The Production Practice To Reduce Power Consumption
Power consumption is the second largest energy consumption after solid fuel consumption in the sintering process, accounting for about 13% to 20%. Therefore, reducing power consumption is also an important measure to reduce energy consumption in the sintering process.
1. Reduce the air leakage rate of the equipment and reduce the power consumption
The power consumption of the main exhaust fan accounts for most of the total power consumption of the sintering plant. Reducing the air leakage rate of the ventilation system and increasing the effective air volume through the material layer is of great significance to saving power consumption.
The air leakage between the sintering trolley and the wind box (sealing plate), the trolley and the slide, and the trolley and the trolley account for more than 80% of the total air leakage of the sintering machine. Therefore, the sealing form between the trolley and the slide is improved, In particular, the sealed structure at the end of the head and tail air boxes can significantly reduce harmful air leakage, increase the effective air flow through the material layer, increase the output of sinter, and save electricity. In addition, timely replacement and maintenance of the trolley, improvement of the cloth method, and reduction of edge air leakage between the trolley baffle and the mixture can effectively reduce harmful air leakage. By strengthening the lubrication, maintenance and management of the equipment, the air leakage rate of the sintering machine is significantly reduced, the effective air flow through the material layer is greatly increased, the quality of the sintered ore is improved, and the power consumption is reduced.
At present, most of the sealing of the trolley and the slideway adopts a spring-loaded floating plate sealing device installed in the sealing groove of the trolley. But the structure is flawed. The elastic slideway sealing device is mainly to install a spiral spring and a floating plate in the sealing groove. Problems with this kind of sealing device:
One is that the size of the floating board is not easy to determine, either large or small, and not just right; the second is the aging of the coil spring and loses its elasticity; the third is the accumulation of dust in the space in the groove where the spring is placed. Under the scouring of the high-speed airflow that entrained dust particles, the two ends of the leaf spring were quickly worn out and could not be used for three to five months. In addition to the shortcomings mentioned above, the above-mentioned three kinds of sealing devices between the trolley and the slideway have a common defect, that is, the gap between the two ends of the floating plate and the side wall of the sealing groove is easy to fall into the slag and the floating plate It is stuck so that it cannot float up and down, which will cause air leakage in the gap between the floating board and the fixed slideway.
Therefore, in order to reduce the sintering air leakage rate, the existing sealing devices that have been adopted must be improved, and the trolley must be regularly inspected and the elastic floating floating plate must be replaced. In order to effectively improve the sealing effect, in a word, all air leakage gaps can be completely sealed to reduce the sintering air leakage rate. Otherwise, reducing the sintering air leakage rate is just empty talk.
2. Improve the air permeability of the mixture
The pipe network resistance of the sintering fan is composed of two parts: the pressure loss of the sintered material layer and the assembly loss of the pipeline. Improving the air permeability of the sintered material layer is the key to reducing the resistance of the fan pipe network and reducing power consumption. The air permeability of the material layer can be expressed by the following formula:
- K = Q/A×(h/P)n
- K—breathability
- Q—air volume passing through the material layer m3/min
- A—material layer area m2
- h—Thickness of material layer mm
- P—resistance loss of material layer Pa
- n—index 0.6
Studies have shown that the particle size of the sintered mixture has a positive relationship with the air permeability, that is, the air permeability of the material layer increases with the increase of the particle size. Therefore, in the production, by adding an appropriate amount of quicklime, the ratio of returning ore is stabilized, the temperature of the hot water in the first mix is increased, and the second mix is preheated by steam.
(1) Add appropriate amount of quicklime
According to the CaO+H2O=Ca(OH)2+64883KJ/Kg reaction formula, it can be roughly calculated that the temperature of the 100Kg sintered material can be increased by 39°C. Actually, the temperature of the material is increased between 8°C and 10°C due to the heat loss during transportation. Theoretically, the ratio of quicklime at 4% can meet the requirement of dew point temperature. Considering the heat loss, the ratio of quicklime in production is 5%.
(2) Increase the temperature of the first mixed hot water
The sprayed water temperature of a mixer is above 60℃, which can increase the temperature of the mixture and promote the digestion of quicklime.
(3) The second mix uses steam to preheat
Passing steam into the secondary mixer is also a measure to increase the material temperature. Practice has proved that the use of steam can increase the material temperature up to 65℃, but when the production encounters a long period of shutdown, it must be confirmed that the steam valve is closed to prevent steam from entering Roller, thereby causing unnecessary production accidents.
The temperature of the mixture is as shown in Table 1:
Table 1 Monthly mixture temperature
Month | 4 | 5 | 6 | 7 | 8 | 9 |
Material Temperature ℃ | 55 | 60 | 60 | 62 | 63 | 55 |
(4) Stable return rate
- ① The amount of returned ore affects the sintering yield. Affect sintering production, cause uneven ore formation, and decrease the strength of ore formation.
- ②Return ore residual C and alkaline substances affect sintering C balance and ore R control.
- ③The mixture can be preheated for returning ore.
- ④Returning ore is conducive to the granulation of the mixture and improves the sintering efficiency. Too small will deteriorate the permeability of the material layer, and too large will easily cause the mixture to melt, make the structure of the sintered ore uniform, and the strength will be worse.
The suitable return particle size is 0.5-5mm; the instability of the residual carbon will cause the fixed carbon in the sinter to fluctuate , Affect the normal progress of the sintering process; high return temperature is conducive to the preheating of the mixture, but it is not conducive to the ball formation of the mixture. Therefore, the ratio of return ore is required to be between 32% and 40% in production. As shown in Table 2:
Table 2 Proportion of monthly return
Month | 4 | 5 | 6 | 7 | 8 | 9 |
Ratio | 35 | 33 | 32 | 35 | 36 | 37 |
3. Reduce sintering resistance
The temperature in the high-temperature zone of sintering is high, and the liquid phase produced will increase the resistance of the airflow. The temperature level in the high-temperature zone is determined by the temperature and thickness of the combustion zone, which depends not only on the heat balance of the combustion zone, but also on the combustion speed and heat transfer rate of the solid carbon. Therefore, the fuel physicochemical properties directly affect the resistance of the sintering combustion zone. It has the following relationship:
Fuel quantity: increase the fuel quantity, which not only increases the temperature of the combustion zone, but also increases its thickness;
Fuel particle size: Increase the fuel particle size. As the burning speed decreases and the burning time is prolonged, the temperature of the combustion zone decreases and the thickness increases. Airflow speed: Airflow speed has an effect on heat transfer speed and combustion speed, but the degree of influence is different. When the airflow speed increases, the heat transfer speed and the combustion speed develop at different speeds, and the gap between the two gradually increases, causing the heat transfer and combustion to become disconnected, reducing the temperature of the combustion layer and increasing the thickness. In actual production, the airflow must be controlled so that the combustion speed and heat transfer speed are similar to achieve the highest combustion temperature and the narrowest combustion zone width. For coke powder, 1mm~3mm is considered to be the best particle size, and the coke powder particle size of the second operation area of Beiying Sintering Zone of Benxi Iron and Steel is basically controlled at 78% if it is less than 3mm. As shown in Table 3:
Table 2 Proportion of monthly return
Month | 4 | 5 | 6 | 7 | 8 | 9 |
Granularity% | 78 | 79 | 78 | 80 | 79 | 80 |
4. Use variable frequency speed regulation and capacitor compensation to reduce power consumption
Frequency conversion speed regulation technology is a safe, reliable and reasonable speed regulation method developed in recent years. It achieves the purpose of adjusting the speed of the motor by converting the alternating current with a certain voltage and frequency used in daily production into an alternating current with a variable frequency and voltage through a converter. After the variable speed motor adopts frequency conversion speed regulation, the average current is reduced and the electric energy is saved. In actual production, in order to pursue the equipment operation rate, coupled with equipment quality, operation and other reasons, the power of the motor is often artificially increased, resulting in the phenomenon of "big horse-drawn cart", which increases the reactive power of the motor and wastes electrical energy. . In the second sintering area of Benxi Iron and Steel's Beiying sintering area, after a year of production practice, it has continuously improved its own operating level and accumulated experience. It has made continuous efforts to save energy and reduce consumption in sintering. During normal production, the average power of the two main exhaust fans has changed from the original The sintering quality and quantity can be reduced to about 5500Kw/h from about 6000Kw/h to about 5500Kw/h. At the same time, the sintering quality and quantity fully meet the production requirements of the blast furnace.
Concluding remarks: Sintering energy saving is a long-term, persistent, difficult task that needs to be completed by sintering workers. It must be constantly explored, summarized, improved, and perfected in production. Only under the premise of quality control and cost reduction can we stand a firm foothold in the current weak steel market, so energy conservation and emission reduction are the life-long task of sinter workers.
Please keep the source and address of this article for reprinting: The Production Practice To Reduce Power Consumption
Minghe Die Casting Company are dedicated to manufacture and provide quality and high performance Casting Parts(metal die casting parts range mainly include Thin-Wall Die Casting,Hot Chamber Die Casting,Cold Chamber Die Casting),Round Service(Die Casting Service,Cnc Machining,Mold Making,Surface Treatment).Any custom Aluminum die casting, magnesium or Zamak/zinc die casting and other castings requirements are welcome to contact us.
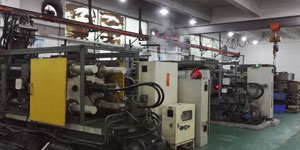
Under the control of ISO9001 and TS 16949,All processes are carried out through hundreds of advanced die casting machines, 5-axis machines, and other facilities, ranging from blasters to Ultra Sonic washing machines.Minghe not only has advanced equipment but also have professional team of experienced engineers,operators and inspectors to make the customer’s design come true.
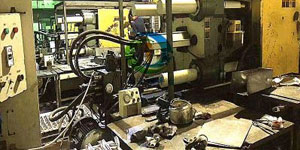
Contract manufacturer of die castings. Capabilities include cold chamber aluminum die casting parts from 0.15 lbs. to 6 lbs., quick change set up, and machining. Value-added services include polishing, vibrating, deburring, shot blasting, painting, plating, coating, assembly, and tooling. Materials worked with include alloys such as 360, 380, 383, and 413.
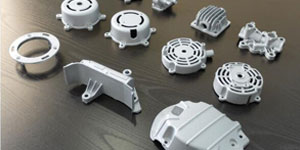
Zinc die casting design assistance/concurrent engineering services. Custom manufacturer of precision zinc die castings. Miniature castings, high pressure die castings, multi-slide mold castings, conventional mold castings, unit die and independent die castings and cavity sealed castings can be manufactured. Castings can be manufactured in lengths and widths up to 24 in. in +/-0.0005 in. tolerance.
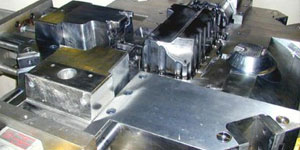
ISO 9001: 2015 certified manufacturer of die cast magnesium, Capabilities include high-pressure magnesium die casting up to 200 ton hot chamber & 3000 ton cold chamber, tooling design, polishing, molding, machining, powder & liquid painting, full QA with CMM capabilities, assembly, packaging & delivery.
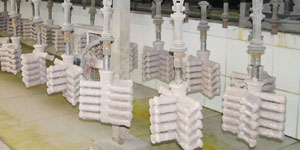
ITAF16949 certified. Additional Casting Service Include investment casting,sand casting,Gravity Casting, Lost Foam Casting,Centrifugal Casting,Vacuum Casting,Permanent Mold Casting,.Capabilities include EDI, engineering assistance, solid modeling and secondary processing.
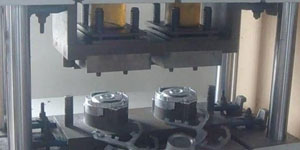
Casting Industries Parts Case Studies for: Cars, Bikes, Aircraft, Musical instruments, Watercraft, Optical devices, Sensors, Models, Electronic devices, Enclosures, Clocks, Machinery, Engines, Furniture, Jewelry, Jigs, Telecom, Lighting, Medical devices, Photographic devices, Robots, Sculptures, Sound equipment, Sporting equipment, Tooling, Toys and more.
What Can we help you do next?
∇ Go To Homepage For Die Casting China
→Casting Parts-Find out what we have done.
→Ralated Tips About Die Casting Services
By Minghe Die Casting Manufacturer |Categories: Helpful Articles |Material Tags: Aluminum Casting, Zinc Casting, Magnesium Casting, Titanium Casting, Stainless Steel Casting, Brass Casting,Bronze Casting,Casting Video,Company History,Aluminum Die Casting |Comments Off