The Operation And Precautions Of Flame Heating Surface Quenching
Preparation before quenching
- 1. The workpiece must undergo pre-heat treatment such as quenching and tempering, normalizing, etc.
- 2. The surface of the workpiece is not allowed to have oxide scale, dirt, oil stains, etc.
- 3. The workpiece with severe decarburization, cracks, blisters and pores on the surface cannot be flame quenched
Flame preheating
Cast steel, cast iron, alloy steel can be slowly heated to about 300~500ºC with a quenching nozzle with a small flame to prevent cracking.
The quenching temperature of steel parts is Ac3+(80~100ºC), and the quenching temperature of iron castings is 730ºC+28×ωSi ºC -25×ωMnºC.
Flame intensity:
- 1. Commonly used fuel gas is acetylene and oxygen, and the ratio of acetylene to oxidation is 1:1.5~1:1.25.
- 2. The oxygen pressure is 0.2~0.5MPa, and the acetylene pressure is 0.003~0.007MPa (the pressure of the float-type acetylene generator is 0.006MPa). Generally, it is better for the flame to be blue and neutral.
- 3. The working pressure of coal gas is 0.003MPa, and the power of propane gas is 0.005~0.01Mpa.
Distance between flame and workpiece:
- 1. Shaft workpieces are generally 8~15mm, the lower limit for large pieces is closer, and the upper limit for small pieces with complex shapes is farther.
- 2. When the gear with modulus less than 8 is heated and quenched at the same time, the distance between the nozzle flame center and the tooth tip is preferably 18mm, and the circular linear velocity of the gear is less than 6m/min.
- 3. When the single tooth of the gear is quenched sequentially, the distance between the flame center and the tooth surface is 2~4mm.
Nozzle or workpiece moving speed:
- 1. Rotation method: linear speed is 50~200mm/min
- 2. Advance method: linear speed is 100~180mm/min
Distance between flame center and spray hole:
- 1. Continuous quenching: 10~20mm, too close, water is easy to splash and fire. Too far, insufficient or too deep hardened layer.
- 2. The water spray column should be inclined backward by 10º~30º, and there should be a partition between the water spray hole and the fire hole.
Quenching medium:
- 1. Tap water, the water pressure is 200~300kPa.
- 2. For alloy steel parts with complex shapes, use 30~40ºC for 1.5~2h, and large workpieces can be tempered by themselves (cold to about 300ºC).
Please keep the source and address of this article for reprinting:The Operation And Precautions Of Flame Heating Surface Quenching
Minghe Die Casting Company are dedicated to manufacture and provide quality and high performance Casting Parts(metal die casting parts range mainly include Thin-Wall Die Casting,Hot Chamber Die Casting,Cold Chamber Die Casting),Round Service(Die Casting Service,Cnc Machining,Mold Making,Surface Treatment).Any custom Aluminum die casting, magnesium or Zamak/zinc die casting and other castings requirements are welcome to contact us.
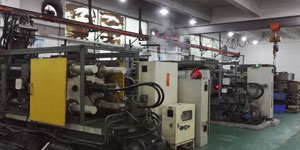
Under the control of ISO9001 and TS 16949,All processes are carried out through hundreds of advanced die casting machines, 5-axis machines, and other facilities, ranging from blasters to Ultra Sonic washing machines.Minghe not only has advanced equipment but also have professional team of experienced engineers,operators and inspectors to make the customer’s design come true.
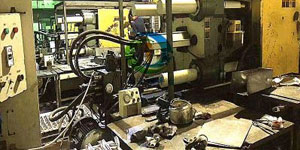
Contract manufacturer of die castings. Capabilities include cold chamber aluminum die casting parts from 0.15 lbs. to 6 lbs., quick change set up, and machining. Value-added services include polishing, vibrating, deburring, shot blasting, painting, plating, coating, assembly, and tooling. Materials worked with include alloys such as 360, 380, 383, and 413.
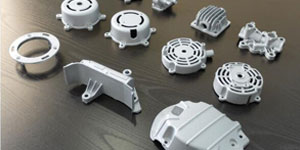
Zinc die casting design assistance/concurrent engineering services. Custom manufacturer of precision zinc die castings. Miniature castings, high pressure die castings, multi-slide mold castings, conventional mold castings, unit die and independent die castings and cavity sealed castings can be manufactured. Castings can be manufactured in lengths and widths up to 24 in. in +/-0.0005 in. tolerance.
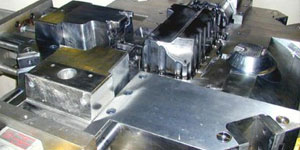
ISO 9001: 2015 certified manufacturer of die cast magnesium, Capabilities include high-pressure magnesium die casting up to 200 ton hot chamber & 3000 ton cold chamber, tooling design, polishing, molding, machining, powder & liquid painting, full QA with CMM capabilities, assembly, packaging & delivery.
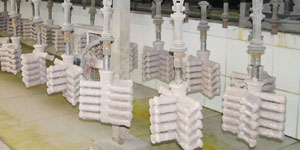
ITAF16949 certified. Additional Casting Service Include investment casting,sand casting,Gravity Casting, Lost Foam Casting,Centrifugal Casting,Vacuum Casting,Permanent Mold Casting,.Capabilities include EDI, engineering assistance, solid modeling and secondary processing.
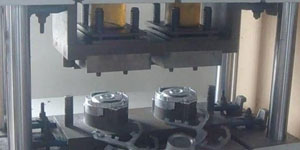
Casting Industries Parts Case Studies for: Cars, Bikes, Aircraft, Musical instruments, Watercraft, Optical devices, Sensors, Models, Electronic devices, Enclosures, Clocks, Machinery, Engines, Furniture, Jewelry, Jigs, Telecom, Lighting, Medical devices, Photographic devices, Robots, Sculptures, Sound equipment, Sporting equipment, Tooling, Toys and more.
What Can we help you do next?
∇ Go To Homepage For Die Casting China
→Casting Parts-Find out what we have done.
→Ralated Tips About Die Casting Services
By Minghe Die Casting Manufacturer |Categories: Helpful Articles |Material Tags: Aluminum Casting, Zinc Casting, Magnesium Casting, Titanium Casting, Stainless Steel Casting, Brass Casting,Bronze Casting,Casting Video,Company History,Aluminum Die Casting |Comments Off