The Melting And Treatment Of ADC12
1. The Basic Characteristics Of Aluminum Alloy
Japan ADCI2 aluminum-silicon alloy has good casting performance, and the casting has high strength, low thermal expansion coefficient, high corrosion resistance and good chipping performance. Therefore, it is widely used in the production of automotive carburetor, cylinder block, cylinder head, and locomotive reducer.
Vibrators, engine gearboxes, agricultural machinery gearboxes, camera bodies, power tool bodies and other parts. In recent years, with the rapid development of the automobile and motorcycle industries, they have been more widely used in the production of brake pump housings for small cars And motorcycle shock absorber shells and other mass-produced small and medium-sized parts with complex shapes and high strength precision.
Si | Fe | Cu | Mn | Mg | Ni | Zn | Sn | Pb |
9.6-12.0 | <0.85 | 1.8-3.5 | <0.5 | <0.3 | <0.5 | <0.95 | <0.1 | <0.1 |
In aluminum alloy ADC12 castings, the a-Al phase is the most important structure. In the as-cast state, the a-Al phase is dendritic and relatively coarse, and its orientation has no certain regularity and is rather messy, which makes its performance not very good. ; Si in the alloy is mainly used to improve casting performance, wear resistance, corrosion resistance and mechanical properties. Cu and Mg form CuAl2 and Mg2Si phases to strengthen the alloy, but if the content is too high, the plasticity will be reduced, and Cu can also increase High temperature performance, but it will reduce corrosion resistance; Mn mainly forms AIFeMnS phase, reduces the harmful effects of Fe impurities, and can improve the heat resistance of castings. Fe is generally regarded as the most harmful impurity element in Al alloys. The Fe phase is a-Fe phase (AlgSiFez) and B-Fe phase (AIsSiFe). The hard and brittle acicular β-Fe phase will destroy the connection strength of the metal matrix and greatly reduce the mechanical properties of the alloy (such as resistance Tensile strength), Fe in Al alloy as a harmful element will significantly reduce: the mechanical properties of the alloy, affect the fracture roughness and so on.
2.The Process Of Aluminum Alloy Raw Materials To Be Controlled
Nowadays, most of the die-casting industry purchase aluminum alloy ingots from aluminum alloy ingot production plants. The prepared aluminum alloy ingots of this type are mostly recycled secondary aluminum products as the main material, and the composition is adjusted (pure aluminum ingots and some intermediates are added). Alloy). Therefore, the cost and selling price of this alloy aluminum ingot are lower than those of pure aluminum ingot as the main material, but the content of impurities is higher. In view of this situation, it is necessary to inspect the chemical composition of the purchased alloy aluminum ingots, and make appropriate adjustments when signing the technical requirements with the alloy aluminum ingot manufacturer according to GB/T8733, and then make progress according to the requirements of die-casting aluminum alloy- Step adjustment. Due to the requirements of the gas content and hard points in the aluminum alloy, the aluminum ingot production plant must do refining, degassing, and slagging to prevent the high gas content and many impurities in the aluminum ingot from being inherited into the die-casting aluminum liquid. The aluminum ingot is required The surface is smooth (after the scum is removed), the fracture is fine and there is no bright crystal grain of crystalline silicon. The air bubbles on the surface of the aluminum ingot are because the paint on the ingot mold has a large amount of water and has not been dried. The surface is not bright because the scum has not been scraped off. The fracture of the aluminum ingot has bright crystal grains because the pouring temperature is too high and there are silicon crystals. In die-casting production, there are 30% to 60% of the recycled material. If the recycled material is oily, it must be burned and then pressed into the aluminum liquid. The crushed aluminum slag must be sieved and dusted, and sand and gravel must be removed before returning to the furnace. Where the recycled material is used The amount of molten aluminum, refining agent, and slag remover must be increased appropriately, and generally controlled according to the upper limit ratio. When smelting, the added aluminum ingot must be dry.
3. The Melting Of Aluminum Alloy
The smelting furnace used by the company is ATM-1500. The company requires that the smelting furnace must be baked every time the shift is opened in order to remove the moisture in the furnace, and the furnace after baking must meet the specified process requirements. During the smelting process, the smelting temperature is required: (680~750)C; the refining furnace temperature: (730+10) C. During the entire smelting process of aluminum alloy, the charge starts to melt when heated, realizing the transformation from solid to liquid. During this transformation process, the metal will be oxidized, burnt and get gas. The oxidation and burning of metal will not only affect the chemical composition of the alloy, but also the slag inclusion caused by the oxidation is one of the most harmful defects of aluminum alloy ingots. The inhalation of the metal will make the ingot too late or impossible during the solidification process. It escapes and exists in the ingot in the form of loose and pores. Therefore, the correctness of the aluminum alloy melting process is directly related to the quality of the melt. It not only affects its chemical composition, but also affects the quality of the ingot and even the final The quality of processed products is closely related. Aluminum is very active, except for inert gases, it reacts with almost all gases:
Moreover, these reactions are irreversible. Once reacted, the metal cannot be reduced, which causes the loss of the metal. Moreover, the products (oxides, carbides, etc.) entering the melt will contaminate the metal and cause defects in the internal structure of the ingot . Therefore, in the melting process of aluminum alloy alloys, there are strict selection of process equipment (such as furnace type, heating method, etc.), and strict selection and measures for the process flow, such as shortening the melting time and controlling the appropriate melting speed. Use flux to cover and so on.
- Due to the activity of aluminum, at smelting temperature, it will chemically react with moisture in the atmosphere and moisture, oil, hydrocarbons, etc. in a series of processes. On the one hand, the gas content in the melt is increased, causing looseness and pores, and on the other hand, the product can stain the metal. Therefore, all measures must be taken to minimize moisture during the melting process, and the process equipment, tools and raw materials must be strictly kept dry and oil stained.
- The company uses a continuous smelting method, this method feeds continuously, and discharges intermittently. For aluminum alloy smelting, due to the structure of the furnace, the residence time of the melt should be as short as possible. Because the residence time of the melt is prolonged, especially at higher melting temperatures, a large number of non-spontaneous crystal nuclei are deactivated, causing coarse ingot crystal grains, resulting in ingot casting waste, and increased metal suction, making the melt non-metallic inclusions and The gas content increases.
- The gas in the atmosphere in the furnace for melting metal is one of the most important sources of gas. Depending on the type and structure of the smelting furnace used, and the combustion or heating method of the fuel used, the furnace atmosphere often contains various proportions of hydrogen (H2), oxygen (O2), water vapor (H2O), carbon dioxide (CO2), and carbon monoxide. (CO), nitrogen (N2), sulfur dioxide (SO2) in addition to various hydrocarbons. These results are of course incomplete, and the composition range is very wide. This is because the combustion product in the furnace-furnace gas changes greatly and is very unstable. Here we mainly introduce the process of hydrogen (H) absorption in aluminum alloy liquid, which mainly includes three processes: adsorption, diffusion, and dissolution.
Because hydrogen is a unit gas with a relatively simple structure, its atoms or molecules are very small, it is easier to dissolve in metals, and it is easy to diffuse rapidly at high temperatures. Therefore, hydrogen is a gas that is easily dissolved in metals.
The dissolution process of hydrogen in molten aluminum: physical adsorption-+ chemical adsorption →> diffusion
Hydrogen does not chemically react with aluminum but exists in the gaps of the crystal lattice in an ionic state, forming an interstitial solid solution. In the absence of an oxide film on the surface of the liquid metal, the diffusion rate of the gas into the metal is inversely proportional to the thickness of the metal, proportional to the square root of the gas pressure, and increases with increasing temperature
Where: v diffusion rate n-constant d-metal thickness E-activation energy p-gas partial pressure R-gas constant T-temperature K Therefore, before reaching the saturation solubility of the gas, the higher the melt temperature, the dissociation of hydrogen molecules The faster the speed, the faster the diffusion speed, so the higher the gas content in the melt.
Under production conditions, no matter what kind of smelting furnace is used to produce aluminum alloy, the melt is directly in contact with air, that is, with air
Oxygen in the gas is in contact with nitrogen. Aluminum is a relatively active metal. After it comes in contact with oxygen, it will inevitably produce strong oxidation to form alumina.
Once aluminum is oxidized, it becomes oxidized slag and becomes an irreversible loss. Alumina is a very stable solid substance, if mixed into the melt, it will become oxidized slag. Due to the high affinity of aluminum and oxygen, the reaction between oxygen and aluminum is very intense. However, the surface aluminum reacts with oxygen to produce Al2O3, and the molecular volume of Al2O is larger than that of aluminum, so the surface layer of aluminum is oxidized to form A12O; the film is dense, which can prevent oxygen atoms from diffusing inward through the oxide film At the same time, it can also prevent aluminum ions from diffusing outward, thus preventing further oxidation of aluminum.
4.Treatment Of Aluminum Alloy
The treatment of aluminum alloy mainly includes slag removal and refining.
- (1) In the process of slagging aluminum alloy smelting, because of the ineffective slag removal and purification, a small amount of slag is dissolved in the melt, resulting in the formation of snow spots on the surface of the aluminum alloy, which seriously affects the quality of the aluminum alloy. If the slag removal is not clean, It will cause slag inclusions and other traps, and the casting will be scrapped. Aluminum is a kind of active metal. It is easy to produce aluminum oxides during the smelting process. Some non-metallic inclusions are also easy to enter the melt. The inclusions are very harmful to aluminum products. The removal of inclusions has become the main task of aluminum melt purification. In production practice, common inclusions in aluminum alloy melts are Al203, SiO2, MgO, etc. It will cause the impurity of the molten metal, the inclusions will affect the fluidity of the melt, the polymerization will produce bubbles during the solidification process, which will affect the degree of shrinkage. Because the density of fine oxide particles is similar to that of aluminum, they are generally suspended in molten aluminum, and it is difficult to remove them by standing still. The removed oxide usually contains a lot of aluminum. Although flux has many other uses, reducing aluminum oxidation and removing oxidized inclusions are the main reasons for using flux.The principle of slagging in the smelting furnace: Sprinkle the slagging agent (or slag remover) on the surface of the molten aluminum to separate the slag and water, and pull the separated slag out of the furnace, because the slagging agent contains NajAIF. (Or KzSiFg), this salt has the ability to strongly adsorb Al2O3, as well as Na2SiF.The first reaction can eat part of Al2O3, and the third reaction separates the slag and water, and pulls the slag out of the furnace to achieve the purpose of slag removal. At the same time, it also generates NaAlF%, which has the effect of strongly adsorbing r-Al2O3, making the slag and aluminum The liquid is separated. The purpose of the slag removal process of aluminum alloy is to remove the impurities and oxide slag that enter the molten aluminum. Often, the slag contains molten aluminum during slag removal. Therefore, it is hoped that the molten aluminum contained in the slag should be as little as possible, and the slag should be scrambled again. The purpose of frying ash is to squeeze out the molten aluminum in the slag and sink to the bottom of the wok, so that the slag is softly broken and dispersed on the upper part, so that the slag and the molten aluminum are separated. In order to achieve this, a good slag removing flux must be selected. . The method of slag removal is based on the amount of molten aluminum in the smelting furnace, evenly put in the slag remover according to the required proportion, and stir at a constant speed, and then pull out the filter slag after standing still for 8-10 minutes. The slagging requires the temperature of the molten aluminum to be 720-740C. Experience has shown that the slag produced by the slag remover is loose, non-black, and off-white is a better slag remover.
- (2) Refining:The chemical properties of aluminum are 17 times more active. Therefore, even if the hydrogen content in the alloy liquid is very low, a large amount of hydrogen will precipitate during solidification, forming pinholes and inclusions in the castings, which will seriously affect the mechanical properties of the aluminum alloy. Improving the quality of aluminum alloy melt and purifying the alloy liquid is one of the key issues in aluminum alloy smelting, and it is also an effective way and means to improve the product quality and market competitiveness of aluminum castings. Unreasonable refining process, alloy degassing is not clean, castings are prone to pores. In order to increase the degassing effect, it is necessary to increase the amount of refining agent added. However, if the amount is too much, it is easy to cause the oxidation burning of Mg. Al, Ti and other elements, and the formation of oxidation slag. For this-a key aluminum alloy refining process is essential. Studies have shown that the shorter the distance required for hydrogen to reach the bubble, the faster the degassing rate. Our company chose a rotating rotor deaerator developed by FOSECO for deaeration of aluminum alloy liquid. Its working principle is: the rotating rotor breaks up the large bubbles of ordinary inert gas into small bubbles, and disperses them in the molten metal. By reducing the diameter of the bubbles, the surface area of the bubbles increases sharply, and there is more inertness. The surface of the bubble is in contact with the hydrogen and impurities in the molten metal, thereby improving the degassing efficiency. Rotating rotor degassing is recognized as one of the best degassing processes. The structure diagram of the rotating rotor degassing machine is: the motor drives the rotating rod and the graphite rotor to rotate, and the inert gas enters the rotating rod through the rotating coupling. The rotating rod and the graphite rotor have a central hole that allows the inert gas to pass through and spray into the metal liquid. The rotating graphite rotor breaks up the inert gas bubbles into very fine bubbles, which are diffused throughout the molten metal. By adjusting and controlling the flow rate of the inert gas and the speed of the graphite rotor, the size of the bubbles is controlled and the purification effect is improved. At the same time, the refining agent placed on the degassing machine is added to the processed aluminum liquid in a certain proportion to ensure that the oxide scum is further removed during the degassing. Refining process requirements: transfer the aluminum water in the smelting furnace to the rotary deaerator with a transfer water bag: the nitrogen pressure required to be controlled at 0.1-0.3mpa to prevent the aluminum from splashing and hurting; the time for refining and degassing Controlled within 5min. The slag removal and refining of die-cast aluminum alloy is a time process, which cannot be completed quickly. It is a wrong operation to shorten the refining time. Both the adsorption of gas in the molten aluminum and the floating of impurities require a fixed time, only a guarantee There is sufficient adsorption time and impurity floating time to achieve the purpose of refining. During refining, ensure that the aluminum liquid is in full contact with the bubbles. Constant agitation is necessary. The gas in the aluminum liquid is removed and the impurities are removed to ensure product pores. The rate is reduced, the hard points are reduced, and the quality is guaranteed.
5.Conclusion
Choosing a reasonable smelting process in the production process of die-casting aluminum alloy is the first step to obtain excellent die-casting product quality. Strict control of raw materials is a key step in smelting. At the same time, it is necessary to have a simple understanding of the effects of different elements in the alloy before smelting. Slag removal and refining are very important processes in the smelting process of aluminum alloys. Through theoretical research on slag removal and degassing, a suitable smelting process for our company has been obtained.
Please keep the source and address of this article for reprinting:The Melting And Treatment Of ADC12
Minghe Die Casting Company are dedicated to manufacture and provide quality and high performance Casting Parts(metal die casting parts range mainly include Thin-Wall Die Casting,Hot Chamber Die Casting,Cold Chamber Die Casting),Round Service(Die Casting Service,Cnc Machining,Mold Making,Surface Treatment).Any custom Aluminum die casting, magnesium or Zamak/zinc die casting and other castings requirements are welcome to contact us.
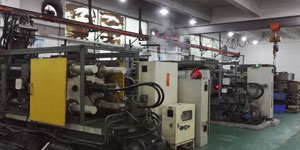
Under the control of ISO9001 and TS 16949,All processes are carried out through hundreds of advanced die casting machines, 5-axis machines, and other facilities, ranging from blasters to Ultra Sonic washing machines.Minghe not only has advanced equipment but also have professional team of experienced engineers,operators and inspectors to make the customer’s design come true.
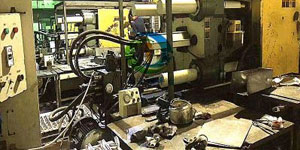
Contract manufacturer of die castings. Capabilities include cold chamber aluminum die casting parts from 0.15 lbs. to 6 lbs., quick change set up, and machining. Value-added services include polishing, vibrating, deburring, shot blasting, painting, plating, coating, assembly, and tooling. Materials worked with include alloys such as 360, 380, 383, and 413.
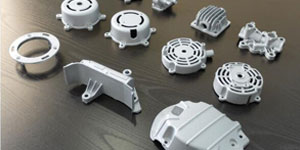
Zinc die casting design assistance/concurrent engineering services. Custom manufacturer of precision zinc die castings. Miniature castings, high pressure die castings, multi-slide mold castings, conventional mold castings, unit die and independent die castings and cavity sealed castings can be manufactured. Castings can be manufactured in lengths and widths up to 24 in. in +/-0.0005 in. tolerance.
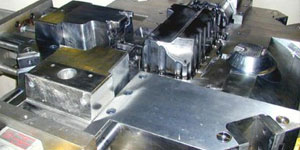
ISO 9001: 2015 certified manufacturer of die cast magnesium, Capabilities include high-pressure magnesium die casting up to 200 ton hot chamber & 3000 ton cold chamber, tooling design, polishing, molding, machining, powder & liquid painting, full QA with CMM capabilities, assembly, packaging & delivery.
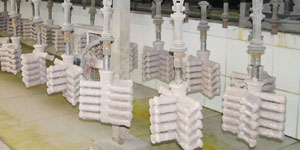
ITAF16949 certified. Additional Casting Service Include investment casting,sand casting,Gravity Casting, Lost Foam Casting,Centrifugal Casting,Vacuum Casting,Permanent Mold Casting,.Capabilities include EDI, engineering assistance, solid modeling and secondary processing.
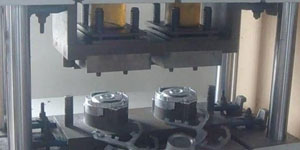
Casting Industries Parts Case Studies for: Cars, Bikes, Aircraft, Musical instruments, Watercraft, Optical devices, Sensors, Models, Electronic devices, Enclosures, Clocks, Machinery, Engines, Furniture, Jewelry, Jigs, Telecom, Lighting, Medical devices, Photographic devices, Robots, Sculptures, Sound equipment, Sporting equipment, Tooling, Toys and more.
What Can we help you do next?
∇ Go To Homepage For Die Casting China
→Casting Parts-Find out what we have done.
→Ralated Tips About Die Casting Services
By Minghe Die Casting Manufacturer |Categories: Helpful Articles |Material Tags: Aluminum Casting, Zinc Casting, Magnesium Casting, Titanium Casting, Stainless Steel Casting, Brass Casting,Bronze Casting,Casting Video,Company History,Aluminum Die Casting |Comments Off