The Method Of Reducing Oxide Inclusions In Bearing Steel
Inclusion in steel is one of the main factors affecting the contact fatigue life of bearing steel. The key to control the inclusions in steel is to control the oxygen content and oxides in steel. The main ideas to reduce oxide inclusions in steel are as follows.
1、 Control of carbon content at tapping end of primary refining furnace
When the carbon content at the tapping end is too low, the dissolved oxygen in the steel is high, which leads to the consumption of a large amount of aluminum during subsequent deoxidation, and the total amount of inclusions will increase, which brings difficulties to the later refining; In addition, the oxidizability of slag will increase obviously, so it is difficult to adjust and control the composition of slag in later refining. But too high carbon content at tapping end will bring pressure to process control of primary refining furnace. In EAF smelting, the end-point carbon content is generally controlled at about 0.2%.
2、 Selection of suitable deoxidizer
In the production process of bearing steel, the oxygen content in the steel can be reduced and a proper amount of acid soluble aluminum can be obtained by final deoxidation with aluminum. When the content of acid soluble aluminum is too high, the protection of molten steel is not good, which is easy to lead to secondary oxidation, thus increasing the content of brittle Al2O3 inclusions; When the content of acid soluble aluminum is low, the secondary oxidation of silicon and the decrease of molten steel temperature lead to the precipitation of dissolved oxygen, which leads to the formation of coarse silicate inclusions rich in SiO2. According to the research, when the content of acid soluble aluminum in the steel is controlled at 0.02% ~ 0.04%, the grain size of the steel can be refined, so as to obtain higher strength and toughness.
Barium is an ideal deoxidizing modifier. Barium alloy not only has strong deoxidizing ability, but also can denature the residual inclusions in steel. According to the research, after deoxidizing the bearing steel with Si Al Ba alloy, the total oxygen content in the steel rapidly drops to a stable value. Finally, there is no barium containing spheroidal inclusions in the steel, and the residual inclusions in the steel are well denatured. The inclusions are fine, dispersed and evenly distributed.
Magnesium has a significant effect on the modification of Al2O3 inclusions in bearing steel. According to the research, when the content of acid soluble aluminum is 0.03%, there is 210-4% magnesium in the steel, that is to say, the inclusion of Al 2O 3 can be modified into MgO · Al 2O 3, and the content of Mg in the steel is more than 10% μ The results show that the Al 2O 3 inclusions with m are transformed into fine and spherical mg Al spinel inclusions, of which less than 5 μ 46%, the others are 5 ~ 10 μ M.
3、 Optimization of refining slag composition
It is found that when the binary basicity of refining slag increases from 2.0 to 4.5, the total oxygen content at the end of molten steel decreases from 20 10-6 to 11 10-6, and the total number and area of inclusions decrease. The typical inclusions in molten steel refined by high basicity slag are brittle inclusions such as Al2O3 and Al Mg spinel, whose size is less than 5 μ m。 Increasing the content of Al2O3 or adding CaF2 and reducing the content of MgO can significantly improve the speed and ability of refining slag to adsorb inclusions.
4、 Optimization of smelting process
In order to obtain high-quality steel, increasing the amount of molten iron and selecting high-quality scrap for smelting are commonly used methods. In ladle metallurgy process, accurately controlling the content of Al, Si or Ca in steel to promote deoxidation and desulfurization, using protective casting in the whole process, the inclusion content will be greatly reduced. Vacuum melting is an important way to reduce the content of inclusions. In higher vacuum, the oxygen content in steel can be reduced to below 10-6. Electroslag refining can obtain better smelting effect than vacuum smelting. Electroslag refining not only reduces the oxygen content in the steel, but also reduces the size of inclusions in the steel, so that the distribution of inclusions is more uniform. After remelting, it provides opportunities for large inclusions to float up.
At present, vacuum induction and vacuum consumable smelting are widely used in bearing steel for important purposes at home and abroad. The purity of new stainless bearing steel 6Cr14Mo produced by this process has been greatly improved, the oxygen content is only 510-4, and the oxide inclusions are less in quantity, smaller in size and more evenly distributed.
Please keep the source and address of this article for reprinting: The Method Of Reducing Oxide Inclusions In Bearing Steel
Minghe Die Casting Company are dedicated to manufacture and provide quality and high performance Casting Parts(metal die casting parts range mainly include Thin-Wall Die Casting,Hot Chamber Die Casting,Cold Chamber Die Casting),Round Service(Die Casting Service,Cnc Machining,Mold Making,Surface Treatment).Any custom Aluminum die casting, magnesium or Zamak/zinc die casting and other castings requirements are welcome to contact us.
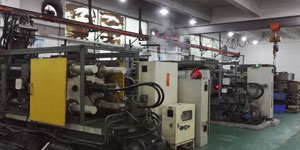
Under the control of ISO9001 and TS 16949,All processes are carried out through hundreds of advanced die casting machines, 5-axis machines, and other facilities, ranging from blasters to Ultra Sonic washing machines.Minghe not only has advanced equipment but also have professional team of experienced engineers,operators and inspectors to make the customer’s design come true.
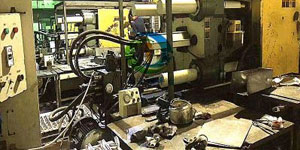
Contract manufacturer of die castings. Capabilities include cold chamber aluminum die casting parts from 0.15 lbs. to 6 lbs., quick change set up, and machining. Value-added services include polishing, vibrating, deburring, shot blasting, painting, plating, coating, assembly, and tooling. Materials worked with include alloys such as 360, 380, 383, and 413.
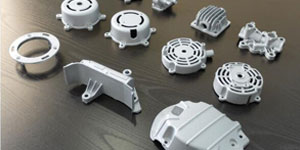
Zinc die casting design assistance/concurrent engineering services. Custom manufacturer of precision zinc die castings. Miniature castings, high pressure die castings, multi-slide mold castings, conventional mold castings, unit die and independent die castings and cavity sealed castings can be manufactured. Castings can be manufactured in lengths and widths up to 24 in. in +/-0.0005 in. tolerance.
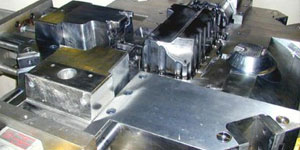
ISO 9001: 2015 certified manufacturer of die cast magnesium, Capabilities include high-pressure magnesium die casting up to 200 ton hot chamber & 3000 ton cold chamber, tooling design, polishing, molding, machining, powder & liquid painting, full QA with CMM capabilities, assembly, packaging & delivery.
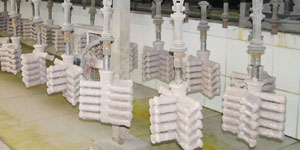
ITAF16949 certified. Additional Casting Service Include investment casting,sand casting,Gravity Casting, Lost Foam Casting,Centrifugal Casting,Vacuum Casting,Permanent Mold Casting,.Capabilities include EDI, engineering assistance, solid modeling and secondary processing.
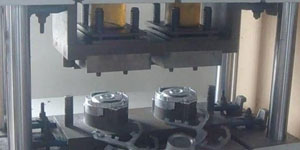
Casting Industries Parts Case Studies for: Cars, Bikes, Aircraft, Musical instruments, Watercraft, Optical devices, Sensors, Models, Electronic devices, Enclosures, Clocks, Machinery, Engines, Furniture, Jewelry, Jigs, Telecom, Lighting, Medical devices, Photographic devices, Robots, Sculptures, Sound equipment, Sporting equipment, Tooling, Toys and more.
What Can we help you do next?
∇ Go To Homepage For Die Casting China
→Casting Parts-Find out what we have done.
→Ralated Tips About Die Casting Services
By Minghe Die Casting Manufacturer |Categories: Helpful Articles |Material Tags: Aluminum Casting, Zinc Casting, Magnesium Casting, Titanium Casting, Stainless Steel Casting, Brass Casting,Bronze Casting,Casting Video,Company History,Aluminum Die Casting |Comments Off