The Smelting Knowledge Of Die Casting Alloys
The Physical And Chemical Phenomena Of Smelting Process
Alloy smelting is an important part of the die-casting process. The smelting process is not only to obtain molten metal, but more importantly, to obtain a chemical composition that meets the requirements, so that the die-casting can obtain a good crystal structure and a metal with very small gas and inclusions.
During the smelting process, the interaction between the metal and the gas and the interaction between the molten metal and the crucible cause changes in the composition, resulting in inclusions and inhalation. Therefore, formulating the correct melting process regulations and strictly implementing them is an important guarantee for obtaining high-quality castings.
1. Interaction between metal and gas
During the smelting process, the gases encountered are hydrogen (H2), oxygen (O2), water vapor (H2O), nitrogen (N2), CO2, CO, etc. These gases either dissolve in the molten metal or react with them. effect.
2. The source of the gas
Gas can enter the alloy liquid from furnace gas, furnace lining, raw materials, flux, tools, etc.
3. The interaction between metal and crucible
When the smelting temperature is too high, the iron crucible reacts quickly with the zinc liquid, and iron oxidation reaction occurs on the surface of the crucible to form oxides such as Fe2O3; in addition, the iron element also reacts with the zinc liquid to form FeZn13 compound (zinc slag), which is dissolved in the zinc liquid in. The wall thickness of the iron crucible is continuously reduced until it is scrapped.
Melting Temperature Control
1. Die-casting temperature
The melting point of the zinc alloy used for die casting is 382 ~ 386℃, and proper temperature control is an important factor in the composition control of the zinc alloy. In order to ensure the good fluidity of the alloy liquid to fill the cavity, the temperature of the molten metal in the zinc pot of the die-casting machine is 415 ~ 430℃. The upper limit of the die-casting temperature of thin-walled and complex parts can be taken; the lower limit of thick-walled and simple parts can be taken. The temperature of the molten metal in the central smelting furnace is 430 ~ 450℃. The temperature of the molten metal entering the gooseneck is basically the same as the temperature in the zinc pot.
The pouring temperature can be accurately controlled by controlling the temperature of the molten zinc in the zinc pot And achieve:
- ① The molten metal is a clean liquid without oxides;
- ② The pouring temperature does not fluctuate.
Harm of excessive temperature:
- ① Burning of aluminum and magnesium elements.
- ② The metal oxidation speed increases, the burning loss increases, and the zinc dross increases.
- ③ The effect of thermal expansion will cause the hammer head to jam.
- ④ More iron is melted into the alloy in the cast iron crucible, and the reaction between zinc and iron is accelerated at high temperatures. Hard particles of iron-aluminum intermetallic compounds are formed, causing excessive wear on the hammer head and gooseneck.
- ⑤ Fuel consumption increases accordingly.
Too low temperature: The alloy has poor fluidity, which is not conducive to forming and affects the surface quality of die castings.
Current die-casting machine melting pots or furnaces are equipped with temperature measurement and control systems. In daily work, regular inspections are mainly used to ensure the accuracy of temperature measuring instruments. Portable thermometers (thermometers) are used to measure and correct the actual temperature of the furnace on a regular basis.
Experienced die-casting unions observe the melt with the naked eye. If the melt is not too viscous and clear after scraping, the slag does not rise quickly, indicating that the temperature is appropriate; if the melt is too viscous, it indicates that the temperature is low; A layer of hoar frost appears on the liquid surface after the slag, and the slag rises too fast, indicating that the temperature is too high and should be adjusted in time.
2. How to keep the temperature stable
- ① One of the best methods: use a central melting furnace and a die-casting machine furnace as a holding furnace to avoid large temperature changes when the zinc ingot is directly added to the zinc pot to melt. Concentrated smelting can ensure the stability of the alloy composition.
- ② The second best method: the use of advanced metal liquid automatic feeding system can maintain a stable feeding speed, alloy liquid temperature and zinc pot liquid level.
- ③ If the current production conditions are direct feeding in the zinc pot, it is recommended to add the whole alloy ingot at one time to adding small alloy ingots multiple times to reduce the temperature change caused by the feeding.
3. Generation and control of zinc slag
It is a complicated physical and chemical process to melt the alloy from solid to liquid. The gas reacts with the molten metal chemically, and the oxygen reaction is the strongest, and the surface of the alloy is oxidized to produce a certain amount of scum. The dross contains oxides and intermetallic compounds of iron, zinc and aluminum. The dross scraped from the surface of the melt usually contains about 90% of zinc alloy. The reaction rate of zinc dross formation increases exponentially as the melting temperature rises.
Under normal circumstances, the slag output of the original zinc alloy ingot is less than 1%, which is in the range of 0.3 ~ 0.5%; while the slag output of remelting nozzles and waste workpieces is usually between 2 and 5%.
Control of the amount of zinc dross
- ① Strictly control the melting temperature, the higher the temperature, the more zinc dross.
- ② Avoid the stirring of the alloy liquid in the zinc pot as much as possible, any way of stirring will cause more alloy liquid to contact with oxygen atoms in the air, thereby forming more scum.
- ③ Do not slag off too frequently. When the molten alloy is exposed to the air, it will oxidize and form scum. Keeping a thin layer of scum on the furnace surface will help the liquid in the pot not to be further oxidized.
- ④ When slagging, use a porous (Ф6 mm) disc-shaped slag raking rake to gently scrape under the scum to avoid agitation of the alloy liquid as much as possible, and pick up the scraped slag. Knock lightly to make the molten metal flow back into the zinc pot.
Treatment of zinc dross
- ① Sell it back to the raw material supplier or special processing plant, because the cost of self-processing may be higher.
- ② The die-casting plant handles it by itself. A separate furnace is required, and the zinc slag remelting temperature is in the range of 420 to 440°C. Add flux at the same time. To smelt 100 kg of slag, 0.5 ~ 1.5 kg of flux needs to be added, which is first evenly distributed on the metal surface, and then mixed evenly into the molten metal with a stirrer (approximately 2 ~ 4 minutes). After holding for 5 minutes, the surface will produce a The layer is more like dirt, so scrape it off.
- ③ Nozzle materials, waste parts remelting nozzle materials, waste materials, garbage locations, scrapped workpieces, etc., should not be directly put into the zinc pot of the die-casting machine for remelting. The reason is that the surface of these nozzle materials is oxidized during the die-casting forming process, and the content of zinc oxide is much higher than that of the original alloy ingot. When these nozzle materials are remelted in the zinc pot, because the zinc oxide is in a viscous state under high temperature conditions, When it is taken out of the zinc pot, a large amount of alloy components will be taken away. The purpose of remelting the nozzle material and other materials is to effectively separate the zinc oxide from the liquid alloy. Some solvent must be added during the smelting and used after being cast into an ingot.
4. Remelting of electroplating waste
Electroplating waste should be smelted separately from non-electroplating waste, because the copper, nickel, chromium and other metals in the electroplating waste are insoluble in zinc and will exist as hard particles in the zinc alloy, which will cause difficulties in polishing and machining.
During the remelting of electroplating scrap, pay attention to separating the coating material from the zinc alloy. Put the electroplating scrap into the crucible containing the zinc alloy melt first. At this time, do not stir the melt or add flux. Use the coating material to have a high melting point. It will not melt into the alloy, but will float on the surface of the melt for the first period of time. When it is completely melted, let the crucible stand for 15-20 minutes to see if there is any scum on the surface, and scrape the scum clean. After this process, we will see whether it is necessary to add a refining agent.
5.Matters needing attention in smelting operation
- 1. Crucible: It must be cleaned before use to remove oil, rust, slag and oxide on the surface. In order to prevent the iron element in the cast iron crucible from dissolving in the alloy, the crucible should be preheated to 150 ~ 200 ℃, spray a layer of paint on the working surface, and then heated to 200 ~ 300 ℃ to completely remove the water in the paint.
- 2. Tools: Before using the smelting tools, the surface dirt should be removed, and the parts in contact with the metal must be preheated and painted. The tool must not be wetted, otherwise it will cause splashing and explosion of the melt.
- 3. Alloy material: clean up and preheat before smelting to remove the moisture adsorbed on the surface. In order to control the alloy composition, it is recommended to use 2/3 of the new material and 1/3 of the recycled material.
- 4. The melting temperature must not exceed 450°C.
- 5. Clean up the scum on the liquid surface in the zinc pot in time, replenish the zinc material in time, and maintain the normal height of the melt level (not less than 30 mm on the crucible surface), because too much scum and too low liquid level are easy The material slag enters the gooseneck cylinder, strains the steel rein, the hammer head and the cylinder itself, resulting in jamming of the hammer head, gooseneck and hammer head scrap.
- 6. The scum on the melt is gently agitated with a slag scraper to accumulate it for removal.
Please keep the source and address of this article for reprinting: The Smelting Knowledge Of Die Casting Alloys
Minghe Die Casting Company are dedicated to manufacture and provide quality and high performance Casting Parts(metal die casting parts range mainly include Thin-Wall Die Casting,Hot Chamber Die Casting,Cold Chamber Die Casting),Round Service(Die Casting Service,Cnc Machining,Mold Making,Surface Treatment).Any custom Aluminum die casting, magnesium or Zamak/zinc die casting and other castings requirements are welcome to contact us.
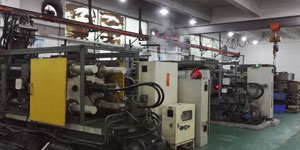
Under the control of ISO9001 and TS 16949,All processes are carried out through hundreds of advanced die casting machines, 5-axis machines, and other facilities, ranging from blasters to Ultra Sonic washing machines.Minghe not only has advanced equipment but also have professional team of experienced engineers,operators and inspectors to make the customer’s design come true.
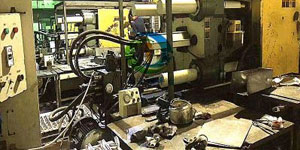
Contract manufacturer of die castings. Capabilities include cold chamber aluminum die casting parts from 0.15 lbs. to 6 lbs., quick change set up, and machining. Value-added services include polishing, vibrating, deburring, shot blasting, painting, plating, coating, assembly, and tooling. Materials worked with include alloys such as 360, 380, 383, and 413.
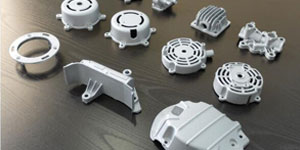
Zinc die casting design assistance/concurrent engineering services. Custom manufacturer of precision zinc die castings. Miniature castings, high pressure die castings, multi-slide mold castings, conventional mold castings, unit die and independent die castings and cavity sealed castings can be manufactured. Castings can be manufactured in lengths and widths up to 24 in. in +/-0.0005 in. tolerance.
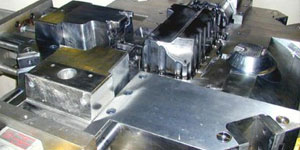
ISO 9001: 2015 certified manufacturer of die cast magnesium, Capabilities include high-pressure magnesium die casting up to 200 ton hot chamber & 3000 ton cold chamber, tooling design, polishing, molding, machining, powder & liquid painting, full QA with CMM capabilities, assembly, packaging & delivery.
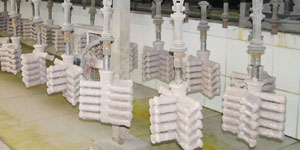
ITAF16949 certified. Additional Casting Service Include investment casting,sand casting,Gravity Casting, Lost Foam Casting,Centrifugal Casting,Vacuum Casting,Permanent Mold Casting,.Capabilities include EDI, engineering assistance, solid modeling and secondary processing.
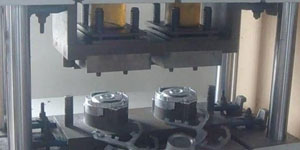
Casting Industries Parts Case Studies for: Cars, Bikes, Aircraft, Musical instruments, Watercraft, Optical devices, Sensors, Models, Electronic devices, Enclosures, Clocks, Machinery, Engines, Furniture, Jewelry, Jigs, Telecom, Lighting, Medical devices, Photographic devices, Robots, Sculptures, Sound equipment, Sporting equipment, Tooling, Toys and more.
What Can we help you do next?
∇ Go To Homepage For Die Casting China
→Casting Parts-Find out what we have done.
→Ralated Tips About Die Casting Services
By Minghe Die Casting Manufacturer |Categories: Helpful Articles |Material Tags: Aluminum Casting, Zinc Casting, Magnesium Casting, Titanium Casting, Stainless Steel Casting, Brass Casting,Bronze Casting,Casting Video,Company History,Aluminum Die Casting |Comments Off