The Production Process Of Brake Drum For Truck
The brake drum is a security part, it relates to the safety of human life and property, and at the same time it is a vulnerable and consumable part. The market demand is particularly large.
At present, the domestic annual output is about 10 million or more. Because the product structure is relatively simple, machine modeling and manual modeling are easy to use, and there are foundries producing brake drums in almost all parts of the country. Several large companies I have visited produce brake drums on a mechanized assembly line, with an annual output of about one million.
I have also been to some small companies with an annual output of tens of thousands. There is also an industrial park in a town in Longyao County, Hebei, where more than a hundred foundries are intensively producing brake drums for automobiles; the output of brake drums in the entire district should be more than one million. It's just that the brake drums produced by large companies are generally supplied to domestic axle factories or exported abroad, while most of the brake drums produced by small companies are supplied to the parts and after-sales parts market. Its product quality and credibility are difficult to be accepted by regular axle factories. According to these companies I have seen and learned, due to different product structures and different supply targets, the production processes are different, but in general, the quality problem There are still many that fail to meet the quality requirements of automotive brake drums. Therefore, I think it is necessary to discuss and research the production process of brake drums with you, and exchange experience with each other. The following is based on my experience and understanding. Situation, take this opportunity to exchange views with you, please correct me if it is wrong.
Quality requirements for truck brake drums
Because gray cast iron has good thermal conductivity, shock absorption, wear resistance, excellent casting performance and low manufacturing cost, almost all brake drums of motor vehicles are made of gray cast iron, and the grades are HT200 and HT250.
There is only one gray cast iron standard in my country that is JB/T9439-2010, and there is no special gray cast iron standard for automobile brake drums. There is no description of special gray cast iron in the machine standard. In the world, only the American Society for Testing and Materials ASTMA159-83 (re-examined in 1993) has specially formulated standards for gray iron parts for automobiles. There are 3 cast iron grades listed for the brake drum according to its load capacity. At the same time, the quality requirements for brake drums in the gray cast iron standard for power machinery of the American Society of Automotive Engineers SAEJ431 are basically the same as ASTMA159-83. At present, most of our country and foreign countries refer to American brake drum standards. The factory standard is given on the drawing or acceptance standard. The level of a standard reflects its level of craftsmanship and quality. Only high-level standards can produce high-quality products.
The following briefly introduces the above-mentioned American standards and the quality requirements of some good foreign companies on brake drums, and introduces the following for your reference
Mechanical properties
Grade | Tensile strength (MPa) | Hardness (HB) |
G2500a |
175 |
170-229 |
G3500b |
245 |
207-255 |
G3500c |
245 |
207-255 |
Chemical Composition
Grade | Total C |
Si |
Mn |
P |
s |
Other alloying elements |
G2500a |
≥3.40 |
1.60-2.10 |
0.60-0.90 |
≤0.15 |
≤0.12 |
As required |
G3500b |
≥3.40 |
1.30-1.80 |
0.60-0.90 |
≤0.15 |
≤0.12 |
|
G3500c |
≥3.50 |
1.30-1.80 |
0.60-0.90 |
≤0.15 |
≤0.12 |
Note:
- The total C is a mandatory requirement and must be guaranteed
- Other elements such as Cr, Cu, Sn are mainly used to ensure mechanical properties and hardness.
- G2500a is used in medium-duty trucks, G3500b is used in heavy-duty trucks, and G3500c is used in super-heavy trucks.
Microstructure
Grade | Graphite type | Shi Chang | Hypokeimenon |
G2500a |
A |
2-4 |
Lamellar pearlite, ferrite <15% |
G3500b |
A |
3-5 |
Layered pearlite, ferrite + cementite <5% |
G3500c |
A |
3-5 |
Layered pearlite, ferrite + cementite <5% |
Other Requirements
In addition to the acceptance of mechanical properties, hardness and metallography, foreign manufacturers and domestic OEMs often put forward requirements for compactness in the technical conditions of brake drums provided.
If there are shrinkage holes, shrinkage porosity, pores, sand inclusions or other casting defects in the castings, they are not dense. These defects can be checked by X-ray or anatomical methods. If the defects are lower than those specified in the following table, it can be accepted. Exceeding its regulations shall be judged as scrap. Of course, if the defect has been exposed during machining, it is generally not accepted.
- ASTME446-98 The internal quality of the brake drum is X-tested defect level
- Advanced dense area, receiving grade is A3, B3, C2
- Generally dense area, the receiving level is A3, B4, C3
- Note: A means stomata, A3 means stomata's acceptance level is 3
- B represents sand and inclusions B4 represents the acceptance level of sand inclusions is level 4
- C means shrinkage porosity C3 means shrinkage porosity acceptance level is 3
Failure modes and causes of brake drums
The failure of the brake drum during use is mainly cracking and abrasion, but from the data statistics reflected in customer complaints and claims, it is mainly the former. That is to say, most of the failed brake drums are under normal or even slight wear, that is, they have cracked and cannot be used. The following are the scraps returned by a factory in 2014. It can be clearly seen from the picture that one to several longitudinal cracks are generated in the brake drum. The transverse cracks mostly appear at the rounded corners of the flange, commonly known as top drop.
From the failure analysis of the failed parts, it is concluded that there are three main reasons for the failure:
- The mechanical properties of the casting body are lower than normal requirements
- There are casting defects inside the casting, especially shrinkage porosity at the rounded corners of the flange.
- The car is seriously overloaded, brakes frequently and is sprayed with water during the braking process, and the mechanical properties and metallography of such failed parts are checked to meet the product requirements.
The first two failure causes should be improved by those of us who produce brake drums. Stabilize and improve the quality of the brake drum. I will discuss with you in more detail below. As for the third reason for the failure, we are powerless, mainly relying on the state's governance of the illegal use of overloaded vehicles. From the point of view of claims, a large part of it is caused by such illegal use. However, the responsibility is generally transferred to the foundry. From what I know, several companies that produce brake drums have claimed a claim ratio of about 3%. There are millions of compensations every year. In fact, this kind of responsibility should be borne by the car owner. Brake drums exported from our country to foreign countries generally reflect well. There is almost never compensation or even complaints. The brake drums of passenger cars and cars transported in plain areas also reflect well. Only a few mountainous areas, mining areas, and individual products have a low service life, all of which are caused by serious domestic overload, frequent emergency braking, and water spraying to cool the brake drum during the braking process. In this case, all the kinetic energy is converted into the thermal load of the brake drum, which can be measured up to 800℃-850℃. This can also be found from the macroscopic and metallographic examination of the failure crack. This type of casting is macroscopically white and bright. Metallographically, it is graphite + martensite + bainite. These are all produced by austenite quenching after high temperature transformation. Therefore, the brake drum fails under the action of bending stress, thermal stress, and resistance to mechanical braking force instead of conventional cracking. This may be a Chinese-style failure mode.
1. Production process of brake drum
The production process of brake drums mainly focuses on two aspects. One is how to ensure its mechanical properties and metallographic structure to meet product requirements. But how to reduce its casting defects. Especially the internal defects of key parts. In terms of reducing casting defects, today I will focus on how to reduce its shrinkage defects, because it is the main type of waste and one of the main reasons for failure.
The first aspect is mainly to provide better metallurgical quality of molten iron. The second aspect is to find out the technological means suitable for the manufacturer.
At present, the materials of domestic truck brake drums are all HT250, so I will focus on several issues that need to be paid attention to in the smelting and process of HT250 used in the production of brake drums.
Originally, if we only needed to meet the mechanical properties of HT250 and the metallographic structure requirements, there would be no difficulty. However, HT250 used in brake drums must ensure mechanical properties, hardness and metallographic structure under high carbon content, which poses some difficulties for some small and even some large manufacturers. They proposed that if the carbon content of the product is to be greater than 3.40%, without adding Cr, Cu, Sn and other alloying elements, it is difficult to guarantee the performance. But their reality is to save costs, and generally only add Cr and Sn to ensure pearlite and tensile strength. However, if the added amount is small, the strength and hardness will not be reached, and if the added amount is large, there will be an excessive amount of cementite in the metallography.
And in a dilemma. Finally, to measure the pros and cons, most of them adopt the method of reducing the carbon content to meet the requirements of mechanical properties and hardness. Of course, so far, although the ASTM standard has made strict regulations on the C content, Chinese factories have not implemented it. Even some foreign customers have not uniformly required that the carbon content must be greater than 3.4% or higher. For example, several customers I know, their requirements for the chemical composition of brake drums are as follows:
Client's Name |
C |
Si |
Mn |
P |
s |
Cr |
Cu |
Sn |
TurkeyADR ltd |
3.2-3.4 |
2.0-2.4 |
0.7-1.0 |
≤0.2 |
≤0.1 |
0.15-0.4 |
0.15-0.5 |
≤0.12 |
Hyundai 250D |
3.1-3.8 |
1.5-2.5 |
0.4-0.9 |
≤0.2 |
≤0.1 |
0.15-0.4 |
0.15-0.5 |
≤0.12 |
However, increasing the total carbon content is scientifically based and is the general trend, because only a high carbon content can guarantee a large amount of graphite and have better thermal conductivity and thermal fatigue resistance. The mandatory regulations made by the United States must have its scientific basis. For us, we should also have the ability to produce qualified mechanical properties, hardness and metallographic structure under the premise of high carbon content.
Through the domestic practice of producing high-strength cast iron with high carbon content over the years, it should be said that a lot of successful experience has been accumulated, and a consensus has been achieved in technology. This has laid a good foundation for our production of brake drums, and the actual situation is also true. The quality of brake drums produced by many large enterprises has been able to meet customer requirements stably. These technologies, in summary, are taking the road of synthetic cast iron. The technology adopted is based on the high proportion of scrap steel added, using a recarburizer to increase recarburization, increase sulfur in the molten iron, good incubation and sufficiently high temperature molten iron. Recently, the pretreatment of molten iron has been proposed. I have already talked a lot about this aspect and published many articles. I will not repeat it. I just want to combine the specific casting of the brake drum and put forward a few comments for your reference
2. Regarding the issue of conception
The purpose of inoculating brake drum liquid iron is the same as that of producing other high-grade cast iron parts. It should mainly ensure that no cementite appears or the total amount of ferrite and carbide does not exceed 5% to ensure a good graphite shape. (Generally it is stipulated that A graphite should be greater than 80%. B, D, E graphite should not be greater than 20%) to ensure good mechanical properties, and at the same time to improve machinability, in the production practice of gray cast iron, its inoculation is generally 0.2 Between %-0.6%. What I want to remind everyone at this point is, please pay attention to the fertility and control the fertility. Because in the minds of most on-site casting technicians and workers, most of them are concerned about how to improve the inoculation effect, how to increase the graphite core, and how to use efficient inoculants. The production of gray cast iron is also the same as the production of ductile iron. It uses multiple inoculations and uses as many inoculants as possible, ignoring the effect of inoculation on the shrinkage properties of gray cast iron. And forget that the shrinkage cavities and porosity accounted for a large proportion of the waste products of the brake drum, and there is no connection between the shrinkage waste products and the abnormal failure of the brake drum.
We all know that, in addition to the scrapped brake drums produced by various factories, many qualified castings in the warehouse have shrinkage holes and shrinkage defects, and most of the manufacturer’s technicians only stop the measures to solve the shrinkage porosity. Lower the pouring temperature and improve the design of the pouring system. I'm just here to tell everyone. More attention and control should be paid to the incubation process of the brake drum.
Many people have now realized that inoculation can promote shrinkage porosity. In the range of carbon equivalent of 3.9-4.3%, the size of inoculated castings is always larger than that of infertile castings. Infertile castings have no shrinkage porosity, but inoculated castings produce Shrinking loose. Therefore, in the production of brake drums, it is necessary to control the inoculation amount not to be too large. Under the condition of ensuring that no cementite appears and ensuring the machining performance, try to add as little inoculant as possible, and not excessive if it is enough. The key point is to do well with the flow inoculation. Do not take two, three, or even four gestations during the process.
3. Regarding the tightness of the mold
The internal shrinkage cavity and porosity of iron castings and the surface shrinkage of castings are largely affected by the mold. After the molten iron is poured into the mold, the volume of the cavity will move the mold wall under the static pressure and heat of the molten iron, which will cause the volume of the mold to become larger, and the size of the casting will be out of tolerance and the weight will increase. The size of the deformation depends on the compactness of the sand mold, the molding material and the performance parameters of the sand. Some people abroad have done research in this area. They extract the brake drum from the mold production line, measure its size and weigh its weight. The results showed that the weight of each sample fluctuates greatly. As shown in the figure below, the weight of the brake drum ranges from 162 pounds to 173 pounds, and the maximum difference is 11 pounds (1 pound is 453 grams). The molding line of the test brake drum is Shock pressure molding machine. This difference in weight indicates that the quality of the mold fluctuates. The sand-impacted soft mold produced severe sand bulging. For molds with good compactness, the swelling is very slight, and the size of the castings is accurate. They found that the brake drum with severe swelling has shrinkage inside, and the quality of the brake drum with normal weight is normal. Therefore, they used this simple inspection method to judge the internal shrinkage of the brake drum by weighing before transporting to machining, and believed that the shrinkage of the brake drum was caused by the movement of the mold. Therefore, improving the rigidity of the mold becomes an important measure to avoid shrinkage and looseness of the brake drum.
The use of iron-type sand-covered brake drums to produce brake drums now promoted in China has no shrinkage defects due to its characteristics. A large-scale enterprise in Shanxi that adopts this process to produce brake drums. There have been three semi-mechanized iron-type sand-coating lines, with more than 430 Nissan brake drums. The process yield rate is 90%, and the product qualification rate is stable at 98%. The fourth iron-type sand-coating line is currently being installed.
A factory in Nanyang, Henan Province uses resin sand to produce Beiben heavy-duty brake drums with top injection and no riser technology, with stable quality and no shrinkage.
In some factories, the distance between the sprue and the brake drum is too close, which is 40mm. The molding sand here is difficult to crush, so shrinkage holes and porosity are often produced here. The distance is changed to 60-80mm, shrinkage porosity It's much lighter.
Some small factories first hit the sand as a whole, and then use a steel rod to insert the sprue to make the entire mold even tighter and easy to hit, reflecting that the casting shrinkage is not serious.
Please keep the source and address of this article for reprinting: The Production Process Of Brake Drum For Truck
Minghe Die Casting Company are dedicated to manufacture and provide quality and high performance Casting Parts(metal die casting parts range mainly include Thin-Wall Die Casting,Hot Chamber Die Casting,Cold Chamber Die Casting),Round Service(Die Casting Service,Cnc Machining,Mold Making,Surface Treatment).Any custom Aluminum die casting, magnesium or Zamak/zinc die casting and other castings requirements are welcome to contact us.
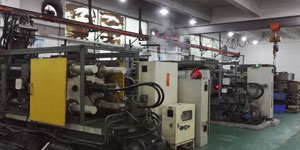
Under the control of ISO9001 and TS 16949,All processes are carried out through hundreds of advanced die casting machines, 5-axis machines, and other facilities, ranging from blasters to Ultra Sonic washing machines.Minghe not only has advanced equipment but also have professional team of experienced engineers,operators and inspectors to make the customer’s design come true.
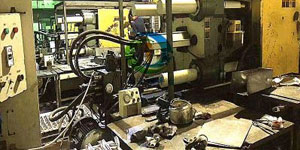
Contract manufacturer of die castings. Capabilities include cold chamber aluminum die casting parts from 0.15 lbs. to 6 lbs., quick change set up, and machining. Value-added services include polishing, vibrating, deburring, shot blasting, painting, plating, coating, assembly, and tooling. Materials worked with include alloys such as 360, 380, 383, and 413.
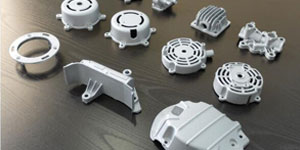
Zinc die casting design assistance/concurrent engineering services. Custom manufacturer of precision zinc die castings. Miniature castings, high pressure die castings, multi-slide mold castings, conventional mold castings, unit die and independent die castings and cavity sealed castings can be manufactured. Castings can be manufactured in lengths and widths up to 24 in. in +/-0.0005 in. tolerance.
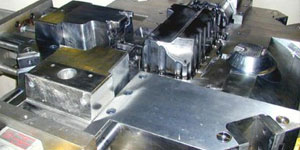
ISO 9001: 2015 certified manufacturer of die cast magnesium, Capabilities include high-pressure magnesium die casting up to 200 ton hot chamber & 3000 ton cold chamber, tooling design, polishing, molding, machining, powder & liquid painting, full QA with CMM capabilities, assembly, packaging & delivery.
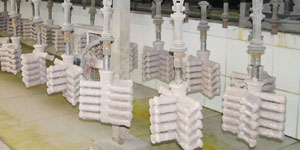
ITAF16949 certified. Additional Casting Service Include investment casting,sand casting,Gravity Casting, Lost Foam Casting,Centrifugal Casting,Vacuum Casting,Permanent Mold Casting,.Capabilities include EDI, engineering assistance, solid modeling and secondary processing.
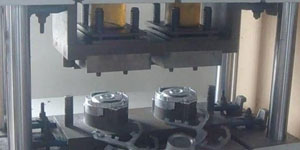
Casting Industries Parts Case Studies for: Cars, Bikes, Aircraft, Musical instruments, Watercraft, Optical devices, Sensors, Models, Electronic devices, Enclosures, Clocks, Machinery, Engines, Furniture, Jewelry, Jigs, Telecom, Lighting, Medical devices, Photographic devices, Robots, Sculptures, Sound equipment, Sporting equipment, Tooling, Toys and more.
What Can we help you do next?
∇ Go To Homepage For Die Casting China
→Casting Parts-Find out what we have done.
→Ralated Tips About Die Casting Services
By Minghe Die Casting Manufacturer |Categories: Helpful Articles |Material Tags: Aluminum Casting, Zinc Casting, Magnesium Casting, Titanium Casting, Stainless Steel Casting, Brass Casting,Bronze Casting,Casting Video,Company History,Aluminum Die Casting |Comments Off