The Research And Application Of Smelting Non-Fluoride Slagging
Fluorite is used as a slag-making agent in the steelmaking process. The calcium fluoride in the converter slag produced in the process will seriously corrode the furnace lining and package lining, and the large amount of fluoride ions produced by fluorite will pollute the ecological environment.
For a long time, the quality of the used ore and fluorite is unstable, which makes it difficult to slag, and the large amount of addition increases the consumption, and also aggravates the erosion of the furnace lining and the package lining and the pollution to the environment. Therefore, the research and development of non-fluorinated steelmaking technology has obvious social benefits. This article is aimed at the research and application of non-fluorinated semi-steel steelmaking process when Shougang Jingtang Iron and Steel United Co., Ltd. (hereinafter referred to as Shougang Jingtang) adopts the converter duplex process to smelt high-quality steel. Great economic benefits.
1 Test Conditions And Methods
Shougang Jingtang has 5 300t converters and adopts top-bottom composite blowing technology, including 2 dephosphorization converters and 3 decarburization converters. With the steady increase of semi-steel smelting output, all high-quality steels are basically semi-steel When smelting, decarburization converter smelting ultra-low-carbon steel, taking high-grade automobile sheet as an example, it requires tapping ω(C)=0.03%~0.06%, ω(P)<0.01%, ω(S)<0.01%, The tapping temperature is 1675~1705℃. The composition and temperature of the semi-steel entering the furnace are shown in Table 1. In order to optimize the production structure and production cost and make full use of the dephosphorization capacity of the decarburization furnace slag, part of the dephosphorization task has been transferred to the decarburization furnace, and the dephosphorization furnace is now produced The semi-steel is adjusted from the target ω(P)≤0.030% to ω(P)≤0.035%. In addition, the phosphorus content of Shougang Jingtang blast furnace hot metal is relatively stable, which provides a prerequisite for the stable production of fluorine-free steelmaking under the existing dual converter process conditions.
2 Smelting Process Optimization
2.1 Research on slag formation route and slag retention operation
According to the conditions required for slagging, industrial tests were carried out for the Shougang Jingtang fluorine-free slagging process in terms of slag retention operation, gun position control, slag auxiliary materials, and decarburization speed.
In the initial stage of semi-steel smelting, lime, light-burned dolomite and other slag-making materials are added. When cold lime is in contact with the remaining slag, the slag and lime are infiltrated, and the slag will penetrate into the pores and cracks on the lime surface. The diffusion rate of Fe2+ in the slag is greater than that of SiO44-, so Fe2+ will enter the lime block along the pores and cracks and form a CaO-FeO solid solution with low FeO content and a CaO-FeO liquid phase with high FeO content. This liquid phase interacts with the primary slag. The mixing increases the content of CaO in the slag, and the lime starts to melt in the slag. At the same time, the SiO44-, which failed to enter the lime, interacts with CaO to form a high melting point dicalcium silicate (C2S) covering layer, which separates the lime block from the slag and greatly slows down the melting speed of the lime. The formation of the C2S covering layer is due to the slag close to the lime surface entering the (C2S-L) two-phase zone. Changing the slag composition to shrink the two-phase area may delay the entry of the lime surface slag into the two-phase area and make the C2S coating thinner. The melting of lime can be accelerated by increasing the bath temperature and adding MgO, MnO, B2O3 and other components to the slag. In addition, due to the existence of the FeO-rich and poor SiO2 liquid infiltration layer between the lime particles and the C2S covering layer, there is Facilitate the outward diffusion of Ca2+, can also cause the peeling of the C2S covering layer, and may also cause the cracking of the lime block, which is beneficial to accelerate the melting of the lime. It can be seen that FeO in the slag plays an important role in accelerating the melting of lime, so the use of slag retention operation is beneficial to increase the melting speed of lime.
The ternary phase diagram of SiO2-CaO-FeO is shown in Figure 2. The small circle in Figure 1 represents the distribution of the final slag composition at the end of the actual semi-steel smelting in the ternary phase diagram. Obviously, there may be several formation routes for the final slag to reach this composition, but the slag formation rate and influence brought by each slag formation route are very different. There can be 3 routes from the initial slag to the final slag, roughly the ACB, ADB and AEB routes in Figure 1. According to the change of FeO content in the slag during slag formation, AEB can be called the high iron oxide slagging pathway, and ACB can be called the low iron oxide slagging pathway. In the high iron oxide slagging route, the slag fluidity is good, the lime melts quickly, and the slag is fast. The slag is not easy to return to dry in the middle of the conversion. The slag quickly has good dephosphorization and desulfurization capabilities; the low iron oxide slagging route has a high melting point , Lime melts slowly, the slag is sticky, the slag is easy to dry back in the middle of the conversion, and the slag has weak dephosphorization and desulfurization capabilities.
If the slagging rate in the early stage of the converter smelting is fast, the dephosphorization rate before and during the middle of smelting is relatively high, which ensures the dephosphorization effect of the final converter. Shougang Jingtang adopts slag retention operation to ensure the slagging effect in the early stage of the converter, which can stabilize and improve the dephosphorization of the converter while reducing the amount of slag auxiliary materials added. The decarburization converter steelmaking slag with high iron oxide content of the previous heat is left in the furnace (3~5t), so that the high FeO in the final slag of the previous heat converter will directly participate in the early stage of the next heat converter. In the slag, due to the presence of (FeO) in the initial slag, the melting speed of lime is accelerated. In addition, the remaining slag brings in a large amount of physical heat, and the temperature rises rapidly in the early stage of converting, which is also conducive to the melting of lime to promote slag formation.
2.2 Feeding method
In the early stage of semi-steel smelting, a slag agent will be added to help the slag when the slag is retained. In addition to the high lance position as much as possible to generate FeO to help the slag, the addition of Al2O3 in the slag agent at the initial stage of the converter can reduce the 2CaO in the initial slag • SiO2 melting point, rapid formation of initial slag.
2.3 Gun position control and carbon oxygen reaction speed
The carbon in the molten metal in the converter is mainly oxidized in two ways. One is that the carbon in the molten metal directly reacts with the oxygen that is blown in, and the other is that it reacts with FeOx in the slag. It can be seen from the slagging route in Figure 1 that the direct reaction of oxygen with carbon will reduce the FeO content, which is not conducive to slagging, and the direct oxidation reaction of carbon will release a large amount of heat, which will increase the temperature of the molten steel, which will promote the carbon The oxidation rate is further intensified, carbon will consume FeO in the slag, and the FeO in the slag will be rapidly reduced, the slag will dry back, and the increase in carbon reaction will easily cause the molten steel to splash. The carbon-oxygen reaction is too fast, and the temperature of the molten steel rises quickly, which is not conducive to slagging, and the dephosphorization effect of the slag is reduced. In Figure 1, the ADB slagging path between ACB and AEB is the shortest. It requires rapid heating of the smelting process, which easily leads to intense chemical reactions and incoordination of slagging, which in turn leads to a low slag dephosphorization rate and should be avoided as much as possible.
Using high lance operation, the impact of the oxygen jet on the molten steel surface is weakened, reducing the direct contact between oxygen and the molten steel surface, and at the same time the impact surface to the slag will increase, so that the temperature of the molten steel will be slowed down and the carbon-oxygen reaction will not be sharp. At the same time, the droplets in the slag are oxidized, and the FeO content in the slag increases to promote the slagging.
3 Test Results
3.1 Slagging effect
Adopting slag retention operation, gun position control, slag auxiliary materials, and decarburization speed adjustments. Among them, semi-steel smelting slag amount is 3~5t, high gun position control, to ensure the FeO content in the slag, and control the oxidation rate of carbon in the steel. , Silicon carbide and slag agent are added in the early stage of converting to adjust the composition of the early stage slag to form the early stage slag as soon as possible. Taking the smelting of automotive sheet steel as an example, after the use of semi-steel and non-fluorinated slagging, the consumption of fluorite has increased from 1.78Kg/t to the current stop of use.
3.2 Dephosphorization effect
Taking automobile sheet steel smelting as an example, the comparison of the final molten steel in the converter before and after the non-fluorination operation is shown in Figure 2. After the dephosphorization converter realizes the non-fluorination process operation, and the converter slag is restricted by the low temperature conditions, the liquid phase rate will change. The relative decrease leads to a gradual increase in the phosphorus content of the semi-steel, which in turn leads to an upward trend in the phosphorus content at the end of the decarburization furnace (see Figure 2a). However, the end point dephosphorization rate of the decarburization converter does not change much, and it can be stabilized at about 72% (see Figure 2b), indicating that the situation without fluorinated slag is better. At the initial stage of semi-steel smelting without fluorination, the final phosphorus distribution ratio of the converter decreases. After stable production, the phosphorus distribution ratio returns to the level of fluorine operation and gradually stabilizes. The non-fluoride operation technology is slowly maturing.
3.3 Economic benefits of non-fluorination process
Shougang Jingtang decarburization converter operation area in the first two months of 2014 made a total of 4,077 furnaces, used conventional and semi-steel processes to smelt 1,538,800 tons of molten steel. The consumption of fluorite was reduced from an average of 0.7Kg/t in 2013 to zero, and it was cancelled alone. With regard to the consumption of fluorite, the steelmaking cost has been reduced by an average of RMB 1.24/t, and the cost has been reduced by RMB 1.8079 million in two months. The annual cost reduction and efficiency increase are expected to be RMB 10.85 million.
4 Conclusion
- 1) The converter adopts the combination of slag retention operation, high gun position control, flux addition, and decarburization speed control, which can replace the slagging effect of fluorite.
- 2) Industrial applications show that the optimization technology of fluoride-free slagging process is feasible and can stably control the phosphorus content of the required steel.
Please keep the source and address of this article for reprinting: The Research And Application Of Smelting Non-Fluoride Slagging
Minghe Die Casting Company are dedicated to manufacture and provide quality and high performance Casting Parts(metal die casting parts range mainly include Thin-Wall Die Casting,Hot Chamber Die Casting,Cold Chamber Die Casting),Round Service(Die Casting Service,Cnc Machining,Mold Making,Surface Treatment).Any custom Aluminum die casting, magnesium or Zamak/zinc die casting and other castings requirements are welcome to contact us.
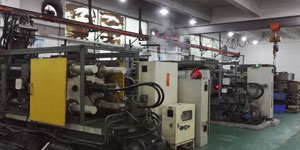
Under the control of ISO9001 and TS 16949,All processes are carried out through hundreds of advanced die casting machines, 5-axis machines, and other facilities, ranging from blasters to Ultra Sonic washing machines.Minghe not only has advanced equipment but also have professional team of experienced engineers,operators and inspectors to make the customer’s design come true.
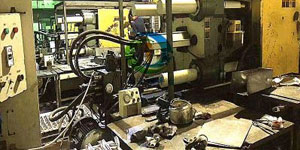
Contract manufacturer of die castings. Capabilities include cold chamber aluminum die casting parts from 0.15 lbs. to 6 lbs., quick change set up, and machining. Value-added services include polishing, vibrating, deburring, shot blasting, painting, plating, coating, assembly, and tooling. Materials worked with include alloys such as 360, 380, 383, and 413.
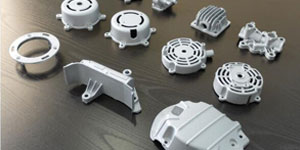
Zinc die casting design assistance/concurrent engineering services. Custom manufacturer of precision zinc die castings. Miniature castings, high pressure die castings, multi-slide mold castings, conventional mold castings, unit die and independent die castings and cavity sealed castings can be manufactured. Castings can be manufactured in lengths and widths up to 24 in. in +/-0.0005 in. tolerance.
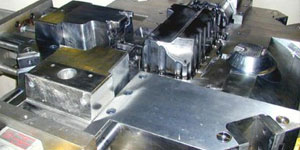
ISO 9001: 2015 certified manufacturer of die cast magnesium, Capabilities include high-pressure magnesium die casting up to 200 ton hot chamber & 3000 ton cold chamber, tooling design, polishing, molding, machining, powder & liquid painting, full QA with CMM capabilities, assembly, packaging & delivery.
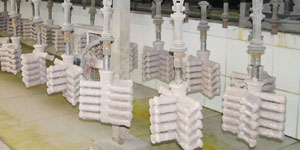
ITAF16949 certified. Additional Casting Service Include investment casting,sand casting,Gravity Casting, Lost Foam Casting,Centrifugal Casting,Vacuum Casting,Permanent Mold Casting,.Capabilities include EDI, engineering assistance, solid modeling and secondary processing.
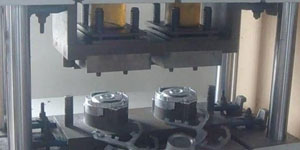
Casting Industries Parts Case Studies for: Cars, Bikes, Aircraft, Musical instruments, Watercraft, Optical devices, Sensors, Models, Electronic devices, Enclosures, Clocks, Machinery, Engines, Furniture, Jewelry, Jigs, Telecom, Lighting, Medical devices, Photographic devices, Robots, Sculptures, Sound equipment, Sporting equipment, Tooling, Toys and more.
What Can we help you do next?
∇ Go To Homepage For Die Casting China
→Casting Parts-Find out what we have done.
→Ralated Tips About Die Casting Services
By Minghe Die Casting Manufacturer |Categories: Helpful Articles |Material Tags: Aluminum Casting, Zinc Casting, Magnesium Casting, Titanium Casting, Stainless Steel Casting, Brass Casting,Bronze Casting,Casting Video,Company History,Aluminum Die Casting |Comments Off