The Production Technology Of Microalloyed Steel
Production technology of pipeline steel
1. Pipeline steel
Medium and thick plates and coils used in the manufacture of oil and natural gas gathering and long-distance pipelines or coal and building materials slurry pipelines are called steel for pipelines. Generally, medium and thick plates are used to make thick-walled longitudinally welded pipes, and coils are used to produce longitudinally welded resistance welded pipes or submerged arc spiral welded pipes. The domestic production capacity of 600,000 tons of spiral welded pipes with an annual diameter of 1800mm or less has been established. In recent years, a production line for straight seam thick-wall welded pipes with a diameter of 1600mm or less has been established. The domestic production of pipeline steel that meets the AP15L standard pipeline engineering design requirements has only a history of more than 10 years. Baosteel is the first to be produced, as well as Anshan Iron and Steel, Wuhan Iron and Steel, Panzhihua Iron and Steel, Jiuquan Iron and Steel, Wugang, etc., stable production of X60-X65 pipeline steel and Occupying a certain position in the international market, the quality of the trial-produced X70 pipeline steel has also reached the international advanced level.
2. Current status of domestic and foreign oil and gas pipeline construction
In the past 50 years, there were 241 auxiliary gas pipelines in Europe, and the consumption of steel reached 5.03 million tons. The use of X65 and X70 pipeline steel accounted for 89%; 33 oil pipelines used 260,000 tons of steel, and X65-X70 pipes were 40 %. X70 grade steel accounted for 55.25% of the newly built oil and gas pipelines in North America between 1969 and 1998. So far, 8 X80 gas pipelines have been built in the world, with a total length of 462Km, pipe diameters f1118-f1219, and wall thicknesses of 12.0-13.6mm. And has successfully developed X90 and X100 grade pipeline steel.
China's oil and gas pipeline construction has entered the second peak period, and the scale of oil and gas development in the next 10 years will exceed the previous 50 years. The oil pipeline of 7540Km and the gas pipeline of 14570Km will be laid. Approximately 5.08 million tons of X42-X65 pipeline steel will be required. The length of the domestic part of the Sino-Russian oil pipeline project and the other four international gas pipelines will be 12385Km. The West-East Gas Pipeline Project is X70 grade, and the designed gas transmission pressure is 10Mpa. Estimated based on the pipe diameter f1016 and the wall thickness of 14.7mm, the pipeline steel needs about 1.75 million tons.
3. Technical requirements for pipeline steel
Modern pipeline steel is a low-carbon or ultra-low-carbon microalloyed steel. It is a product with high technical content and high added value. The production of pipeline steel has almost applied all the new technological achievements in the metallurgical field for more than 20 years. The current development trend of pipeline engineering is large pipe diameter, high pressure rich gas transportation, high cold and corrosive service environment, and thicker submarine pipelines. Therefore, modern pipeline steel should have high strength, low Bauschinger effect, high toughness and resistance to brittle fracture, low welding carbon content and good weldability, as well as resistance to HIC and H2S corrosion. The optimized production strategy is to improve the cleanliness and organization uniformity of steel. C≤0.09%, S≤0.005%, P≤0.01%, O≤0.002%, and adopt microalloying, vacuum degassing +CaSi, light reduction in continuous casting process, multi-stage thermomechanical rolling and multi-function Intermittent accelerated cooling and other processes. The performance of pipeline steel is very stable, the fluctuation value of X70 yield strength and tensile strength is less than 70Mpa, and the impact energy fluctuation value of anti-HIC steel is about 70J. There is no toughness index for pipeline steel in domestic and foreign pipeline specifications, only specific requirements for pipe materials:
- ① DWTT≥85%SA at the lowest operating temperature (-5℃);
- ② Charpy impact absorption energy ≥145J at the lowest operating temperature (-5℃).
Production technology of shipbuilding steel
1. Shipbuilding steel
Steel materials used to build civil or military ships are called shipbuilding steels. There are steel plates, profiles, pipes, castings and forgings, etc. But traditionally, shipbuilding steel only refers to steel plates used for ship hulls. There are three categories: general-strength shipbuilding steel plates, high-strength shipbuilding steel plates, and naval ship hulls.
2. Technical requirements for shipbuilding steel
- ① Requirements for strength. The higher strength can reduce the weight of the hull, reduce the welding workload, and increase the load-bearing capacity. The use of high-strength steel is restricted by the rigidity and corrosion resistance of the hull.
- ② The shape of the hull is relatively complicated. There are many types of single curves or hyperboloids, and various forming operations such as cold, hot bending and correction are required. The suitability of the steel to the shipbuilding process is required, including welding and repairing.
- ③ The requirements for plasticity and toughness are sufficient to compensate for the influence of work hardening and thermal cycles on the material due to various operations in the construction process. For important parts such as the bow, the part where the longitudinal bending stress of the hull is the largest, the bottom of the ship and the side crack arrester, high crack resistance is required, and it is required to have a low extension-brittle transition temperature and sufficient impact absorption under low temperature conditions. .
- ④ Seawater corrosion resistance
3. Demand for shipbuilding steel
In the 1990s, the growth of international shipping volume was higher than the increase in shipping capacity. In the shipping market, new ship construction and old ship transactions were active. In the first five years, new ship transactions reached 32 million displacement tonnages. China's Shipbuilding Industry Corporation alone has built 6.76 million tons of ships, and 3.5-4 million tons can be rebuilt in the next five years. It accounts for 1/10 of the world's shipbuilding volume.
China’s shipbuilding industry has been able to build 280,000-ton class oil tankers, 150,000-ton class bulk carriers, 1,200-ton drilling platforms, 4200m3LPG ships, 3000m3 liquefied gas ships, and full-range self-controlled high-speed hydrofoil vessels.
The shipbuilding capacity of domestic shipbuilding companies, the Ministry of Transport and the Ministry of Agriculture is about 6 million tons. It can build thousands of non-ship products in 24 categories for metallurgy, electric power, petrochemical, hydropower, coal, urban construction and light industry industries. However, the production capacity is slightly lower than Japan's 14 million tons and South Korea's 13 million tons.
At present, the annual demand for shipbuilding steel is 2 million tons, of which shipbuilding steel plates are about 1 to 1.2 million tons. Basically, four steel products and five grades of ship plates can be produced in China. The demand for 240Mpa general-strength shipboard is still the main one, and 450, 600Mpa-level high-strength shipboard can also be produced.
4. Key points of production technology of shipbuilding steel
- ① For Class A and D ship plates, cleanliness requirements are ≤0.008s, ≤0.015P, Class E requirements are ≤0.005%S, ≤0.010%P, Class F requirements are ≤0.002%S, and ≤0.005%P. For steel plates for naval vessels, to ensure NDT≤-550C, it is required to be ≤0.002%S, ≤0.005%P, ≤40ppmN, ≤10ppmO and ≤1.0ppmH. The refining process is essential.
- ② Grades A and D can be delivered by hot rolling and controlled rolling. Grades E and F allow normalizing or thermomechanical rolling.It is necessary to distinguish the gap between controlled rolling and thermomechanical rolling. The current standard stipulates that no E-class and F-class ship plates can be produced without heat treatment conditions.
- ③ The quality requirements of steel also include requirements for shape and dimensional accuracy, requirements for ultrasonic flaw detection and requirements for performance stability.
At present, almost all domestic steel mills with rolling plate conditions have passed the demonstration and can produce general strength Class A, B, and D ship plates.
However, the E-class and high-strength class of general ship plates are limited to Anshan Iron and Steel, Wuhan Iron and Steel, Wushan Iron and Steel, Pudong Iron and Steel, and Chongqing Iron and Steel.
Production technology of steel for bridges
1. Steel for bridges
The steel for bridges mentioned here refers to steel plates or profiles used for bolt-welded structures of large box girder structures, highway bridges and railway bridges, excluding steel wire ropes for suspension cables and suspension cables, and high-strength bolts steel for bolt-welded beams.
2. Characteristics of bridge steel
In the 1950s, bridge construction transitioned from riveted structure to welded structure. The requirements for bridge steel have changed a lot. There are mainly several aspects: higher strength, good weldability, good fracture and aging performance. , Higher low-cycle fatigue performance, and better atmospheric corrosion resistance. Historically, 3% chromium steel or nickel steel was used to build bridges. After using low-alloy high-strength steel, the yield strength of bridge steel was gradually upgraded from 230Mpa to 590Mpa tensile strength and 785Mpa quenched and tempered heat treatment type. The steel, some foreign atmospheric corrosion-resistant steels are also used to build bridges, such as Japan's SMA570. Corten steel in the United States, etc.
3. Demand for bridge steel
In the 1950s,China used 345Mpa grade CXЛ-1 steel to build the Wuhan Yangtze River Bridge. In the 1960s and 1980s, the Nanjing Yangtze River Bridge and other bolt-welded bridges were basically built with the same strength grade of 16Mnq steel. For the first time on the line, 440Mpa grade 15MnVNq steel was used to construct the Jiujiang Yangtze River Bridge. The application of microalloying and controlled rolling steel has opened a new page in China's modern bridge steel. StE355 steel is used for the Nanpu, Yangpu and Xupu bridges on the Huangpu River in Shanghai, and 14MnNbq steel is used for the Wuhu Yangtze River Bridge, Wuhan Yangtze River Second Bridge and Nanjing Yangtze River Second Bridge.
The average annual construction of general roads in China is 8500Km and highways are 1300Km. There are 8 highway bridges with a single span of more than 400m. In terms of railway construction, including east-west passage, west-south passage and international railway projects, a total of more than 10,000 kilometers will be newly built and reconstructed. Only the bridge construction on the line requires 150,000 tons of bridge steel. It is predicted that during 2001-2005, the demand for steel plates for bridges will be between 230,000 and 250,000 tons.
4. Technical points for the production of steel for bridges
Bridge steel is distinguished between weathering steel and non-weathering steel, and non-weathering steel is the main type. Typical steel grades are 16Mnq, 15MnVNq, 14MnNbq, SM490. SM520, SM590B, C, ASTMA709, STE355, STE380, STE420, etc. According to the development trend of domestic applications, 14MnNbq is mainly used for railway bridges, and STE355 is mainly used for suspension bridges and cable-stayed bridges of highways. Both of these grades belong to Nb-containing, microalloyed steel.
Regardless of converter or electric furnace smelting, refining outside the furnace is required, and cleanliness requirements are not very high, but it is necessary to ensure that ≤0.010%S.≤0.02%P.
In terms of performance, a smaller range of fluctuations is required. Nb-Ti composite microalloying (14MnNbq) and Nb-V-(Mo) composite microalloying can not only achieve impact absorption energy of 120~160J and zero plastic transformation temperature below -45℃, but also have better Anti-aging performance is very important for bridge steel.
Production technology of steel for high-rise steel structure construction
1. Steel for high-rise steel structures
Since the 1950s, high-rise buildings have become the international development trend of urban architecture. China's building codes are also developing, especially since the reform and opening up, high-rise buildings have become a symbol of urban modernization, from reinforced concrete structures, reinforced concrete-steel hybrid structures, and transitioning to steel structures. Steel structure buildings use special steel plates and profiles. Due to the particularity of technical requirements and production processes, a special steel variety is formed, collectively referred to as steel for high-rise steel structures.
2. The status quo of high-rise steel structures in China
The modern high-rise steel structure buildings for civil use in China started in 1985, and about 30 buildings have been built or are under construction. The completed structures of Shenzhen Diwang Building with a height of 294.1m and Shanghai Jinmao Building with a height of 365m are the current high-rise steel buildings in China. The most structural building, the total steel consumption is 12,000 tons and 14,000 tons respectively.
Before 1976 in Taiwan Province of China, the height of buildings for residential use was no more than 20m. In 1977, the height was relaxed to 200m. After 71 years, earthquake-resistant steel and frame diagonal bracing structure were adopted, and 16 buildings have been completed so far. The Shin Kong Life Building in Taipei City was built in 1990 with 50 floors and used 20,000 tons of steel. Kaohsiung International Plaza was completed in 1993 with 85 floors and used 58,000 tons of steel.
3. Basic technical requirements for steel structure
- ① High-rise steel structure buildings are subject to complex forces, requiring safety and reliability, and being able to withstand sudden disasters (such as water, fire, earthquake, storm, etc.). Therefore, in addition to sufficient yield strength and tensile strength, it is also required to have a low yield ratio, good cold deformation ability and high plastic deformation work, so that no instantaneous fracture will occur in the case of local overload instability.
- ② Has good weldability
- ③ Good fracture toughness
- ④ The steel used for welding and connecting beam-column joints with a thickness of more than 40mm requires laminar tear resistance
4. Technical key points of steel for high-rise steel structure building
The production of this special steel variety in China started late. At present, Wugang and Pudong Iron and Steel have formed plate production bases and H-shaped steel production bases based on Maanshan Iron and Steel and Anshan Iron and Steel. The main steel grades are Q345B, Q345B—Z8 .5, SM400B, SM490B, SM490B-Z25, and ASTMA572/A572M Gr50, etc.
- ① Wugang adopts the process of ultra-high power electric furnace smelting-LF/VD external refining-continuous casting or die casting-4200 rolling mill-heat treatment. Products are used in Tianjin Yunding Building, Shanghai Information Hub Building, Dalian Yunshan Building, Xiamen International Convention and Exhibition Center.
- ② Pugang adopts the technological process of Baosteel TDS hot metal pre-desulfurization-converter smelting-cas-OB/RH-OB refining-continuous casting of steel billets by the 4200/3500 rolling mill of the factory-double walking beam heat treatment furnace. The products have also been successfully used in the construction of Dalian Ocean Building, Shenzhen World Trade Building, Tianjin International Trade Building and Changchun Everbright Bank.
- ③ Maanshan Iron & Steel: H-shaped steel production adopts multi-stand universal H-shaped steel rolling mills imported from Germany and the United States. Has a high degree of automation. The total design capacity of Maanshan Iron and Steel, Anshan Iron and Steel and Laiwu Iron and Steel is 1.4 million tons. Can produce 100-700mm products. At present, the narrow flange series with a belly height of more than 700mm and the wide flange series with a flange width of more than 400mm cannot be produced. These specifications are used in railway bridges and offshore oil platforms in a high proportion.
5. Special requirements for construction steel
- ① The high-rise steel structure building bears the action of wind load, and the displacement angle between floors is 1/400, which is about twice that of the reinforced concrete structure. Under the action of an earthquake, the displacement angle between floors is 1/250, which is about twice that of the reinforced concrete structure. Take Shanghai Pudong Finance Building as an example, the wind load displacement angle is 1/533, and the earthquake displacement angle of Beijing China International Trade Center is 1/266.
- ② The yield strength of general construction steel is basically stable below 3000C. At 500°C and 600°C, the yield strength is 0.48 and 0.27% at room temperature, respectively. It is very important to improve the fire resistance of steel, which is far more labor-saving and material-saving than the use of fire-retardant coatings and the addition of fire-retardant layer structure, which increases the effective use area of the building and reduces environmental pollution. Japan and the United States have set the index requirements for refractory steel, and the yield strength is greater than 2/3 of that at room temperature within 1-3 hours at 600°C.Existing experience shows that steel with acicular ferrite and benzal structure has high-temperature strength stability. Adding Mo, Mo-Nb and reducing Mn can effectively improve fire resistance.
- ③ Widely use light steel construction color coated steel plate
Production technology of automobile steel
The automobile manufacturing industry is a symbol of a country's comprehensive national strength. Vigorously develop China's automobile production and list the automobile manufacturing industry as a supporting industry is one of China's economic development goals since the "Eighth Five-Year Plan". It is planned that in 2000, the total output of automobiles will be 2.7 million, and the amount of automobile insurance will reach 2210-23.2 million. By 2010, it will be 6 million and 44-50 million, respectively. How to realize the localization of automobile steel and improve the quality of automobile steel has become a key issue.
1. Automotive Steel
Automobile manufacturing mainly uses iron and steel materials. Generally speaking, automobile steel refers to three categories:
- ① Steel for automobile beams
- ② Steel for automobile rolling wheels
- ③ Stamping sheet steel
All types of trucks mainly use high-strength stamped steel plates to manufacture the longitudinal beams, crossbeams and bumpers of the chassis; the rims and spokes of the wheels generally use hot-rolled plates, and the production of cars is mainly cold-rolled or hot-rolled sheet, and hot-dip galvanized Thin plates account for the main part. The current development of ultra-light cars requires high-strength deep-drawable plates, while high-end cars require IF steel and fingerprint-free steel plates. The agricultural vehicle series require durable steel plates, and the strength level and accuracy are not the main goals.
2. Basic requirements for automotive panels
In addition to the necessary strength and plastic toughness ratio for structural materials, it is also necessary to meet:
- ① Good formability, can be stamped and formed, wrinkle-resistant and crack-resistant,
- ② Good rigidity and anti-sag performance, which can absorb energy to the maximum in the case of collision.
- ③ Good corrosion resistance. For cars, it is required to have no rust for 5 years and no perforation for 10 years.
- ④ Good weldability to ensure efficient online welding and assembly.
- ⑤ Good sprayability and excellent attachment to the coating layer.
- ⑥ Higher dimensional accuracy and surface quality. It is the demand for automatic production lines and the demand for high-quality cars.
3. Steel for conventional vehicles
Automobiles usually use hot-rolled carbon steel plates, high-strength low-alloy steel plates, hot-rolled sheets, cold-rolled sheets, hot-dip galvanized sheets, electro-galvanized sheets, aluminum-plated sheets, chrome-plated sheets, color-coated sheets and stainless steel sheets.
The current development trend of automotive sheet varieties is in four aspects:
- ① For ultra-deep-drawing and super-deep-drawing thin plates, the third generation of stamping steel is mainly the production of ultra-low carbon non-interstitial atomic steel.
- ② In order to meet the existing excellent stamping formability, the production of all bake hardened steels with sufficient rigidity, dent resistance and corrosion resistance.
- ③ Production of galvanized sheet with alloying treatment to improve corrosion resistance.
- ④ The production of high-brightness mirror panels improves the flatness, reflectivity and lubricity of automotive panels.
4. Technical points of automobile plate production
Take stamping or forming automotive sheet as an example:
- ① The total amount of S, P, N, O, and H is less than 100ppm through the process technology of hot metal pretreatment, selected scrap steel and ladle refining
- ② Low carbon or ultra-low carbon, combined converter blowing and vacuum degassing technology can make the carbon content of steel less than 10ppm
- ③ The content of microalloying elements is controlled within 0.02%.
- ④ In order to ensure the excellent comprehensive performance of high-strength steel plates, a multi-stage forced cooling process is adopted if conditions permit.
- ④ Pay attention to the annealing process of cold-rolled sheets to achieve the maximum uniformity of mechanical properties.
Production technology of container steel
1. Main features of container steel
Container transportation is the main modern transportation method in the world today. With the active international trade, the development of multimodal transportation, and the communication of land bridges, the development of container transportation is becoming more and more important.China's container manufacturing industry started late, but it has developed rapidly, with about 40 manufacturing plants. The output in 1993 was the first in the world, and the output in 1997 was 1 million TEUs. It accounts for 70% of the world's total output.
The main steel materials for container manufacturing include steel plates, channel steels, square pipes and castings.
In 1997, China produced 1.1 million tons of various types of steel for containers, 300,000 domestic steel plates, and 400,000 tons of imported steel plates. In recent years, Baosteel and Wuhan Iron and Steel have developed a series of weather-resistant steel plates and non-weather-resistant steel plates for containers. The self-sufficiency rate of steel plates has reached 75% for Corten boxes and semi-Corten boxes. With the development of high-tech, high-value-added refrigerated boxes, insulation boxes, tank boxes, foldable flat-frame boxes, etc., the demand for corrosion-resistant steel and low-temperature resistant steel has increased.
2. Technical requirements for the production of container steel
There are three main requirements for container panels:
- ① Sufficient anti-sag and anti-damage properties.
- ② Good corrosion resistance, especially the corrosion resistance of the marine atmosphere is required.
- ③ Good processing performance requires weldability and formability.
The reason for the widespread use of Corten steel is that the yield strength is 40% higher than that of carbon steel, it can withstand greater impact, does not appear dents and scratches, and has good surface paint adhesion. Bare Corten steel will not corrode in the sea for a long time.
Baosteel has produced more than 300,000 tons of steel for containers since 1996, and developed three types of ordinary economical Cu-p weathering steel, high weather resistance steel and high weldability steel. WISCO has developed weathering steel for container manufacturing, with an annual production capacity of 300,000 tons.
Production technology of steel for construction machinery
1. Steel for construction machinery
The equipment used in mining and various engineering constructions, such as drilling rigs, electric furnaces, electric wheel dump trucks, excavators, loaders, bulldozers, various lifting equipment and coal mine hydraulic supports, are collectively referred to as engineering machinery. The materials for welding structural parts required for the manufacture of these machines are usually referred to as construction machinery steels, which belong to the category of welded high-strength steels. Steel for construction machinery can also include profiles, track shoes, wear-resistant cast steel, steel ropes, and steel strands.
In 2000, the demand for high-strength steel plates of various construction machinery is shown in Table 22. The approximate annual increase in demand is 12-15%. It is predicted that the consumption will be 1.4 million tons and 2.2 million tons in 2005 and 2010, respectively.
2. Technical requirements for steel for construction machinery
There are basically two types of steel plates for construction machinery, one is welded high-strength steel plates, and the other is high-hardness and wear-resistant plates.
For welding high-strength steel, the main structure of construction machinery is subjected to complex and variable cyclic loads. Therefore, the steel is required to have high yield strength and fatigue limit, good impact toughness, cold formability and excellent welding performance. With the development of construction machinery in the direction of large-scale and light-weight, energy saving and life extension are required, so higher strength levels of steel are required, and the plate thickness is from 6mm to 50mm, even up to 200mm. The strength plates range from 400Mpa to 1200Mpa, and the use states include different types such as hot rolling, normalizing, quenching and tempering, and aging.
High hardness and high wear-resistant steel is mainly used for the wear-resistant parts of construction machinery, such as the bucket plate of the loader, the backing plate of the dump truck, and the shovel teeth of the excavator. The surface hardness of the steel is required to have different levels of HB235-500, so this Class steels are often delivered in the quenched + tempered quenched and tempered state. And choose the steel grade and grade according to the actual hardness and plate thickness.
In terms of steel production technology for automobiles, the former includes strength while improving toughness. For this reason, lower carbon content and welding carbon equivalent should be used to focus on the synthesis and heat treatment process of steel; the latter category Do not pay attention to high weldability. Pay attention to the solid solution strengthening mechanism of the steel and the crystal structure type of the hard precipitate phase and the dispersion distribution in the steel.
3. The development of steel for construction machinery in recent years
- ① With the renewal of steelmaking technology and equipment, new alloy designs and process parameters have been realized, such as deep deoxidation and titanium treatment processes, and the application of thin slab continuous casting.
- ② Using microalloying, the thermo-mechanical treatment of Nb microalloyed steel has been widely promoted and applied.
- ③ The application of the direct quenching technology after rolling of boron-containing steel has produced 980Mpa welded high-strength steel and 1080Mpa weldable wear-resistant steel.
Please keep the source and address of this article for reprinting:The Production Technology Of Microalloyed Steel
Minghe Die Casting Company are dedicated to manufacture and provide quality and high performance Casting Parts(metal die casting parts range mainly include Thin-Wall Die Casting,Hot Chamber Die Casting,Cold Chamber Die Casting),Round Service(Die Casting Service,Cnc Machining,Mold Making,Surface Treatment).Any custom Aluminum die casting, magnesium or Zamak/zinc die casting and other castings requirements are welcome to contact us.
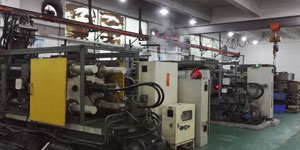
Under the control of ISO9001 and TS 16949,All processes are carried out through hundreds of advanced die casting machines, 5-axis machines, and other facilities, ranging from blasters to Ultra Sonic washing machines.Minghe not only has advanced equipment but also have professional team of experienced engineers,operators and inspectors to make the customer’s design come true.
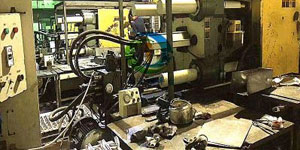
Contract manufacturer of die castings. Capabilities include cold chamber aluminum die casting parts from 0.15 lbs. to 6 lbs., quick change set up, and machining. Value-added services include polishing, vibrating, deburring, shot blasting, painting, plating, coating, assembly, and tooling. Materials worked with include alloys such as 360, 380, 383, and 413.
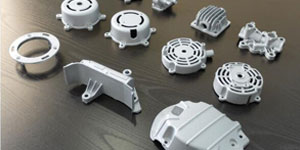
Zinc die casting design assistance/concurrent engineering services. Custom manufacturer of precision zinc die castings. Miniature castings, high pressure die castings, multi-slide mold castings, conventional mold castings, unit die and independent die castings and cavity sealed castings can be manufactured. Castings can be manufactured in lengths and widths up to 24 in. in +/-0.0005 in. tolerance.
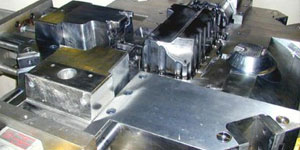
ISO 9001: 2015 certified manufacturer of die cast magnesium, Capabilities include high-pressure magnesium die casting up to 200 ton hot chamber & 3000 ton cold chamber, tooling design, polishing, molding, machining, powder & liquid painting, full QA with CMM capabilities, assembly, packaging & delivery.
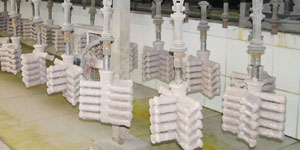
ITAF16949 certified. Additional Casting Service Include investment casting,sand casting,Gravity Casting, Lost Foam Casting,Centrifugal Casting,Vacuum Casting,Permanent Mold Casting,.Capabilities include EDI, engineering assistance, solid modeling and secondary processing.
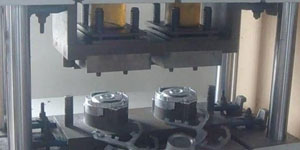
Casting Industries Parts Case Studies for: Cars, Bikes, Aircraft, Musical instruments, Watercraft, Optical devices, Sensors, Models, Electronic devices, Enclosures, Clocks, Machinery, Engines, Furniture, Jewelry, Jigs, Telecom, Lighting, Medical devices, Photographic devices, Robots, Sculptures, Sound equipment, Sporting equipment, Tooling, Toys and more.
What Can we help you do next?
∇ Go To Homepage For Die Casting China
→Casting Parts-Find out what we have done.
→Ralated Tips About Die Casting Services
By Minghe Die Casting Manufacturer |Categories: Helpful Articles |Material Tags: Aluminum Casting, Zinc Casting, Magnesium Casting, Titanium Casting, Stainless Steel Casting, Brass Casting,Bronze Casting,Casting Video,Company History,Aluminum Die Casting |Comments Off