The Problems and Solutions of Internal Defects of Aluminum Alloy Die Castings
Internal Defects Of Die Castings
Stoma
(1) Features and inspection methods: Appearance inspection or flaw detection inspection after dissection, the pores have a smooth surface and a round shape.
(2) Reasons:
- The direction of introduction of the alloy liquid is unreasonable or the flow velocity of the molten metal is too high, resulting in injection;
- The exhaust duct is blocked prematurely or the frontal impacts the wall to form a vortex to envelop the air. This kind of pores are mostly caused by poor or deep exhaust. At the cavity;
- Because the charge is not clean or the smelting temperature is too high, more gas in the molten metal is not removed, precipitated during solidification, and cannot be fully discharged;
- The coating has a large amount of gas or is used too much, and it is not cleared before pouring. Pouring clean, so that the gas is involved in the casting, this gas mostly presents a dark gray surface; the high-speed switching point is wrong.
(3) Treatment method:
- Using clean furnace charge, controlling the melting temperature, and performing exhaust treatment;
- Choosing reasonable process parameters, injection speed, and high-speed switching point;
- Guiding the metal liquid pressure to balance, filling the cavity in an orderly manner, favorable for gas exhaust;
- Exhausting groove, The overflow tank should have sufficient exhaust capacity;
- Choose a paint with a small air volume and control the air volume.
Shrinkage and porosity
(1) Features and inspection methods:
- Anatomy or flaw detection, the shape of the holes is irregular, not smooth, and the surface is dark;
- Large and concentrated, small shrinkage holes and scattered shrinkage porosity.
(2) Reasons:
- During the solidification process of the casting, cavities are caused by shrinkage and no metal compensation;
- The pouring temperature is too high, and the mold temperature gradient distribution is unreasonable;
- The injection ratio is low, and the boost pressure is too low;
- Inner gate Thinner, too small area, premature solidification, which is not conducive to pressure transmission and liquid metal feeding;
- There are hot spots or cross-section changes in the casting structure;
- The amount of molten metal pouring is too small, and the remaining material is too thin to lift. Feeding effect.
(3) Treatment method:
- Reduce the pouring temperature and reduce the shrinkage;
- Increase the injection pressure and boost pressure to improve the compactness;
- Modify the inner gate to make the pressure transfer better, which is conducive to the feeding effect of the liquid metal;
- Change the casting structure to eliminate Where the metal accumulates, the wall thickness is as uniform as possible;
- Speed up the cooling of thick parts;
- Thicken the material handle 15~30mm to increase the shrinking effect.
Inclusions
(1) Features and inspection methods:
The metallic or non-metallic impurities mixed into the die-casting parts can be seen irregularly, dots or holes with different sizes, colors, and heights after processing.
(2) Reasons:
- The charge is not clean and there is too much recharge;
- The alloy liquid is not refined;
- The molten slag is brought into the pouring with a spoon;
- The graphite in the graphite crucible or the coating falls off and is mixed into the molten metal;
- The temperature is high during heat preservation and lasts for a long time long.
(3) Treatment method:
Use clean alloy material, especially the dirt on the recharge material must be cleaned;
- The alloy melt must be refined and degassed, and the slag must be cleaned;
- When using a spoon to pour the liquid, carefully remove the liquid surface to avoid mixing Slag and oxide scale;
- Clean the cavity and pressure chamber;
- Control the heat preservation temperature and reduce the heat preservation time.
2.4 Brittleness
(1) Features and inspection methods:
The crystal grains of the base metal of the casting are too large or very small, which makes the casting easy to break or break.
(2) Reasons:
- The impurity of zinc, iron, lead and tin in the aluminum alloy exceeds the specified range;
- The alloy liquid is overheated or the holding time is too long, resulting in coarse grains;
- Intensive overcooling causes the grains to be too fine.
(3) Treatment method:
- Strictly control the impurity composition in the metal;
- Control the smelting process to reduce the pouring temperature;
- Increase the mold temperature.
2.5 Leakage
(1) Features and inspection methods:
Die-casting parts have undergone pressure test, resulting in air leakage and water seepage.
(2) Reasons:
- Insufficient pressure, poor density of matrix structure;
- Internal defects such as pores, shrinkage holes, slag holes, cracks, shrinkage porosity, cold partitions, patterns;
- Poor design of pouring and exhaust system;
- Die-casting punch wear and pressure Unstable shooting.
(3) Treatment method:
- Improve the specific pressure;
- take corresponding measures against internal defects;
- improve the gating system and exhaust system;
- implement treatment to make up for the defects;
- replace the pressure chamber and punch.
2.6 Non-metallic hard points
(1) Features and inspection methods:
Mechanical processing or appearance inspection or metallographic inspection after machining found that there are small particles or lumps with higher hardness than the metal matrix on the casting, which makes the tool wear seriously, and often shows different brightness after cnc machining.
(2) Reasons:
- Non-metallic hard spots;
- Inclusion of oxides on the surface of the alloy liquid;
- Reactions of aluminum alloy and furnace lining;
- Metallic materials infiltrate foreign bodies;
- Inclusions.
(3) Treatment method:
- Do not scoop the oxide on the surface of the alloy liquid into the spoon during casting;
- After removing the oxide on the surface of the iron crucible, apply paint. Clean up the residue on the furnace wall and bottom in time;
- Remove oxides on tools such as spoons;
- Use furnace lining materials that do not react with aluminum;
- Pure metal materials.
2.7 Metal hard point
(1) Features and inspection methods:
The appearance inspection or metallographic inspection during mechanical processing or after CNC machining found that there are small particles or lumps with higher hardness than the metal matrix on the castings, which makes the tool wear serious, and often shows different brightness after cnc machining.
(2) Reasons:
- Metal hard spots are mixed with unmelted silicon elements;
- Primary crystal silicon: The temperature of the aluminum liquid is lower and the parking time is longer;
- The FE and MN elements segregate to produce intermetallic compounds.
(3) Treatment method:
- When smelting aluminum-silicon alloy, do not use silicon element powder;
- When high-speed alloy composition, do not directly add silicon element, must use intermediate alloy
- Increase melting temperature and pouring temperature;
- Control alloy composition, especially FE impurities; Avoid the segregation of FE, MN and other elements;
- The Si content in the alloy should not be close to or exceed the eutectic composition;
- Control the amount of primary silicon in the matrix metallurgical structure for raw materials.
The Influencing Factors Of Defects
3.1 Common defects and influencing factors of die castings
3.2 Ideas to solve defects
Since the causes of each type of defect come from multiple different influencing factors, it is necessary to solve the problem in actual production. In the face of many reasons, is it to adjust the machine first? Or repair the mold first? It is recommended to simplify according to the degree of difficulty. After complex processing, the sequence:
- Clean the parting surface, clean the cavity, clean the ejector pin; change the coating, improve the spraying process; increase the clamping force; increase the amount of metal poured; these can be implemented by simple operations Measures.
- Adjust process parameters, injection force, injection speed, filling time, mold opening time, pouring temperature, mold temperature, etc.
- Change materials, select high-quality alloy ingots, change the ratio of new materials to reheated materials, and improve the smelting process.
- Modify the mold, modify the pouring system, add internal gates, add overflow grooves, exhaust grooves, etc.
3.3 For example, the cause of flashing in die castings
- Die casting machine problem: the clamping force is adjusted incorrectly.
- Process problem: The injection speed is too high, resulting in a pressure shock peak that is too high.
- Mold problems: deformation, debris on the parting surface, uneven wear of inserts and sliders, and insufficient template strength.
- The order of measures to solve the flash: 1. Clean the parting surface 2. Improve the clamping force 3. Adjust the process parameters 4. Repair the worn parts of the mold 5. Improve the rigidity of the mold.
Please keep the source and address of this article for reprinting:The Problems and Solutions of Internal Defects of Aluminum Alloy Die Castings
Minghe Die Casting Company are dedicated to manufacture and provide quality and high performance Casting Parts(metal die casting parts range mainly include Thin-Wall Die Casting,Hot Chamber Die Casting,Cold Chamber Die Casting),Round Service(Die Casting Service,Cnc Machining,Mold Making,Surface Treatment).Any custom Aluminum die casting, magnesium or Zamak/zinc die casting and other castings requirements are welcome to contact us.
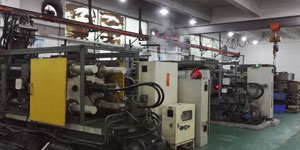
Under the control of ISO9001 and TS 16949,All processes are carried out through hundreds of advanced die casting machines, 5-axis machines, and other facilities, ranging from blasters to Ultra Sonic washing machines.Minghe not only has advanced equipment but also have professional team of experienced engineers,operators and inspectors to make the customer’s design come true.
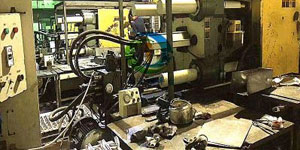
Contract manufacturer of die castings. Capabilities include cold chamber aluminum die casting parts from 0.15 lbs. to 6 lbs., quick change set up, and machining. Value-added services include polishing, vibrating, deburring, shot blasting, painting, plating, coating, assembly, and tooling. Materials worked with include alloys such as 360, 380, 383, and 413.
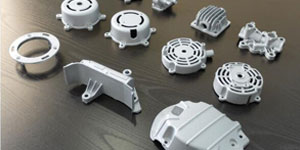
Zinc die casting design assistance/concurrent engineering services. Custom manufacturer of precision zinc die castings. Miniature castings, high pressure die castings, multi-slide mold castings, conventional mold castings, unit die and independent die castings and cavity sealed castings can be manufactured. Castings can be manufactured in lengths and widths up to 24 in. in +/-0.0005 in. tolerance.
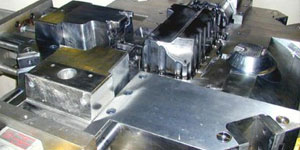
ISO 9001: 2015 certified manufacturer of die cast magnesium, Capabilities include high-pressure magnesium die casting up to 200 ton hot chamber & 3000 ton cold chamber, tooling design, polishing, molding, machining, powder & liquid painting, full QA with CMM capabilities, assembly, packaging & delivery.
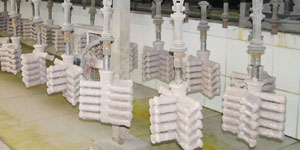
ITAF16949 certified. Additional Casting Service Include investment casting,sand casting,Gravity Casting, Lost Foam Casting,Centrifugal Casting,Vacuum Casting,Permanent Mold Casting,.Capabilities include EDI, engineering assistance, solid modeling and secondary processing.
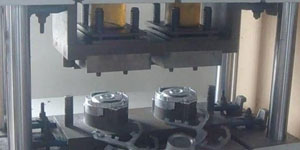
Casting Industries Parts Case Studies for: Cars, Bikes, Aircraft, Musical instruments, Watercraft, Optical devices, Sensors, Models, Electronic devices, Enclosures, Clocks, Machinery, Engines, Furniture, Jewelry, Jigs, Telecom, Lighting, Medical devices, Photographic devices, Robots, Sculptures, Sound equipment, Sporting equipment, Tooling, Toys and more.
What Can we help you do next?
∇ Go To Homepage For Die Casting China
→Casting Parts-Find out what we have done.
→Ralated Tips About Die Casting Services
By Minghe Die Casting Manufacturer |Categories: Helpful Articles |Material Tags: Aluminum Casting, Zinc Casting, Magnesium Casting, Titanium Casting, Stainless Steel Casting, Brass Casting,Bronze Casting,Casting Video,Company History,Aluminum Die Casting |Comments Off