The Ways To Solve The Special Problems Of Large Ductile Iron Castings
There are many types of large ductile iron parts, such as: large diesel engine block, large wheel hub, large ball mill end cover, blast furnace cooling stave, large rolling mill frame, large injection molding machine template, large steam turbine bearing seat, wheel hub in wind power equipment and Bases and waste slag tanks in nuclear power equipment, etc. In addition to the mechanical properties specified in the standards, these components also have some special performance requirements, such as low-temperature impact toughness required for wind power castings, and many additional special acceptance standards for nuclear slag tanks. Therefore, the production of these castings must be carefully considered in advance.
1) The first thing to consider is how to obtain a sound, dense, and qualified size casting
The technical process of producing large spheroidal graphite cast iron parts is basically the same as that of gray cast iron parts, as long as the selection of the scale and the design of the flask are slightly modified in accordance with the characteristics of the spheroidal graphite cast iron.
2) Secondly, corresponding work should be done for the common characteristics of large ductile iron castings
The common feature of large-scale ductile iron castings is that they are extremely heavy. Most of them require ferrite matrix, mechanical properties must meet standard data, and sometimes low-temperature impact performance requirements are added.
Special problems in the production of large ductile iron castings
Due to the slow cooling rate of large-scale ductile iron parts, the eutectic solidification period is as long as several hours. During this period, the main structure of ductile iron will be formed. Therefore, a series of problems unique to large-section ductile iron or large-scale ductile iron parts appear. :Small number of nodular ink, large diameter of nodular ink, distortion of nodular ink, graphite floating, segregation of chemical composition, intercrystalline carbides, and chunky graphite (Chunky Graphite), etc. These problems have long attracted attention. Although the formation mechanism is not unified, preliminary measures have been taken to solve specific problems.
Another important question is how to meet and solve the requirements of low-temperature impact toughness? The coincidence of the problem is that the directions and measures to solve these two problems are roughly the same.
Ways to solve the unique problems of large ductile iron castings
1) Intensified cooling to accelerate solidification
There are two generally accepted theories about the cause of fragmented graphite: one is caused by the crushing of spheroidal graphite; the other is that the stability of the austenite shell is reduced due to heat flow or segregation of certain alloying elements, especially Ce and La. Causes the growth pattern of spheroidal ink to change and form. Regardless of the theory or theory, it is certain that too long solidification time (ie slow cooling) in the eutectic stage is a direct and objective factor for the formation of fragmented graphite. Therefore, no matter what method is adopted, as long as the time of the solidification stage can be shortened, the appearance of fragmented graphite can be effectively prevented.
It is also pointed out in the literature that there is a critical cooling rate (0.8 ℃/min) for spheroidal ink distortion. Graphite distortion is sometimes an abrupt process, so accelerating cooling, shortening the solidification time, especially shortening the solidification time of the eutectic stage, find ways to shorten the eutectic solidification stage to less than 2 h, which has a significant effect. There are many measures around this principle: forced cooling; metal type hanging sand; use of cold iron and so on.
The high thermal conductivity of cold iron, especially the strong heat storage capacity, is widely considered to be a powerful measure that can be applied. The thermal conductivity of graphite is higher than that of sand-mounted chilled iron (45W/m•℃ and 17 W/m•℃ respectively), but its heat storage capacity is lower than that of chilled iron. If there is forced cooling, graphite is used for comparison. suitable. For large or extra large ductile iron castings, forced cooling is still a powerful measure. Generally, air-cooled, mist-cooled or water-cooled devices can be used, and even liquid nitrogen cooling can be used to accelerate the solidification rate of castings. Data shows that when the 20 t grade ductile iron spent container casting is solidified, the heat transfer effect is: metal type heat absorption accounts for 58%, graphite and sand mold (core part) heat absorption accounts for 3.5%, and sand mold and other devices partly absorb heat. Heat accounted for 3.5%, and water-cooled heat conduction accounted for 3.5%. It can be seen that the metal mold can conduct more than 50% of the heat of the casting, while the core part transfers little heat. Obviously, forced cooling is necessary.
2) Improve process technology
(1) Carefully select raw materials
In order to produce high-quality large-scale ductile iron parts, it is worthwhile to select the furnace charge no matter how. The interference elements of the raw materials should be as low as possible. Special attention should be paid to the source of pig iron, the type of scrap steel, and the selection of recarburizers.
(2) Chemical composition design
CE should not be too high (4.2%~4.3%), if w(C) is 3.6%~3.7%, w(Si) must be as low as 1.8%~2.0%; in addition, w(Mn)<0.3%, w( P) and w(S) should also be strictly restricted. Except in special circumstances, alloys are generally not used, so scrap steel must be strictly selected.
Low w(Si) must be achieved, otherwise fragmented graphite will easily appear, and low-temperature performance will not meet the requirements. The problem lies in the low w(Si) or low w(Si) And the ills that arise. The composition of 100-ton spent fuel containers in Japan is: w(C) 3.6%, w(Si) 2.01%, w(Mn) 0.27%, w(P) 0.025%, w(S) 0.004%, w(Ni) 0.78 %, w(Mg) 0.065%.
(3) Choose duplex smelting
Duplex smelting can give full play to the strong nucleation ability of cupola molten iron and high thermal efficiency of electric furnace. The molten iron must be discharged at a high temperature, and S can be removed when possible, and the time in the electric furnace should not be too long. The spheroidization temperature is determined according to the situation, and cannot be too high or too low.
The author advocates not to use the flushing method for spheroidization of large pieces because it takes too long. At least use the cover method, preferably the special method or the silk feeding method. The silk is fed in a fixed place, and it can even be fed together with the fertile silk. Do not use commonly used spheroidizing agents. It is best to mix heavy rare earth spheroidizing agents and light rare earth spheroidizing agents. If the spheroidizing agent is used, w (Mg) 6% and w (RE) 1.0% to 1.5% are sufficient; if the pig iron is relatively pure, w (RE) 0.5% to 1.0% is also acceptable. If the wire feeding method is used, a spheroidizing agent with a high w (Mg) amount can be used, but w (RE) should be low, with a little Ca.
The pouring temperature should be appropriate (1300~1350 ℃), not too high, otherwise the liquid shrinkage will be too large; it is advisable to use the dispersed inner runner for medium-speed pouring, and use high-rigidity molds as much as possible to make full use of the graphitization expansion for self-feeding of ductile iron. , To reduce the burden on the riser and ensure the inner compactness of the casting.
(4) Pay attention to the problem of pregnancy
Inoculation is one of the most important technological measures. Only by solving this problem can it be possible to ensure low w (Si) content without problems, and to ensure low-temperature performance. The problem of inoculation is nothing more than the choice of inoculants and inoculation treatment methods. You can choose an inoculant with a long inoculation time, such as a Ba-containing agent (Sr-containing agent is more effective for gray cast iron and lower Ca), a graphite-containing inoculant, or an appropriate mixture of RESiFe in the inoculant.
At present, many companies have self-made inoculants, and I guess they follow this principle. In short, the incubation "must be delayed, but instantaneous", not only the effect is good, but the dosage can be greatly reduced. The old method, such as covering during treatment, has very poor effect, but w(Si) is lowered. The problem now is that if w (Si) is to be low and the effect is to be good, the only way out is to change the method. Facts have proved that 2.0% of w (Si) is achievable, and the sign of success is that graphite should be smaller and larger. If it is smaller, the spheroidization rate will be higher. If it is smaller, no cementite will be produced. If it is smaller, the degree of segregation will be lighter. For large parts, if the number of graphite balls is 200 pieces/mm2 or more, and the size is 5-6, the spheroidization rate and the amount of ferrite will naturally not be a problem. In a word, the main method to fight against graphite and strive for smaller and more graphite is through inoculation. The w(Si) is low, and there is no free cementite, the plasticity and the impact toughness at room temperature and low temperature are easy to pass. For large castings, it is easy to carry out a large inoculation process in the pouring cup and to put an inoculation block in the runner. The problem is that there must be a correct concept.
(5) Utilization of alloys and trace elements
The only alloying element that can be considered for use in extra-large ductile iron castings is Ni, because of its unique effect. From a technical point of view, w(Ni)<1% is beneficial, but whether it is used or not depends on specific circumstances and economic considerations.
Microelements have mature use experience in large items are Bi and Sb. It is believed that adding w(Bi) 0.008%~0.010%, so that w(RE)/w(Bi)=1.4~1.5 ratio, to increase the number of balls, It is beneficial to reduce the risk of fragmented graphite. Sb can also be used in thick and bulky parts. Some people think that it will increase the amount of pearlite, but some people use it in ferritic ductile iron. It may be a problem with the amount, and the amount of 50 ppm should be no problem. Professor Zhou Jiyang once pointed out that using w(Sb) 0.005%~0.007% can also inhibit the harmful effects of excessive Ti and RE in molten iron.
Although the industry's opinions on the role and mechanism of the addition of Bi and Sb are still not unified, a consensus has been formed on the addition of Ni.
(6) The role of pretreatment is critical
Pretreatment of nodular iron stock solution with graphite pretreatment agent before spheroidization has a positive effect of improving and stabilizing the quality of castings [3]. Methods as below:
After adjusting the composition [pretreatment will increase w(C) by 0.2%] → de-S → return to the electric furnace → add 0.2% to 0.25% of pretreatment agent when 1/4 volume is added → return to the electric furnace and then slightly increase the temperature to 1 470 ~1 480 ℃ → spheroidizing treatment → inoculation treatment (Ultraseed available) → pouring.
(7) Use of anti-crater agent QKS
The inventor believes that there is a 1 μm foreign inclusion in the center of the spheroidal ink, forming a double-layer core; the inner layer is MgS, CaS (0.5 μm), and the outer layer is MgO, SiO, and silicate. Therefore, the inventor added a certain amount of O and S to the inoculant to combine with the metal elements in the inoculant to produce more sulfides and oxides, thereby forming more graphite cores, which produces Ferrosilicon inoculant of Ca, Ce and S, O. This inoculant can significantly increase the number of graphite spheres, and it precipitates in the late stage of crystallization, and the later period of graphitization expansion can effectively offset the shrinkage in the late stage of solidification. In particular, it is more effective for shrinkage porosity of local hot joints [4]. The experiment pointed out: for the stepped test block of 5-40 mm, when SrSiFe is used, the graphite balls are reduced from 300/mm2 to 150/mm2; when Ca-Ce-O-S agent is used, the number of graphite balls is not affected by the wall thickness. Compared with BaSiFe and 75SiFe. The shrinkage defect on the hot joints of the cross test block shows that there are shrinkage holes at the hot joints of the cross section with the inoculant containing Ba and Sr, while the Ca-Ce-O-S agent does not.
Please keep the source and address of this article for reprinting: The Ways To Solve The Special Problems Of Large Ductile Iron Castings
Minghe Casting Company are dedicated to manufacture and provide quality and high performance Casting Parts(metal die casting parts range mainly include Thin-Wall Die Casting,Hot Chamber Die Casting,Cold Chamber Die Casting),Round Service(Die Casting Service,Cnc Machining,Mold Making,Surface Treatment).Any custom Aluminum die casting, magnesium or Zamak/zinc die casting and other castings requirements are welcome to contact us.
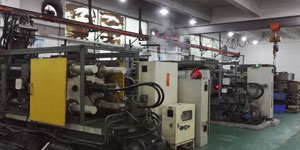
Under the control of ISO9001 and TS 16949,All processes are carried out through hundreds of advanced die casting machines, 5-axis machines, and other facilities, ranging from blasters to Ultra Sonic washing machines.Minghe not only has advanced equipment but also have professional team of experienced engineers,operators and inspectors to make the customer’s design come true.
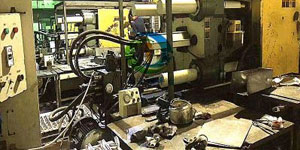
Contract manufacturer of die castings. Capabilities include cold chamber aluminum die casting parts from 0.15 lbs. to 6 lbs., quick change set up, and machining. Value-added services include polishing, vibrating, deburring, shot blasting, painting, plating, coating, assembly, and tooling. Materials worked with include alloys such as 360, 380, 383, and 413.
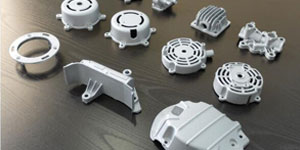
Zinc die casting design assistance/concurrent engineering services. Custom manufacturer of precision zinc die castings. Miniature castings, high pressure die castings, multi-slide mold castings, conventional mold castings, unit die and independent die castings and cavity sealed castings can be manufactured. Castings can be manufactured in lengths and widths up to 24 in. in +/-0.0005 in. tolerance.
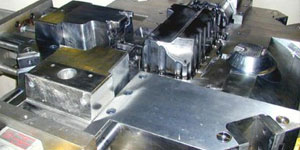
ISO 9001: 2015 certified manufacturer of die cast magnesium, Capabilities include high-pressure magnesium die casting up to 200 ton hot chamber & 3000 ton cold chamber, tooling design, polishing, molding, machining, powder & liquid painting, full QA with CMM capabilities, assembly, packaging & delivery.
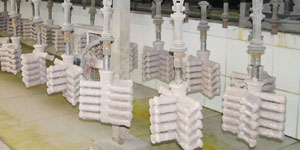
ITAF16949 certified. Additional Casting Service Include investment casting,sand casting,Gravity Casting, Lost Foam Casting,Centrifugal Casting,Vacuum Casting,Permanent Mold Casting,.Capabilities include EDI, engineering assistance, solid modeling and secondary processing.
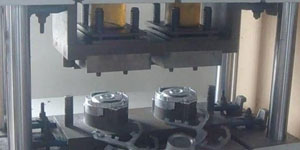
Casting Industries Parts Case Studies for: Cars, Bikes, Aircraft, Musical instruments, Watercraft, Optical devices, Sensors, Models, Electronic devices, Enclosures, Clocks, Machinery, Engines, Furniture, Jewelry, Jigs, Telecom, Lighting, Medical devices, Photographic devices, Robots, Sculptures, Sound equipment, Sporting equipment, Tooling, Toys and more.
What Can we help you do next?
∇ Go To Homepage For Die Casting China
→Casting Parts-Find out what we have done.
→Ralated Tips About Die Casting Services
By Minghe Die Casting Manufacturer |Categories: Helpful Articles |Material Tags: Aluminum Casting, Zinc Casting, Magnesium Casting, Titanium Casting, Stainless Steel Casting, Brass Casting,Bronze Casting,Casting Video,Company History,Aluminum Die Casting |Comments Off