The Process Purpose Of Stainless Steel Bright Annealing
Eliminate work hardening to obtain satisfactory metallographic structure
Bright annealing furnace is mainly used for heat treatment of finished stainless steel under protective atmosphere. When the performance requirements are different, the requirements for the metallographic structure after the bright annealing are different, and the process of the bright heat treatment is also different.
The typical heat treatment process of 300 series austenitic stainless steel is solution treatment. During the heating process, the carbide is dissolved into the austenite, heated to 1050~1150℃, kept properly for a short period of time, so that all the carbides are dissolved in the austenite, and then quickly cooled to below 350℃ to obtain a supersaturated solid solution that is uniform The unidirectional austenite structure. The key to this heat treatment process is rapid cooling, which requires a cooling rate of 55°C/s, and quickly passes through the re-precipitation temperature zone (550-850°C) after carbide solid solution. The holding time should be as short as possible, otherwise the crystal grains will be coarse, which will affect the surface finish.
400 series ferritic stainless steel has a relatively low heating temperature (about 900°C), and slow cooling is often used to obtain annealed softened structure. Martensitic stainless steel is annealed, and it can also be treated by quenching and tempering in sections.
From the above, it can be seen that the heat treatment system of 300 series and 400 series stainless steel is very different. To obtain qualified metallographic structure, the cooling section of the bright annealing furnace is required to have a lot of room for adjustment. Therefore, the modern advanced bright annealing furnace often adopts strong convection cooling in its cooling section, with three cooling sections, which can individually adjust the air volume. It is divided into three sections along the width direction of the strip, and the cooling speed in the width direction of the strip is adjusted by the air volume diversion to control the plate shape.
Another key issue in the heat treatment of cold-rolled stainless steel strip is that the entire strip is required to have a uniform structure in width and length. The muffle-type bright annealing furnace adopts a large-size muffle tube, which evenly organizes the heating airflow from the outside of the muffle tube to spiral around, so that the strip is evenly heated. To ensure the uniform structure of the strip along the length direction, the linear velocity of the strip in the heating furnace must be kept constant. Therefore, a roller tension adjustment device that can be precisely adjusted is installed before and after the modern vertical bright heat treatment furnace. Not only must the strip steel import and export speed meet the requirements of the heat treatment speed, and not be affected by the empty or full sleeve quantity, but also the small tension of the strip must be established and precisely adjusted according to the strip shape to meet the requirements of the strip shape. Claim.
2Obtain a bright surface without oxidation
Bright annealing is the heat treatment of strip steel under H2 protective atmosphere. To meet the requirements of the BA board, the protective atmosphere in the furnace must be very strictly controlled to avoid oxidation as much as possible. How does oxidation occur under H2 protective atmosphere?
The main alloy components of stainless steel strip are Fe, Cr, Ni, Mn, Ti, Si, etc. In the annealing temperature range, the oxidation of Fe and Ni is not a major problem. However, the oxidation range of Cr, Mn, Si, and Ti is just within the heating temperature range. It is the oxidation of these alloying elements that affects the surface brightness of the strip steel. In particular, the oxidation of chromium dechromates the surface of the strip steel, which will reduce the corrosion resistance of stainless steel. When the content of Cr is between 17% and 18% and the content of Ti is 0.5%, the dew point of H2 must be lower than -60°C to avoid the oxidation of Cr and Ti in the heating range of 800°C to 1150°C.
In addition, how to maintain the purity of the shielding gas in the furnace is also a key issue. In this regard, the muffle cover has good sealing performance and will not cause pollution of the protective atmosphere such as the material of the electric heating furnace body, providing a purer environmental space. In addition, the strip steel inlet and outlet of the vertical furnace are located at the lowest part of the furnace, and the furnace pressure is stable. Therefore, compared with the horizontal furnace, the risk of air entering is much smaller. However, the inlet and outlet sealing boxes of the bright annealing furnace, the strip conveying section, the tension adjustment roller and the furnace top guide roller box should be ensured to meet the sealing requirements of a few parts per million (ppM level), so that oxygen and water vapor cannot enter, and the protective gas Can't let it out.
Related issues that need to be paid attention to when building a vertical bright annealing furnace
1) Creep and treatment of the muffle cover
The muffle cover will creep and extend in a long-term high temperature state. Structurally, the muffle cover is hung on the top of the furnace and is in a suspended state. The lower part of the cover is sealed with a water ring and is not fixed, allowing a certain amount of creep. The creep has accumulated to a certain amount, remove the water seal, and cut off a section of the lower edge of the muffle cover with a special plasma cutting machine. Cut once every six months. The cutting operation requirements are relatively high. Full attention should be paid to its special equipment, operating space and structure, and operating reliability.
2) Safety maintenance of vertical furnace
The furnace uses hydrogen as the protective gas. The sealing requirement reaches the 10-6th power level. A small amount of air leakage will also destroy the protective atmosphere and cause the strip to oxidize. Once the hydrogen leaks, it will be very dangerous to rise and accumulate in the tower structure. Therefore, foolproof measures must be taken to ensure safety. To this end, the furnace must have the following means:
- Equipped with flame detectors beside the sealing device of the steel belt inlet and outlet;
- Furnace condition monitoring (temperature, pressure) system;
- Nitrogen cleaning device and automatic emergency measures;
- Hydrogen pressure monitoring equipment and automatic emergency measures;
- The equipment's fire extinguishing device and automatic emergency measures;
- fire extinguishing and forced ventilation measures for buildings;
- Fire Alarm Center.
The body of the vertical bright heat treatment furnace is about 45m high. For equipment operation monitoring of vertical furnaces, adequate instrument communication means must be provided. The vertical structure also brings some maintenance difficulties, such as the problem of dust removal. A well-known stainless steel cold rolling mill in the United States was plagued by the above-mentioned problems and had to solve it by increasing the frequency of dust removal.
3) Replacement of the muffle cover
The main body of the is about 45m high, the muffle cover is about 16m long, and the service life is about 4 years. When replacing the muffle cover, it needs to be drawn out from the top of the furnace, and the lifting height is estimated to be about 65m. The corresponding tower crane and operating space are required. In this regard, full consideration must be given to the design and layout of the plant.
4) Factory supporting
The plant supporting the vertical furnace is in the shape of a partial tall tower. In order to ensure uniform strip tension, good plate shape, and smooth operation, the equipment installation accuracy is required to be very high. Therefore, the uneven settlement of the foundation should be strictly controlled. Measures such as large-height hoisting cranes, elevators, fire fighting, and forced ventilation required for daily maintenance of the plant must be in place.
5) Equipment maintenance and accessories
The vertical bright annealing furnace has high technical requirements. Equipment manufacturers have strict requirements for equipment maintenance and spare parts supply. Some of the equipment maintenance and spare parts supply only provide services and supplies, and do not provide drawings, which are expensive.
Please keep the source and address of this article for reprinting: The Process Purpose Of Stainless Steel Bright Annealing
Minghe Die Casting Company are dedicated to manufacture and provide quality and high performance Casting Parts(metal die casting parts range mainly include Thin-Wall Die Casting,Hot Chamber Die Casting,Cold Chamber Die Casting),Round Service(Die Casting Service,Cnc Machining,Mold Making,Surface Treatment).Any custom Aluminum die casting, magnesium or Zamak/zinc die casting and other castings requirements are welcome to contact us.
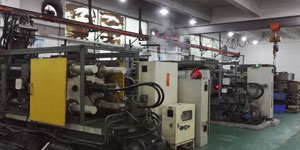
Under the control of ISO9001 and TS 16949,All processes are carried out through hundreds of advanced die casting machines, 5-axis machines, and other facilities, ranging from blasters to Ultra Sonic washing machines.Minghe not only has advanced equipment but also have professional team of experienced engineers,operators and inspectors to make the customer’s design come true.
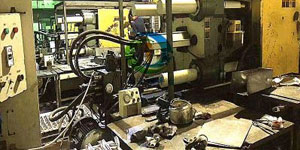
Contract manufacturer of die castings. Capabilities include cold chamber aluminum die casting parts from 0.15 lbs. to 6 lbs., quick change set up, and machining. Value-added services include polishing, vibrating, deburring, shot blasting, painting, plating, coating, assembly, and tooling. Materials worked with include alloys such as 360, 380, 383, and 413.
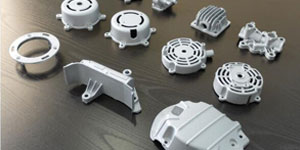
Zinc die casting design assistance/concurrent engineering services. Custom manufacturer of precision zinc die castings. Miniature castings, high pressure die castings, multi-slide mold castings, conventional mold castings, unit die and independent die castings and cavity sealed castings can be manufactured. Castings can be manufactured in lengths and widths up to 24 in. in +/-0.0005 in. tolerance.
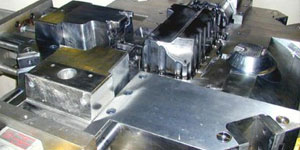
ISO 9001: 2015 certified manufacturer of die cast magnesium, Capabilities include high-pressure magnesium die casting up to 200 ton hot chamber & 3000 ton cold chamber, tooling design, polishing, molding, machining, powder & liquid painting, full QA with CMM capabilities, assembly, packaging & delivery.
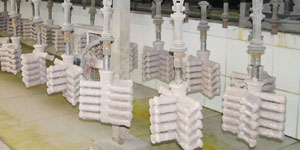
ITAF16949 certified. Additional Casting Service Include investment casting,sand casting,Gravity Casting, Lost Foam Casting,Centrifugal Casting,Vacuum Casting,Permanent Mold Casting,.Capabilities include EDI, engineering assistance, solid modeling and secondary processing.
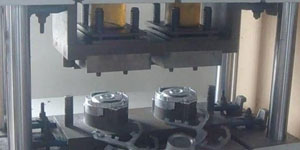
Casting Industries Parts Case Studies for: Cars, Bikes, Aircraft, Musical instruments, Watercraft, Optical devices, Sensors, Models, Electronic devices, Enclosures, Clocks, Machinery, Engines, Furniture, Jewelry, Jigs, Telecom, Lighting, Medical devices, Photographic devices, Robots, Sculptures, Sound equipment, Sporting equipment, Tooling, Toys and more.
What Can we help you do next?
∇ Go To Homepage For Die Casting China
→Casting Parts-Find out what we have done.
→Ralated Tips About Die Casting Services
By Minghe Die Casting Manufacturer |Categories: Helpful Articles |Material Tags: Aluminum Casting, Zinc Casting, Magnesium Casting, Titanium Casting, Stainless Steel Casting, Brass Casting,Bronze Casting,Casting Video,Company History,Aluminum Die Casting |Comments Off