The Processing Flow Of Precision Casting Mold
The precision casting mold is also called lost wax casting, and its old product is complex, precise, and close to the final shape of the part. It can be used directly without processing or with a lot of processing, so investment casting is an advanced technology with near net shape. Minghe Hardware will introduce to you how the processing flow of precision casting molds is formed?
Factors affecting the dimensional accuracy of precision casting molds
Under normal circumstances, the dimensional accuracy of precision casting is affected by many factors such as casting structure, mold making, casting material, roasting, shell making, pouring, etc. Any setting or unreasonable operation of any link will cause the shrinkage of the casting. Changes have led to deviations in the dimensional accuracy of the castings from the requirements. The following are the main factors that may cause defects in the dimensional accuracy of precision castings:
- The influence of casting material: the higher the carbon content in the material, the smaller the linear shrinkage, and the lower the carbon content, the greater the linear shrinkage; the casting shrinkage of common materials is as follows: casting shrinkage k=(LM-LJ) /LJ*100%, LM is the cavity size, LJ is the casting size. K is affected by the following factors: wax mold K1, casting structure K2, alloy type K3, pouring temperature K4;
- The influence of shell-making materials: zircon sand, Shangdian sand, zircon powder, and Shangdian powder are used. Because of their small expansion coefficient, only 4.6*10-6/℃, it can be ignored;
- The influence of casting structure: casting wall thickness, large shrinkage rate, thin casting wall, small shrinkage rate; large free shrinkage rate, small hindering shrinkage rate;
- The effect of mold making on the linear shrinkage rate of castings: the linear shrinkage rate of wax (mold) material is 0.9-1.1%; the radial shrinkage rate of the wax mold is only 30-40% of the longitudinal shrinkage rate, and the wax injection temperature is free The effect of shrinkage is far greater than that of hindered shrinkage (the best sand shooting temperature is 57-59℃, the higher the temperature, the greater the shrinkage); the influence of wax injection temperature, wax injection pressure, and pressure holding time on the investment size The wax injection temperature is the most obvious, followed by the wax injection pressure. The pressure holding time ensures that the final size of the investment mold after the investment is formed is small; when the investment is stored, it will shrink further, and its shrinkage value is about the total 10% of the shrinkage, but after 12 hours of storage, the investment size is basically stable;
- The influence of casting temperature: the higher the casting temperature, the greater the shrinkage rate, and the lower the casting temperature, the smaller the shrinkage rate, so the casting temperature should be appropriate;
- The influence of the mould shell roasting: due to the small expansion coefficient of the mould shell, when the mould shell temperature is 1150℃, it is only 0.053%, so it can be ignored.
Ancient China: Prince Wuding, Bronze Lion, Bronze Forbidden, etc., are all masterpieces of investment casting. Since investment casting was used in industrial production in the 1940s, it has been developing at a relatively rapid rate for half a century. Especially European and American countries are developing rapidly. Investment casting is used in almost all industrial sectors, except for the aviation and weapons sectors. Especially in the sectors of electronics, chemicals, Giti Transportation, petroleum, energy, textiles, medical equipment, light industry, pharmaceuticals, valves, pumps, etc. China has also developed rapidly in recent years.
The development of investment technology has enabled investment casting components to produce small castings and relatively large castings. The outline size of the largest investment casting is nearly 2m, while the minimum wall thickness is less than 2mm. At the same time, investment castings are becoming more and more popular. Precision, in addition to linear tolerances, parts can also reach higher geometric tolerances, and the surface roughness of investment castings is getting smaller and smaller, which can reach RaO.4um.
Please keep the source and address of this article for reprinting: The Processing Flow Of Precision Casting Mold
Minghe Die Casting Company are dedicated to manufacture and provide quality and high performance Casting Parts(metal die casting parts range mainly include Thin-Wall Die Casting,Hot Chamber Die Casting,Cold Chamber Die Casting),Round Service(Die Casting Service,Cnc Machining,Mold Making,Surface Treatment).Any custom Aluminum die casting, magnesium or Zamak/zinc die casting and other castings requirements are welcome to contact us.
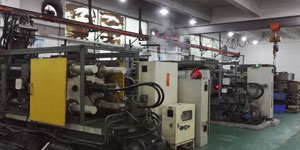
Under the control of ISO9001 and TS 16949,All processes are carried out through hundreds of advanced die casting machines, 5-axis machines, and other facilities, ranging from blasters to Ultra Sonic washing machines.Minghe not only has advanced equipment but also have professional team of experienced engineers,operators and inspectors to make the customer’s design come true.
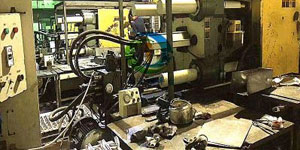
Contract manufacturer of die castings. Capabilities include cold chamber aluminum die casting parts from 0.15 lbs. to 6 lbs., quick change set up, and machining. Value-added services include polishing, vibrating, deburring, shot blasting, painting, plating, coating, assembly, and tooling. Materials worked with include alloys such as 360, 380, 383, and 413.
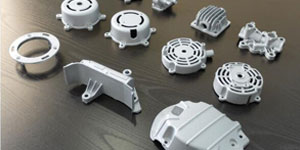
Zinc die casting design assistance/concurrent engineering services. Custom manufacturer of precision zinc die castings. Miniature castings, high pressure die castings, multi-slide mold castings, conventional mold castings, unit die and independent die castings and cavity sealed castings can be manufactured. Castings can be manufactured in lengths and widths up to 24 in. in +/-0.0005 in. tolerance.
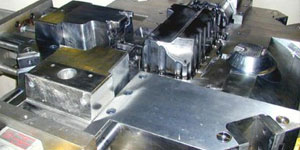
ISO 9001: 2015 certified manufacturer of die cast magnesium, Capabilities include high-pressure magnesium die casting up to 200 ton hot chamber & 3000 ton cold chamber, tooling design, polishing, molding, machining, powder & liquid painting, full QA with CMM capabilities, assembly, packaging & delivery.
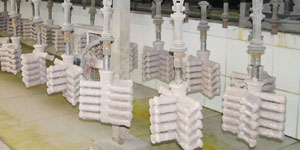
ITAF16949 certified. Additional Casting Service Include investment casting,sand casting,Gravity Casting, Lost Foam Casting,Centrifugal Casting,Vacuum Casting,Permanent Mold Casting,.Capabilities include EDI, engineering assistance, solid modeling and secondary processing.
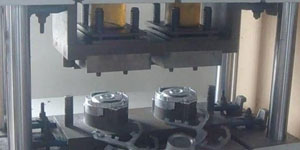
Casting Industries Parts Case Studies for: Cars, Bikes, Aircraft, Musical instruments, Watercraft, Optical devices, Sensors, Models, Electronic devices, Enclosures, Clocks, Machinery, Engines, Furniture, Jewelry, Jigs, Telecom, Lighting, Medical devices, Photographic devices, Robots, Sculptures, Sound equipment, Sporting equipment, Tooling, Toys and more.
What Can we help you do next?
∇ Go To Homepage For Die Casting China
→Casting Parts-Find out what we have done.
→Ralated Tips About Die Casting Services
By Minghe Die Casting Manufacturer |Categories: Helpful Articles |Material Tags: Aluminum Casting, Zinc Casting, Magnesium Casting, Titanium Casting, Stainless Steel Casting, Brass Casting,Bronze Casting,Casting Video,Company History,Aluminum Die Casting |Comments Off