The Solution To Wet Knotting In Intermediate Frequency Induction Furnace
Furnace knotting is an important process in the smelting and casting of intermediate frequency induction furnaces. Over the years, the repetition of knotting the furnace and purchasing the integral furnace has been unsatisfactory. We adopt the wet knotting technology of the intermediate frequency induction electric furnace, which has been well improved.
1. Advantages
The wet knotting technology of the intermediate frequency induction furnace is a new technology for the knotting of the furnace that has appeared in recent years. After being introduced to our company in 2012, through serious preliminary demonstrations, we succeeded in one fell swoop, and solved the problem of high labor intensity, time-consuming, and difficult knotting quality that have been plagued by our furnace tying work. Moreover, this method of tying The knotted furnace is also easy to disassemble, and the service life is almost the same as that of dry knotting. The 1t furnace can ensure the safe melting of more than 60t molten metal every time.
2. Basic method
At the initial stage of application, we used silica sand as the base material for the furnace bladder knotting material. The basic ingredients are: silica sand: 2# (8~10 mesh) 5 %, 3# (10~26 mesh) 35%, 4# (16~24 mesh) 35%, 8# (250~400 mesh) 25%; Boric acid: 2.5%; water: 8%. After three-dry and three-wet rebuilding, the knot is gradually knotted to the furnace mouth by using a vibrating rod while feeding. After natural drying for 4-6h (depending on the temperature), pull out the steel mold, and then dry it naturally for no less than 2h (depending on the temperature, if possible, the natural drying time can be extended to 8-10h best). After finishing the furnace collar, put 6-8 steel pipes in the furnace against the furnace wall, and put a steel pipe (with base) in the middle, and then start the power oven. The specifications of the oven are the same as those of the dry-knotted furnace.
3. Compare
Compared with the dry-knotted furnace, the wet-knotted furnace has no layer seams that may exist in the dry-knotted furnace. The furnace charge added each time is filled evenly under the action of the vibrating rod, and the excess water continues to rise, ensuring that the combination of the newly added furnace charge and the first furnace charge does not stratify. Especially afterwards, we used a mixer to mix the furnace material, and completely eliminated the labor intensity problem of the furnace. Knotting the furnace is not only easy, but also the quality can be fully guaranteed. Now we use refractory aggregate (a kind of multi-specification furnace material preparation) produced by a professional factory to make it easier to tie the furnace bladder. The only shortcoming is that the physical strength is not as high as that of the dry-knotted furnace, but as long as the smelting operation is carried out according to its characteristics, its shortcomings are not a problem.
4. Technical points
Technical points to pay attention to when using wet knotting furnace:
- (1) The holding of the moisture of the stirring charge should be dry rather than wet, so as to avoid excessive moisture overflow during knotting.
- (2) The oven must be carried out separately, and the oven with materials cannot be carried out. For the first smelting, especially the initial charging of the charge, the charge should hit the bottom and the furnace wall as much as possible. At other times, avoid using the furnace wall as a support to move the charge.
- (3) When adding furnace charge, pay special attention to avoiding shed material to avoid the occurrence of material shifting operation.
- (4) When the furnace bladder partially falls off, brush it with water glass and plug it tightly with wet furnace material.
Concluding remarks
The practice of several years has proved that the wet-knotting furnace bladder technology is an easy, reliable and safe method for furnace bladder knotting, which can be used by enterprises with confidence.
Please keep the source and address of this article for reprinting: The Solution To Wet Knotting In Intermediate Frequency Induction Furnace
Minghe Die Casting Company are dedicated to manufacture and provide quality and high performance Casting Parts(metal die casting parts range mainly include Thin-Wall Die Casting,Hot Chamber Die Casting,Cold Chamber Die Casting),Round Service(Die Casting Service,Cnc Machining,Mold Making,Surface Treatment).Any custom Aluminum die casting, magnesium or Zamak/zinc die casting and other castings requirements are welcome to contact us.
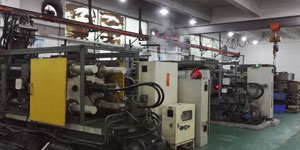
Under the control of ISO9001 and TS 16949,All processes are carried out through hundreds of advanced die casting machines, 5-axis machines, and other facilities, ranging from blasters to Ultra Sonic washing machines.Minghe not only has advanced equipment but also have professional team of experienced engineers,operators and inspectors to make the customer’s design come true.
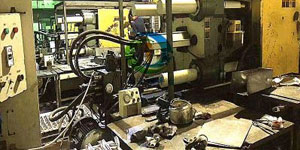
Contract manufacturer of die castings. Capabilities include cold chamber aluminum die casting parts from 0.15 lbs. to 6 lbs., quick change set up, and machining. Value-added services include polishing, vibrating, deburring, shot blasting, painting, plating, coating, assembly, and tooling. Materials worked with include alloys such as 360, 380, 383, and 413.
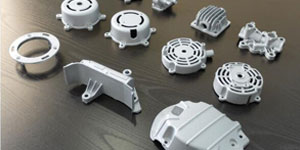
Zinc die casting design assistance/concurrent engineering services. Custom manufacturer of precision zinc die castings. Miniature castings, high pressure die castings, multi-slide mold castings, conventional mold castings, unit die and independent die castings and cavity sealed castings can be manufactured. Castings can be manufactured in lengths and widths up to 24 in. in +/-0.0005 in. tolerance.
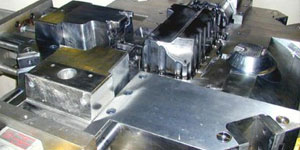
ISO 9001: 2015 certified manufacturer of die cast magnesium, Capabilities include high-pressure magnesium die casting up to 200 ton hot chamber & 3000 ton cold chamber, tooling design, polishing, molding, machining, powder & liquid painting, full QA with CMM capabilities, assembly, packaging & delivery.
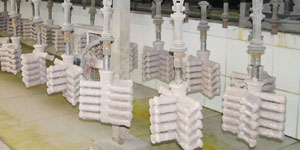
ITAF16949 certified. Additional Casting Service Include investment casting,sand casting,Gravity Casting, Lost Foam Casting,Centrifugal Casting,Vacuum Casting,Permanent Mold Casting,.Capabilities include EDI, engineering assistance, solid modeling and secondary processing.
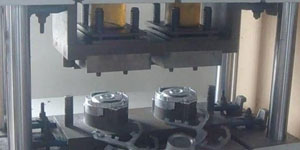
Casting Industries Parts Case Studies for: Cars, Bikes, Aircraft, Musical instruments, Watercraft, Optical devices, Sensors, Models, Electronic devices, Enclosures, Clocks, Machinery, Engines, Furniture, Jewelry, Jigs, Telecom, Lighting, Medical devices, Photographic devices, Robots, Sculptures, Sound equipment, Sporting equipment, Tooling, Toys and more.
What Can we help you do next?
∇ Go To Homepage For Die Casting China
→Casting Parts-Find out what we have done.
→Ralated Tips About Die Casting Services
By Minghe Die Casting Manufacturer |Categories: Helpful Articles |Material Tags: Aluminum Casting, Zinc Casting, Magnesium Casting, Titanium Casting, Stainless Steel Casting, Brass Casting,Bronze Casting,Casting Video,Company History,Aluminum Die Casting |Comments Off