The New Way To Purify Molten Iron
In recent years, China's machinery manufacturing industry has brought an epoch-making leap to China's manufacturing industry in the process of integrating with international standards. In particular, the rapid development of traditional and emerging industries such as automobile manufacturing, wind power generation, and metallurgical machinery, coupled with the new trend of international manufacturing shifting to China and Asian countries, has injected vitality and vitality into China’s traditional foundry industry, making China foundry Karma has gained room for survival and development.
Whoever has new technologies, new processes, and new products will have the first opportunity to win in the fierce market competition. The continuous improvement of the quality of casting products, especially the strict requirements of foreign high-end castings on the quality of molten iron, has caused us to face new challenges and new contradictions. How to obtain high-quality molten iron with high cleanliness and adopt effective molten iron purification measures to produce high-quality casting products has attracted widespread attention and great attention from the domestic foundry industry. Next, I will elaborate on the proposition of "breaking through the casting bottleneck and exploring new ways to purify molten iron".
The impact of molten iron purity on the quality of casting products
As we all know. There are many factors that affect the quality of castings. Such as modeling, process flow, raw material quality, worker quality, molten iron quality, heat treatment process, casting processing, etc. However, molten iron quality is an important factor affecting the quality of castings. The concept of traditional molten iron quality is composed of three major indicators: molten iron temperature, chemical composition, and purity. According to the current trend of adding various metals to produce alloyed molten iron, certain metal elements have also brought about the segregation problem of the metallographic structure while optimizing the metallographic structure of the molten iron. At present, the precise control of the temperature and chemical composition of the molten iron is no longer a problem, and many methods are effective. Although the research on the problems of molten iron purification and the uniformity of the metallographic structure has attracted the attention of many domestic manufacturers, no concrete and feasible measures have been formulated. In some monographs analyzing the occurrence mechanism of casting defects and prevention measures, more attention has been paid to the problems of modeling and process design, and the causal relationship between the low purity of molten iron, poor metallographic structure uniformity and the formation of casting defects has been ignored. Misunderstandings appeared when thinking about the formation mechanism of various casting defects.
- First of all, in the production of castings, because the molten iron is not pure and the uniformity of the metallographic structure is objective, there is no need to question it. Because the molten iron is in the process of smelting, tempering, and adding various metal elements. There are various harmful gases and various non-metallic inclusions in the water, and due to the material characteristics, melting point, density, and particle size during the process of adding certain metal elements Other factors. It is difficult to ensure that they melt evenly in molten iron. The objective existence and effect of these factors caused various casting defects after the molten iron solidified, which affected the performance of casting products: the hard spots formed by non-metallic inclusions also affected the cutting performance of castings.
- Secondly, with the same chemical composition and the same metallographic structure, we found that in the process of benchmarking domestic parts and imported parts, imported parts are often 1-2 grades higher than domestic parts: the hardness of imported parts is higher than the cutting performance of domestic parts. On the contrary, the main reason for the superiority of domestic castings is that the uniformity of the metallographic structure of the material is good.
Analysis of the causes of impure molten iron
The causes of various harmful gases and various non-metallic inclusions in molten iron are discussed in detail in many casting monographs. At present, the impurity and poor uniformity of molten iron caused by non-metallic inclusions in cast iron, ferrosilicon alloy inoculant, rare earth spheroidizing agent and rare earth vermicularizing agent account for more than 60% of the casting material scrap rate.
It is understood. Now that the manufacturers of ferrosilicon are restricted by the resources of silica and steel scraps and driven by cost reduction, most manufacturers use cheap iron oxide scales (containing about 60% of iron oxide) to replace relatively expensive steel scraps; silica is charged into the furnace. The silicon content is lower than the national standard, and the silica containing less than 98% is used as shoddy; in order to pursue high yield and low power consumption, the low furnace temperature of the ferrosilicon directly leads to the low purity of the ferrosilicon product and the large amount of slag inclusion. The increase is very harmful to casting. Because the melting point of silicon carbide is as high as 2 450 ℃ or more, it is difficult for our conventional molten iron temperature to melt it and remain in the molten iron, forming casting defects. Especially in gray iron smelting, the more prominent slag accumulation agent is difficult to completely eliminate.
In terms of pig iron production, high-quality iron ore resources are becoming increasingly scarce. Some manufacturers re-mined low-grade iron ore that was abandoned in the past to produce cast iron. These companies often use blast furnaces below 200 m3 for smelting. The temperature of the blast furnace is not equipped with hot blast furnaces. The harmful elements in the ore are not burnt cleanly. In addition to the unreasonable raw material preparation, there are serious problems with the purity of the cast iron produced. Bring various impurities and oxides to the molten iron. Problems in the production of spheroidizing agents are also very prominent. Due to the state's control of rare earth resources
In particular, the strict regulation of the Baotou Baiyun Obo rare earth mine has forced most domestic manufacturers of nodulizers to produce nodulizers from recycled rare-earth raw materials in Mianning, Sichuan. Its absorption rate and use effect are greatly reduced, making the originally impure molten iron worse.
The above-mentioned reasons directly affect the purity of molten iron should be taken seriously and effective measures should be taken to solve it.
Specific measures for the purification of molten iron
With FAW Foundry Co., Ltd. as the leader, Baotou Xinghuo Rare Earth Ferroalloy Co., Ltd. specifically cooperates with the organic combination of the two industrial chains of smelting and smelting, effectively solving the problem of molten iron purification, solving the difficult problems that have plagued the foundry industry chain for many years, and breaking through the bottleneck of casting And proposed specific solutions in production as follows.
- (1) The use of high-temperature smelting above 1500℃ is an effective measure to improve the purification of molten iron, especially the hot air or oxygen-enriched air used in cupola smelting can effectively improve the quality of molten iron and make the quality of molten iron purified and even. In this regard, the huge gap between domestic and foreign countries should arouse great attention and gradually narrow the gap in this regard.
- (2) Large amounts of scrap steel with high purity are used. If the process permits, increase the input of scrap steel to replace pig iron, and the purity of molten iron can be significantly improved by increasing carbon. When we were investigating some famous European automobile foundry companies, we found a common problem through the analysis and comparison of their iron smelting process and casting charge, which is to make a fuss about the purification of molten iron, and the large-scale use of scrap steel instead of pig iron is one of the basic measures. . For example, the amount of nodular iron crankshaft scrap for car engines produced by our company's special foundry for FAW-Volkswagen has reached 70%, and the next step is to increase it to 90% after the resources are stabilized. At present, the comprehensive scrap rate of ductile iron crankshafts is below 2%, which is recognized by the German side, completely replacing German imported products. The material quality and processing performance have reached the international advanced level.
- (3) The use of rare earth magnesium alloy cored wire as a spheroidizing agent reduces the impurities brought by the block spheroidizing agent to the molten iron and improves the purity of the molten iron after spheroidization, while the spheroidization rate reaches more than 90%. We have used this process on some export castings that require high spheroidization grades and have achieved good results. Because the rare earth magnesium alloy cored wire is a high-purity material, and its absorption rate is 30% higher than that of the block spheroidizing agent.
- (4) It is very important that the cast iron must be produced in a blast furnace of more than 200m3. The quality of pig iron on the market is uneven. The influence of some trace harmful elements in pig iron on the quality of castings cannot be underestimated.
- (5) Other charging materials such as ferrosilicon, rare earth spheroidizing agent, inoculant, rare earth vermillioning agent and rare earth master alloy, etc. We require rare earth ferroalloy manufacturers to adopt the complete deslagging process of rare earth smelting to purify the impurities in these charges Go out to obtain extremely pure materials. Take ferrosilicon as an example, it is necessary to use high-grade ferrosilicon, that is, the internationally used ferrosilicon with a silicon content of more than 75%, and the quality of ferrosilicon used as an inoculant should be strictly controlled to ensure uniform composition and prevent casting lumpiness. Too large causes uneven component segregation during condensation. At present, many domestic enterprises have not paid enough attention to this and are still using the national standard ferrosilicon whose silicon content is basically at the lower limit of 72%.
- (6) The solution to the uniformity of molten iron is to use master alloys. Some high-melting or low-melting metal elements that must be added in an appropriate amount are not added separately in the traditional method of adding in front of the furnace, but are handed over to the ferroalloy manufacturer to make a special intermediate alloy from the previous industrial chain to solve the problem. In the past, we used the method of adding various metals to the electric smelting furnace or adding to the molten iron ladle to adjust the composition of the molten iron in front of the furnace. From the actual effect, there are the following shortcomings. Due to the limitation of molten iron temperature and the difference between the melting point and density of some metals added and molten iron, it is easy to produce metallographic deviation of castings. Then we use the characteristics of the equipment and process of ferroalloy production enterprises and their patented technology to effectively solve the problem by producing special master alloys such as the chromium-manganese-silicon alloy additives currently used by our company, rare earth chromium-platinum-manganese-silicon alloy additives, and silicon-calcium-manganese alloy additives. Alloy melting and uniformity issues greatly reduce the incidence of hard spots. According to the characteristics, melting point, temperature, density, and particle size of various materials, a new type of master alloy is produced by synthesis or purification technology as a nodulizer, vermicularizing agent, alloy additive or inoculant to treat molten iron instead of being added separately before the casting furnace Methods of certain metal elements. Because the production of the alloy adopts the new process of full slag removal for mixed smelting, it effectively solves the organic combination between rare earths and various metals, so that the technical components of rare earth and other intermediate alloys are very stable, accurate, pure and free of impurities. Through the metallographic analysis of castings, the use of master alloys has a uniform structure and stable use, which greatly improves the yield of castings. Later, it has become one of the basic measures to reduce the rejection rate of castings. At present, domestic and foreign steel companies also use the method of adding master alloys to refining molten steel to produce high-quality steel.
By taking the above measures, the molten iron in casting has been effectively purified, which greatly improves the inherent quality of our company's castings. The various castings of Jiefang trucks produced by our company are praised by users for their high quality. Due to the improvement of the quality of castings, the market for car castings is also expanding. At the same time, we promote the localization of some castings of FAW-Volkswagen Company. This all stems from some exploratory work we have done in the field of molten iron purification, and we have achieved impressive results. Satisfactory results. It has not only realized the breakthrough of the difficult points in the casting process control process, but also improved the quality of the castings, increased the yield of castings production, and achieved good economic benefits.
Please keep the source and address of this article for reprinting:The New Way To Purify Molten Iron
Minghe Die Casting Company are dedicated to manufacture and provide quality and high performance Casting Parts(metal die casting parts range mainly include Thin-Wall Die Casting,Hot Chamber Die Casting,Cold Chamber Die Casting),Round Service(Die Casting Service,Cnc Machining,Mold Making,Surface Treatment).Any custom Aluminum die casting, magnesium or Zamak/zinc die casting and other castings requirements are welcome to contact us.
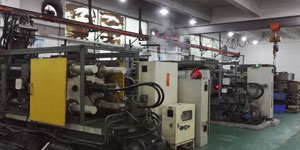
Under the control of ISO9001 and TS 16949,All processes are carried out through hundreds of advanced die casting machines, 5-axis machines, and other facilities, ranging from blasters to Ultra Sonic washing machines.Minghe not only has advanced equipment but also have professional team of experienced engineers,operators and inspectors to make the customer’s design come true.
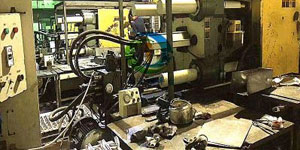
Contract manufacturer of die castings. Capabilities include cold chamber aluminum die casting parts from 0.15 lbs. to 6 lbs., quick change set up, and machining. Value-added services include polishing, vibrating, deburring, shot blasting, painting, plating, coating, assembly, and tooling. Materials worked with include alloys such as 360, 380, 383, and 413.
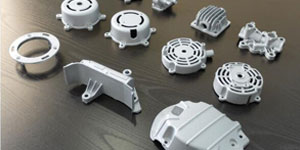
Zinc die casting design assistance/concurrent engineering services. Custom manufacturer of precision zinc die castings. Miniature castings, high pressure die castings, multi-slide mold castings, conventional mold castings, unit die and independent die castings and cavity sealed castings can be manufactured. Castings can be manufactured in lengths and widths up to 24 in. in +/-0.0005 in. tolerance.
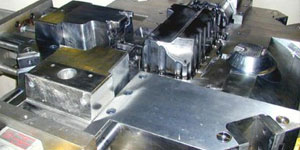
ISO 9001: 2015 certified manufacturer of die cast magnesium, Capabilities include high-pressure magnesium die casting up to 200 ton hot chamber & 3000 ton cold chamber, tooling design, polishing, molding, machining, powder & liquid painting, full QA with CMM capabilities, assembly, packaging & delivery.
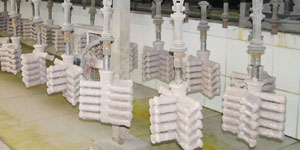
ITAF16949 certified. Additional Casting Service Include investment casting,sand casting,Gravity Casting, Lost Foam Casting,Centrifugal Casting,Vacuum Casting,Permanent Mold Casting,.Capabilities include EDI, engineering assistance, solid modeling and secondary processing.
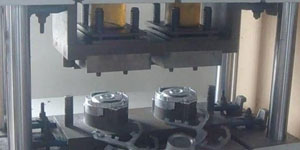
Casting Industries Parts Case Studies for: Cars, Bikes, Aircraft, Musical instruments, Watercraft, Optical devices, Sensors, Models, Electronic devices, Enclosures, Clocks, Machinery, Engines, Furniture, Jewelry, Jigs, Telecom, Lighting, Medical devices, Photographic devices, Robots, Sculptures, Sound equipment, Sporting equipment, Tooling, Toys and more.
What Can we help you do next?
∇ Go To Homepage For Die Casting China
→Casting Parts-Find out what we have done.
→Ralated Tips About Die Casting Services
By Minghe Die Casting Manufacturer |Categories: Helpful Articles |Material Tags: Aluminum Casting, Zinc Casting, Magnesium Casting, Titanium Casting, Stainless Steel Casting, Brass Casting,Bronze Casting,Casting Video,Company History,Aluminum Die Casting |Comments Off