The Problems And Countermeasures Of Cutting Fluid Deterioration-Smell
The main reason for the deterioration and smell of cutting fluid is that the cutting fluid contains a large number of bacteria, and the bacteria in the cutting fluid mainly include aerobic bacteria and anaerobes. Aerobic bacteria live in environments with minerals, such as water, concentrated liquid of cutting fluid, and oil leaked from machine tools. Under aerobic conditions, they split into two every 20-30 minutes.
The anaerobic bacteria live in an environment without oxygen, split into two per hour, metabolize and release SO2, smell of rotten eggs, and the cutting fluid turns black. When the bacteria in the precision laser cutting and cutting fluid is greater than 106, the cutting fluid will become smelly.
Bacteria enter the cutting fluid mainly through the following channels
- Bacteria invade during the preparation process, such as bacteria in the water used to prepare the cutting fluid.
- Bacteria in the air enter the cutting fluid.
- The transfer of workpieces between processes causes the infection of cutting fluid.
- Bad habits of operators, such as littering.
- The cleanliness of the machine tool and workshop is poor.
Methods to control the growth of bacteria
- Use high-quality, stable cutting fluid.
- Using pure water to prepare a concentrated solution is not only easy to prepare, but also can improve the lubricity of the cutting fluid, reduce the amount of chips carried away, and prevent bacterial erosion.
- When using, it is necessary to control the ratio of the concentrated liquid in the cutting fluid not to be too low, otherwise it is easy to cause bacteria to grow.
- Since the oil used by the machine tool contains bacteria, it is necessary to minimize the oil leaked from the machine tool mixed into the cutting fluid.
- When the pH of the cutting fluid is between 8.3 and 9.2, it is difficult for bacteria to survive, so new cutting fluid should be added in time to increase the pH.
- Keep the cutting fluid clean and do not allow the cutting fluid to come into contact with dirt, oil, food, tobacco, etc.
- Frequent use of bactericides.
- Keep the workshop and machine tools clean.
- If the equipment does not have a filter device, the oil slick should be regularly skimmed to remove dirt.
Please keep the source and address of this article for reprinting: The Problems And Countermeasures Of Cutting Fluid Deterioration-Smell
Minghe Die Casting Company are dedicated to manufacture and provide quality and high performance Casting Parts(metal die casting parts range mainly include Thin-Wall Die Casting,Hot Chamber Die Casting,Cold Chamber Die Casting),Round Service(Die Casting Service,Cnc Machining,Mold Making,Surface Treatment).Any custom Aluminum die casting, magnesium or Zamak/zinc die casting and other castings requirements are welcome to contact us.
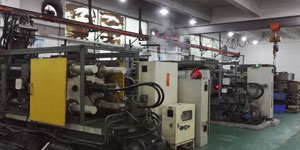
Under the control of ISO9001 and TS 16949,All processes are carried out through hundreds of advanced die casting machines, 5-axis machines, and other facilities, ranging from blasters to Ultra Sonic washing machines.Minghe not only has advanced equipment but also have professional team of experienced engineers,operators and inspectors to make the customer’s design come true.
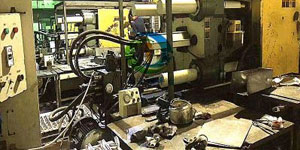
Contract manufacturer of die castings. Capabilities include cold chamber aluminum die casting parts from 0.15 lbs. to 6 lbs., quick change set up, and machining. Value-added services include polishing, vibrating, deburring, shot blasting, painting, plating, coating, assembly, and tooling. Materials worked with include alloys such as 360, 380, 383, and 413.
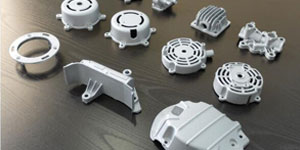
Zinc die casting design assistance/concurrent engineering services. Custom manufacturer of precision zinc die castings. Miniature castings, high pressure die castings, multi-slide mold castings, conventional mold castings, unit die and independent die castings and cavity sealed castings can be manufactured. Castings can be manufactured in lengths and widths up to 24 in. in +/-0.0005 in. tolerance.
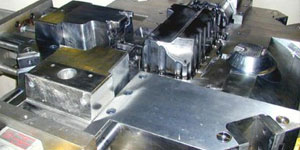
ISO 9001: 2015 certified manufacturer of die cast magnesium, Capabilities include high-pressure magnesium die casting up to 200 ton hot chamber & 3000 ton cold chamber, tooling design, polishing, molding, machining, powder & liquid painting, full QA with CMM capabilities, assembly, packaging & delivery.
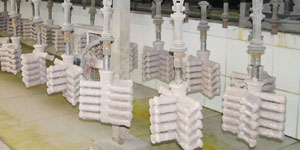
ITAF16949 certified. Additional Casting Service Include investment casting,sand casting,Gravity Casting, Lost Foam Casting,Centrifugal Casting,Vacuum Casting,Permanent Mold Casting,.Capabilities include EDI, engineering assistance, solid modeling and secondary processing.
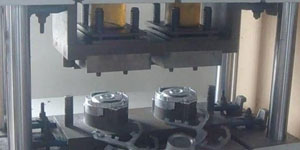
Casting Industries Parts Case Studies for: Cars, Bikes, Aircraft, Musical instruments, Watercraft, Optical devices, Sensors, Models, Electronic devices, Enclosures, Clocks, Machinery, Engines, Furniture, Jewelry, Jigs, Telecom, Lighting, Medical devices, Photographic devices, Robots, Sculptures, Sound equipment, Sporting equipment, Tooling, Toys and more.
What Can we help you do next?
∇ Go To Homepage For Die Casting China
→Casting Parts-Find out what we have done.
→Ralated Tips About Die Casting Services
By Minghe Die Casting Manufacturer |Categories: Helpful Articles |Material Tags: Aluminum Casting, Zinc Casting, Magnesium Casting, Titanium Casting, Stainless Steel Casting, Brass Casting,Bronze Casting,Casting Video,Company History,Aluminum Die Casting |Comments Off