The relationship between iron cost reduction and blast furnace production
In the increasingly fierce competition and the current difficult steel market situation, cost reduction can be described as "an inch of gold". Whoever has stronger cost control means has more room for survival and development.
With the recent increase in steel prices, various steel plants will resume production, the operating rate of blast furnaces will also rise further, the demand for iron ore will increase, and the price of iron ore will rise. With reference to past data, the price of iron ore is relatively elastic. Therefore, the current profit improvement situation for steel mills due to rising steel prices and lagging ore prices will not last forever, and problems in subsequent production organizations will gradually be exposed. Therefore, reducing costs is a long-term continuous process, and it is also a need for steel companies to respond to market changes.
The cost of pig iron accounts for 70-80% of the cost of steel production, which is the key to improving cost control. In other words, the cost of molten iron directly determines the cost of steel. So, how do we organize to reduce costs while ensuring the stability of the production system? Combine Longgang's production status to talk about our thoughts and practices.
Establishing blast furnace direct production is the biggest cost
Blast furnace operation is a complex process, which is affected by all aspects such as raw materials, equipment, operation level, management level, and peripheral guarantees. The stable, efficient and low-cost operation of the blast furnace is inseparable from the guarantee of coke, pellets, lump ore procurement, sintering production organization, power energy and other links. Under Longgang's existing management system, all links are closely organized around the stable and smooth blast furnace organization produce.
The core of blast furnace anterograde is to ensure the lower liquid permeability and upper air permeability. To improve the lower liquid permeability and upper gas permeability, it is necessary to make a fuss about the quality of the raw fuel and the operation. The composition and metallurgical properties of the raw fuel must be "stable", and the higher the degree of stability, the better. The content and load of harmful elements in the furnace must be "strictly controlled" and "knowledgeable" so that the blast furnace can take effective measures in time.
Blast furnace operations must be flexible. For companies like Longgang that rely on outsourced raw materials to maintain production, the supply of raw materials and fuels is extremely unbalanced. Basically, what do you have to eat? The difficulty of adjusting blast furnace operations is greatly increased. At present, it has basically achieved what kind of raw materials and fuels are available, and the furnace condition management concept of what kind of operation is matched, eliminating the previous "big unified" or "long-term unchanging" extensive management. The energy of blast furnace management is mainly focused on solving the problems that affect the smooth movement of the blast furnace. It is not only to ensure the safe and smooth implementation of the production organization, but also the key to ensuring the continuous reduction of pig iron costs.
Insist on the concentrate and not relax
Restricted by sintering and ore blending resources, Longgang seldom does sinter cup test. Basically, it is equipped with whatever ore is available. As a result, the sintering process has long-term unreasonable ore blending, unstable quality, poor physical quality of sintered ore, and under the blast furnace tank. The foaming rate is high.
In 2016, led by the technical team of the iron smelter, it integrated the charge optimization group, the raw material operation area, the pipe group and the technical strength of the ironmaking and sintering process, and built a pre-iron raw material management platform. The entire pre-iron system started services around the blast furnace. For example, the technical team and the charge optimization team will move the service forward, requiring all-day mastering of incoming materials, ingredients and yard change information, focusing on tracking changes in coke, injection coal and other coal blending, accurately predicting composition changes, and sending quality fluctuations to the blast furnace in advance The early warning information minimizes the negative impact of changes in raw materials and fuels on the stability of the blast furnace, and continuously explores the management and operation methods of "economic materials" and "fine pipes" to lay the foundation for the long-term stability of the blast furnace.
Economical and reasonable ingredients
The prerequisite for economical ingredients is scientific and reasonable ingredients, and we have a good understanding of the characteristics of all raw materials and fuels purchased in order to maximize our strengths and avoid weaknesses. The production organization of ironmaking must strengthen communication and coordination with various units before iron, and formulate a reasonable raw material procurement plan. In the implementation of sintering batching, not only must the efficiency and quality of the batching work be improved, and the cost of sintering must be reduced, but also Consider the control of various harmful elements; it is necessary to make the quality of sintered ore more stable, with better indicators, but also to make the overall cost of sintering lower, and to make the blast furnace "eat better".
The reasonable charge structure of the blast furnace is aimed at achieving the best economic benefits for ironmaking. To increase the clinker rate, it is necessary to use less or no lump ore. However, the unit price of lump ore is lower and has cost advantages, but it has different ingredients. Stable, poor metallurgical properties, poor particle size composition, disadvantages of blast furnace smelting.
At present, Longgang has established a charge optimization team mainly composed of key technicians to strengthen communication with the procurement department. According to the quality of raw materials, prices, resources, harmful elements, scientific ingredients, and careful calculations, the calculation is carried out first. Stacking, through reasonable calculation and guide the actual cost with theoretical cost, so that the ingredients and materials are well known in the process. At the same time, select the charge structure under current conditions according to the production status of the blast furnace. While optimizing the charge structure, the unfavorable factors affecting the blast furnace must be gradually solved (mainly the control of the load of harmful elements into the furnace). The optimization team also actively communicated with other advanced enterprises to make up for shortcomings, improve the batching procedures, and basically form its own set of batching optimization and cost calculation models.
However, we still have problems in the selection of the blast furnace charge structure. The proportion of lump ore basically reaches 15-20%, with no or only 3-5% pellets. The main problem faced is how to select sinter, pellets and sinters reasonably in the case of poor metallurgical properties of sintered ore (the low-temperature reduction pulverization index (+3.15mm) averaged 53.97 and 61.64% respectively in February and March 2016). The proportion of lump ore still needs us to constantly explore and summarize.
Optimize the sintering process to improve the quality of sintered ore
Sintered ore accounts for 75-80% of the total raw materials of the blast furnace. The composition, strength, particle size composition and metallurgical properties of the sintered ore directly affect the stability of the blast furnace. The high temperature of the sinter and the droplet performance play a vital role in the stability of blast furnace smelting.
From January to March 2016, the metallurgical properties of Longgang's sintered ore were poor. The worst-case low-temperature reduction pulverization index (+3.15mm) was only 44.56%, which caused great damage to the production of the blast furnace, and the pressure was uncomfortable for a long time. Only low-intensity operation can be guaranteed. Now, we have realized the importance of the quality of sinter, and have conducted in-depth research on sintering production technology and optimization of ore blending, based on improving the metallurgical properties of sinter, actively exploring the main factors affecting the high-temperature performance of sinter, and strengthening economic ore to influence blast furnaces. In the research of stable production, more than 10 furnaces have been organized for sinter reduction test and low-temperature pulverization test, which provides technical guarantee for the large-scale use of economic ore, stable sinter quality, blast furnace indicators and costs.
Favorable conditions must be created for low-cost operation of blast furnaces
Focusing on the reduction of the furnace grade and the large amount of low-cost raw materials entering the sintering and blast furnace, it will bring many disadvantages to the blast furnace. The production organization must plan ahead to ensure the minimum reserve of production materials, and scientifically formulate multiple sets of technical and operational guarantee programs. Refined fuel management should deal with the incompatibility of the blast furnace caused by the adjustment of the blended material structure, and ensure that both low-priced ore into the furnace can be achieved, and the goal of ensuring the smooth blast furnace can be ensured.
With the current overcapacity of pig iron, the high-intensity smelting and high-yield production organization of Longgang's 2000m3 blast furnace is no longer suitable for market requirements. The output of the blast furnace should be adjusted appropriately and explore ways to stabilize production and reduce fuel ratio under different raw material and fuel conditions. The operation method continues the long-term and stable good momentum of the blast furnace.
At this stage, the blast furnace needs to support high-quality coke to increase the coal injection ratio and reduce the coke ratio. Under the current situation of unstable raw fuel supply and unstable quality of Longgang, it is necessary to improve the quality of coke, improve the thermal index, and reduce the blast furnace Long-term stable and smooth travel is placed on the same position as cost reduction, creating favorable conditions for reducing the cost of the iron front system.
The professional training leader is unremitting
At present, the pressure on environmental protection, resources, cost, and manpower surplus of the former system of Long Steel is increasing, and at the same time, it faces the difficulties of lack of reserve talents and slow growth of young backbones. Now that we have realized the shortcomings in talent training, we should make short-, medium-, and long-term plans. The more difficult and difficult the period is, the more we must step up the training of talents. In the Shaanxi Iron and Steel Ironmaking Technology Training Course organized on March 20-25, the teachers explained the details, covered comprehensive content, deeply cut into the key points, and communicated with the actual situation of Longgang. The whole process benefited a lot and was well received by the students.
At the same time, the branch plant organizes training from time to time. All training focuses on meeting production needs and solving practical problems. The learning requirements of the operators are regularly collected, and the training materials are organized according to the learning requirements, so that the trainers must understand, learn, and remember. live. Each major organizes on-site practical training every quarter, explaining and operating at the same time, combining theory with practice, and improving the training effect.
Conclusion
- The iron front system must pay close attention to the corresponding relationship between stable blast furnace production and cost reduction, firmly establish the "red line" awareness of the production organization of the iron front system, and take effective measures to promote stable blast furnace production and continuous cost reduction. At the same time, pay attention to process and equipment accidents, carefully analyze the causes of the accidents, and quickly formulate plans to ensure the stable operation of the blast furnace.
- For a long time, the Longgang Ironmaking Plant has always faced the difficulties of large differences in the quality of raw materials and fuels, tight supply, and complex logistics balance, which have brought great challenges to the stability of ironmaking production. In the face of unfavorable factors, we closely focused on the goal of "optimizing the cost of molten iron", carried out in-depth "four-level cost accounting", participated in cost management for all employees, comprehensively and throughout the process, and continued to promote the "five modernizations", which basically achieved Clean, stable, low-consumption and low-cost production of the iron front system.
Please keep the source and address of this article for reprinting:The relationship between iron cost reduction and blast furnace production
Minghe Die Casting Company are dedicated to manufacture and provide quality and high performance Casting Parts(metal die casting parts range mainly include Thin-Wall Die Casting,Hot Chamber Die Casting,Cold Chamber Die Casting),Round Service(Die Casting Service,Cnc Machining,Mold Making,Surface Treatment).Any custom Aluminum die casting, magnesium or Zamak/zinc die casting and other castings requirements are welcome to contact us.
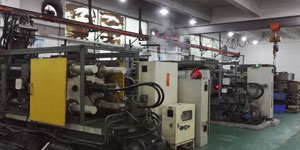
Under the control of ISO9001 and TS 16949,All processes are carried out through hundreds of advanced die casting machines, 5-axis machines, and other facilities, ranging from blasters to Ultra Sonic washing machines.Minghe not only has advanced equipment but also have professional team of experienced engineers,operators and inspectors to make the customer’s design come true.
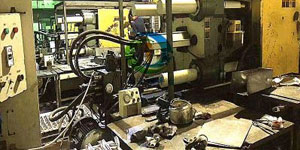
Contract manufacturer of die castings. Capabilities include cold chamber aluminum die casting parts from 0.15 lbs. to 6 lbs., quick change set up, and machining. Value-added services include polishing, vibrating, deburring, shot blasting, painting, plating, coating, assembly, and tooling. Materials worked with include alloys such as 360, 380, 383, and 413.
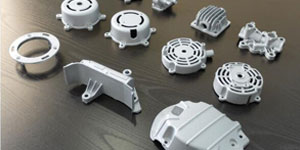
Zinc die casting design assistance/concurrent engineering services. Custom manufacturer of precision zinc die castings. Miniature castings, high pressure die castings, multi-slide mold castings, conventional mold castings, unit die and independent die castings and cavity sealed castings can be manufactured. Castings can be manufactured in lengths and widths up to 24 in. in +/-0.0005 in. tolerance.
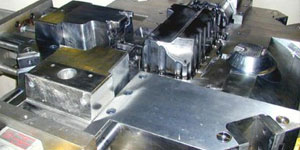
ISO 9001: 2015 certified manufacturer of die cast magnesium, Capabilities include high-pressure magnesium die casting up to 200 ton hot chamber & 3000 ton cold chamber, tooling design, polishing, molding, machining, powder & liquid painting, full QA with CMM capabilities, assembly, packaging & delivery.
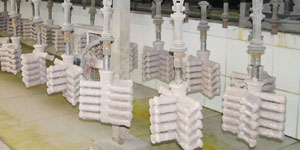
ITAF16949 certified. Additional Casting Service Include investment casting,sand casting,Gravity Casting, Lost Foam Casting,Centrifugal Casting,Vacuum Casting,Permanent Mold Casting,.Capabilities include EDI, engineering assistance, solid modeling and secondary processing.
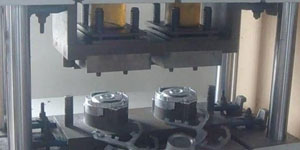
Casting Industries Parts Case Studies for: Cars, Bikes, Aircraft, Musical instruments, Watercraft, Optical devices, Sensors, Models, Electronic devices, Enclosures, Clocks, Machinery, Engines, Furniture, Jewelry, Jigs, Telecom, Lighting, Medical devices, Photographic devices, Robots, Sculptures, Sound equipment, Sporting equipment, Tooling, Toys and more.
What Can we help you do next?
∇ Go To Homepage For Die Casting China
→Casting Parts-Find out what we have done.
→Ralated Tips About Die Casting Services
By Minghe Die Casting Manufacturer |Categories: Helpful Articles |Material Tags: Aluminum Casting, Zinc Casting, Magnesium Casting, Titanium Casting, Stainless Steel Casting, Brass Casting,Bronze Casting,Casting Video,Company History,Aluminum Die Casting |Comments Off