The Relationship Between Sticky Mold Problem And Mold Release Agent
Sticking is the high-pressure and high-speed repeated impact of the filling metal liquid, which causes a chemical reaction between the surface of the mold steel and the casting alloy, and a chemical reaction layer is formed on the surface of the mold, which leads to the phenomenon of sticking of the casting. Generally, the most serious mold sticking is the core.
When the die-casting parts stick to the mold, the lighter surface is rough, which affects the roughness of the appearance; the heavyer surface peels, lacks meat, strains, tears, and even causes the casting to leak. The formation and expansion of the sticky mold not only reduces the surface quality and dimensional accuracy of the casting, destroys the dense layer of the mold surface, especially the runner position of the mold, but also increases the man-hours and costs for mold repair, and even leads to casting waste and early mold failure.
The state of the contact surface between the molten metal and the mold under high temperature and high pressure is very complicated. Although people's research on the sticking problem in die casting is gradually moving from the macro surface to the micro surface, from qualitative analysis to the establishment of mathematical model analysis, from single factor research to multiple factors Comprehensive research develops from static research to dynamic research, but most of them still stay on intuitive qualitative analysis. According to the specific conditions of the sticky mold, some factors that affect its formation and expansion are summarized, and some preventive measures are taken accordingly. At present, the consensus is that: die casting process parameters, mold design, mold temperature, mold surface quality, filling temperature, chemical composition and quality of mold release agent, spraying process, etc., all have an important impact on mold sticking, rather than sticking. The mold is simply linked to the release agent intuitively. However, the quality and use method of the release agent is indeed inextricably linked with the die-casting sticky mold. For die-casting workers, understanding and knowing the relationship between them, knowing yourself and the enemy, can control the die-casting process more accurately.
The release agent itself is a chemical product, and it is a different field of knowledge from metal materials and molding processes. However, cross-disciplinary crossover has always been the inevitable orientation of innovation and development. The author tries to focus on "what force produces sticky mold? What factors are mainly affected by sticky mold How to prevent?” and other issues are analyzed and summarized. On this basis, take aluminum alloy die-casting as an example, and then talk about the relationship between mold release agent and die-casting mold.
The Physicochemical Properties Of Sticky Mold
Sticky mold theory is a comprehensive theory based on metal science, chemistry and mechanics. Fundamentally, the sticking mold is the physical and chemical interaction between the molecules or atoms of the interface material between the casting and the mold, the most important of which is the adhesion.
Aluminum, zinc, magnesium, copper and other die-cast metal materials and mold materials have a polycrystalline structure, and surface molecules have greater potential energy than internal molecules, that is, surface energy. They all have the instinct that tends to the lowest surface energy, that is, the instinct to drive the arrangement of atoms on the free surface to balance. If the two metal surfaces are very close to each other, in order to reduce the surface energy, the lattices between each other will be combined, causing adhesion. As we all know, there is gravitational force between solids in contact with each other. The gravitational force is formed by metal bond, covalent bond and ionic bond, which belongs to short-range bond force. There is also the long-range Von Der Wools Force (Von Der Wools Force). When the contact distance is a few nanometers, all van der Waals forces work. Within 1 nanometer, various short-range forces come into play. To estimate the strength of the adhesion bond, first determine the cohesion of the metal, and then calculate the surface force of the contact surface. However, due to the complex electronic structure of metals, it is not possible to theoretically solve the cohesive strength at present.
From the perspective of phenomenon, the sticking is nothing more than a chemical combination or a mechanical occlusion. The main factors related to the adhesion strength are: the type of metal, the mutual solubility of the metal, the orientation of the crystal lattice, the way of elastoplastic deformation during contact, elastic recovery, segregation and oxidation, dislocation and microcracking, contact temperature, etc. The surface hardening of the mold itself, surface roughness, contact pressure, etc. are also important factors. The bonding ability of different atoms is different, and the alloys of different compositions show different sticking tendencies. Therefore, choosing the appropriate mold material and mold release agent formula can minimize the adhesion between the casting and the mold.
The Causes Of Aluminum Sticking In Die Casting Molds
Adhesive aluminum itself is a chemical diffusion reaction between metals.
1) Chemical Composition
The greater the affinity between die-casting alloy and die steel, the easier it is to melt and bond with each other. When the iron content in the aluminum alloy is less than 0.7%, the iron atoms on the surface of the mold can penetrate into the aluminum liquid faster due to the concentration gradient, and it is easy to form iron-aluminum or iron-aluminum-silicon intermetallic compounds and stick to the mold. Obviously, the sticking tendency of pure aluminum is the most serious, while the sticking tendency of eutectic aluminum-silicon alloy commonly used in die casting is smaller. Nickel has the effect of promoting the growth of intermetallic compounds, and the inclusions in the aluminum liquid and chromium and nickel may increase the chance of aluminum adhesion. High silicon and increased manganese can slow down the growth rate of the intermediate metal phase and reduce mold sticking. A small amount of strontium (0.004%) and titanium (0.125%) can also reduce aluminum adhesion.
In short, strictly control the alloy composition within a reasonable range, and adhere to the cleanliness of the aluminum alloy liquid, which is the basis for avoiding mold sticking.
2) Mold Material
Mold materials accounted for about 10% of the total cost of molds. In the 1950s, 3Cr2W8V hot-worked mold steel imported from the former Soviet Union was widely used in China. When die-casting 10,000 to 20,000 molds, hairline cracks began to appear in the cavity, and the mold was not sticky. avoid. In the 1990s, the excellent steel grade H13 was introduced from the United States. As an air-cooled hardening hot work die steel with both toughness and toughness, its life span can reach 15 to 200,000 die times. A variety of similar steel grades have been extended using this steel grade as the matrix, such as: Japan SKD61 of (JIS); STD61 of South Korea (KS); BH13 of Britain (BS), etc. If the quality of the selected mold material is low, its hardenability, toughness, wear resistance, heat treatment stability are poor, the mold hardness is insufficient, the mold surface is squeezed by the die-casting alloy during demolding, or the core is bent and deformed, which increases the mold pairing The mold release resistance of castings is easy to cause defects such as mold surface cracks and welding due to congenital defects, which directly lead to mold sticking. The mold sticking part of the casting often presents drawing marks such as rough surface, peeling or lack of material. In the case of severe adhesion, the casting will be torn and damaged. The surface of the mold cavity will adhere to a laminate casting alloy, and the color will be white, as shown in the picture.
The reason why sticking easily occurs at the hot spot of the mold or directly opposite the gate is that the intermetallic compound layer is easy to form here, and the formed intermetallic compound layer Al4FeSi and the H13 mold have a strong bonding strength. The thin intermetallic compound layer formed is caused by the high-speed melt repeatedly scouring the surface of the mold during filling, causing the intermetallic compound layer to peel off from the surface of the mold. The wear-resistant material Cr23C6 can effectively prevent the chemical impact of the aluminum alloy melt and reduce the loss of mold materials and the occurrence of mold sticking.
3) Mold Design
When the die-casting operation process is normal, but a new mold sticks to the mold, debugging the die-casting process and spraying can be remedied, but if it is unstable, it means that the main reason is the problem of the casting structure design, mold design or manufacturing.
The first is the internal gate design, such as improper control of flow direction, cross-sectional area, injection speed, etc., the molten metal directly erodes the core or wall, which is most prone to mold sticking. If it hits the side of the fixed mold, the packing force of the casting on the side of the fixed mold will increase. When the overall or partial shrinkage of the casting has an unbalanced and reasonable distribution of the clamping force of the mold, the casting will appear deviated, skewed, inclined, deformed, cracked, broken due to the sticking of the mold, and even stick to the fixed mold, or stick to the top of the movable mold. . If the demolding slope of the fixed mold cavity or the core forming surface is too small or has a reverse slope, the casting resistance will increase, causing scratches during core pulling and part removal. In addition, the mold design is not rigid enough to lose the accuracy it should be prematurely; the mold surface finish and surface strengthening treatment are lacking; the cooling system design on the moving and fixed molds is unreasonable, which makes the mold working temperature unbalanced and stable; there are hot nodes, etc. Lead to sticky mold.
4) Mold Processing
The frictional heat generated during the grinding process of the mold will cause grinding cracks on the surface. The presence of grinding stress will also reduce the thermal fatigue resistance of the mold. The surface of the mold cavity, especially the rough surface of the runner or the place with a small amount of scratches and scribe marks on the mold surface, are potential sources of cracks. The local high temperature of EDM finish machining forms the tempered zone under the surface. The structure and chemical composition of this zone are different from that of the matrix. The hardness of this zone is high. In addition to the existence of residual stress on the surface, the polishing treatment may not be in place, and it may form micro cracks in the early use of the mold. Lead to sticky mold.
5) Die Casting Process
If the filling temperature of the alloy liquid is too high, the diffusion and reaction of iron will be accelerated. The more easily the lubricating film will be destroyed, the easier the mold surface will be annealed, and it will be more susceptible to erosion and aluminum adhesion. If the injection speed and pressure are too high, the mold temperature is too high, and the mold hardness is low, melting, welding adhesion and mold sticking will easily occur.
6) Release Agent
The primary function of the release agent is to protect the mold and form a firm lubricating film to reduce the thermal impact of high-speed molten aluminum on the mold.
Inferior mold release agents do not have the function of protecting the mold, because its chemical composition determines that it is impossible to quickly form a lubricating film that is firm, smooth, heat-retaining, less gassing, no residue, and conducive to the flow of alloy liquid within the mold temperature range required by the process. No matter how the spraying process is adjusted, its essential characteristics cannot be changed, so the hidden danger of mold sticking is inevitable.
The Ways To Solve The Sticking Mold Problem
The problem of mold sticking is a comprehensive reaction of many factors. Therefore, to solve the problem of sticking mold, we must analyze and judge from multiple angles, allowing trial and error, but do not make subjective judgments. The following items summarized by the author are purely empirical skills based on the black box theory, that is, the mold is regarded as a black box, and the internal changes of the filling process are not investigated, and only the two ends of the black box are input parameters and molding effects. To solve the sticky mode fundamentally, it needs the guidance of in-depth micro-theoretical research results, and it has a long way to go.
- Check the factors that affect the gate speed: punch speed, punch size, specific pressure, gate size, reduce the gate speed as much as possible or adjust the gate direction to contact the cavity surface at a smaller angle to avoid contact angle Close to 180 degrees to reduce erosion to the cavity and avoid impact to the core. Reduce the filling time to narrow the window of thermal shock.
- Adjust the mold cooling channel, especially the hot node and core easy to stick to the mold, add a cooler if necessary. Add a second spray or insert high thermal conductivity mold material in the sticking part to reduce the mold temperature of the sticking part and achieve a stable and balanced mold temperature.
- In the smallest ejection area of the casting, high filling pressure may promote mold sticking. Under the premise of satisfying the quality of castings, reduce the filling pressure as much as possible. Both static pressure and pressurization are important. At the same time, the pressure adjustment should be calculated and adjusted according to the PQ2 diagram.
- High mold temperature and pouring temperature will increase the tendency of mold sticking. When there are several factors that affect mold sticking, lowering the mold temperature or pouring temperature is the best way to correct it.
- High-strength special materials, such as Mo-785, Ti-6AI-4V and Anviloy 1150, can be used where mold sticking is likely to occur. Various mold surface treatment methods can significantly reduce mold sticking. Such as nitriding and carbonitriding treatment, physical vapor deposition dense layer such as {TiAl}N and CrC and aluminum film, etc., strengthening treatment of mold surface, mold coating ---CVD, PVD, TD, etc. The existing sticky mold needs to be eliminated as soon as possible. If it is allowed to develop, more and more difficulties and repetitions will appear.
- Use high-quality mold release agents with high film-forming heat resistance temperature, strong mold quality and good lubricating effect. Apply mold paste when trying out new molds to prevent strain. For high temperature areas where molds are easy to stick, anti-stick wax paste can be applied regularly or partially sprayed with anti-stick wax liquid.
- Carefully monitor the mold ejection angle, and its maximum allowable value should be in accordance with the die casting mold standard.
- The composition design of die-casting alloy should take into account the factors that may cause mold sticking. For example, within the allowable range, it is advisable to control the iron content in the aluminum alloy to not less than 0.7%. It is necessary to prevent mold sticking caused by mixing with low melting point metals. When using a master alloy to adjust the chemical composition, in addition to individual metals such as magnesium and zinc, pure metals cannot be added to the aluminum liquid to prevent severe segregation from causing mold sticking.The purified alloy liquid has good fluidity and can expand the process window for avoiding mold sticking.
- The greater the shrinkage of the die-casting alloy, the easier it is to stick to the mold and the worse the high-temperature strength. Some alloys have a larger shrinkage rate. The wider the liquid and solid temperature range of the alloy, the greater the shrinkage of the alloy. According to the structural shape and complexity of the casting, if the sticking and deformation caused by shrinkage are difficult to eliminate, it is necessary to consider switching to an alloy with low volume shrinkage and linear shrinkage and high high temperature strength; or adjust the alloy composition (such as aluminum silicon When the silicon content in the alloy increases, the shrinkage rate of the casting becomes smaller) reduce its shrinkage rate; or modify the alloy, such as adding 0.15% to 0.2% of titanium and other grain refiners to the aluminum alloy liquid to reduce The tendency of alloys to shrink.
The Relationship Between Mold Release Agent And Sticky Mold
Die casting is a dynamic thermodynamic process. Alloys such as aluminum and zinc have a strong tendency to adhere to the surface of the cavity. The sprayed release agent can act as a parting agent between the cavity and the liquid metal to prevent the metal from adhering to the surface of the cavity. Careful selection of release agent (composition, conjunctival temperature, air volume, residue, conjunctival strength, influence on subsequent surface coating, etc.) and reasonable operation technology (release agent concentration, mold temperature distribution, atomization process, spraying Time and distance, etc.) are important factors to prevent mold sticking.
For more than half a century, with the advancement of die-casting technology, mold release agents have also improved accordingly. These improvements include release agent composition, film formation, temperature resistance, lubricity, prevention of mold sticking and welding, and compliance with environmental protection requirements, which is harmless and safe to the body. From the early oil + graphite coatings to water-based coatings, from ordinary oil-based soap emulsion series to the currently widely used modified silicone oil series of water-based release agents, anhydrous concentrated release agents (for micro-spraying) , And develop towards reactive semi-permanent coatings and powder inorganic coatings. But so far, there has not been a release agent that can provide all possible properties without limitations or disadvantages. Semi-permanent paint has been tested for zinc alloy die-casting. It is chemically connected to the surface of the mold. The coating is stable at 698ºC, but it is easy to wear off, so it is necessary to try to extend its durability. For the die casting of aluminum and magnesium alloys, it is mainly how to improve the thermal stability of the coating. From the perspective of environmental protection and safety, consideration should also be given to reducing or eliminating harmful solvents. In recent years, a lot of research work has been directed to semi-permanent molds and permanent molds. By developing new coatings, overcoming welding and sticking, and finally abandoning mold release agents, this is a disruptive innovation. However, the results obtained so far cannot be used in industrial applications. The main problems are the durability of the coating, the coating method and the price.
In the foreseeable future, the development and research of various release agents will still be indispensable. There is considerable contact pressure between the molding surface of the die-casting part and the mold surface. The casting part is subjected to three-way non-uniformly distributed compressive stress during die-casting. Therefore, the lubricating film formed by spraying release agent is easy to rupture, and high temperature also causes chemical changes in the lubricating film. . During the second extrusion, a small amount of new metal surface will appear. The new surface has different physical and chemical properties from the original metal surface. There is no lubricant protection, and it is easy to adhere to the mold and cause the mold to wear. At the same time, the additional stress and residual stress caused by the uneven distribution of the internal deformation of the casting also increase the difficulty of taking the part until the mold is stuck.
For the mold, due to the change of the die-casting process and the temperature field of the mold, the forming process is a kind of intermittent and unstable friction, and different parts of the mold are different. The lubrication mechanism in this state cannot be analyzed and described by the Coulomb friction theorem in general physics. Experts at home and abroad have successively put forward the theory of mechanical-molecular friction, adhesion-ligou friction theory, boundary friction, mixed friction, elastic viscous friction theory, etc., while studying lubricants with various complex chemical compositions.
Graphite release agents used to reduce aluminum sticking to molds are no longer used due to environmental impact. The mechanism of the release agent is to form a protective film between the casting and the mold, while preventing the aluminum alloy liquid from directly contacting the mold surface. This requires the release agent to have sufficient strength to withstand the separation and impact of the aluminum alloy liquid. The temperature of the mold surface is generally controlled at 35% to 45% of the alloy casting temperature, so that the release agent can be fully absorbed on the mold surface and protect the mold. The mold near the gate and deep grooves are prone to aluminum sticking. The shape of the mold surface where aluminum alloy sticking occurs is shown in the figure. The initial diameter of these small irregular pits is about 0.6 microns, and eventually they gradually develop into small pits with a diameter of 3.6 microns. As the tendency to form a sticky mold increases, the diameter of these small pits can reach 15 µm, and eventually cracks are formed. These small pits and cracks are eventually filled with aluminum, and mechanical bonding may also occur.
The role of the release agent is to separate the surface of the mold and the die casting, reduce the damage of the mold, make the surface of the casting smooth, and at the same time play a role in cooling, adjusting and controlling the mold. The release agent and the mold surface can produce non-polar or polar physical adsorption film, chemical adsorption film and chemical reaction film. When there are no polar molecules in the release agent, the release agent can only produce a non-polar physical adsorption film on the mold surface; otherwise, it can produce a polar physical adsorption film. The strength of the latter is greater than that of the non-polar physical adsorption membrane. When the atoms in the mold release agent component and the atoms on the mold surface share common electrons, a chemical adsorption film will be produced on the mold surface. Its strength is higher than the polar physical adsorption film. Under a certain contact pressure and temperature, the extreme pressure agent in the release agent may also chemically react with the mold surface to produce a chemical reaction film. Its strength is greater than the chemical adsorption membrane. Generally speaking, the higher the strength of the adsorption film of the release agent, the better the effect of preventing sticking. Therefore, according to different die-casting parts, it is very important to choose the corresponding release agent to form a high-strength adsorption film.
The water-based release agent prepared with general mineral oil is a non-polar hydrocarbon organic compound (CnH2n+1). The formed film has weak adsorption force on the surface of the mold and the cohesion of the molecules themselves, and the film strength is very low. A water-based release agent prepared from animal and vegetable oils, such as fatty acids, fatty acid sodium soaps, acids (ROH), etc., with a non-polar hydrocarbon group at one end and a polar end at the other end. This molecule has a permanent dipole When in contact with the mold surface, the polar end attracts the mold surface, while the non-polar end faces outwards and is aligned on the metal surface. The layer of adsorbed molecules is only a few nanometers thick. When polarizing additives are added, it can Polymerization forms a solid film on the surface of the mold and at the same time strengthens the side adsorption force of the molecules. The strength and lubricity of this physical adsorption film is much higher than that of non-polar molecule physical adsorption film.
The physical adsorption film is very sensitive to temperature, and the polar molecules adsorbed on the surface of the mold are in a dynamic equilibrium state of continuous adsorption and desorption. The temperature rises, the desorption increases, the thickness of the adsorption film decreases, and the strength of the boundary adsorption film decreases, causing molecules to desorb, chaotic direction, and even melt the film, and vice versa. The physical adsorption film is only effective under low contact pressure and low temperature conditions, so this type of release agent can only work at low mold temperatures. Physical adsorption has no selectivity, while chemical adsorption has obvious selectivity, that is, a certain adsorbent can only adsorb certain substances. Therefore, different mold release agents should be selected according to the mold and die casting material, die casting process conditions (such as mold temperature, casting wall thickness, filling temperature, pressure, etc.) in order to obtain the desired effect.
The water-based release agent prepared with modified silicone oil high molecular polymer as the main body, its polar molecules are chemically combined with the surface of the mold, which belongs to the chemical adsorption formed by the combination of chemical bonding force and the surface. Therefore, the film has good heat resistance, high thermal stability, irreversible adsorption film, strong adhesion, and good release effect. Although the price is slightly higher, it has obvious advantages in preventing mold sticking for die casting that requires high mold temperature, high pressure, and large and thin-walled complex parts.
The spraying process is very important to prevent mold sticking. When the operator finds that the mold sticks, it is natural to reason that it is because the concentration is low or the dosage is small, and the film is too thin to resist the thermal stress and turbulent impact of the molten metal, and then spray more mold release agent on the sticky mold. The result is often local paint accumulation or residue, causing pores and complicating the problem. The correct method should be to apply a kind of anti-sticking paste---anti-sticking wax to the area where the sticking has occurred, and carry out special treatment. Anti-sticking wax is an easy-to-brush anti-welding ointment, which is prepared from semi-synthetic high-temperature raw materials. The effective component does not contain harmful substances. The high temperature resistant tungsten-based compound or molybdenum-based compound content in the paste can effectively avoid the interface effect of aluminum alloy and prevent mold sticking.
Mold temperature is an important factor that affects the adsorption effect of the release agent. Too low (below 150ºC), the mold temperature quickly drops below the vaporization point of water, the mold release agent cannot be deposited on the mold surface, but just rushes through the mold surface, and the carrier water is too late to vaporize, which may cause diffuse pores; mold temperature Too high (above 398ºC), the mold release agent is repelled by the vapor layer on the mold surface, and the adsorption capacity of the mold release agent is greatly reduced. Only when the wetting temperature required by the characteristics of the mold release agent is reached, can it really contact with the mold surface to form a compact The coating plays a role of isolation.
The spraying process also directly affects the adsorption effect. Generally, when the pressure of the spray pipe is 0.35-0.70bar higher than the pressure of the release agent (1.05bar may be required for large-area spraying), the atomization effect is good; for micro spraying and pulse spraying, the atomization effect is better. Is important. As for the spraying time, as short as 0.10-2.0 seconds is enough to form a sufficiently thick isolation film. The pulse spraying time is in this range, but because the release agent is currently used in large quantities to cool the cavity, it usually takes 5.0-120 seconds. Obviously, part of the release agent just flows through the surface of the mold and is wasted. With the advent of more complex and precise automatic spraying devices, the spraying angle and distance only need to be adjusted and fixed before production.
I think that for die-casting engineers who use mold release agents, the important thing is not to exhaust the professional knowledge of mold release agents and then choose them according to their own judgments, but to learn from the European and American die-casting industries and let manufacturers specialize in the production of mold release agents. According to the die-casting structure diagram provided by the die-casting manufacturer, the tonnage of the die-casting machine, the performance requirements of the castings and the post-treatment process requirements, the most suitable model of release agent and the method of use are recommended until satisfactory results are achieved. Because manufacturers who truly specialize in the production of mold release agents must know the performance characteristics of mold release agents best, and interact with them to get rid of blindness and maintain a virtuous cycle of production.
The Correctly Handle Mold Sticking
The core of die casting production is the quality of alloy smelting and molds. Among all the factors that prevent and deal with sticky molds, the choice of high-quality mold materials is the basis, mold design and processing and standardized heat treatment are the key, and timely and effective maintenance during use is the main way. When mold sticking occurs, the party who executes the die-casting process and the mold manufacturer often blame each other. This is understandable, because the factors that induce sticking are diverse, and it is difficult to make an accurate judgment for the time being. But in any case, the intrinsic property falls on the mold, so for molds that have been stuck, we should first analyze and deal with the mold itself.
- The surface polishing of the die-casting mold must meet the requirements. Thoroughly polish to remove the hard layer of EDM, and the surface should not be highly polished.
- Clean the aluminum sticking on the die-casting mold in time, and perform surface treatment and stress relief on the mold in time. If there is aluminum adhesion on the surface of the mold, and there are small bubbles on the surface, use emery cloth and oilstone to polish the surface and then repeatedly stick the mold. The better treatment method is to shot blast the mold surface of the sticking mold, or the mold in the sticking position On the surface, a mesh pattern with a width of 0.2-0.5 mm, a depth of 0.2-0.5 mm, and an interval of 2-5 mm can be produced, which can eliminate the defects of mold sticking on the surface of the casting.
- Try to minimize the temperature where the mold is easy to stick to aluminum.
- Use special materials with a higher melting point to perform surface treatment on the mold, and it can be glued to the position where the mold is stuck on the surface of the mold to avoid mold sticking. New materials such as molybdenum alloys, tungsten alloys, titanium alloys, special nitrides or low-temperature carbon and nitrogen compounds. The activation energy between aluminum and molybdenum is relatively high, so the use of molybdenum infiltration on the surface of the mold can effectively improve the anti-sticking performance.
- For new molds and molds that are prone to castings sticking to the fixed mold, the mold should be well prepared before die-casting.Preheat, heat the mold through a flame spray gun. It is not allowed to directly pour the alloy liquid into the mold for heating, and the preheating temperature is controlled at 180~220ºC. And before starting the low-speed injection, apply mold paste to the mold cavity and blow it evenly with compressed air. It is applied once per die-casting mold, and the test die-casting is about 20 molds, which is very effective to avoid straining the mold. If the mold is still stuck, it means there is a problem with the mold and the mold needs to be repaired
- When disassembling the movable part of the mold or the small core, only soft copper, aluminum, lead rods or rubber hammers are allowed to tap lightly to avoid damage to the cavity.
- After die-casting to a certain number of molds, the mold should be subjected to stress relief treatment on a regular basis.
There are many reasons for die-casting sticking, and the measures to solve sticking are also different. The reasons for sticking should be carefully observed and analyzed, and corresponding measures should be taken in a targeted manner. At present, the research on the formation mechanism of the sticking phenomenon is still in the qualitative analysis stage. Different alloy materials show different sticking tendencies; it is necessary to find more effective test methods and under the guidance of quantitative theoretical research results. , To carry out further experimental research.
With the continuous emergence of new materials and new process technologies, new ideas and new methods to solve the problem of mold sticking and even disruptive innovative technologies are impacting the existing traditional rules that rely on preventing sticking. For example, North American die casting is developing a self-developed The permanent mold with healing function and no release agent may cause the existing process technology to be overturned or eliminated in the future. Therefore, we need to continue to absorb advanced die-casting technology, while maintaining patience in scientific research, steady and steady, a new leap in China's die-casting is just around the corner.
Minghe Die Casting Company Is Custom manufacturer of precision & non-ferrous die castings. Products include aluminum & zinc die castings. Aluminum die castings are available in alloys including 380 & 383. Specifications include plus /- 0.0025 tolerances & maximum molding weight of 10 lbs. Zinc die casting parts are available in standard alloys such as Zamak no. 3, Zamak no. 5 & Zamak no. 7 & hybrid alloys such as ZA-8 & ZA-27. Specifications include plus /- 0.001 tolerances & maximum molding weight of 4.5 lbs.
Please keep the source and address of this article for reprinting: The Relationship Between Sticky Mold Problem And Mold Release Agent
Minghe Die Casting Company are dedicated to manufacture and provide quality and high performance Casting Parts(metal die casting parts range mainly include Thin-Wall Die Casting,Hot Chamber Die Casting,Cold Chamber Die Casting),Round Service(Die Casting Service,Cnc Machining,Mold Making,Surface Treatment).Any custom Aluminum die casting, magnesium or Zamak/zinc die casting and other castings requirements are welcome to contact us.
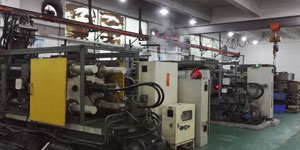
Under the control of ISO9001 and TS 16949,All processes are carried out through hundreds of advanced die casting machines, 5-axis machines, and other facilities, ranging from blasters to Ultra Sonic washing machines.Minghe not only has advanced equipment but also have professional team of experienced engineers,operators and inspectors to make the customer’s design come true.
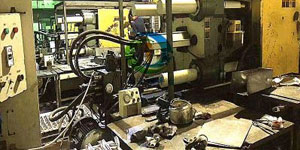
Contract manufacturer of die castings. Capabilities include cold chamber aluminum die casting parts from 0.15 lbs. to 6 lbs., quick change set up, and machining. Value-added services include polishing, vibrating, deburring, shot blasting, painting, plating, coating, assembly, and tooling. Materials worked with include alloys such as 360, 380, 383, and 413.
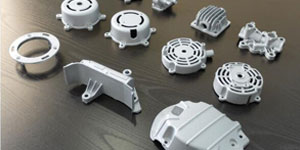
Zinc die casting design assistance/concurrent engineering services. Custom manufacturer of precision zinc die castings. Miniature castings, high pressure die castings, multi-slide mold castings, conventional mold castings, unit die and independent die castings and cavity sealed castings can be manufactured. Castings can be manufactured in lengths and widths up to 24 in. in +/-0.0005 in. tolerance.
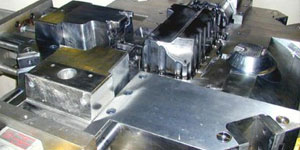
ISO 9001: 2015 certified manufacturer of die cast magnesium, Capabilities include high-pressure magnesium die casting up to 200 ton hot chamber & 3000 ton cold chamber, tooling design, polishing, molding, machining, powder & liquid painting, full QA with CMM capabilities, assembly, packaging & delivery.
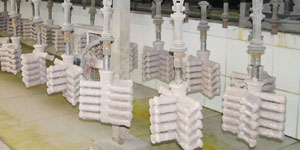
ITAF16949 certified. Additional Casting Service Include investment casting,sand casting,Gravity Casting, Lost Foam Casting,Centrifugal Casting,Vacuum Casting,Permanent Mold Casting,.Capabilities include EDI, engineering assistance, solid modeling and secondary processing.
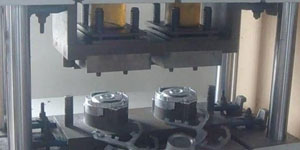
Casting Industries Parts Case Studies for: Cars, Bikes, Aircraft, Musical instruments, Watercraft, Optical devices, Sensors, Models, Electronic devices, Enclosures, Clocks, Machinery, Engines, Furniture, Jewelry, Jigs, Telecom, Lighting, Medical devices, Photographic devices, Robots, Sculptures, Sound equipment, Sporting equipment, Tooling, Toys and more.
What Can we help you do next?
∇ Go To Homepage For Die Casting China
→Casting Parts-Find out what we have done.
→Ralated Tips About Die Casting Services
By Minghe Die Casting Manufacturer |Categories: Helpful Articles |Material Tags: Aluminum Casting, Zinc Casting, Magnesium Casting, Titanium Casting, Stainless Steel Casting, Brass Casting,Bronze Casting,Casting Video,Company History,Aluminum Die Casting |Comments Off