The Solve Method Of Sticking Mold At Die Casting Gate
In the process of die-casting production, it is often encountered that serious sticking or sticking occurs at the gate part of the mold. The aluminum alloy adheres to the wall around the gate and is not easy to remove. This situation occurs more frequently in new molds. many. When the factory first started to produce 186 boxes, the gate parts were stuck in blocks and cracks appeared, resulting in a low product qualification rate and affecting the normal production of die casting. There are many factors that cause mold sticking, such as the unqualified chemical composition of the alloy, because aluminum alloy and iron have a strong affinity, under certain conditions, it is easy to react with H13 molds and cause sticking; the use of mold release agents is poor The setting of process parameters is unreasonable; the gate design of the mold is unreasonable; the rigidity or surface roughness of the mold is not enough, etc., which need to be solved in the specific production process. After analysis and summary: We took the following measures to solve the problem of adhesion and cracks in the 186 box gate.
1. Analysis of the chemical composition of aluminum alloy
Aluminum alloy and iron have a strong affinity. When the iron content in the aluminum alloy is less than 0.7%, the aluminum alloy is prone to chemically react with the H13 mold to produce compounds, which adhere to the mold surface and produce sticky molds, but iron can Reduce the tendency of aluminum alloy to stick to molds and facilitate die-casting. With the increase of iron content, the mechanical properties decrease, especially the impact toughness and plasticity decrease, the tendency of hot cracking increases, and hard spots appear in the aluminum alloy, and the processing performance deteriorates. Therefore, the iron content in die-cast aluminum alloy should be controlled within 0.7%~1.3%.
Therefore, we should first analyze the chemical composition of the aluminum alloy. After spectral analysis, the iron content of ADC12 aluminum alloy used in this product is about 0.9%, and there is no problem with the alloying element composition.
2. Adjustment of die casting process parameters
The setting of process parameters also has a great influence on the sticking mold, such as the pressure and speed, the pouring temperature of the alloy, the temperature of the mold, etc., so reasonable process parameters must be calculated according to the structure and use requirements of the casting.
- Adjustment of pressure and speed. High metal pressure flow will increase the bonding between the alloy and the mold, and the friction heat between different metals under high pressure makes the welding between the metals, which is also a sticking phenomenon. The pressure of the metal flow needs to be calculated and set the minimum pressure required to produce high-quality casting products. This product is produced under the Lijin DCC1600 model. According to the requirements of the product, the required boost pressure is calculated to be 24~26Mpa to avoid metal flow bonding under excessive pressure and reduce the tightness of the mold, which can also be avoided. The occurrence of cracks. The high-speed metal flow scoured the shaped wall, the accelerated die-casting mold was worn out, and the high-speed metal flow entered the shaped wall in a mist form, adhered to the surface of the mold, and could not fuse with the subsequent metal flow to form surface defects. Pressure and speed are two factors that complement each other and restrict each other. In order to meet the technological requirements of castings, the pressure and filling speed of die casting must be adjusted steplessly.
- Control of mold and alloy temperature. The level of mold temperature is very important for whether mold sticking occurs. The higher the mold temperature, the easier it is to produce sticky molds. The water inlet of the mold is the high temperature zone. In this area, we should increase the number of sprayed copper pipes, or use a spray gun to cool the mold part, and check the cooling water effect of the mold. In the actual production process, we can use infrared The thermometer detects the sticking part of the mold and controls the mold temperature between 150°C and 220°C to allow the mold to reach thermal equilibrium. The aluminum alloy pouring temperature is set to the lowest according to the requirements of the casting, between 610℃~680℃, to reduce the formation of sticky molds.
- Through the debugging of the above process. The mold sticking at the gate is relieved to a certain extent, but it is still unstable and more scrapped. So we started to improve the mold runner. The high internal gate speed increases the temperature of the local mold when the metal flow impacts the shaped wall and accelerates the formation of the sticky mold. Therefore, it is necessary to consider reducing the inner gate speed. Inner gate speed = injection speed * punch area / gate area. It can be seen from the formula that reducing the speed of the inner gate can increase the cross-sectional area of the inner pouring, reduce the injection speed and Replace the pressure chamber. We increase the cross-sectional area of the inner pouring and adjust the injection speed to reduce the speed of the inner gate and reduce the formation of sticky mold.
The runner of the 186 box adopts an internal gate. The direct impact of the metal flow on the surface of the mold can easily destroy the dense oxide metal film on the surface of the mold, making the surface of the mold uneven and causing the mold to stick. By modifying the runner to make the metal flow contact the surface of the cavity at a smaller angle, it is also possible to apply a circular arc on the runner.
3. Use of release agent
The mold release agent helps to reduce mold sticking. It is necessary to use a good mold release agent. The mold release agent can form a protective film between the casting and the mold to prevent the molten soup from directly contacting the mold to prevent mold sticking. Even on the polished mold surface, when measured in micrometers, many uneven areas can be seen. The release agent fills up this unevenness and produces a lubricating effect, but the release agent will be washed away under the action of the vortex flow of the molten metal to form a sticky mold. A good release agent must have enough strength to withstand the separation or impact of molten metal. The cooling water temperature of the mold should be lower than the temperature of the mold surface, so that the release agent can be fully attached to the mold surface and play an ideal protective role. If the temperature of the mold is too high, the release agent will be more difficult to adhere to the mold surface. This is because the release agent will be heated to a very high temperature, so that it will quickly evaporate and cannot adhere to the mold surface, which increases the tendency of mold sticking. The best ideal temperature for the release agent to form a protective film on the mold surface is 200°C~250°C. When the injection metal flow makes the surface of the mold rough, the tendency of mold sticking will increase. In the place where sticking is more serious, you can also apply some special lubricating grease and mold release paste on the part of the mold. These products are all It has a good lubricating and demoulding effect and reduces the formation of sticky molds.
4. Mold surface treatment
Some surface treatment methods can prevent the occurrence of sticking. Special materials with higher melting points should be used to treat the surface of the mold. This alloy can be mixed with iron and can adhere to the position of the mold surface to avoid sticking. It is also possible to use various materials to prevent sticking at the sticking position to treat the surface of the mold, increase the hardness of the material on the mold surface at high temperatures, and reduce the activity of the mold surface to avoid sticking.
In Conclusion:
Through the adjustment and improvement of various factors that affect mold sticking, sticking and sticking at the gate have been basically controlled, and the product qualification rate has reached the company's requirements, ensuring the normal production of die-casting.
Main control measures:
- Analysis and inspection of chemical composition in aluminum alloy
- Reduce the mold temperature to the minimum where the mold is prone to sticking
- The mold release agent and special mold release products sprayed on the mold surface can effectively reduce the occurrence of mold sticking.
- Under the condition of ensuring the quality, try to reduce the temperature of the molten metal as much as possible
- The direction of molten metal entering the mold must contact the surface of the cavity at a small angle
- Under meeting the technological requirements of castings, the pressure and filling speed of die casting must be adjusted steplessly
- Some mold surface treatment methods can prevent the occurrence of mold sticking, increase the hardness of the material on the mold surface at high temperatures, and reduce the activity of the mold surface to avoid mold sticking.
Please keep the source and address of this article for reprinting: The Solve Method Of Sticking Mold At Die Casting Gate
Minghe Die Casting Company are dedicated to manufacture and provide quality and high performance Casting Parts(metal die casting parts range mainly include Thin-Wall Die Casting,Hot Chamber Die Casting,Cold Chamber Die Casting),Round Service(Die Casting Service,Cnc Machining,Mold Making,Surface Treatment).Any custom Aluminum die casting, magnesium or Zamak/zinc die casting and other castings requirements are welcome to contact us.
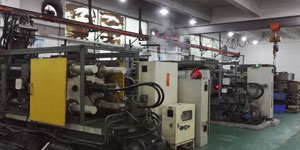
Under the control of ISO9001 and TS 16949,All processes are carried out through hundreds of advanced die casting machines, 5-axis machines, and other facilities, ranging from blasters to Ultra Sonic washing machines.Minghe not only has advanced equipment but also have professional team of experienced engineers,operators and inspectors to make the customer’s design come true.
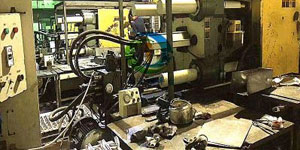
Contract manufacturer of die castings. Capabilities include cold chamber aluminum die casting parts from 0.15 lbs. to 6 lbs., quick change set up, and machining. Value-added services include polishing, vibrating, deburring, shot blasting, painting, plating, coating, assembly, and tooling. Materials worked with include alloys such as 360, 380, 383, and 413.
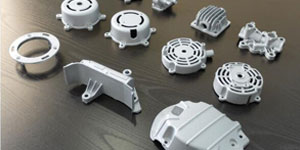
Zinc die casting design assistance/concurrent engineering services. Custom manufacturer of precision zinc die castings. Miniature castings, high pressure die castings, multi-slide mold castings, conventional mold castings, unit die and independent die castings and cavity sealed castings can be manufactured. Castings can be manufactured in lengths and widths up to 24 in. in +/-0.0005 in. tolerance.
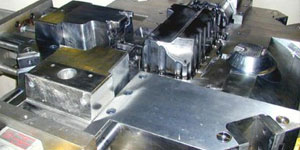
ISO 9001: 2015 certified manufacturer of die cast magnesium, Capabilities include high-pressure magnesium die casting up to 200 ton hot chamber & 3000 ton cold chamber, tooling design, polishing, molding, machining, powder & liquid painting, full QA with CMM capabilities, assembly, packaging & delivery.
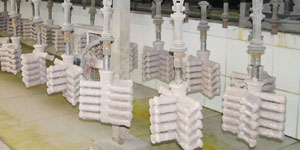
ITAF16949 certified. Additional Casting Service Include investment casting,sand casting,Gravity Casting, Lost Foam Casting,Centrifugal Casting,Vacuum Casting,Permanent Mold Casting,.Capabilities include EDI, engineering assistance, solid modeling and secondary processing.
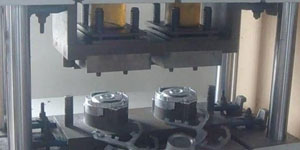
Casting Industries Parts Case Studies for: Cars, Bikes, Aircraft, Musical instruments, Watercraft, Optical devices, Sensors, Models, Electronic devices, Enclosures, Clocks, Machinery, Engines, Furniture, Jewelry, Jigs, Telecom, Lighting, Medical devices, Photographic devices, Robots, Sculptures, Sound equipment, Sporting equipment, Tooling, Toys and more.
What Can we help you do next?
∇ Go To Homepage For Die Casting China
→Casting Parts-Find out what we have done.
→Ralated Tips About Die Casting Services
By Minghe Die Casting Manufacturer |Categories: Helpful Articles |Material Tags: Aluminum Casting, Zinc Casting, Magnesium Casting, Titanium Casting, Stainless Steel Casting, Brass Casting,Bronze Casting,Casting Video,Company History,Aluminum Die Casting |Comments Off