The Quality Control In Quenching With Waste Heat After Forging
Countries around the world vigorously advocate the policy of reducing emissions and consumption: many domestic scholars and companies have taken measures from various aspects, and the quenching of waste heat after forging is one of the important measures.
Residual heat quenching after forging is a high-temperature thermomechanical heat treatment in thermomechanical heat treatment. The data [1, 2, 3] have specific descriptions. So far, many domestic manufacturers have used the after-forging waste heat quenching, and a few manufacturers have launched → dismounted → remounted or mount → dismounted → continue to dismount due to poor quality control measures.
Compared with conventional heat treatment, due to high-temperature heating and casting deformation, the martensite small-angle grain boundary of the steel increases, the dislocation density increases, the original hydrogen partially escapes, the original cracks are healed and reduced, and the carbides are dispersed and precipitated. The quenching hardness of steel parts has improved significantly (generally improved by about 10%). During tempering, steel parts have a high tempering resistance (tempering temperature is improved compared with conventional ones, generally 20℃-30℃).
- 1. When we went to the heat treatment plant for various reasons, many engineering and technical staff suggested that the raw materials and other aspects are good, how to predict the quenching fracture phenomenon after looking at each other? This is the summary of the three major effects (these three major effects also have reference value for hydrogen embrittlement and stress corrosion fracture in the surface treatment process).
- 1.1 Chemical composition effect: For example: carbon steel: same size ф6, same quenching salt water: 35 steel, 40 steel, 45 steel, 50 steel, 55 steel, 60 steel, 65 steel, the result is that 45 steel ~ 60 steel is easily broken. Because the higher the martensite carbon content, the greater the stress, and the maximum carbon content is about 0.6%. When the carbon content of steel is very high, it will be more than 0.6%, and residual A will be generated, which slows down the selective release of martensite stress and is not easy to fracture. Generally speaking: Alloy steel is the most vulnerable to quenching and cracking. For example: 42CrM. When the size is large ф100, the quenching water will not crack. This is the size effect described below.
- 1.2 Size effect: For example: 45 steel: ф1, ф2, ф3...... ф10 quenching results found that ф6 is the most likely to be quenched. Because below ф6, it can generally be quenched into martensite. However, the overall transformation of ф6 into martensite has the largest stress, so it is the easiest to break.The same reason: the maximum overall stress of alloy steel is the hardenability index (hardenability is half martensite), which is about 2/3. Therefore, first check the hardenability index of a certain alloy steel, and then look at the workpiece. What is the most dangerous size?
- 1.3 Shape effect: sudden change in cross-section, too small R angle, protruding adjacent sharp corners, deep grooves on the edges, punching and marking sharp edges, blind holes, bottom openings, portal openings, improper hole spacing, and different aperture sizes Etc., cross-sectional area asymmetry, etc.
- 2. Selection of pre-cooling temperature:Everyone knows that the martensite structure grains of directly quenched without pre-cooling after forging are smaller. It can meet the current domestic general metallographic standard requirements, and the performance is also good, but for large and complex parts, quenching oil cannot meet the requirements, quenching with water or aqueous quenching medium will easily cause cracking. It is quenching oil, in order to prevent pollution and save costs, it should be changed to water-based quenching medium as much as possible;42CrM in the Steyr heavy-duty truck assembly produced by a company in Chongqing. Steel; Forgings of front axle beam and balance shaft, a certain technical staff of the company unilaterally changed the pre-cooling ≈800℃ to ≥850℃ direct quenching, which caused about 80% of large quenching cracks. Of course, the cause of the fracture was analyzed, and the B content of the raw material reached 0.0022% of the inspection report of the Chongqing Construction Group, and the Changan Group of the Southwestern Physical and Chemical Inspection Center of the Ministry of Weapons reported 0.0042%. Note: (1). The national military standard GJB2720-1996, the boron content standard of boron steel is 0.0005~0.0035%; (2). The technical conditions of gold-bearing structural steel GB3077-88 boron content standard of boron steel is 0.0005~0.0035%. Band segregation to level I... is also one of the reasons.The problem of severe zonal segregation of raw materials reaching level I is an important factor for cracks (heavier segregation causes uneven chemical composition and heat treatment quenching stress distribution, which is easy to cause quenching cracks);
Using X-ray energy spectrum analysis:The grain boundaries and matrix in the prepared metallographic sample structure were analyzed qualitatively and semi-quantitatively with a Vantage X-ray energy spectrum analyzer. The analysis results are shown in Figure 1, Figure 2 and Table 1.
However, the other furnace steel has high boron content and large segregation. The PAG concentration is adjusted by lowering the pre-cooling temperature, so no cracks have occurred.
The choice of pre-cooling temperature: First of all, according to the three effects mentioned above, determine the most vulnerable part. The process parameters should be adjusted appropriately. E.g:
- (1) "Above front axle beam" 42CrM. We pre-cool ≈800℃ to quench PAG, and it is easy to control HRC at 48-52.
- (2) A large motorcycle crankshaft factory in Chongqing: adopts the method of queuing and pre-cooling after forging to achieve pre-cooling ≈770 ℃ for quenching PAG, and adopts a mesh belt lifting mechanism to leave the liquid surface without being cold and slightly self-tempering. After blanking, the pre-cooling temperature of 45 steel and 40Cr is similar, but the PAG concentration is different.
- (3) A crankshaft factory in Chongqing: adopts a device that enters a constant temperature furnace after forging to keep it pre-cooled at ≈770℃ and quench into a water-based solution...
The choice of quenching medium: based on the latest research from all over the world, the so-called hard shell effect. Requirements: The first cooling rate of pearlite rotation must be fast to form a hard shell effect with compressive stress. The martensite turns slowly, so that cracks are not easy to occur, and a series of research results such as the use of program-controlled spray cooling to control the speed are worthy of popularization and application.
The PAG-ⅢA and PAG-ⅢB quenching fluids developed by us are based on the urgent need for a new type of pearlite transformation speed similar to salt water and alkaline water, and martensite transformation speed similar to oil, which truly replaces water quenching and oil cooling. Quenching liquid, and the anti-rust ability is maintained for more than 5 days. To make the pearlite change similar to salt and alkaline water, the bubble film formed when the quenching work enters the liquid must be quickly ruptured, so that the cooling rate is accelerated. For example, at a concentration of 3%, the first cooling rate is not as good as brine and alkaline water, that is, one or more mixed additives must be added to meet the above requirements. In fact, the concentration of PAG-ⅢA reaches the first speed faster than water and polyvinyl alcohol, and the second speed is slower than that of other manufacturers under the same concentration of PAG....... In carburizing and quenching of mesh belt furnaces: PAG-ⅢA has been developed and applied in many ways... At present, there are more than 20 mesh belt furnaces in use across the country; especially mesh belt furnace carburizing solves the problem of soft spots, insufficient hardness, large deformation... …. The anti-rust ability is more than 5 days, and the consumption of PAG is reduced by 20%.
There are 6 PAG-ⅢA applications in Chongqing. Because some manufacturers use this model, some special products solve problems that are difficult to solve with other media, and the output is increasing. For the sake of confidentiality, we will not introduce them one by one. It is widely used in high frequency; medium frequency quenching automobile axle shaft.
Concentration, temperature and stirring of quenching liquid
The unit we serve: the PAG concentration of the quenching liquid, according to the steel grade, the size of the parts, and the external dimensions according to the theory and experience to adjust its concentration....
The liquid temperature is controlled at 30-50℃, and a large circulating pool outside the plant is used for circulating heat exchange. Stirring and circulation are an integral whole.
Hardness control after quenching
The hardness after quenching is a very important indicator to prevent cracking: especially when water-based quenching fluid is used, the higher the hardness, the cracks and the increase in deformation are easy to occur. Take 42CrMo. For example, the front axle beam should be controlled at HRC48~52.
Tempering should be done immediately after quenching
Quenching and tempering interval: ≤30 minutes (The military and civilian products of Chongqing Construction Group require that the water-based liquid quenching to the water return interval exceeds 30 minutes, then it will be scrapped) Small parts production can be used in continuous tempering production lines.
Metallographic structure and properties after forging and quenching
Forging heat quenching, if pre-cooling is required, the grains are generally larger. Data [1, 2, 3] due to the test of the students' graduation thesis that year, the small specimens generally used are not pre-cooled and directly quenched, giving a very important Theoretical basis.
With people’s innovation and development: the current production technology currently adopts pre-cooling and quenching, and the grain size is generally 2-3, but the performance is excellent. Take the above-mentioned front axle beam as an example: The grain is small, and the standard fatigue cycle data is that it is allowed to break after 900,000 times, and the pre-cooling and quenching fatigue cycle after forging is adopted to reach 1.3 million times without breaking.
Why is the forging, pre-cooling and quenching coarse grains and good test performance? The main reason is that the small-angle grain boundaries increase and the dislocation density increases, which are invisible under a general metallurgical microscope. Therefore, many forging and quenching units have to "teach problems" with the previous inspection unit. For this reason, it is an urgent matter for the engineering and technical staff who are currently engaged in metallographic standards to quickly formulate forging and quenching metallographic standards...
Conclusion
- Application of pre-cooling method for waste heat quenching after forging The choice of pre-cooling temperature is based on the required structure and performance, as long as it meets the requirements, the lower the better.
- After forging, the quenching medium for quenching by residual heat is selected as far as possible to use the first cooling rate (the pearlite transformation rate) to form a hard shell effect. The second quenching liquid with slow cooling rate (slow martensite transformation rate).
- When the raw materials and other aspects are good, whether the pre-planning is to produce cracks should understand the three major effects.
- The chemical composition and segregation of raw materials are particularly prone to cracks. It is recommended that when the furnace number is changed, a small batch of trial production and 100% magnetization inspection must be performed. Take advantage to find measures to prevent a large number of scraps from happening.
Please keep the source and address of this article for reprinting: The Quality Control In Quenching With Waste Heat After Forging
Minghe Die Casting Company are dedicated to manufacture and provide quality and high performance Casting Parts(metal die casting parts range mainly include Thin-Wall Die Casting,Hot Chamber Die Casting,Cold Chamber Die Casting),Round Service(Die Casting Service,Cnc Machining,Mold Making,Surface Treatment).Any custom Aluminum die casting, magnesium or Zamak/zinc die casting and other castings requirements are welcome to contact us.
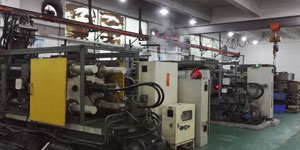
Under the control of ISO9001 and TS 16949,All processes are carried out through hundreds of advanced die casting machines, 5-axis machines, and other facilities, ranging from blasters to Ultra Sonic washing machines.Minghe not only has advanced equipment but also have professional team of experienced engineers,operators and inspectors to make the customer’s design come true.
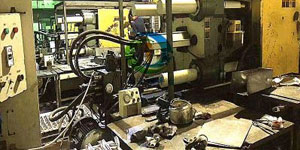
Contract manufacturer of die castings. Capabilities include cold chamber aluminum die casting parts from 0.15 lbs. to 6 lbs., quick change set up, and machining. Value-added services include polishing, vibrating, deburring, shot blasting, painting, plating, coating, assembly, and tooling. Materials worked with include alloys such as 360, 380, 383, and 413.
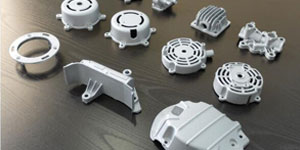
Zinc die casting design assistance/concurrent engineering services. Custom manufacturer of precision zinc die castings. Miniature castings, high pressure die castings, multi-slide mold castings, conventional mold castings, unit die and independent die castings and cavity sealed castings can be manufactured. Castings can be manufactured in lengths and widths up to 24 in. in +/-0.0005 in. tolerance.
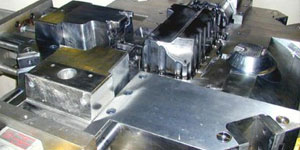
ISO 9001: 2015 certified manufacturer of die cast magnesium, Capabilities include high-pressure magnesium die casting up to 200 ton hot chamber & 3000 ton cold chamber, tooling design, polishing, molding, machining, powder & liquid painting, full QA with CMM capabilities, assembly, packaging & delivery.
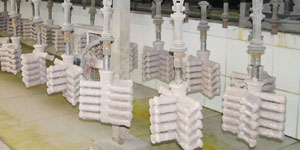
ITAF16949 certified. Additional Casting Service Include investment casting,sand casting,Gravity Casting, Lost Foam Casting,Centrifugal Casting,Vacuum Casting,Permanent Mold Casting,.Capabilities include EDI, engineering assistance, solid modeling and secondary processing.
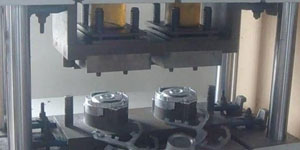
Casting Industries Parts Case Studies for: Cars, Bikes, Aircraft, Musical instruments, Watercraft, Optical devices, Sensors, Models, Electronic devices, Enclosures, Clocks, Machinery, Engines, Furniture, Jewelry, Jigs, Telecom, Lighting, Medical devices, Photographic devices, Robots, Sculptures, Sound equipment, Sporting equipment, Tooling, Toys and more.
What Can we help you do next?
∇ Go To Homepage For Die Casting China
→Casting Parts-Find out what we have done.
→Ralated Tips About Die Casting Services
By Minghe Die Casting Manufacturer |Categories: Helpful Articles |Material Tags: Aluminum Casting, Zinc Casting, Magnesium Casting, Titanium Casting, Stainless Steel Casting, Brass Casting,Bronze Casting,Casting Video,Company History,Aluminum Die Casting |Comments Off