The Method For Repairing Casting Defects
Repair situation and equipment analysis Caster glue: simple, extensive castings, generally repairing does not require subsequent processing, and there is no special strength and hardness requirements. The added value of this type of casting is relatively low.
Welding repair: More than 90% of foundry manufacturers choose welding repair to solve the casting defects encountered in production. Due to the use of metal filler (welding material generally matches the material of the casting), the weld repair performance can basically reach the standard of the base metal, and the operation is simple, and the welding repair efficiency is high. It is recognized and trusted by many manufacturers.
At present, there are many types of welding machines in the market, and they are generally used in defect repairing, which are generally as follows: Electric welding machines: traditional methods used for welding and repair of cast iron and cast steel.
Advantages: repair large defects, high efficiency. Disadvantages: The hardness of the solder joints after welding is too high, there are internal stresses, and cracks are prone to occur. Generally, annealing heat treatment is required to meet the processing requirements. In addition, due to the limitation of welding conditions, secondary defects such as pores and slag inclusion are prone to occur inside.
Argon arc welding: precision castings (alloy steel, stainless steel precision castings), aluminum alloy die castings are mostly welded by argon arc welding machines. Some mold manufacturing and repairing manufacturers also use this welder to repair mold defects.
Advantages: high welding repair efficiency and higher accuracy than electric welding machines. There are many types of welding wire, and the most widely used in stainless steel and aluminum alloy products. It can be used for welding with high strength.
Disadvantages: Used for defect repair. When repairing small defects (pores, sand holes), there are traces on the edge of the molten pool due to excessive impact. Welded steel parts have hard spots. Due to thermal influence, thermal deformation is likely to occur when welding non-ferrous castings or thin-walled parts. Operational technical requirements are high.
Cold welding machine: It is a new repair technology born at the beginning of the 21st century. Because the workpiece generates very little heat in the welding repair process, it is called a cold welding machine. After several years of development, the application direction and technology of welding machines have been greatly developed, and they have occupied a large share of the repair market.
According to the classification of repair products: placement machine and electric spark surfacing repair machine.
Mounter: Adopt the principle of instantaneous high-frequency discharge to paste the solder tabs (0.05-0.20mm) to the surface of the workpiece. The maximum thickness of each pasting is equal to the thickness of the solder tabs. The welding quality depends on whether the discharge is uniform. It is suitable for workpiece wear and processing tolerance repair, and has a certain influence in the mold market. The machine can also fill solder powder (or processing waste) to defects (such as blisters), and repair them after discharge. The color difference of the repaired workpiece is small. The disadvantage is that the repair speed is slow. The common disadvantage of cold welding machines is that the welding repair efficiency is not as high as that of electric welding machines and argon arc welding machines. However, when repairing millimeter-level defects and machining surface defects, its outstanding advantages make people prefer cold welding.
Please keep the source and address of this article for reprinting:The Method For Repairing Casting Defects
Minghe Die Casting Company are dedicated to manufacture and provide quality and high performance Casting Parts(metal die casting parts range mainly include Thin-Wall Die Casting,Hot Chamber Die Casting,Cold Chamber Die Casting),Round Service(Die Casting Service,Cnc Machining,Mold Making,Surface Treatment).Any custom Aluminum die casting, magnesium or Zamak/zinc die casting and other castings requirements are welcome to contact us.
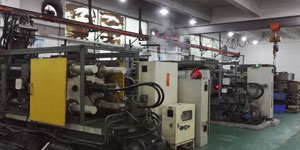
Under the control of ISO9001 and TS 16949,All processes are carried out through hundreds of advanced die casting machines, 5-axis machines, and other facilities, ranging from blasters to Ultra Sonic washing machines.Minghe not only has advanced equipment but also have professional team of experienced engineers,operators and inspectors to make the customer’s design come true.
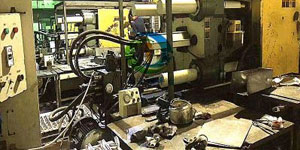
Contract manufacturer of die castings. Capabilities include cold chamber aluminum die casting parts from 0.15 lbs. to 6 lbs., quick change set up, and machining. Value-added services include polishing, vibrating, deburring, shot blasting, painting, plating, coating, assembly, and tooling. Materials worked with include alloys such as 360, 380, 383, and 413.
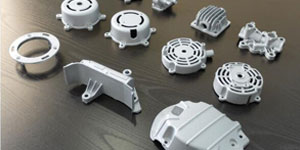
Zinc die casting design assistance/concurrent engineering services. Custom manufacturer of precision zinc die castings. Miniature castings, high pressure die castings, multi-slide mold castings, conventional mold castings, unit die and independent die castings and cavity sealed castings can be manufactured. Castings can be manufactured in lengths and widths up to 24 in. in +/-0.0005 in. tolerance.
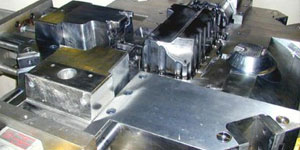
ISO 9001: 2015 certified manufacturer of die cast magnesium, Capabilities include high-pressure magnesium die casting up to 200 ton hot chamber & 3000 ton cold chamber, tooling design, polishing, molding, machining, powder & liquid painting, full QA with CMM capabilities, assembly, packaging & delivery.
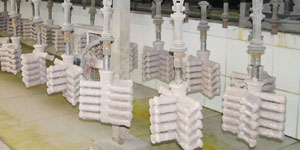
ITAF16949 certified. Additional Casting Service Include investment casting,sand casting,Gravity Casting, Lost Foam Casting,Centrifugal Casting,Vacuum Casting,Permanent Mold Casting,.Capabilities include EDI, engineering assistance, solid modeling and secondary processing.
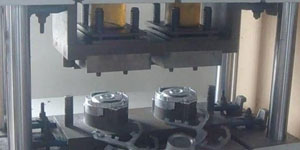
Casting Industries Parts Case Studies for: Cars, Bikes, Aircraft, Musical instruments, Watercraft, Optical devices, Sensors, Models, Electronic devices, Enclosures, Clocks, Machinery, Engines, Furniture, Jewelry, Jigs, Telecom, Lighting, Medical devices, Photographic devices, Robots, Sculptures, Sound equipment, Sporting equipment, Tooling, Toys and more.
What Can we help you do next?
∇ Go To Homepage For Die Casting China
→Casting Parts-Find out what we have done.
→Ralated Tips About Die Casting Services
By Minghe Die Casting Manufacturer |Categories: Helpful Articles |Material Tags: Aluminum Casting, Zinc Casting, Magnesium Casting, Titanium Casting, Stainless Steel Casting, Brass Casting,Bronze Casting,Casting Video,Company History,Aluminum Die Casting |Comments Off