The Process Analysis of New Type Die Casting Automotive Parts
The Mg-9Al-1Zn-0. 5Ce automobile new die-casting parts samples were die-casted, and the mechanical properties and corrosion resistance were tested and analyzed. The results show that with the increase of the pouring temperature and the acceleration of the injection speed, the tensile strength and yield strength of the sample first increase and then decrease, the corrosion potential moves positively and then gradually negatively, and the elongation rate changes slightly. Performance and corrosion resistance are both improved first and then decreased; compared with 620 ℃ pouring temperature, the tensile strength and yield strength at 650 ℃ pouring temperature increased by 13.08%, 23.78%, respectively, elongation after breaking The corrosion potential is reduced by 1%, and the corrosion potential is positively shifted by 43 mV; compared with the 1 m/s injection speed during die-casting, the tensile strength and yield strength under 3 m/s die-casting have increased by 11.20%, respectively. 16. 45%, the elongation after fracture is reduced by 0.8%, and the corrosion potential is positively moved by 31 mV. The optimal die-casting process parameters of Mg-9Al-1Zn-0. 5Ce automobile new die-casting parts are: 650 ℃ initial forging temperature, 3 m/s injection speed.
Preface In today's rapid economic development, people's lives and travel are increasingly inseparable from automobiles, and there are higher requirements for the quality, performance, economy, and service life of automobiles. At the same time, based on the impact of new development concepts such as energy saving, emission reduction, consumption reduction, and lightweight, automotive materials are becoming more lightweight, high-performance, and environmentally friendly. Lightweight metals such as aluminum and magnesium alloys have received more research and applications. However, there are many types of auto parts and complex shapes, such as cylinder blocks, gearboxes, cylinder heads, wheels, etc., which are mostly large and complex thin-walled parts. Therefore, the production process is gradually shifting to die-casting. Die-casting parts for automobiles have been affected by the industry. More attention and application. Although the die-casting process is better than ordinary casting technology, the surface is smoother, the wall is thinner, the precision, the strength is higher, the process is simple, the production efficiency is high, and the raw materials can be greatly saved, but the die-casting process is only suitable for fluid metal processing, and its development is subject to certain In addition, die-casting also has certain casting defects, which are easy to produce pores, oxide impurities, etc., and the cost of equipment and molds required for die-casting is higher, so it is suitable for mass production. Although my country’s die-casting technology is becoming more mature, greatly improving the quality and performance of auto parts, but based on the high requirements of the industry and society on the performance of auto die-casting parts, it is necessary to continuously develop and innovate die-casting technology to promote new-type auto die-casting. The development of parts and components has taken a step forward.
1. Test
The research object is Mg-9Al-1Zn-0.5Ce automobile new die-casting parts. The raw materials of Mg-9Al-1Zn-0.5Ce alloy are pure magnesium ingots, aluminum ingots, zinc ingots, cerium powder, and fine manganese with a purity of more than 99%. powder.
The smelting is carried out in a crucible resistance furnace. First, preheat the crucible. After the crucible turns dark red, sprinkle RJ-2 flux on the bottom and around the crucible, and add magnesium ingots, fine manganese powder, cerium powder, aluminum ingots, and zinc ingots in batches. After all the components are melted, slag removal and refining are carried out. After standing for 10 minutes, the alloy liquid is poured into the cavity of the 1250kN horizontal cold chamber die casting machine, and the die casting test is carried out on the 1250kN horizontal cold chamber die casting machine. During the die-casting process, keep the preheating temperature of the mold at 250°C and the injection pressure of 90MPa unchanged, and change the pouring temperature and injection speed.
All die-cast samples were not heat treated. The main dimensions of the new automobile die-casting parts forgings are: outer diameter 88mm, height 54mm, thickness 5mm, inner diameter 42mm, and total length 101mm.
The mechanical properties of the new Mg-9Al-1Zn-0.5Ce automobile die-casting parts are tested at room temperature. The instrument uses the Instron8032 electronic tensile testing machine, which is stretched at a constant speed of 2mm/min, and the strength, elongation after fracture and fracture are recorded. The morphology was observed with S-530 scanning electron microscope. Corrosion resistance is tested at room temperature using electrochemical corrosion method, the test instrument is PARSTAT electrochemical three-electrode system system, the corrosion medium is NaCl solution, the concentration is 3.5%, the polarization curve test is performed at a speed of 0.4mV/s, and combined with the analysis software Tafel fitting, record the electrochemical parameters (corrosion potential), and observe the corrosion morphology with S-530 scanning electron microscope.
2. Test results and discussion
2.1 Test of mechanical properties of samples at different pouring temperatures
The test results of the mechanical properties of the Mg-9Al-1Zn-0.5Ce automobile new die-casting parts samples prepared at a constant injection speed of 3m/s at different pouring temperatures. It can be seen that the lower the pouring temperature, the lower the strength, and the increase in pouring temperature can effectively enhance the tensile strength and yield strength of the sample, and the elongation after fracture is relatively slightly reduced. The tensile strengths at pouring temperatures of 620, 635, 650, 675, 700 ℃ are 237, 253, 268, 257, 242 MPa, the yield strength is 143, 165, 177, 169, 154 MPa, and the elongation after fracture is respectively 8.9%, 8.2%, 7.9%, 8.1%, 8.4%.
It can be seen that the tensile strength and yield strength of the sample are the smallest at the pouring temperature of 620°C, and the elongation after fracture is the largest. At this time, the mechanical properties of the sample are the worst; when the casting temperature is 650°C, the tensile strength of the sample is The strength and yield strength are the highest, which are increased by 13.08% and 23.78% respectively compared with 620℃ die-casting, and the elongation after fracture is only reduced by 1%. At this time, the mechanical properties are the best. When the pouring temperature continues to increase, the strength of the sample decreases, the elongation after fracture decreases, and the mechanical properties begin to decrease again.
2.2 Test of mechanical properties of samples at different injection speeds
Test results of mechanical properties of Mg-9Al-1Zn-0.5Ce automobile new die-casting parts samples prepared at a constant pouring temperature of 650℃ with different injection speeds: the slower the injection speed, the lower the intensity, and the injection speed The acceleration can effectively enhance the tensile strength and yield strength of the sample, and the elongation after fracture is relatively slightly reduced. The tensile strengths at 1, 2, 3, 4, 5m/s injection speed are 241, 255, 268, 259, and 244MPa, respectively, the yield strength is 152, 164, 177, 168, 153 MPa, and the elongation after fracture They were 8.7%, 8.4%, 7.9%, 8.2%, and 8.5% respectively. It can be seen that the tensile strength and yield strength of the sample are the smallest under the injection speed of 1m/s, and the elongation after fracture is the largest. At this time, the mechanical properties of the sample are the worst; when the die-casting speed is 3m/s, the sample’s The tensile strength and yield strength are the largest, which are increased by 11.20% and 16.45% respectively compared with 1m/s die-casting, and the elongation after fracture is only reduced by 0.8%. At this time, the mechanical properties are the best. When the injection speed continues to increase, the strength of the sample decreases, the elongation after fracture decreases, and the mechanical properties begin to decrease again. 2.3 Tensile fracture morphology of the sample
Pictures of tensile fractures of Mg-9Al-1Zn-0.5Ce automobile new type die-casting parts samples when die-casting at 620 and 650℃ respectively. It can be seen that when die-casting at two pouring temperatures, the tensile fractures of the specimens all show typical ductile fracture characteristics. When die-casting at 620℃, the tearing edge of the sample is large, the dimples are irregular, and it has poor toughness; when die-casting at 650℃, the dimples of the sample are significantly reduced, the shape is more rounded, the distribution is more regular and uniform, and the toughness is greatly improved. , The mechanical properties are the best. Synthesizing the test results of the strength and elongation of the new Mg-9Al-1Zn-0.5Ce automobile die-casting parts samples at different pouring temperatures, we can know that from the optimization of the Mg-9Al-1Zn-0.5Ce automobile new-type die-casting parts samples Considering its mechanical properties, the pouring temperature of 650℃ is preferred.
2.4 Corrosion resistance of samples at different pouring temperatures
The corrosion resistance test results of Mg-9Al-1Zn-0.5Ce automobile new die-casting parts samples prepared at a constant injection speed of 3m/s and prepared at different pouring temperatures are shown in Figure 6. It can be seen that the increase of the pouring temperature can make the corrosion potential of the sample move positively, and the corrosion resistance can be improved. As the pouring temperature increases from 620°C to 650°C, the corrosion resistance of the sample increases first and then decreases. The corrosion potentials at pouring temperatures of 620, 635, 650, 675, and 700°C were -0.924, -0.913, -0.881, -0.893, -0.908V, respectively. It can be seen that the corrosion potential of the sample is the most negative at the pouring temperature of 620℃, and the corrosion resistance of the sample is the worst; when the pouring temperature of 650℃ is die-casting, the corrosion potential of the sample is the most positive, which is more positive than that of the die-casting at 620℃. At 43mV, the corrosion resistance is the best at this time. When the pouring temperature continues to increase, the corrosion potential of the sample begins to move negatively, and the corrosion resistance begins to decline again.
2.5 Corrosion resistance of specimens at different injection speeds
The corrosion resistance test results of the Mg-9Al-1Zn-0.5Ce automobile new die-casting parts samples prepared at a constant pouring temperature of 650℃ and different injection speeds. It can be seen that the acceleration of the injection speed can make the corrosion potential of the sample move positively, and the corrosion resistance can be improved. As the injection speed increases from 1m/s to 5m/s, the corrosion potential of the sample moves positively and then gradually moves negatively. The corrosion potentials at 1, 2, 3, 4, and 5m/s injection speeds are -0.912,- 0.906, -0.881, -0.892, -0.904V. It can be seen that the corrosion potential of the sample under die-casting with an injection speed of 1m/s is the most negative, and the corrosion resistance of the sample at this time is the worst; when die-casting with an injection speed of 3m/s, the corrosion potential of the sample is the most positive, and the pressure is relatively high. When the shooting speed is 1m/s, the positive shift is 31mV, and the corrosion resistance is the best at this time. When the injection speed continues to increase, the corrosion potential of the sample begins to move negatively, and the corrosion resistance begins to decline again.
2.6 Corrosion morphology of samples under different die-casting processes
Corrosion morphology pictures of Mg-9Al-1Zn-0.5Ce automobile new die-casting parts samples when die-casting at 620 and 650℃ respectively. It can be seen that when die-casting at 620℃, the corrosion pits of the sample are densely grouped, and the depth of the pits is deep, and the corrosion degree is serious at this time; when die-casting at 650℃, the corrosion degree of the sample is greatly reduced, and only a few corrosion points appear. Corrosion potential test values of Mg-9Al-1Zn-0.5Ce automotive new die-casting parts specimens at different pouring temperatures can be known from the optimization of the corrosion resistance of Mg-9Al-1Zn-0.5Ce automotive new die-casting parts specimens Considering performance, the casting temperature of 650°C is preferred.
When the injection speed is 3m/s, the corrosion points on the surface of the sample are small and few, and the corrosion resistance is the best at this time; when the injection speed is increased to 5m/s, the corrosion of the sample is aggravated and a larger shape appears Corrosion pits, the corrosion resistance is reduced. According to the corrosion potential test values of Mg-9Al-1Zn-0.5Ce automobile new die-casting parts samples under different injection speeds, it can be known that in order to optimize the corrosion resistance of Mg-9Al-1Zn-0.5Ce automobile new die-casting parts samples , Preferably 3m/s injection speed.
3 Conclusion
Die-casting samples of new Mg-9Al-1Zn-0.5Ce automobile die-casting parts with different pouring temperatures and injection speeds, and testing and analysis of mechanical properties and corrosion resistance. The summary is as follows:
- (1) With the increase of the pouring temperature and the acceleration of the injection speed, the tensile strength and yield strength of the sample first increase and then decrease. The corrosion potential moves positively and then gradually negatively. The elongation rate changes slightly. Performance and corrosion resistance are improved first and then decreased. The tensile strength and yield strength of the new Mg-9Al-1Zn-0.5Ce automobile die-cast parts specimens at 650°C pouring temperature and 3m/s injection speed are the largest, the elongation after fracture is the smallest, the corrosion potential is the most positive, and the mechanical properties are good. The best corrosion resistance.
- (2) Compared with 620℃ pouring temperature, the tensile strength and yield strength at 650℃ pouring temperature increased by 13.08% and 23.78% respectively, the elongation after fracture decreased by 1%, and the corrosion potential shifted positively. 43mV; Compared with the 1m/s injection speed when die-casting, the tensile strength and yield strength under 3m/s die-casting are increased by 11.20% and 16.45%, respectively, the elongation after fracture is reduced by 0.8%, and the corrosion potential is positively shifted了31mV.
- (3) In order to optimize the mechanical properties and corrosion resistance of Mg-9Al-1Zn-0.5Ce automotive new die-casting parts samples, the die-casting process parameters of Mg-9Al-1Zn-0.5Ce automotive new die-casting parts samples are optimized as follows: 650℃ initial forging temperature, 3m/s injection speed.
Please keep the source and address of this article for reprinting:The Process Analysis of New Type Die Casting Automotive Parts
Minghe Die Casting Company are dedicated to manufacture and provide quality and high performance Casting Parts(metal die casting parts range mainly include Thin-Wall Die Casting,Hot Chamber Die Casting,Cold Chamber Die Casting),Round Service(Die Casting Service,Cnc Machining,Mold Making,Surface Treatment).Any custom Aluminum die casting, magnesium or Zamak/zinc die casting and other castings requirements are welcome to contact us.
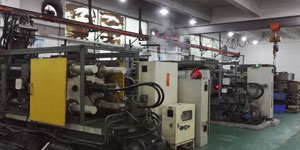
Under the control of ISO9001 and TS 16949,All processes are carried out through hundreds of advanced die casting machines, 5-axis machines, and other facilities, ranging from blasters to Ultra Sonic washing machines.Minghe not only has advanced equipment but also have professional team of experienced engineers,operators and inspectors to make the customer’s design come true.
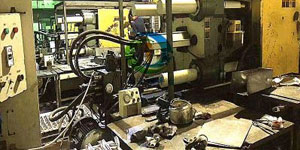
Contract manufacturer of die castings. Capabilities include cold chamber aluminum die casting parts from 0.15 lbs. to 6 lbs., quick change set up, and machining. Value-added services include polishing, vibrating, deburring, shot blasting, painting, plating, coating, assembly, and tooling. Materials worked with include alloys such as 360, 380, 383, and 413.
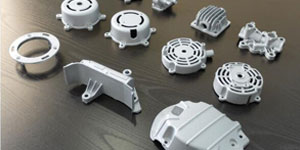
Zinc die casting design assistance/concurrent engineering services. Custom manufacturer of precision zinc die castings. Miniature castings, high pressure die castings, multi-slide mold castings, conventional mold castings, unit die and independent die castings and cavity sealed castings can be manufactured. Castings can be manufactured in lengths and widths up to 24 in. in +/-0.0005 in. tolerance.
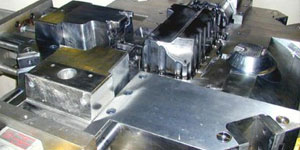
ISO 9001: 2015 certified manufacturer of die cast magnesium, Capabilities include high-pressure magnesium die casting up to 200 ton hot chamber & 3000 ton cold chamber, tooling design, polishing, molding, machining, powder & liquid painting, full QA with CMM capabilities, assembly, packaging & delivery.
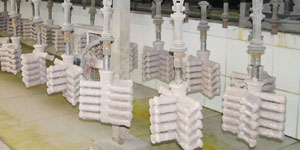
ITAF16949 certified. Additional Casting Service Include investment casting,sand casting,Gravity Casting, Lost Foam Casting,Centrifugal Casting,Vacuum Casting,Permanent Mold Casting,.Capabilities include EDI, engineering assistance, solid modeling and secondary processing.
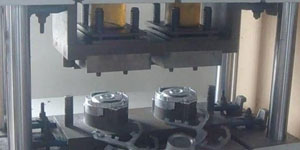
Casting Industries Parts Case Studies for: Cars, Bikes, Aircraft, Musical instruments, Watercraft, Optical devices, Sensors, Models, Electronic devices, Enclosures, Clocks, Machinery, Engines, Furniture, Jewelry, Jigs, Telecom, Lighting, Medical devices, Photographic devices, Robots, Sculptures, Sound equipment, Sporting equipment, Tooling, Toys and more.
What Can we help you do next?
∇ Go To Homepage For Die Casting China
→Casting Parts-Find out what we have done.
→Ralated Tips About Die Casting Services
By Minghe Die Casting Manufacturer |Categories: Helpful Articles |Material Tags: Aluminum Casting, Zinc Casting, Magnesium Casting, Titanium Casting, Stainless Steel Casting, Brass Casting,Bronze Casting,Casting Video,Company History,Aluminum Die Casting |Comments Off