Thoughts On Research And Development Of Stainless Steel Smelting
- The initial carbon content of stainless steel smelting is relatively high, which improves the activity coefficient of phosphorus and reduces the activity coefficient of chromium, which is beneficial to dephosphorization and chromium preservation. The initial carbon allocation of some foreign manufacturers has reached 1.9%. The high carbon content is beneficial to reduce the oxidation of chromium in the melting process, and reduce or eliminate the operation of adding reducing agent to the surface of the molten pool during the melting process.
- The use of carbon oxidation exothermic can reduce power consumption, which is in line with the development trend of metallurgical technology. Moreover, it is easier to decarburize in the high carbon content area, and decarburization will not become too much burden in modern electric arc furnace steelmaking technology. The development of modern electric arc furnace steelmaking technology has made it possible to dephosphorize stainless steel in the electric arc furnace. In addition to changing the smelting process conditions, the use of DC electric arc furnace steelmaking technology can also promote dephosphorization due to electrochemical reactions.
- It is possible to combine foam slag technology, smelting reduction technology, direct alloying and dephosphorization technology to develop a new process flow.
- Develop the top-bottom combined blowing converter smelting process for stainless steel, and use the returned stainless steel scraps as ingredients only.
- For electric arc furnace steelmaking plants, the production organization of stainless steel should be done well, using carbon steel dephosphorization, or low-phosphorus, sulfur molten steel plus scrap steel, and then adding stainless steel return material for stainless steel production process to ensure the phosphorus of the product Content requirements. Of course, this requires the use of the return method to produce stainless steel production plants, change the traditional stainless steel production process without dephosphorization, and re-coordinate the feeding, melting, and refining processes. The use of molten iron in electric arc furnaces can not only alleviate the shortage of scrap steel in our country, but also an important energy-saving measure that meets the requirements of technological progress.
- Due to the high viscosity of chromium-containing slag, precise control technology of chromium oxide in the slag should be developed.
- Continue to develop stainless steel and high-chromium alloy dephosphorization technology. Combined with the development trend of metallurgical process, the dephosphorization process system will be studied.
Please keep the source and address of this article for reprinting: Thoughts On Research And Development Of Stainless Steel Smelting
Minghe Die Casting Company are dedicated to manufacture and provide quality and high performance Casting Parts(metal die casting parts range mainly include Thin-Wall Die Casting,Hot Chamber Die Casting,Cold Chamber Die Casting),Round Service(Die Casting Service,Cnc Machining,Mold Making,Surface Treatment).Any custom Aluminum die casting, magnesium or Zamak/zinc die casting and other castings requirements are welcome to contact us.
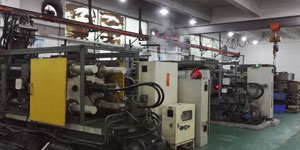
Under the control of ISO9001 and TS 16949,All processes are carried out through hundreds of advanced die casting machines, 5-axis machines, and other facilities, ranging from blasters to Ultra Sonic washing machines.Minghe not only has advanced equipment but also have professional team of experienced engineers,operators and inspectors to make the customer’s design come true.
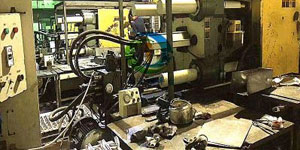
Contract manufacturer of die castings. Capabilities include cold chamber aluminum die casting parts from 0.15 lbs. to 6 lbs., quick change set up, and machining. Value-added services include polishing, vibrating, deburring, shot blasting, painting, plating, coating, assembly, and tooling. Materials worked with include alloys such as 360, 380, 383, and 413.
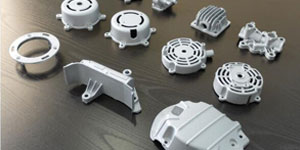
Zinc die casting design assistance/concurrent engineering services. Custom manufacturer of precision zinc die castings. Miniature castings, high pressure die castings, multi-slide mold castings, conventional mold castings, unit die and independent die castings and cavity sealed castings can be manufactured. Castings can be manufactured in lengths and widths up to 24 in. in +/-0.0005 in. tolerance.
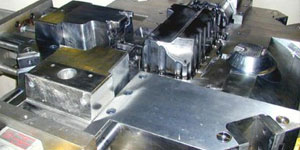
ISO 9001: 2015 certified manufacturer of die cast magnesium, Capabilities include high-pressure magnesium die casting up to 200 ton hot chamber & 3000 ton cold chamber, tooling design, polishing, molding, machining, powder & liquid painting, full QA with CMM capabilities, assembly, packaging & delivery.
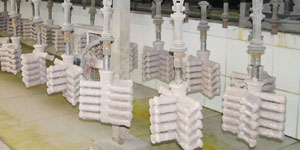
ITAF16949 certified. Additional Casting Service Include investment casting,sand casting,Gravity Casting, Lost Foam Casting,Centrifugal Casting,Vacuum Casting,Permanent Mold Casting,.Capabilities include EDI, engineering assistance, solid modeling and secondary processing.
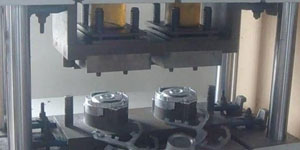
Casting Industries Parts Case Studies for: Cars, Bikes, Aircraft, Musical instruments, Watercraft, Optical devices, Sensors, Models, Electronic devices, Enclosures, Clocks, Machinery, Engines, Furniture, Jewelry, Jigs, Telecom, Lighting, Medical devices, Photographic devices, Robots, Sculptures, Sound equipment, Sporting equipment, Tooling, Toys and more.
What Can we help you do next?
∇ Go To Homepage For Die Casting China
→Casting Parts-Find out what we have done.
→Ralated Tips About Die Casting Services
By Minghe Die Casting Manufacturer |Categories: Helpful Articles |Material Tags: Aluminum Casting, Zinc Casting, Magnesium Casting, Titanium Casting, Stainless Steel Casting, Brass Casting,Bronze Casting,Casting Video,Company History,Aluminum Die Casting |Comments Off