases the cost of cutting, but also cuts off the denser surface of the casting, and exposes the loose part with slower cooling in the center. This design is undesirable because it is unreasonable from the perspective of casting or machining. The solution is to change the design of the casting. If the design is not allowed to change, the correct method is to use cold iron, control the pouring temperature and adjust the pouring system.
- (5) Inappropriate core design at the thick section, incorrect core support, or other technologies that cause eccentricity, will cause changes in the section of the casting and cause coarse grains.
2. Pouring and riser system
- (1) Failure to achieve sequential solidification" The failure of the pouring system to achieve sequential solidification well is usually the cause of coarse grains. For castings with sharp cross-section changes, attention must be paid to the number and location of the gate. In order to perform feeding, keeping hot molten metal in the action area of the feeder will reduce the cooling rate of the thick section to the extent that coarse grains are produced. Improper riser design, such as too long riser neck, improper riser pad design, or too large riser size, will cause excessive heat collection at the thicker section.
- (2) Pouring riser distribution that is likely to cause heat sinks. Similarly, in order to feed thick sections, excessive heat collection is often caused in local areas. For example, because the side riser can cause overheating of thick sections and slow down the cooling rate, it is sometimes inconvenient to use in actual operation. In actual production, a reasonable riser design is required to reduce the size of the riser as much as possible.
- (3) The connection between the inner gate or the riser and the casting causes the local hot joint. The inner gate or the riser neck is short, which is beneficial for feeding, but it will make the runner or riser too close to the casting. Slow down the cooling rate of this part. Enlarging the neck of the riser will cause problems for feeding. Therefore, the best measure is to adopt an effective riser design, reduce the size of the riser as much as possible, do not make the runner and the riser too close to the key section that is easy to form a coarse product, and set the runner and the riser appropriately. To achieve feeding.
- (4) Insufficient number of internal gates. Too few internal gates will not only easily cause sand washing, but also cause local hot spots and coarse grain structure. This phenomenon is common in all cast metals, even aluminum alloys with lower casting temperatures. In some cases, because the number of gates is too small, it will cause shrinkage defects. This shrinkage defect may conceal the coarse grain defects caused by the same reason. In fact, when the coarse grain defect deteriorates seriously, it becomes a shrinkage defect. Therefore, the prevention and control measures for these two defects are often the same.
3. Molding sand
Only when the displacement of the molding wall caused by the molding sand is sufficient to increase the cross-sectional size of the critical section (the section that is easy to form coarse grains), the mold sting is a factor that causes the coarse grain defects. Since the wall movement at the thick section may be the largest, this kind of defect is still possible, and the coarse grain defect produced at this time is related to the expansion of sand.
4. Core making
In production, the use of unbaked or air-hardened oil sand cores should be avoided, because such cores may produce an exothermic reaction and cause excessive heat collection. This happens either in large castings, or in thick and large cores using adhesives with exothermic properties. In a sense, this core acts as a highly efficient insulator and slows down the cooling rate of molten metal to a dangerous level.
5. Modeling
- (1) Lack of vent holes that can accelerate the cooling rate. For thicker casting sections, the cooling rate of the casting is related to the rate of heat dissipation through the molding sand. Adequate exhaust will help the water vapor to be expelled quickly, thereby producing a cooling effect.
- (2) The absence of chill nails or cold iron is usually caused by carelessness.
6. Chemical composition
Essentially, the coarse crystal grains and the chemical composition of the metal are related to the cooling rate, so it is very important to choose this combination. If the cooling rate is difficult to adjust, then the coarse-grained structure must be due to the improper chemical composition of the metal. Due to the importance of metal components, each metal is briefly described as follows.
- (1) The carbon equivalent of gray cast iron and malleable cast iron is too high. The mathematical calculation of carbon and silicon effects can usually be summarized as: CE=C+1/3Si. The coarse grains may be caused by excessive carbon or silicon, or excessive carbon and silicon. To. Compared with silicon, the effect of carbon is three times that of silicon, so the change in the amount of carbon is much more dangerous than the change in the same amount of silicon. This effect of carbon and silicon affects both malleable cast iron and gray cast iron. For malleable cast iron, the coarse grains do not appear as black, nor do they appear as pits that indicate primary graphite. Instead, they appear in the form of general coarse grains. This is due to the high carbon or silicon content, or Both are too high. Phosphorus also affects the coarseness of crystal grains. When wp=0.1%, the shrinkage cavity defect will be aggravated, especially in the section where the cooling is slower, the degree of coarse grain defects will be aggravated.
- (2) Cast steel: In the melting and deoxidation operation of cast steel, some elements that delay the growth of grains are added. Therefore, compared with forged steel, cast steel is less likely to form coarse grains. Steel castings with coarse grains caused by composition can be refined by annealing or normalizing.
- (3) Aluminum alloy and iron impurities will make aluminum castings coarser grains and increase brittleness. Most of these defects are caused by improper melting operations. In aluminum alloys, especially those requiring overheating, it is necessary to add an appropriate amount of refined alloy elements.
- (4) Copper alloys: Defects with coarse grains in copper alloys are often covered by pinholes, pores or shrinkage. Copper alloys will cause coarser grains due to changes in composition, but usually pinholes, pores or shrinkage porosity always appear first.
7.Melting
The small melting operation will have an impact on the rest of the grain structure. For different cast metals, Xiaotong’s melting process must be adopted.
- (1) The cupola melts gray cast iron. The unbalanced blast volume and coke will cause excessive carbon increase. For example, the height of the bottom coke is too high and the reduction of the blast volume will cause excessive carbon increase. When the furnace lining is eroded, the carbon increase will be more serious. Because the diameter of the cupola becomes larger, in order to maintain the same carbon content, the blast volume needs to be increased. Melting at an excessively high temperature will increase the amount of carbon, which is the case if hot air smelting is used. According to experience, every increase of 55°C in the blast temperature will increase the carbon (mass fraction) by 0.10%. If oxygen is used to increase the temperature, it does not necessarily cause the same problem.The interval between tapping liquid is too long, or the liquid iron stays in the hearth for too long, it will also cause carbon increase. The production of low-carbon cast iron generally uses a shallower hearth and shortens the interval between tapping molten iron, and tries to achieve continuous tapping of molten iron as much as possible.Intermittent melting will cause excessive carburization, resulting in a coarse-grained structure. In addition, the melting is interrupted due to the stop of the wind, almost without exception, causing fluctuations in the carbon and silicon content. After stopping the wind, it usually takes 15 minutes to regain the original chemical composition.
- (2) Malleable cast iron. Deviations in the weighing or batching of the charge will lead to changes in the chemical composition; the amount of blast in the furnace is not guaranteed, which will affect the control of the chemical composition; overheating of melting or smoke filling in the flame will cause carbon increase.
- (3) The use of dirty crucibles for brass and bronze, as well as the remaining condensed shells or thin metal layers from the last melting on the bottom and side walls of the crucible, will cause pollution to the next melting, so the production In the process, we should avoid the use of waste materials of unknown origin, and prevent the incorporation of gas-producing raw materials into the metal furnace charge, such as wet, oil-contaminated or other dirty materials.
- (4) Aluminum Overheating of molten aluminum due to improper melting temperature control is a common cause of coarse aluminum alloy grains. Therefore, the overheated molten aluminum should be slowly cooled down during production to lower it to a lower pouring temperature. In addition, carelessness or contamination of the charge during the batching process can also cause coarse grain defects.
8. Pouring
For all metals, too high a pouring temperature can easily cause coarse grain defects.
9. Other
- (1) Excessive cooling speed is not only related to design, pouring system and metal composition, but also related to other factors, such as low molding sand compactness, when it is necessary to use cold iron, and the time interval between pouring and falling sand Too long, and stacking hot castings after falling sand, etc.
- (2) Improper heat treatment” is also one of the main reasons for the coarse particles of some metals.
- (3) Improper machining "Improper machining can make the actually dense castings look like they have coarse grain defects. The so-called improper machining refers to the improper grinding of the tool, the blunt tool, the wrong cutting speed or feed control, and the improper roughing method, etc., which will cause a porous appearance with certain damage. This appearance will make It is believed that the casting has the defect of coarse grains.
Please keep the source and address of this article for reprinting:The Measures To Prevent Coarse Grains Of Castings
Minghe Die Casting Company are dedicated to manufacture and provide quality and high performance Casting Parts(metal die casting parts range mainly include Thin-Wall Die Casting,Hot Chamber Die Casting,Cold Chamber Die Casting),Round Service(Die Casting Service,Cnc Machining,Mold Making,Surface Treatment).Any custom Aluminum die casting, magnesium or Zamak/zinc die casting and other castings requirements are welcome to contact us.
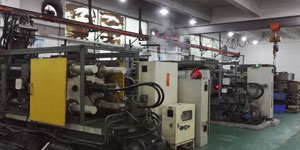
Under the control of ISO9001 and TS 16949,All processes are carried out through hundreds of advanced die casting machines, 5-axis machines, and other facilities, ranging from blasters to Ultra Sonic washing machines.Minghe not only has advanced equipment but also have professional team of experienced engineers,operators and inspectors to make the customer’s design come true.
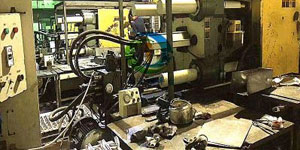
Contract manufacturer of die castings. Capabilities include cold chamber aluminum die casting parts from 0.15 lbs. to 6 lbs., quick change set up, and machining. Value-added services include polishing, vibrating, deburring, shot blasting, painting, plating, coating, assembly, and tooling. Materials worked with include alloys such as 360, 380, 383, and 413.
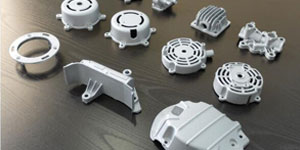
Zinc die casting design assistance/concurrent engineering services. Custom manufacturer of precision zinc die castings. Miniature castings, high pressure die castings, multi-slide mold castings, conventional mold castings, unit die and independent die castings and cavity sealed castings can be manufactured. Castings can be manufactured in lengths and widths up to 24 in. in +/-0.0005 in. tolerance.
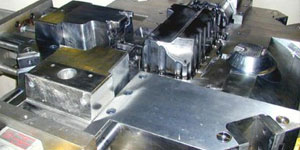
ISO 9001: 2015 certified manufacturer of die cast magnesium, Capabilities include high-pressure magnesium die casting up to 200 ton hot chamber & 3000 ton cold chamber, tooling design, polishing, molding, machining, powder & liquid painting, full QA with CMM capabilities, assembly, packaging & delivery.
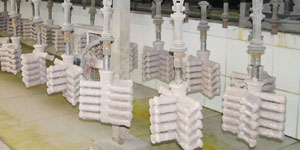
ITAF16949 certified. Additional Casting Service Include investment casting,sand casting,Gravity Casting, Lost Foam Casting,Centrifugal Casting,Vacuum Casting,Permanent Mold Casting,.Capabilities include EDI, engineering assistance, solid modeling and secondary processing.
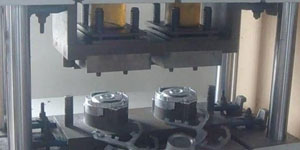
Casting Industries Parts Case Studies for: Cars, Bikes, Aircraft, Musical instruments, Watercraft, Optical devices, Sensors, Models, Electronic devices, Enclosures, Clocks, Machinery, Engines, Furniture, Jewelry, Jigs, Telecom, Lighting, Medical devices, Photographic devices, Robots, Sculptures, Sound equipment, Sporting equipment, Tooling, Toys and more.
What Can we help you do next?
∇ Go To Homepage For Die Casting China
→Casting Parts-Find out what we have done.
→Ralated Tips About Die Casting Services
By Minghe Die Casting Manufacturer |Categories: Helpful Articles |Material Tags: Aluminum Casting, Zinc Casting, Magnesium Casting, Titanium Casting, Stainless Steel Casting, Brass Casting,Bronze Casting,Casting Video,Company History,Aluminum Die Casting |Comments Off