The Precautions Of Cold Box Technology
1Using an amino acid scrubber for exhaust gas purification
Add sulfuric acid to a clean scrubber. If triethylamine is used, the solution must contain 23% sulfuric acid. If the solution is to be prepared in the scrubber, first add water and then slowly add concentrated sulfuric acid, and there should be good agitation, exothermic reaction.
If the amount of solution in the scrubber decreases due to evaporation, just add water to maintain the liquid level. (Or use about 80% phosphoric acid for neutralization).
The pH value of the liquid must be checked frequently. When the pH is higher than 4.5, the acid is waste. The solution in the entire scrubber needs to be poured out, and a new solution is added. If the time is too late, you can add some concentrated sulfuric acid for a while.
2 Sand core hardening time is too long
Sand core weight and ideal hardening time:
Sand cores of different weights have different hardening times because of insufficient amine supply from the amine generator. A 14-inch (889px) thick sand core has the same hardening time as a small sand core.
Hardening pressure:
- Low pressure: 2PSI—9PSI (0.0138Mpa—0.062Mpa),
- High pressure: 15-30PSI (0.1MPa—0.2Mpa).
Generally, increasing the amount of amine and increasing the purification pressure of the core box will greatly reduce the hardening time.
Others: The venting system of the core box must fulfill its total venting area, the ratio of intake and exhaust areas, and whether the venting is uniform.
3 The sand core does not harden when demolding
For these unhardened parts, it is usually necessary to extend the hardening time; this phenomenon is that some parts of the sand core do not pass through the amine gas. The corrective method is to extend the hardening cycle or improve it according to the above-mentioned method.
The amine is not fixed by the unhardened sand core, and the uncured position of the local sand core with uneven sand mixing is variable. This is a way to distinguish the two reasons for the local uncured sand core.
4 The amount of triethylamine is too large
Among them (1) and (2) are two main reasons:
- (1) The core box air passage is improper, causing a gas short circuit in the thinner part of the core.
- (2) The hardening pressure is too low to allow the catalyst in the intake zone to diffuse and press into every corner of the core.
- (3) If the exhaust area in the horizontally divided core box is larger than the intake area, a gas short circuit will also occur, causing the gas to pass through the core with the least resistance to form a short circuit channel. This phenomenon can be overcome when more catalysts are used. (The balance of exhaust during side blowing and blowing is not very important. When the exhaust setting is correct, the resistance of the sand to the gas will establish sufficient back pressure, even if the exhaust area is larger than the intake area, the gas can be dispersed) .
- (4) The negative pressure applied on the exhaust side of the core box will further promote short circuits and insufficient core box pressure. Although the purpose of applying negative pressure is to remove the catalyst, at the same time it reduces the barrier effect of the molding sand on the airflow. This reduces the ability of the amine gas to diffuse to the side. The exhaust zone should be controlled within the range of +1PSI (+0.006895Mpa) and -1PSI (-0.006895Mpa) during blowing and high negative pressure.
- (5) Parting surface leakage or leakage between the positive pressure area of the intake air and the core box. The same phenomenon is caused by the leakage caused by the poor sealing of the air blowing port of the core box with side-blown sand. The catalyst that has leaked into the air cannot be used to harden the core. Leakage not only affects the normal pressure of the cavity, but also pollutes the working environment.
5 Triethylamine smell is too big
- 1) Leakage of generator;
- 2), tooling leakage;
- 3) Clean the amine remaining in the core after blowing. The uniformly hardened and uniformly blown core has almost no detectable amine odor. The residual amine smell is firstly caused by improper core box exhaust, and secondly, the amount of amine is large and a small amount of cleaning air is used. This problem can be solved by increasing the cleaning and blowing time before correcting the tooling.
6 dip mold
"The so-called dipping means that a part of the resin remains on the core box. This phenomenon cannot be avoided by adding more release agent.
Cause of:
Factors that cause insufficient compaction of the sand core will cause the resin to remain on the core box when the sand core is demolded;
When the hardened layer is not thick enough, and the applied high-pressure curing gas takes a long time, a layer of resin will be attached near the vent hole and separated from other sand cores. This phenomenon will occur in any parting surface form , The reason is that excessive curing gas brings the resin to the vicinity of the vent;
The phenomenon of mold sticking is related to the composition of sand particles. When the shape of the sand particles is polygonal rather than round, the tendency is more increased. The resin is uniform on the surface of the round sand particles, and there is excess resin coating in the concave corners of the polygonal sand particles. The vent plug is blocked, so that the entire inner cavity of the core box is attached with a layer of resin film. This phenomenon is very common. The solution is to clean the core box with a cleaning agent (or dry ice cleaning). The phenomenon of mold sticking is also related to the distance from the sand injection nozzle to the impact point and the sand injection pressure. The closer the distance, the greater the sand injection pressure and the greater the tendency to stick the mold. The impact point is also the most vulnerable part of the mold."
The solution to the problem of mold staining:
- (1) Improve resin composition and add internal release agent;
- (2) When it is too late to replace the resin, stick transparent tape on the part of the core box that is easy to stick to the mold. Because of the wetting angle, after sticking on the transparent tape, it will not stick. This method is simple and easy to do, and it is immediate, but it is just a solution. After sand shooting, the edge of the tape is warped, which provides us with a feasible idea for plating a certain kind of coating on the mold to solve the problem of mold sticking.
7 Defects of bright carbon
Mr. Li Chuanshi of the China Foundry Association believes: “This kind of defect is easy to occur along the two sides of the first molten iron entering the cavity, and it is also easy to occur near the inner gate. It is common on the side and above the liquid flow. If the gating system used makes the mold If turbulence occurs in the cavity, the film may be flushed into the casting to form a subcutaneous sandwich. If the film is sandwiched between two streams, it may penetrate the casting and cause the casting to leak." The defects on the surface of the castings like cracks in the picture below are bright carbon.
Measures to prevent defects in bright carbon
If bright carbon defects are found on the castings, some measures can be taken to prevent such defects in the process when it is inconvenient to switch to resins with a lower bright carbon index.
- (1) Increasing the pouring temperature can strengthen the oxidizing atmosphere in the mold during the filling process, and can effectively oxidize the hydrocarbons produced by pyrolysis, thereby reducing or eliminating bright carbon defects. Experiments have proved that this defect can be completely eliminated after the pouring temperature is increased to 1480°C.
- (2) Increasing the pouring rate and shortening the pouring time can reduce the amount of pyrolysis of the resin during the filling process, thereby effectively reducing the precipitation of the bright carbon film.
- (3) Increase the vent hole of the mold to discharge the resin pyrolysis product, which can also effectively reduce the bright carbon defect.
- (4) Adding iron red powder (Fe2O3) 2% to the surface sand can completely eliminate the bright carbon defect. However, after 2% iron red powder is added to the resin sand, the mold strength will be significantly reduced. According to foreign research reports, using aluminum sulfate instead of iron red powder only needs 1% addition to achieve the same effect. In this case, the impact on the strength of the resin sand is very small."
8 High scrap core rate and damage during storage and transportation
- (1) The problem of the inclination of the mold;
- (2) The mold is not smooth;
- (3) The initial strength (strength from the mold) is too low;
- (4) The density of the sand core is low (the loose shot is not solid)-adjust the shot Sand pressure or correction tooling to keep the balance between sand shooting and exhaust. The fluidity of cold core sand should be considered when designing tooling.
The low hardness of a local location is often caused by the low density of that location, while the low hardness of the entire sand core may be caused by insufficient core sand agitation, or caused by too low gas pressure during the hardening period. The core sand is not well mixed, or the mixing is not complete, or the amount of resin is small, or the water content of the raw sand is high, the water content of the compressed air is high, the sand temperature is lower than 10℃, the resin temperature is low, the viscosity is high, and the fineness of the molding sand is low. Angular coefficient, mud content and fine powder content are also influencing factors.
9 Veining and sintering
The main reason is:
At 573°C, the expansion stress caused by the phase change of the quartz sand and the volume change caused the sand mold or sand core to crack. The more concentrated the particle size of quartz sand, the greater the probability of sand core cracking. The higher the silica content of quartz sand, the greater the probability of sand core cracking. The veining tendency of quartz sand with relatively round grain shape and finer grain size is more serious than that of quartz sand with multi-angle grain shape and coarser grain size.
The molten metal penetrates into the cracks to form veins. The temperature of the interface between the sand core and the molten iron is higher than the solidus temperature of iron. This will continue as soon as the infiltration starts. Only when the leading edge of the infiltrating molten iron solidifies, the penetration stops. The sand core cracks or pores penetrate the entire cross-section of the core to form the so-called sand core sintering, that is, the metal infiltration type mechanical sanding. Facts have proved that this kind of metal penetration is impossible to clean up, so the casting has to be scrapped. To avoid or reduce veining and metal penetration defects, it is necessary to overcome the sand core cracking and inhibit the penetration of molten metal into the cracks.
Solution: Adding some degrading additives to the molding sand or core sand can reduce the expansion stress of the sand mold and reduce the veining tendency. Choose low silica content sand, and choose 4 or even 5 sieves to reduce the veining tendency; improve the sand core In the high temperature strength and toughness, to ensure that the surface layer is subjected to the thermal phase transformation stress, the deformation of its own can alleviate the cracking tendency; the use of sintered coatings on the surface of the sand core that is prone to veining is also to make the sand core in the high temperature molten iron High temperature toughness and high temperature strength can be achieved under the action of thermal shock. From another perspective, when the molten metal contacts the surface of the sand core to form a hot zone, if this part of the heat is quickly diffused and transferred to the inside of the sand core by technological means, the temperature of the sand core surface can be as short as possible It is similar to the inside of the sand core. On the other hand, when the molten metal contacts and impacts the surface of the sand core, if the surface of the sand core can chill the molten metal and accelerate the shrinkage, the molten metal can be solidified quickly, plus the sand core The heat toughness formed on the surface at high temperature will prevent veining more effectively.
Adding 5%-10% of Maikexing can effectively prevent veining defects.
Another: use special sand.
10 Prevention of cracked nitrogen holes
When the amount of carbon and silicon is low, the solubility of N in molten iron increases, thin-walled parts control N<0.013%, thick-walled parts control: N<0.008%,
The content of Ti in the molten iron: 0.02%-0.025%. The nitrogen fixation effect of Ti can eliminate the cracked nitrogen holes. Of course, adding iron oxide powder to the sand is also one of the methods.
11 Water-based paint or alcohol-based paint, application time
Water-based coatings are preferred because alcohol-based coatings have a large penetration depth and have a large impact on the strength of the sand core.
Application time of water-based paint: timely application and timely drying. It is recommended to complete application within half an hour and dry immediately. Do not apply for more than 2 hours after the core is removed, because the solvent will evaporate within 2 hours, and the solvent can prevent the coating water from penetrating into the sand core.
Application time of alcohol-based paint: When alcohol-based paint has to be used for various reasons, it must be applied after the core is released. It is best to apply after 8 hours, or apply after 4 hours. The reason is alcohol-based The penetration of the paint causes the strength of the core to decrease. In actual production, of course, there are also applications immediately after the core is produced, but it is a helpless approach and is not recommended.
12 Sand inclusion and scarring defects in the inner cavity of the cold box casting
Yu Mingdao, Xing Qimin, Xu Zhixin and Niu Benqing from Yituo Group have detailed analysis and discussion on this issue. I won't repeat it here, but focus on the influence of the "bad thermal effects of sand cores" of several teachers, as shown in the figure below: Many manufacturers solve the problem of scarring as soon as the "water in the drape seam" is eliminated.
13 The opening of the sand nozzle on the working surface of the cold core box sand core
Many units have sand-shooting nozzles on the round rod cores of the cylinders.
14 The problem of dipping the whole core of the cold box
To what extent is the core assembly, the cleaning of the core support paint of the cylinder water jacket, the drying of the sand core, and the problem of the overflow groove of the sand core paint before drying.
15 The device for raising the upper template of the cold core machine when changing the template
A device that can stand up the upper template for easy maintenance and cleaning during quick mold change.
16 The problem of the angle of repose of the mixture in the sand shooting head of the cold core machine
Considering that the core making machine is not big enough and you want to shoot a larger sand core or the stroke is too small, the opening angle of the sand shooting head is too large. It may be that the farthest sand shooting nozzle is in the first and second molds due to the repose angle of the mixture. When there is no sand, a sand guide block should be set on the sand shooting board at this time.
Please keep the source and address of this article for reprinting:The Precautions Of Cold Box Technology
Minghe Die Casting Company are dedicated to manufacture and provide quality and high performance Casting Parts(metal die casting parts range mainly include Thin-Wall Die Casting,Hot Chamber Die Casting,Cold Chamber Die Casting),Round Service(Die Casting Service,Cnc Machining,Mold Making,Surface Treatment).Any custom Aluminum die casting, magnesium or Zamak/zinc die casting and other castings requirements are welcome to contact us.
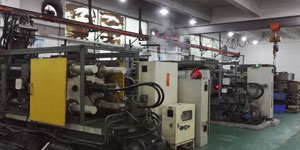
Under the control of ISO9001 and TS 16949,All processes are carried out through hundreds of advanced die casting machines, 5-axis machines, and other facilities, ranging from blasters to Ultra Sonic washing machines.Minghe not only has advanced equipment but also have professional team of experienced engineers,operators and inspectors to make the customer’s design come true.
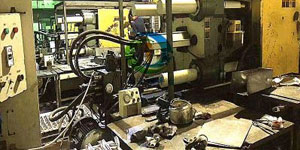
Contract manufacturer of die castings. Capabilities include cold chamber aluminum die casting parts from 0.15 lbs. to 6 lbs., quick change set up, and machining. Value-added services include polishing, vibrating, deburring, shot blasting, painting, plating, coating, assembly, and tooling. Materials worked with include alloys such as 360, 380, 383, and 413.
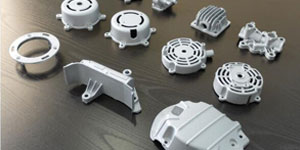
Zinc die casting design assistance/concurrent engineering services. Custom manufacturer of precision zinc die castings. Miniature castings, high pressure die castings, multi-slide mold castings, conventional mold castings, unit die and independent die castings and cavity sealed castings can be manufactured. Castings can be manufactured in lengths and widths up to 24 in. in +/-0.0005 in. tolerance.
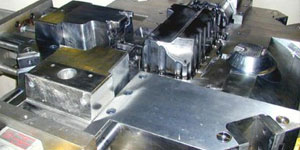
ISO 9001: 2015 certified manufacturer of die cast magnesium, Capabilities include high-pressure magnesium die casting up to 200 ton hot chamber & 3000 ton cold chamber, tooling design, polishing, molding, machining, powder & liquid painting, full QA with CMM capabilities, assembly, packaging & delivery.
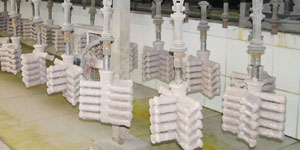
ITAF16949 certified. Additional Casting Service Include investment casting,sand casting,Gravity Casting, Lost Foam Casting,Centrifugal Casting,Vacuum Casting,Permanent Mold Casting,.Capabilities include EDI, engineering assistance, solid modeling and secondary processing.
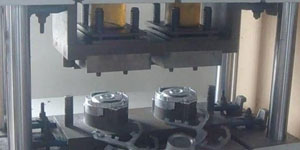
Casting Industries Parts Case Studies for: Cars, Bikes, Aircraft, Musical instruments, Watercraft, Optical devices, Sensors, Models, Electronic devices, Enclosures, Clocks, Machinery, Engines, Furniture, Jewelry, Jigs, Telecom, Lighting, Medical devices, Photographic devices, Robots, Sculptures, Sound equipment, Sporting equipment, Tooling, Toys and more.
What Can we help you do next?
∇ Go To Homepage For Die Casting China
→Casting Parts-Find out what we have done.
→Ralated Tips About Die Casting Services
By Minghe Die Casting Manufacturer |Categories: Helpful Articles |Material Tags: Aluminum Casting, Zinc Casting, Magnesium Casting, Titanium Casting, Stainless Steel Casting, Brass Casting,Bronze Casting,Casting Video,Company History,Aluminum Die Casting |Comments Off