The Water Filling Method Of Centrifugal Pump
Centrifugal pumps (except self-priming pumps) must be filled with water before starting the pump and the water inlet pipe, otherwise the water pump will not work. The centrifugal pump does not produce water after it is started, which is often caused by the fact that the air in the pump has not been drained and the water has not been filled.
There are two main water filling methods before starting: one is to use the assembled bottom valve to fill the water. The bottom valve is a one-way valve and is installed at the inlet of the water inlet pipe. The disadvantage of this method is that the bottom valve has a large head loss, which affects The device efficiency of the water pump; the other is water filling without a bottom valve. The biggest advantage of this method is energy saving, which can save energy by 10% to 15% compared to a pump station with a bottom valve. The following introduces several water filling methods of centrifugal pumps for users to choose when running the pump.
■ Self-Diversion And Water Filling Method
For the semi-submerged pump house (that is, the pump station where the height of the inlet pipe and the pump top are below the water surface of the inlet pool), water can be introduced into the pump by itself without manual irrigation. The disadvantage of this kind of pumping station is that it does not make full use of the pump's water absorption capacity, and the installation height of the pump is reduced, which not only increases the amount of foundation excavation, but also has less convenient operation and management; but the advantages are also obvious, that is, it is easy to realize the pumping station. Automation and timeliness is strong.
■ Artificial Water Filling Method
For small pumping stations with a water inlet pipe diameter of less than 300mm, there is usually a bottom valve at the inlet of the water inlet pipe, and the manual water filling method is generally used, that is, a water filling funnel (or a water filling funnel (or a Remove the inverted ordinary bottle from the bottom of the bottle) Fill it with water. For small pumping stations with the inlet pipe diameter less than 300mm, the inlet of the inlet pipe is usually equipped with a bottom valve, and the pump can also be filled with water from the outlet pipe of the pump (pumping station with short outlet pipe). Since there is no need to purchase other water filling equipment, this kind of water filling method is more common in the current small rural pumping stations.
For small pumping stations that do not have bottom valves or check valves and have short pipelines, it is also possible to start up while filling the water pump from the outlet of the water outlet, so as to gradually take out the air in the pump and pipeline. , Generally, after a few minutes of continuous water filling, the water pump can work normally.
■ Vacuum Water Tank Filling Method
For small pumping stations without a bottom valve, the vacuum water tank filling method can be used. The vacuum water tank is a closed water tank made of iron sheet welding. Its volume is at least 3 times the volume of the water inlet pipe. The location of the water tank should be as close as possible to the pump, and the bottom height of the water tank should also be slightly lower than the axis of the pump. The height of the vacuum water tank is generally twice the diameter of the water tank.
Before starting the pump, fill the water tank with water to seal it. After the water pump is started, the water pump enters the water from the vacuum tank. As the water level of the water tank drops, a certain vacuum is formed in the water tank. The water pump starts to operate normally.
■ Jet Pump Water Filling Method
When the diesel engine is used to drive the water pump to pump water, the exhaust gas discharged from the diesel engine can be used to pass into the jet that communicates with the top of the water pump for pumping and filling water, thereby removing the bottom valve of the water pump. When the water pump is started, the valve cover connected to the handle is closed, the exhaust gas is ejected from the jet, and the air in the pump is sucked out through the connecting pipe. After filling the water, open the valve cover and close the control valve. The advantage of this water filling method is that it makes full use of the power machine, and the other is that it improves the efficiency of the pumping station.
■ Self-Suspension Water Diversion And Water Filling Method
The self-suspension water diversion and water filling method uses the difference in bulk density of water and air, and is realized by the principle of "water-air displacement". This method can remove the bottom valve of the water pump.
First of all, design a ventilation tank with an appropriate amount of containers. The ventilation tank is generally made of plastic products, but can also be made of thin metal parts, and the cost is only one-half of the bottom valve. Then, place the ventilating tank at the water inlet of the water pump to form a connected body with the water pump and the pipeline. At the same time, install an air exchange control valve on the air exchange channel between the air exchange tank and the water pump. When filling water, fill the air exchange tank with water in advance, then seal it with a cap, and then open the air exchange valve. After the air exchange is complete, close the air exchange valve, and a part of the water will be suspended in the inlet pipe. Repeat this method several times, all the air will be exhausted, and the water inlet pipe will be filled with water.
At this point, the water pump can be started for lifting operations. Before shutting down, as long as the gate valve is closed and then shut down, the water diversion will not sit back. There is no need to irrigate and divert water the next time it is started. The advantages of this water-filling method are lower price of the gas exchange tank, easy manufacture, low labor intensity, and energy saving.
■ Vacuum Pump Water Filling Method
For large and medium-sized pumping stations with a water inlet pipe diameter greater than 300mm, or pumping stations with a high degree of automation requirements, a vacuum pumping device is a commonly used water-filling device. It is assembled by vacuum pumps and other equipment. The vacuum pumps often used in irrigation and drainage stations are mostly water ring vacuum pumps.
An eccentric toothed impeller is installed in the cylindrical pump casing of the water ring vacuum pump. The pump casing is filled with circulating water. When vacuuming, the impeller rotates. Under the action of centrifugal force, the circulating water in the pump casing is thrown around the impeller, forming a rotating water ring on the inner wall of the pump casing. And because the impeller is eccentrically installed in the pump casing, the size of the space formed between the water ring and the toothed blades is different. When the impeller rotates clockwise, the space between the two blades on the right half of the impeller gradually increases. Under the closed condition, as the air volume increases, the pressure decreases, forming a vacuum, and the air in the water pump and the pipeline passes through The suction pipe enters the crescent-shaped suction port on the right side of the vacuum pump casing and is sucked into the vacuum pump. The space between the two blades of the left half of the vacuum pump impeller is gradually reduced. Therefore, the air is compressed and the pressure increases, and finally passes through the vacuum pump. The crescent-shaped exhaust port on the left side of the pump casing discharges the vacuum pump and enters the water-gas separation box to separate the circulating water that is carried out before reuse. When the impeller keeps rotating, the vacuum pump continuously sucks and exhausts air, and finally fills the water pump with water.
■ Hand Pump Water Filling Method
As a kind of reciprocating positive displacement pump, manual pumps are widely used in rural my country. Farmers can use their own manual pumps as vacuum pumps to fill centrifugal pumps with water, which is convenient and economical. The most common usage is: install the hand pump on the suction hole of the centrifugal pump or on the water inlet pipe close to the water pump to pump and divert water, making it a tool for filling water when the centrifugal pump is turned on, thus eliminating the need for the water pump inlet pipe The bottom valve reduces energy loss and improves the efficiency of the water pump device.
■ Self-Diversion And Water Filling Method
For the semi-submerged pump house (that is, the pump station where the height of the inlet pipe and the pump top are below the water surface of the inlet pool), water can be introduced into the pump by itself without manual irrigation. The disadvantage of this kind of pumping station is that it does not make full use of the pump's water absorption capacity, and the installation height of the pump is reduced, which not only increases the amount of foundation excavation, but also has less convenient operation and management; but the advantages are also obvious, that is, it is easy to realize the pumping station. Automation and timeliness is strong.
■ Self-Suspension Water Diversion And Water Filling Method
The self-suspension diversion and water filling method uses the difference in bulk density of water and air,
The principle of "replacement" is realized. This method can remove the bottom valve of the water pump.
First of all, design a ventilation tank with an appropriate amount of containers. The ventilation tank is generally made of plastic products, but can also be made of thin metal parts, and the cost is only one-half of the bottom valve. Then, the ventilating tank is placed at the water inlet of the water pump to form a communicating body with the water pump and the pipeline. At the same time, install an air exchange control valve on the air exchange channel between the air exchange tank and the water pump. When filling water, fill the air exchange tank with water in advance, then seal it with a cap, and then open the air exchange valve. After the air exchange is completed, close the air exchange valve, and a part of the water will be suspended in the inlet pipe. Repeat this method several times, all the air will be exhausted, and the water inlet pipe will be filled with water. At this point, the water pump can be started for lifting operations. Before shutting down, as long as the gate valve is closed and then shut down, the water diversion will not sit back. There is no need to irrigate and divert water the next time it is started. The advantages of this water-filling method are lower price of the gas exchange tank, easy manufacture, low labor intensity, and energy saving.
■ Vacuum Pump Water Filling Method
For large and medium-sized pumping stations with a water inlet pipe diameter greater than 300mm, or pumping stations with a high degree of automation requirements, a vacuum pumping device is a commonly used water-filling device. It is assembled by vacuum pumps and other equipment. The vacuum pumps often used in irrigation and drainage stations are mostly water ring vacuum pumps. An eccentric toothed impeller is installed in the cylindrical pump casing of the water ring vacuum pump. The pump casing is filled with circulating water. When vacuuming, the impeller rotates. Under the action of centrifugal force, the circulating water in the pump casing is thrown around the impeller, forming a rotating water ring on the inner wall of the pump casing. And because the impeller is eccentrically installed in the pump casing, the size of the space formed between the water ring and the toothed blades is different.
When the impeller rotates clockwise, the space between the two blades on the right half of the impeller gradually increases. Under the closed condition, as the air volume increases, the pressure decreases, forming a vacuum, and the air in the water pump and the pipeline passes through The suction pipe enters the crescent-shaped suction port on the right side of the vacuum pump casing and is sucked into the vacuum pump. The space between the two blades of the left half of the vacuum pump impeller is gradually reduced, so the air is compressed and the pressure increases, and finally passes through the vacuum pump. The crescent-shaped exhaust port on the left side of the pump casing discharges the vacuum pump and enters the water-gas separation box to separate the circulating water that is carried out before reuse. When the impeller keeps rotating, the vacuum pump continuously sucks and exhausts air, and finally fills the water pump with water.
Please keep the source and address of this article for reprinting:The Water Filling Method Of Centrifugal Pump
Minghe Die Casting Company are dedicated to manufacture and provide quality and high performance Casting Parts(metal die casting parts range mainly include Thin-Wall Die Casting,Hot Chamber Die Casting,Cold Chamber Die Casting),Round Service(Die Casting Service,Cnc Machining,Mold Making,Surface Treatment).Any custom Aluminum die casting, magnesium or Zamak/zinc die casting and other castings requirements are welcome to contact us.
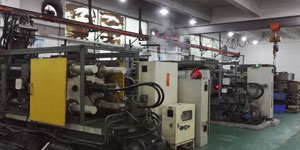
Under the control of ISO9001 and TS 16949,All processes are carried out through hundreds of advanced die casting machines, 5-axis machines, and other facilities, ranging from blasters to Ultra Sonic washing machines.Minghe not only has advanced equipment but also have professional team of experienced engineers,operators and inspectors to make the customer’s design come true.
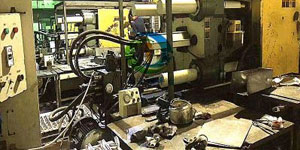
Contract manufacturer of die castings. Capabilities include cold chamber aluminum die casting parts from 0.15 lbs. to 6 lbs., quick change set up, and machining. Value-added services include polishing, vibrating, deburring, shot blasting, painting, plating, coating, assembly, and tooling. Materials worked with include alloys such as 360, 380, 383, and 413.
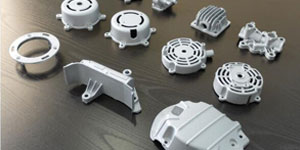
Zinc die casting design assistance/concurrent engineering services. Custom manufacturer of precision zinc die castings. Miniature castings, high pressure die castings, multi-slide mold castings, conventional mold castings, unit die and independent die castings and cavity sealed castings can be manufactured. Castings can be manufactured in lengths and widths up to 24 in. in +/-0.0005 in. tolerance.
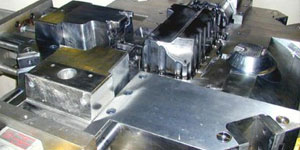
ISO 9001: 2015 certified manufacturer of die cast magnesium, Capabilities include high-pressure magnesium die casting up to 200 ton hot chamber & 3000 ton cold chamber, tooling design, polishing, molding, machining, powder & liquid painting, full QA with CMM capabilities, assembly, packaging & delivery.
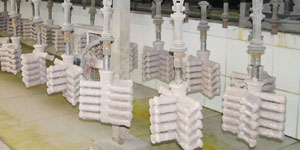
ITAF16949 certified. Additional Casting Service Include investment casting,sand casting,Gravity Casting, Lost Foam Casting,Centrifugal Casting,Vacuum Casting,Permanent Mold Casting,.Capabilities include EDI, engineering assistance, solid modeling and secondary processing.
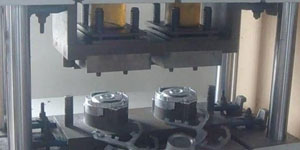
Casting Industries Parts Case Studies for: Cars, Bikes, Aircraft, Musical instruments, Watercraft, Optical devices, Sensors, Models, Electronic devices, Enclosures, Clocks, Machinery, Engines, Furniture, Jewelry, Jigs, Telecom, Lighting, Medical devices, Photographic devices, Robots, Sculptures, Sound equipment, Sporting equipment, Tooling, Toys and more.
What Can we help you do next?
∇ Go To Homepage For Die Casting China
→Casting Parts-Find out what we have done.
→Ralated Tips About Die Casting Services
By Minghe Die Casting Manufacturer |Categories: Helpful Articles |Material Tags: Aluminum Casting, Zinc Casting, Magnesium Casting, Titanium Casting, Stainless Steel Casting, Brass Casting,Bronze Casting,Casting Video,Company History,Aluminum Die Casting |Comments Off