The Rapid Manufacturing Of Complex Castings
China is a large casting country, but not a powerful casting country. Many small and medium-sized enterprises have long relied on the production of simple castings with low added value, but are afraid of complex castings with higher technical difficulties. Because for complex castings, especially for thin-walled castings with complex shapes and produced in small batches, casting has always been a problem. What's more, customers now have high requirements for short cycle and low cost, and traditional craftsmanship is difficult to handle.
The emergence and development of rapid prototyping (RP) provide a promising new way to solve the above problems, so we should make good use of this advanced technology to serve the foundry industry. Rapid Prototyping Technology (RP) is an emerging technology that integrates computer-aided design, precision machinery, CNC laser technology and materials science. It uses the principles of software discretization and material accumulation to convert the CAD model of the designed object into a physical sample. Because RP technology uses the principle of transforming three-dimensional shapes into two-dimensional planes and layered manufacturing, it can handle arbitrarily complex components, and the more complex the components, the more it can reflect its superiority.
But the parts produced by rapid prototyping equipment are only prototypes or models instead of castings. Using these prototypes or models to produce castings can choose a variety of process routes, and how to choose the best process route requires corresponding professional knowledge. The Rapid Prototyping Center of Huazhong University of Science and Technology began research on rapid prototyping technology in 1991. It was one of the earliest units in China to carry out this technology research and achieved fruitful results. It successfully launched a variety of rapid prototyping systems. Has achieved significant economic and social benefits. In recent years, a large number of studies have been carried out on the application of rapid prototyping in various industries, especially the rapid manufacturing of complex castings, and a wealth of experience has been accumulated. Here we introduce these research results to readers.
Selection and comparison of master mold manufacturing methods
At present, a variety of rapid prototyping methods have been studied at home and abroad. The more mature and practical ones are mainly LOM, SLA, SLS, FDM, and 3DP. These technologies have their own advantages and disadvantages. The specific principles and characteristics are as follows:
1. Stereo Lithography (SLA)
SLA is a UV laser scanning photosensitive resin, which is cured layer by layer under the action of the laser. The SLA prototype can replace wooden molds in casting and wax molds in investment casting. SLA technology has fast forming speed and high precision. Since the resin used in SLA is a thermosetting photosensitive resin, it cannot be lost by heating but can only be lost by burning. Therefore, the firing process is relatively high during investment casting, and the prototype is best made into a hollow structure. The SLA prototype is more sensitive to water, and it is easy to absorb moisture and deform in a humid environment for a long time, so pay attention to moisture. SLA's equipment and operating costs are relatively high, and it is suitable for manufacturing thin-wall fine-profile precision casting models.
2. Layered Entity Manufacturing (LOM)
LOM process is a three-dimensional entity that is stacked layer by layer by laser cutting thin materials according to the contour information obtained by layering the parts. The main features of LOM are lower equipment and material prices, and lower operating costs. After the prototype is processed, it has good strength, high precision and no deformation. It can replace complex wooden molds in casting, and is especially suitable for single-piece or small batch production in small and medium-sized foundries.
3. Selective laser sintering (SLS)
The principle is: the laser beam scans the powder under the control of the computer, scanning the entity formed by melting and bonding part of the powder. The biggest feature of SLS technology is a wide range of forming materials. Plastics, ceramics, metals, wax powder, peritoneal sand and their composite materials can all be used as forming materials for SLS to prepare corresponding functional parts, metal parts, wax molds and sand molds (cores) , So the applicability is strong. SLS is currently the most widely used method in China to make wax molds for investment casting. It not only has relatively low cost, but also has high precision, good surface quality and no support. It can produce wax molds with extremely complex shapes to produce complex castings.
4. Fuse deposition (FDM)
Fuse deposition liquefies the material and deposits it layer by layer through a nozzle to form parts. The forming materials include plastic filaments, wax filaments, etc., so plastic prototypes and wax molds are prepared. There is no expensive laser in this process, so the equipment is low in price, and because the material is completely melted, the strength of the part is high. However, the forming speed is slow, the precision of the parts is poor, the surface quality is poor, and the nozzle of the spinneret is prone to casting and clogging.
5.Three-dimensional printing (3DP)
The working principle of 3D printing is similar to that of an inkjet printer. The materials of this technology include ceramics, metal/organic composite materials and so on. This technology has low cost, fast forming speed and high precision, but the surface of the part is rough, the strength is not high, and the print nozzle is easily blocked. In casting, it is suitable for prototype verification to make wax molds or make plaster molds.
Rapid manufacturing and casting method selection
1.Investment casting
The wax model obtained by SLS rapid prototyping can be directly used for investment casting to obtain metal parts. This kind of rapid prototyping process does not need to produce profiling, greatly shortens the production cycle of the blank, and can realize small batch production.
SLS is not only fast in making wax molds, relatively cheap in price, and high in surface quality, but the properties of the wax used are similar to those of high-temperature wax or medium wax in general casting. It can be achieved by slightly changing the current baking process in investment casting. Roasting of SLS wax material is released. SLS wax molds are widely used in investment casting. They can be used to cast small precision castings as well as large complex castings. In particular, they can be welded with conventional low-melting wax modules to form composite wax molds, that is, they can be molded with ordinary wax materials. Making simple parts of castings and using SLS to make complex parts greatly improves production efficiency and reduces wax mold production costs.
The resin parts made by the SLA method can also be used for investment casting. SLA resin parts have high strength and good surface quality, so they can be used to cast very fine small castings. However, due to the complex firing process and the requirement to use SLA special resin that is easy to burn, the manufacturing cost of prototype parts is also high, so it is not as widely used in China as the SLS method. FDM can also extrude wax, but the forming speed of FDM is slow and the surface quality is not high, so there are not many applications in this area.
Investment precision casting is one of the effective methods to realize the mass production of castings. In the traditional investment casting process, the most difficult link is the rapid production of investment molding, which is more prominent for large-scale parts with complex shapes. It is usually designed according to the shape and size of the casting and is made by metal cutting. Long and costly. Use rapid prototyping technology to manufacture master molds, and obtain investment casting profiling through rapid soft molds or rapid transition molds. Then use this pressure-molded injection wax mold, and then use this wax mold to make metal castings through the traditional lost wax casting process, which is not only simple in process but also low in cost. The production process can be divided into:
- (1) Use rapid prototyping to make a master mold and then turn it into a silicon rubber soft mold, a metal cold spray mold, a plaster mold, a ceramic mold, and an alloy mold, an electroforming mold, and an epoxy resin mold that undergo intermediate conversion. When the female mold is used as a pressing mold, press the wax mold;
- (2) Use rapid prototyping to directly produce the pressed mold, such as the polymer/metal composite material developed by Huazhong University of Science and Technology, which is formed by selective laser sintering, and the parts can be directly processed after surface treatment. As an investment mold, it greatly simplifies the steps of small batch production of castings.
2.Plaster type and ceramic type precision casting
Gypsum mold and ceramic mold casting have the advantages of high precision and low surface roughness value. There are many ways to use rapid prototyping to obtain cast ceramic or plaster molds:
- (1) Use prototypes made by LOM, SLA, SLS, and 3DP as master molds, and directly turn them into ceramic or plaster molds. For those with complex shapes and difficult to draft The parts can be converted into silicone rubber type first. This method is characterized by low cost and can realize small batch production, but this method is not suitable for parts with complex shapes and cannot be drawn;
- (2) Similar to the method of investment casting, use SLS, SLA, 3DP or FDM makes wax molds, which are lost after melting or burning.
3.Sand Casting
Traditional sand casting generally requires the manufacture of wooden molds first, and the manual method of making wooden molds is often difficult to fully meet the requirements in terms of technology, production cycle, precision and material. The LOM model obtained by rapid prototyping can be directly used in casting production instead of wooden molds. Due to the special treatment, the paper mold is as hard as hardwood, and the surface is smooth, which is good for sand casting. It works below 200°C and can reproduce 50 to 200 sand molds.
Its advantages are low cost, fast manufacturing speed, high-precision patterns can be made in a short time without high-level wood molders and corresponding woodworking machinery, and its advantages are particularly prominent for large and medium-sized castings with complex shapes. Such as engine block, cylinder head, intake (exhaust) air pipe and chassis transmission clutch housing, etc. can be manufactured by this method. The replacement of wood molds by paper molds or resin molds greatly reduces the manufacturing cycle and cost of metal mold blanks, and the improvement of precision can reduce machining allowances and processing costs.
SLS sintered coated sand can be used to directly form sand molds (cores) for casting. This method is economical and fast, especially for castings with particularly complex inner cavity runners, which have advantages that other methods cannot match.
Please keep the source and address of this article for reprinting: The Rapid Manufacturing Of Complex Castings
Minghe Die Casting Company are dedicated to manufacture and provide quality and high performance Casting Parts(metal die casting parts range mainly include Thin-Wall Die Casting,Hot Chamber Die Casting,Cold Chamber Die Casting),Round Service(Die Casting Service,Cnc Machining,Mold Making,Surface Treatment).Any custom Aluminum die casting, magnesium or Zamak/zinc die casting and other castings requirements are welcome to contact us.
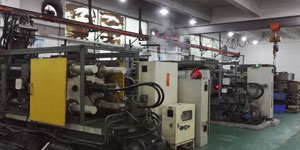
Under the control of ISO9001 and TS 16949,All processes are carried out through hundreds of advanced die casting machines, 5-axis machines, and other facilities, ranging from blasters to Ultra Sonic washing machines.Minghe not only has advanced equipment but also have professional team of experienced engineers,operators and inspectors to make the customer’s design come true.
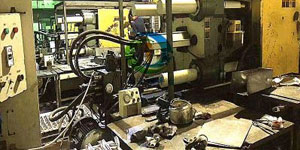
Contract manufacturer of die castings. Capabilities include cold chamber aluminum die casting parts from 0.15 lbs. to 6 lbs., quick change set up, and machining. Value-added services include polishing, vibrating, deburring, shot blasting, painting, plating, coating, assembly, and tooling. Materials worked with include alloys such as 360, 380, 383, and 413.
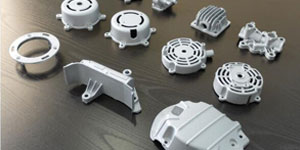
Zinc die casting design assistance/concurrent engineering services. Custom manufacturer of precision zinc die castings. Miniature castings, high pressure die castings, multi-slide mold castings, conventional mold castings, unit die and independent die castings and cavity sealed castings can be manufactured. Castings can be manufactured in lengths and widths up to 24 in. in +/-0.0005 in. tolerance.
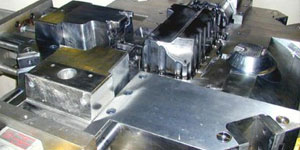
ISO 9001: 2015 certified manufacturer of die cast magnesium, Capabilities include high-pressure magnesium die casting up to 200 ton hot chamber & 3000 ton cold chamber, tooling design, polishing, molding, machining, powder & liquid painting, full QA with CMM capabilities, assembly, packaging & delivery.
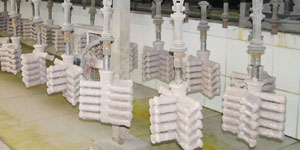
ITAF16949 certified. Additional Casting Service Include investment casting,sand casting,Gravity Casting, Lost Foam Casting,Centrifugal Casting,Vacuum Casting,Permanent Mold Casting,.Capabilities include EDI, engineering assistance, solid modeling and secondary processing.
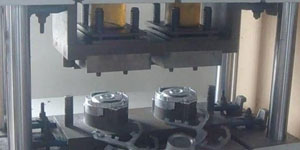
Casting Industries Parts Case Studies for: Cars, Bikes, Aircraft, Musical instruments, Watercraft, Optical devices, Sensors, Models, Electronic devices, Enclosures, Clocks, Machinery, Engines, Furniture, Jewelry, Jigs, Telecom, Lighting, Medical devices, Photographic devices, Robots, Sculptures, Sound equipment, Sporting equipment, Tooling, Toys and more.
What Can we help you do next?
∇ Go To Homepage For Die Casting China
→Casting Parts-Find out what we have done.
→Ralated Tips About Die Casting Services
By Minghe Die Casting Manufacturer |Categories: Helpful Articles |Material Tags: Aluminum Casting, Zinc Casting, Magnesium Casting, Titanium Casting, Stainless Steel Casting, Brass Casting,Bronze Casting,Casting Video,Company History,Aluminum Die Casting |Comments Off