The Methods To Improve Electromagnetic Pure Iron Wear Resistance
Electromagnetic pure iron is a widely used soft magnetic material. It has high magnetic induction and is suitable for making magnetic parts that work in a strong magnetic field. Electromagnetic pure iron materials are cheap, and the heat treatment process is simple. At present, they are widely used in civil aircraft products. However, the alloying element content of electromagnetic pure iron material is almost zero, there is no alloy strengthening phase, and its hardness is the lowest among iron metals. Electromagnetic pure iron is often used as parts such as the shell, armature, valve core, and movable iron core of solenoid valves.
The structure and execution of the solenoid valve are roughly similar to a small actuator. At the same time, electromagnetic pure iron parts play the role of general structural parts, even transmission parts, and must have certain mechanical strength and good wear resistance. Many electromagnetic pure iron parts of the solenoid valve move relative to each other when they are working, and surface friction occurs. If the material hardness is not enough, it will seriously affect the working life of the device. Therefore, the surface of the pure iron material must be strengthened. Nitriding process can improve the surface hardness of pure iron. However, the nitriding treatment of electromagnetic pure iron has the risk of reducing its magnetic properties. Therefore, finding a suitable nitriding process can improve the surface hardness of the pure iron material while keeping its magnetic properties within the required range of actual use. , It is necessary.
The Beijing Institute of Aeronautical Materials has optimized the nitriding process according to the characteristics of flight control servo actuators in civil aircrafts working in a strong magnetic field. While ensuring the magnetic performance requirements of B5000, B10000, coercivity and maximum permeability, the surface hardness It was increased to more than 900 HV, and good results were obtained. Their research uses DT4A electromagnetic pure iron material, the surface roughness is controlled at 1.6 μm, the sample is annealed at 900 ℃ before nitriding, and the surface hardness after annealing is 120 HV0.01. The nitriding medium is pure ammonia gas. Before entering the nitriding medium, the sample is kept at 350°C for 40 min. During the holding time, compressed air is filled. After the nitriding is completed, it is filled with 110 kPa pressure nitrogen and cooled to below 150°C.
The uniformity and thickness of the surface dense layer after nitriding are the most critical factors that determine the hardness of pure iron after nitriding. The nitriding process must ensure that a continuous surface dense layer is formed, and the thickness should be above 5 μm. Through comparative experiments, it was found that under the following process conditions: temperature 450℃, holding time 240min, ammonia decomposition rate 6-7/%, this surface dense layer can be obtained. X-ray diffraction shows that the surface phase is composed of γ'phase, Fe3N (ε phase) and α phase, and a dense continuous mixed layer of γ'phase and ε phase is formed on the surface. The presence of the mixed layer improves the surface hardness of the sample. The test proved that the surface hardness reached HV0.01 = 986. The increase in nitriding time can increase the thickness of the mixed layer, but it hardly thickens after reaching about 5 μm.
The magnetic performance test of the sample showed that the low magnetic properties of the sample B500 and B1000 decreased by 16% and 10%, respectively, the medium magnetic properties of B2500 decreased by 4%, but the strong magnetic properties of B5000 and B10000 only decreased by 1.5% and 1%. Compared with the technical requirements in GB/T 6983-1986 "Technical Conditions for Electromagnetic Pure Iron Bars", the low magnetic properties and medium magnetic properties are relatively low, but the strong magnetic properties can meet the requirements of the national standard; the coercivity of the sample and the maximum The magnetic permeability also meets the requirements of the national standard.
The above research proves that, in response to the requirement of electromagnetic pure iron material in the flight control servo actuator for strong magnetic field work, by adjusting the nitriding process parameters, the sample can achieve the strength of strong magnetic performance, coercivity and maximum permeability after nitriding. The technical indicators can meet the comprehensive requirements of its magnetic performance and hardness, so that the surface wear resistance of electromagnetic pure iron parts can be solved, and the long life of civil aircraft flight control servo actuator products can be realized.
Please keep the source and address of this article for reprinting: The Methods To Improve Electromagnetic Pure Iron Wear Resistance
Minghe Die Casting Company are dedicated to manufacture and provide quality and high performance Casting Parts(metal die casting parts range mainly include Thin-Wall Die Casting,Hot Chamber Die Casting,Cold Chamber Die Casting),Round Service(Die Casting Service,Cnc Machining,Mold Making,Surface Treatment).Any custom Aluminum die casting, magnesium or Zamak/zinc die casting and other castings requirements are welcome to contact us.
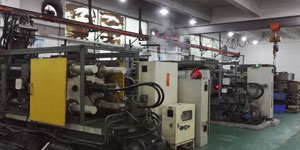
Under the control of ISO9001 and TS 16949,All processes are carried out through hundreds of advanced die casting machines, 5-axis machines, and other facilities, ranging from blasters to Ultra Sonic washing machines.Minghe not only has advanced equipment but also have professional team of experienced engineers,operators and inspectors to make the customer’s design come true.
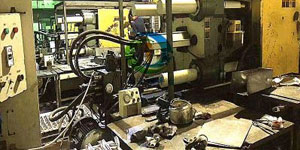
Contract manufacturer of die castings. Capabilities include cold chamber aluminum die casting parts from 0.15 lbs. to 6 lbs., quick change set up, and machining. Value-added services include polishing, vibrating, deburring, shot blasting, painting, plating, coating, assembly, and tooling. Materials worked with include alloys such as 360, 380, 383, and 413.
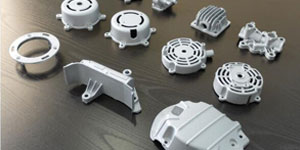
Zinc die casting design assistance/concurrent engineering services. Custom manufacturer of precision zinc die castings. Miniature castings, high pressure die castings, multi-slide mold castings, conventional mold castings, unit die and independent die castings and cavity sealed castings can be manufactured. Castings can be manufactured in lengths and widths up to 24 in. in +/-0.0005 in. tolerance.
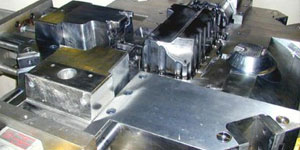
ISO 9001: 2015 certified manufacturer of die cast magnesium, Capabilities include high-pressure magnesium die casting up to 200 ton hot chamber & 3000 ton cold chamber, tooling design, polishing, molding, machining, powder & liquid painting, full QA with CMM capabilities, assembly, packaging & delivery.
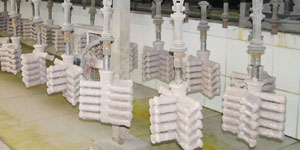
ITAF16949 certified. Additional Casting Service Include investment casting,sand casting,Gravity Casting, Lost Foam Casting,Centrifugal Casting,Vacuum Casting,Permanent Mold Casting,.Capabilities include EDI, engineering assistance, solid modeling and secondary processing.
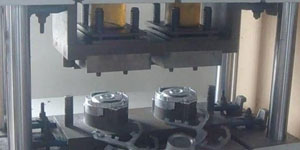
Casting Industries Parts Case Studies for: Cars, Bikes, Aircraft, Musical instruments, Watercraft, Optical devices, Sensors, Models, Electronic devices, Enclosures, Clocks, Machinery, Engines, Furniture, Jewelry, Jigs, Telecom, Lighting, Medical devices, Photographic devices, Robots, Sculptures, Sound equipment, Sporting equipment, Tooling, Toys and more.
What Can we help you do next?
∇ Go To Homepage For Die Casting China
→Casting Parts-Find out what we have done.
→Ralated Tips About Die Casting Services
By Minghe Die Casting Manufacturer |Categories: Helpful Articles |Material Tags: Aluminum Casting, Zinc Casting, Magnesium Casting, Titanium Casting, Stainless Steel Casting, Brass Casting,Bronze Casting,Casting Video,Company History,Aluminum Die Casting |Comments Off