The Tempering And Quenching Of Cast Iron
The so-called quenching is to reduce the temperature of the material from the austenite region at a very fast rate to prevent the formation of pearlite or sorbite. The cooling from the austenite region to the Ms temperature will not cause carbon diffusion due to too short time. It is basically directly transformed into martensite.
This structure is very hard but also quite brittle. It can be softened by tempering to improve toughness. Therefore, after different temperatures, different combinations of hardness, strength and toughness can be obtained.
There is the so-called constant temperature quenching or hot melt quenching, that is, quenching in the salt bath and metal bath, resulting in the mesophase or the structure of the toughened iron. In the cast iron, the quenching and tempering treatment is often performed on spheroidal graphite cast iron. In terms of it, it has no special significance. At most, quenching treatment is considered when the abrasion strength of gray cast iron is to be improved. In fact, this result can be achieved by surface treatment.
For spheroidal grey cast iron, after quenching and tempering treatment, the same strength as casting or normalization treatment can be obtained, but it has higher yield strength, resulting in greater elasticity, especially higher toughness, because After quenching and tempering, the base contains higher carbon, and in this case, it is easier to perform surface hardening treatment than when it contains Bain structure.
If it is cooled in air, the hardening ability of non-alloyed and low-alloyed cast iron is not high enough, so it must be quenched in some liquid. In order to avoid hot cracking during quenching, the quenching liquid used is preferably oil or some kind of suspension The use of water should be avoided. During quenching, a temperature gradient will form inside the casting. At the same time, due to the time difference, the volume change rate caused by the formation of martensite is also different. At the same time, the internal stress inside the casting increases. It is easy to form hot cracks or form very high internal stress in the casting. In this case, the temperature of the oil bath should be increased to between 50~100℃, so as to avoid the formation of stress. For large castings, be especially careful to extend the thicker part to the quenching liquid first, so as to reduce the thermal stress on the thinner part. At the same time, the oil in the oil must be stirred or allowed to flow. Or keep the casting swaying in the quenching liquid.
The quenching temperature of cast iron should be between 820~920℃, and the most commonly used temperature in general factories is between 850~900℃. When the quenching temperature is too low, the austenite with lower carbon content will be softer after quenching, and the strength of the martensite formed will be lower. On the contrary, if the quenching temperature is too high, the austenite will contain carbon. If the amount is too high, the risk of hot cracking during quenching will increase, and the chance of forming retained austenite will also increase.
The quenched cast iron is actually very brittle and contains too high internal stress. In order to improve its hardness and toughness, it must be tempered. The processing procedure is similar to that of steel. The heating rate should be lower than 100℃/hour. The temperature should be between 450~600℃, and the tempering time is about 4 hours. If the tempering time is too long or the temperature is too high, the strength and hardness will decrease a lot, but the elasticity can be improved. Tempering within a period of time can result in a fairly uniform tempering effect. At the same time, the distribution of the characteristics of the entire casting is also very uniform. In order to prevent the recurrence of internal stress, especially for complex castings, it should be slowly cooled to below 200°C after tempering. .
Please keep the source and address of this article for reprinting:The Tempering And Quenching Of Cast Iron
Minghe Die Casting Company are dedicated to manufacture and provide quality and high performance Casting Parts(metal die casting parts range mainly include Thin-Wall Die Casting,Hot Chamber Die Casting,Cold Chamber Die Casting),Round Service(Die Casting Service,Cnc Machining,Mold Making,Surface Treatment).Any custom Aluminum die casting, magnesium or Zamak/zinc die casting and other castings requirements are welcome to contact us.
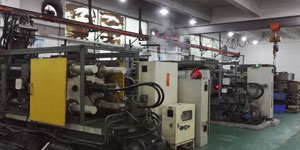
Under the control of ISO9001 and TS 16949,All processes are carried out through hundreds of advanced die casting machines, 5-axis machines, and other facilities, ranging from blasters to Ultra Sonic washing machines.Minghe not only has advanced equipment but also have professional team of experienced engineers,operators and inspectors to make the customer’s design come true.
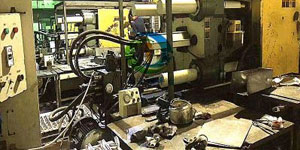
Contract manufacturer of die castings. Capabilities include cold chamber aluminum die casting parts from 0.15 lbs. to 6 lbs., quick change set up, and machining. Value-added services include polishing, vibrating, deburring, shot blasting, painting, plating, coating, assembly, and tooling. Materials worked with include alloys such as 360, 380, 383, and 413.
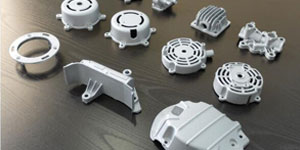
Zinc die casting design assistance/concurrent engineering services. Custom manufacturer of precision zinc die castings. Miniature castings, high pressure die castings, multi-slide mold castings, conventional mold castings, unit die and independent die castings and cavity sealed castings can be manufactured. Castings can be manufactured in lengths and widths up to 24 in. in +/-0.0005 in. tolerance.
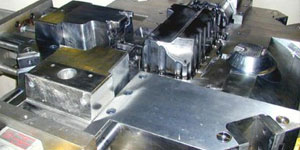
ISO 9001: 2015 certified manufacturer of die cast magnesium, Capabilities include high-pressure magnesium die casting up to 200 ton hot chamber & 3000 ton cold chamber, tooling design, polishing, molding, machining, powder & liquid painting, full QA with CMM capabilities, assembly, packaging & delivery.
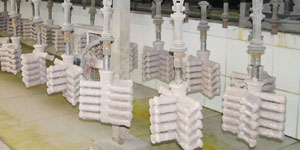
ITAF16949 certified. Additional Casting Service Include investment casting,sand casting,Gravity Casting, Lost Foam Casting,Centrifugal Casting,Vacuum Casting,Permanent Mold Casting,.Capabilities include EDI, engineering assistance, solid modeling and secondary processing.
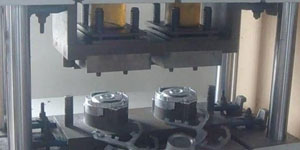
Casting Industries Parts Case Studies for: Cars, Bikes, Aircraft, Musical instruments, Watercraft, Optical devices, Sensors, Models, Electronic devices, Enclosures, Clocks, Machinery, Engines, Furniture, Jewelry, Jigs, Telecom, Lighting, Medical devices, Photographic devices, Robots, Sculptures, Sound equipment, Sporting equipment, Tooling, Toys and more.
What Can we help you do next?
∇ Go To Homepage For Die Casting China
→Casting Parts-Find out what we have done.
→Ralated Tips About Die Casting Services
By Minghe Die Casting Manufacturer |Categories: Helpful Articles |Material Tags: Aluminum Casting, Zinc Casting, Magnesium Casting, Titanium Casting, Stainless Steel Casting, Brass Casting,Bronze Casting,Casting Video,Company History,Aluminum Die Casting |Comments Off