The Process Characteristics Of Low Pressure Casting
In the casting technology of aluminum alloy castings, the most common is low pressure casting. Low pressure casting provides good quality assurance for automobile wheels and other parts, and its irreplaceable superiority has been recognized by the majority of automobile manufacturers. This article mainly introduces the history, principle, process characteristics and required conditions of low pressure casting, aiming to provide corresponding reference for the industry insiders.
The low-pressure casting method has been used for several decades, and it occupies an important position especially in aluminum alloy castings. The low pressure casting method is a mainstream method with powerful functions, which can increase the strength of the material and improve the performance of the material. Low-pressure casting is a very practical casting method. The castings it casts are of good quality, and the method has a relatively high degree of automation.
1. The History Of Low Pressure Casting
The low-pressure casting method has a history of more than one hundred years. In the 1920s, the two countries that applied the low-pressure casting method to aluminum alloy casting were France and Germany, but they were still in the trial application stage. By 1945, low-pressure manufacturing began to be used on a large scale, mainly in the production of rainwater pipes and beer containers in the UK. In 1958, the Americans applied the low-pressure casting method to the casting of automobile engine parts. This was the opportunity for the low-pressure casting to be widely used. The world automobile industry began to notice this magical casting method, and the method was introduced to China in the late 1950s.
In my country, the use of low-pressure casting began in 1961. When the manufacturing of air-cooled cylinder heads can be magically realized by the low-pressure casting method, this method began to be highly valued. Since then, low-pressure casting technology has been continuously applied in the automotive industry, and its material utilization rate is very high, especially in aluminum alloy castings, which is as high as one-half of the low-pressure casting technology. The quality of aluminum alloy castings produced by this technology is excellent, and the types of products produced are constantly expanding. In the 1970s, low-pressure casting technology began to be used in the production of automobile wheels. In modern times, people began to pay attention to the lightweight development of automobiles. Low-pressure casting technology began to manufacture parts with better performance, higher internal quality, and stricter mechanical properties.
2. Basic Principles
The basic principle of low pressure casting is mainly to promote the molten soup into the mold by applying pressure, and the molten soup gradually solidifies by slowly filling, and the solidification of the gate part is the time when the pressure is applied. The castings solidified in this way will be perfect. The direction of solidification starts from the gate direction, does not conflict with pressure, and will not be disturbed by pressure, and the solidification process and cooling are completed naturally and smoothly.
3. The Characteristics Of Low Pressure Casting Process
The pressure and speed of low pressure casting can be flexibly adjusted during pouring, so that casting can be carried out according to different casting shapes. Low-pressure casting mainly adopts bottom injection type filling, which can ensure the stable filling of molten metal, can also effectively avoid the interference of space to molten metal, and avoid the formation of quality defects after the casting is formed. Under the action of pressure, the molded castings have high quality, smooth surface and high performance. At the same time, low-pressure casting greatly reduces the labor intensity, the environment is better, and the equipment is convenient and practical. Compared with other casting methods, low-pressure casting has certain peculiarities and also possesses very distinct process characteristics.
3.1 Features compared with ordinary casting Low-pressure casting can use metal molds, sand molds, stone grinding molds, etc., and its application range is very wide, so the low-pressure casting method has many advantages that ordinary casting methods have. Low-pressure casting is suitable for non-ferrous metals and ferrous metals, which is not achieved by many common casting methods. The filling of low pressure casting is very stable, because it mainly adopts the bottom construction type, so the pressure and speed can be adjusted flexibly. Under the action of pressure, the solidification of the molten metal is very sufficient, the utilization rate is high, and the fluidity is better, and the quality of the casting is improved. The more complex the casting, the more it can show its advantages.
3.2 Features compared with die casting
Low-pressure casting can be used to manufacture many types of castings, and heat treatment can be carried out flexibly according to the actual situation. It can be used to manufacture thin-walled castings as well as thick-walled castings, and it can fully avoid the interference of air during the casting process. , Get high-quality castings, smooth surface, fine structure, and less bubbles. Moreover, the mechanical properties of the castings are very outstanding, with more types, finer, and lower cost.
3.3 Disadvantages Affected by the location and quantity of gates, as well as the thickness of the inner wall, the product will be subject to certain restrictions. In order to fully reflect the good fluidity of the molten metal and ensure that solidification begins at the gate, the casting cycle will be increased and the solidification rate will also slow down. When molten metal fills the cavity, the mechanical properties of the molten metal surface will be limited.
4. Conditions Required For Low Pressure Casting
4.1 Temperature
The temperature of the molten soup will be affected by the type and shape, but the overall difference will not be too great. Whether its temperature is suitable or not will directly affect the quality and aesthetics of the product, so the temperature should be controlled within a reasonable range. It should be noted that the mold temperature cannot be ignored either.
From the perspective of molten metal solidification, the distribution of mold temperature is mainly from the gate to the upward direction gradually lower, but because this will prolong the casting cycle and affect the rate of solidification, so the upper and horizontal cooling must be carried out. The production cycle, molten metal temperature and other aspects need to be carefully considered and adjusted, which will profoundly affect the internal and external quality of the casting, so the temperature difference of the gate can be increased according to the actual situation, so that the status quo can be changed.
4.2 Pressurization Time
Pressurization time mainly refers to the time taken by the molten metal from filling to solidification at the gate. The pressurization time may be affected by various factors, which requires consideration of the cylinder head time. The extension should be as long as possible, and the basis for extension is mainly based on the weight. The pressurization time is easily affected by temperature conditions. If the temperature is stable, the pressurization time will also be very stable.
The solidification time of molten metal may be unstable due to changes in heat and decrease in temperature. Because the number of castings will continue to increase, the temperature will be very unstable, and at the same time, the cross-sectional area of the gate will decrease, which will cause the solidification time to change, resulting in internal defects in the quality of the castings. Therefore, we must pay great attention to the influence of factors such as temperature, gate and feed pipe to the soup system.
4.3 Setting Time
The solidification time refers to the time from the completion of pressurization to the demolding of the product. After the casting is demolded, it is not really completed, but to ensure that the casting is not deformed and the quality of the casting is guaranteed. The time required for this part must be added to the time required for solidification. The solidification time will not take long, it is related to the temperature, and the solidification speed will be faster than the pressurization time. In order to shorten the solidification time, the cooling rate can be increased.
4.4 Pressurized Conditions
In order to ensure the filling effect, pay attention to adjusting the pressurizing speed, too fast or too slow will affect the filling effect and the quality of the casting. Specifically, if the speed is slow, it will cause the problem of poor liquidity of the molten soup; if the speed is too fast, the product will be disturbed by gas and cause quality defects. Therefore, it is imperative to adjust the speed of pressurization. Since the flow rate will be affected by the difference in the shape of the flow path, it is necessary to control the speed according to the actual situation.
5. Conclusion
In summary, low pressure casting technology has great advantages and is the mainstream casting technology for aluminum alloy castings. Compared with other casting methods, this technology has a wide range of applications, with high casting quality, high precision, good performance and high degree of automation. Low pressure casting technology has a history of one hundred years since its inception, and it is influencing the alloy casting industry with a better development trend.
Please keep the source and address of this article for reprinting:The Process Characteristics Of Low Pressure Casting
Minghe Die Casting Company are dedicated to manufacture and provide quality and high performance Casting Parts(metal die casting parts range mainly include Thin-Wall Die Casting,Hot Chamber Die Casting,Cold Chamber Die Casting),Round Service(Die Casting Service,Cnc Machining,Mold Making,Surface Treatment).Any custom Aluminum die casting, magnesium or Zamak/zinc die casting and other castings requirements are welcome to contact us.
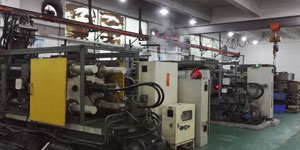
Under the control of ISO9001 and TS 16949,All processes are carried out through hundreds of advanced die casting machines, 5-axis machines, and other facilities, ranging from blasters to Ultra Sonic washing machines.Minghe not only has advanced equipment but also have professional team of experienced engineers,operators and inspectors to make the customer’s design come true.
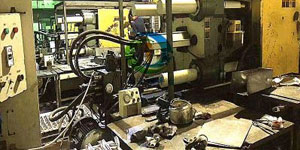
Contract manufacturer of die castings. Capabilities include cold chamber aluminum die casting parts from 0.15 lbs. to 6 lbs., quick change set up, and machining. Value-added services include polishing, vibrating, deburring, shot blasting, painting, plating, coating, assembly, and tooling. Materials worked with include alloys such as 360, 380, 383, and 413.
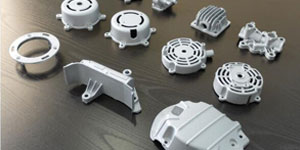
Zinc die casting design assistance/concurrent engineering services. Custom manufacturer of precision zinc die castings. Miniature castings, high pressure die castings, multi-slide mold castings, conventional mold castings, unit die and independent die castings and cavity sealed castings can be manufactured. Castings can be manufactured in lengths and widths up to 24 in. in +/-0.0005 in. tolerance.
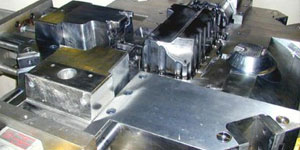
ISO 9001: 2015 certified manufacturer of die cast magnesium, Capabilities include high-pressure magnesium die casting up to 200 ton hot chamber & 3000 ton cold chamber, tooling design, polishing, molding, machining, powder & liquid painting, full QA with CMM capabilities, assembly, packaging & delivery.
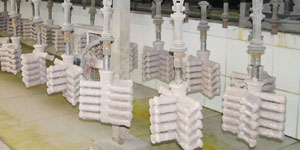
ITAF16949 certified. Additional Casting Service Include investment casting,sand casting,Gravity Casting, Lost Foam Casting,Centrifugal Casting,Vacuum Casting,Permanent Mold Casting,.Capabilities include EDI, engineering assistance, solid modeling and secondary processing.
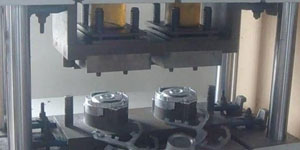
Casting Industries Parts Case Studies for: Cars, Bikes, Aircraft, Musical instruments, Watercraft, Optical devices, Sensors, Models, Electronic devices, Enclosures, Clocks, Machinery, Engines, Furniture, Jewelry, Jigs, Telecom, Lighting, Medical devices, Photographic devices, Robots, Sculptures, Sound equipment, Sporting equipment, Tooling, Toys and more.
What Can we help you do next?
∇ Go To Homepage For Die Casting China
→Casting Parts-Find out what we have done.
→Ralated Tips About Die Casting Services
By Minghe Die Casting Manufacturer |Categories: Helpful Articles |Material Tags: Aluminum Casting, Zinc Casting, Magnesium Casting, Titanium Casting, Stainless Steel Casting, Brass Casting,Bronze Casting,Casting Video,Company History,Aluminum Die Casting |Comments Off