The Measures To Reduce Energy Consumption Of Sintering Ignition
The energy consumption of the sintering process accounts for about 10% of the total energy consumption of iron and steel production, second only to ironmaking, and is the second largest energy consumer in iron and steel production. Sintering ignition system is an important link in sintering production. The ignition system directly affects the progress of the sintering process, the technical and economic indicators of sintering production, and the quality of sintered ore.
In actual production and operation, the process parameters such as ignition intensity, ignition negative pressure, oxygen content in ignition flue gas, ignition temperature, etc. often cannot meet the appropriate sintering and ignition requirements, resulting in uneven distribution of ignition along the width of the trolley, and the surface mixture The combustion of coke powder is insufficient, the ignition and combustion efficiency is reduced and the ignition energy consumption is increased. The countermeasures are:
1. In view of the difficulty of ignition of blast furnace gas, low ignition temperature and inability to meet sintering requirements, the ignition medium is changed from blast furnace gas to coke oven gas.
After using coke oven gas to ignite, the ignition heat consumption is 72.61MJ/t, which is at a good level. By using coke oven gas as ignition fuel, the drum index is increased by about 2%.
2. Aiming at the problem of ignition negative pressure, at the sintering ignition site, the pressure of the furnace can be reduced by adjusting the pressure of the wind box under the igniter.
The purpose of low negative pressure ignition is achieved by reducing the negative pressure of the furnace, which can not only ensure the ignition depth, but also prevent the heat from being quickly removed, which helps to reduce the energy consumption of sintering and ignition.
3. Aiming at the problem of oxygen content, the oxygen content in the ignition flue gas can be significantly increased by using oxygen-enriched ignition technology.
When the oxygen content in the ignition-supporting air increases, the solid carbon of the surface sintering material is burned more fully, the ignition temperature and the temperature of the surface mixture are increased, the combustion efficiency is improved, and the ignition conditions are improved.
When the oxygen content in the ignition gas stream increases to 7% to 8%, the yield of sintered ore is increased by about 2.0%, and the solid fuel consumption is also reduced by about 6.3kg/t.
4. Aiming at the problem of low ignition temperature, by recycling waste hot air to assist ignition, the ignition effect is enhanced, the heat supply of the mixture layer is increased, and the fuel consumption is reduced while ensuring the same ignition temperature.
After hot air is used for combustion-supporting ignition, the oxygen content of the flue gas is obviously increased, and the combustion degree of the fuel is obviously improved, and the sintering combustion efficiency is improved. And by recovering part of the waste heat of sintering production, the energy consumption of the sintering process can be reduced to a certain extent.
5. Aiming at the problem of the air permeability of the material layer, the use of a material leveling device to level the material surface can improve the ignition effect and eliminate the "edge effect".
By leveling the material surface, the air permeability of the material layer is improved, the pressure and temperature distribution of the material surface are more uniform, and the ignition heat is used to a greater extent.
Please keep the source and address of this article for reprinting:The Measures To Reduce Energy Consumption Of Sintering Ignition
Minghe Die Casting Company are dedicated to manufacture and provide quality and high performance Casting Parts(metal die casting parts range mainly include Thin-Wall Die Casting,Hot Chamber Die Casting,Cold Chamber Die Casting),Round Service(Die Casting Service,Cnc Machining,Mold Making,Surface Treatment).Any custom Aluminum die casting, magnesium or Zamak/zinc die casting and other castings requirements are welcome to contact us.
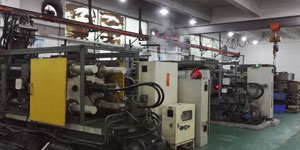
Under the control of ISO9001 and TS 16949,All processes are carried out through hundreds of advanced die casting machines, 5-axis machines, and other facilities, ranging from blasters to Ultra Sonic washing machines.Minghe not only has advanced equipment but also have professional team of experienced engineers,operators and inspectors to make the customer’s design come true.
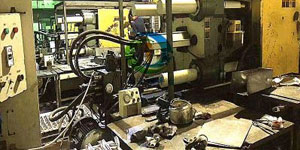
Contract manufacturer of die castings. Capabilities include cold chamber aluminum die casting parts from 0.15 lbs. to 6 lbs., quick change set up, and machining. Value-added services include polishing, vibrating, deburring, shot blasting, painting, plating, coating, assembly, and tooling. Materials worked with include alloys such as 360, 380, 383, and 413.
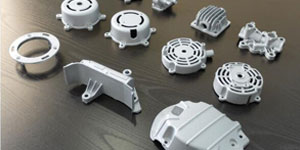
Zinc die casting design assistance/concurrent engineering services. Custom manufacturer of precision zinc die castings. Miniature castings, high pressure die castings, multi-slide mold castings, conventional mold castings, unit die and independent die castings and cavity sealed castings can be manufactured. Castings can be manufactured in lengths and widths up to 24 in. in +/-0.0005 in. tolerance.
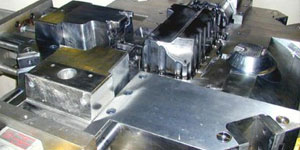
ISO 9001: 2015 certified manufacturer of die cast magnesium, Capabilities include high-pressure magnesium die casting up to 200 ton hot chamber & 3000 ton cold chamber, tooling design, polishing, molding, machining, powder & liquid painting, full QA with CMM capabilities, assembly, packaging & delivery.
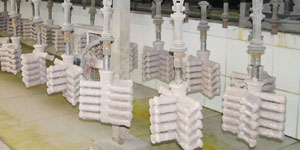
ITAF16949 certified. Additional Casting Service Include investment casting,sand casting,Gravity Casting, Lost Foam Casting,Centrifugal Casting,Vacuum Casting,Permanent Mold Casting,.Capabilities include EDI, engineering assistance, solid modeling and secondary processing.
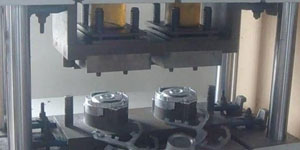
Casting Industries Parts Case Studies for: Cars, Bikes, Aircraft, Musical instruments, Watercraft, Optical devices, Sensors, Models, Electronic devices, Enclosures, Clocks, Machinery, Engines, Furniture, Jewelry, Jigs, Telecom, Lighting, Medical devices, Photographic devices, Robots, Sculptures, Sound equipment, Sporting equipment, Tooling, Toys and more.
What Can we help you do next?
∇ Go To Homepage For Die Casting China
→Casting Parts-Find out what we have done.
→Ralated Tips About Die Casting Services
By Minghe Die Casting Manufacturer |Categories: Helpful Articles |Material Tags: Aluminum Casting, Zinc Casting, Magnesium Casting, Titanium Casting, Stainless Steel Casting, Brass Casting,Bronze Casting,Casting Video,Company History,Aluminum Die Casting |Comments Off