Three Key Factors Of Mold Deformation
At present, in mold manufacturing, new technologies such as electric discharge machining, form grinding, wire cutting, etc. have been applied to better solve the problems of complex mold processing and heat treatment deformation. However, these new processes have not yet been widely used due to various constraints. Therefore, how to reduce the heat treatment deformation of the mold is still a very important issue.
Generally, molds require high precision. After heat treatment, it is inconvenient or even impossible to process and correct. Therefore, after heat treatment, even if the structure and performance have reached the requirements, if the deformation is out of tolerance, it will still be scrapped because it cannot be saved. Not only affects production, but also causes economic losses.
The general law of heat treatment deformation is not discussed here. The following is a brief analysis of some factors affecting mold deformation.
The influence of mold material on heat treatment deformation
The influence of materials on heat treatment deformation includes the influence of the chemical composition of steel and the original structure.
From the point of view of the material itself, the heat treatment deformation is mainly affected by the influence of the composition on the hardenability and Ms point.
When carbon tool steel is quenched with water and oil at the normal quenching temperature, a large thermal stress is generated above the Ms point; when it is cooled below the Ms point, austenite transforms to martensite, resulting in structural stress, but Due to the poor hardenability of carbon tool steel, the value of the structural stress is not large. In addition, the Ms point is not high. When the martensite transformation occurs, the plasticity of the steel is already very poor and plastic deformation is not easy to occur. Therefore, the deformation characteristics caused by thermal stress are retained, and the mold cavity tends to shrink. However, if the quenching temperature is increased (>850°C), the structure stress may also play a leading role, and the cavity tends to expand.
When making molds with low alloy tool steels such as 9Mn2V, 9SiCr, CrWMn, GCr15 steel, the quenching deformation law is similar to that of carbon tool steel, but the amount of deformation is smaller than that of carbon tool steel.
For some high-alloy steels, such as Cr12MoV steel, due to its high content of carbon and alloying elements and low Ms point, there is more retained austenite after quenching, which has a significant effect on the volume expansion due to martensite. Therefore, the deformation after quenching is quite small. Generally, when quenching with air cooling, air cooling, and nitrate salt bath, the mold cavity tends to expand slightly; if the quenching temperature is too high, the amount of retained austenite will increase. The cavity may also shrink.
If the mold is made of carbon structural steel (such as 45 steel) or some alloy structural steel (such as 40Cr), because of its high Ms point, when the surface starts to transform into martensite, the core temperature is still higher, and the yield strength It is low and has a certain degree of plasticity. The instantaneous tensile tissue stress of the surface to the core easily exceeds the yield strength of the core and the cavity tends to swell.
The original structure of steel also has a certain influence on quenching deformation. The "primary structure of steel" referred to here includes the level of inclusions in the steel, the level of banded structure, the degree of segregation of components, the directionality of the distribution of free carbides, etc., as well as the different structures obtained due to different pre-heat treatments ( Such as pearlite, tempered sorbite, tempered troostite, etc.). For die steel, the main consideration is the segregation of carbides, the shape and distribution of carbides.
The effect of carbide segregation in high-carbon and high-alloy steel (such as Cr12 steel) on quenching deformation is particularly obvious. As the carbide segregation causes the compositional inhomogeneity of the steel after heating to the austenite state, the Ms points in different regions will be high or low. Under the same cooling conditions, the transformation of austenite to martensite occurs first, and the specific volume of the transformed martensite varies depending on the carbon content, and even some low-carbon and low-alloy regions may There is no martensite (but bainite, troostite, etc.), all of which will cause uneven deformation of the parts after quenching.
Different carbide distribution forms (distributed in granular or fibrous form) have different effects on the expansion and contraction of the matrix, which will also affect the deformation after heat treatment. Generally, the cavity expands along the direction of the carbide fibers, and it is more obvious While the direction perpendicular to the fiber is reduced, but not significant. Some factories have made special regulations for this. The surface of the cavity should be perpendicular to the direction of the carbide fiber to reduce the deformation of the cavity. When the carbide is granular When it is evenly distributed, the cavity shows uniform expansion and contraction.
In addition, the state of the structure before the final heat treatment also has a certain influence on the deformation. For example, the original structure of spherical pearlite has a smaller tendency to deform after quenching than the flaky pearlite. Therefore, molds with strict deformation requirements are often subjected to quenching and tempering treatment after rough machining, and then finishing and final heat treatment.
The influence of mold geometry on deformation
The influence of mold geometry on heat treatment deformation actually works through thermal stress and organizational stress. Since the shape of the mold is diverse, it is still difficult to sum up the exact deformation law from it.
For symmetrical molds, the deformation tendency of the cavity can be considered according to the cavity size, shape size and height. When the wall of the mold is thin and the height is small, it is easier to quench through. At this time, it is possible that the tissue stress plays a leading role. Therefore, the cavity often tends to swell. On the contrary, if the wall thickness and height are large, it is not easy to harden. At this time, thermal stress may play a leading role. Therefore, the cavity often tends to shrink. What is mentioned here is a general trend. In the production practice, it is necessary to consider the specific shape of the part, the steel grade and the heat treatment process, etc., and continuously summarize the experience through practice. In actual production, the external dimensions of the mold are often not the main working dimensions, and the deformation can be corrected by grinding, etc., so the main analysis above is the deformation trend of the cavity.
The deformation of asymmetrical molds is also the result of the combined effects of thermal stress and tissue stress. For example, for a thin-walled and thin-sided mold, because the mold wall is thin, the temperature difference between the inside and the outside is small during quenching, so the thermal stress is small; but it is easy to be quenched and the structure stress is large, so the deformation tends to expand the cavity.
In order to reduce the deformation of the mold, the heat treatment department should work with the mold design department to improve the mold design, such as avoiding mold structures with large differences in cross-sectional size, symmetrical mold shapes, and split structures for complex molds.
When the mold shape cannot be changed, in order to reduce the deformation, some other measures can be taken. The general consideration of these measures is to improve the cooling conditions so that each part can be cooled uniformly; in addition, various compulsory measures can also be assisted to limit the quenching deformation of the parts. For example, adding process holes is a measure for uniform cooling of each part, that is, opening holes in some parts of the mold, so that each part of the mold can be uniformly cooled to reduce deformation. It can also be wrapped with asbestos on the periphery of the mold that is easy to expand after quenching to increase the cooling difference between the inner hole and the outer layer and shrink the cavity. Retaining ribs or reinforcing ribs on the mold is another compulsory measure to reduce deformation. It is especially suitable for die with swelling cavity and die with notch that is easy to expand or shrink.
The influence of heat treatment process on mold deformation
1. The influence of heating speed
Generally speaking, during quenching heating, the faster the heating speed, the greater the thermal stress generated in the mold, which is likely to cause deformation and cracking of the mold. Especially for alloy steel and high alloy steel, due to their poor thermal conductivity, special attention should be paid to preheating For some high-alloy molds with complex shapes, it is necessary to take multiple preheating steps. However, in individual cases, rapid heating can sometimes reduce deformation. At this time, only the surface of the mold is heated, while the center remains "cold", so the tissue stress and thermal stress are correspondingly reduced, and the deformation resistance of the core is greater. , Thereby reducing the quenching deformation, according to some factory experience, used to solve the hole pitch deformation has a certain effect.
2. The influence of heating temperature
The quenching heating temperature affects the hardenability of the material, and at the same time affects the composition and grain size of austenite.
- (1) From the perspective of hardenability, high heating temperature will increase the thermal stress, but at the same time increase the hardenability, so the structural stress also increases, and gradually dominates.E.g. For carbon tool steels T8, T10, T12, etc., when quenched at general quenching temperature, the inner diameter shows a tendency to shrink, but if the quenching temperature is increased to ≥850°C, the hardenability increases and the structural stress gradually becomes dominant , So the inner diameter may show a tendency to swell.
- (2) From the perspective of austenite composition, the increase in quenching temperature increases the austenite carbon content, and the squareness of martensite after quenching (increased specific volume), which increases the volume after quenching.
- (3) From a closer look at the effect on the Ms point, the higher the quenching temperature, the coarser austenite grains, which will increase the deformation and cracking tendency of the parts.
In summary, for all steel grades, especially some high-carbon medium and high alloy steels, the quenching temperature will obviously affect the quenching deformation of the mold. Therefore, the correct selection of the quenching heating temperature is very important.
Generally speaking, choosing too high a quenching heating temperature is not good for deformation. Under the premise of not affecting the performance, a lower heating temperature is always used. However, for some steel grades with more retained austenite after quenching (such as Cr12MoV, etc.), the amount of retained austenite can also be adjusted by adjusting the heating temperature to adjust the deformation of the mold.
3. The influence of quenching cooling rate
In general, increasing the cooling rate above the Ms point will significantly increase the thermal stress, and as a result, the deformation caused by the thermal stress tends to increase; increasing the cooling rate below the Ms point mainly causes the deformation caused by the tissue stress to tend Increase.
For different steel grades, due to the different heights of the Ms points, when the same quenching medium is used, there are different deformation tendencies. For the same steel grade, if different quenching media are used, they also have different deformation tendencies due to their different cooling capabilities.
For example, the Ms point of carbon tool steel is relatively low, so when water cooling is used, the influence of thermal stress tends to prevail; when cooling is used, the structural stress may prevail.
In actual production, molds are usually not fully quenched when they are graded or graded-austempered, so thermal stress is often the main effect, which tends to shrink the cavity. However, because the thermal stress is not very large at this time, Therefore, the total deformation is relatively small. If water-oil double-liquid quenching or oil quenching is used, the thermal stress caused is greater, and the cavity shrinkage will increase.
4. The influence of tempering temperature
The effect of tempering temperature on deformation is mainly caused by the transformation of the structure during the tempering process. If the phenomenon of "secondary quenching" occurs during the tempering process, the retained austenite is transformed into martensite, and the specific volume of the martensite generated is larger than that of the retained austenite, which will cause the mold cavity to expand; For some high-alloy tool steels, such as Cr12MoV, high temperature quenching is used to require red hardness as the main requirement. When multiple tempering, the volume expands once every time the tempering is performed.
If tempered in other temperature regions, the specific volume decreases due to the transformation of quenched martensite to tempered martensite (or tempered sorbite, tempered troostite, etc.), and therefore, the cavity tends to shrink.
In addition, during tempering, the relaxation of the residual stress in the mold also affects the deformation. After the mold is quenched, if the surface is in a state of tensile stress, the size will increase after tempering; on the contrary, if the surface is in a state of compressive stress, it will shrink. But of the two effects of organizational transformation and stress relaxation, the former is the main one.
Please keep the source and address of this article for reprinting: Three Key Factors Of Mold Deformation
Minghe Die Casting Company are dedicated to manufacture and provide quality and high performance Casting Parts(metal die casting parts range mainly include Thin-Wall Die Casting,Hot Chamber Die Casting,Cold Chamber Die Casting),Round Service(Die Casting Service,Cnc Machining,Mold Making,Surface Treatment).Any custom Aluminum die casting, magnesium or Zamak/zinc die casting and other castings requirements are welcome to contact us.
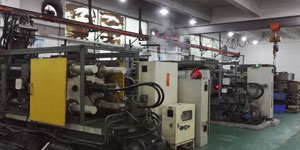
Under the control of ISO9001 and TS 16949,All processes are carried out through hundreds of advanced die casting machines, 5-axis machines, and other facilities, ranging from blasters to Ultra Sonic washing machines.Minghe not only has advanced equipment but also have professional team of experienced engineers,operators and inspectors to make the customer’s design come true.
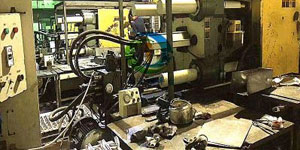
Contract manufacturer of die castings. Capabilities include cold chamber aluminum die casting parts from 0.15 lbs. to 6 lbs., quick change set up, and machining. Value-added services include polishing, vibrating, deburring, shot blasting, painting, plating, coating, assembly, and tooling. Materials worked with include alloys such as 360, 380, 383, and 413.
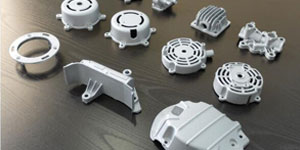
Zinc die casting design assistance/concurrent engineering services. Custom manufacturer of precision zinc die castings. Miniature castings, high pressure die castings, multi-slide mold castings, conventional mold castings, unit die and independent die castings and cavity sealed castings can be manufactured. Castings can be manufactured in lengths and widths up to 24 in. in +/-0.0005 in. tolerance.
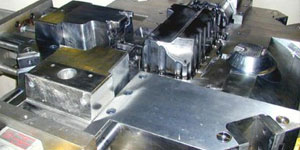
ISO 9001: 2015 certified manufacturer of die cast magnesium, Capabilities include high-pressure magnesium die casting up to 200 ton hot chamber & 3000 ton cold chamber, tooling design, polishing, molding, machining, powder & liquid painting, full QA with CMM capabilities, assembly, packaging & delivery.
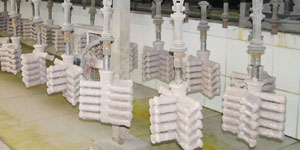
ITAF16949 certified. Additional Casting Service Include investment casting,sand casting,Gravity Casting, Lost Foam Casting,Centrifugal Casting,Vacuum Casting,Permanent Mold Casting,.Capabilities include EDI, engineering assistance, solid modeling and secondary processing.
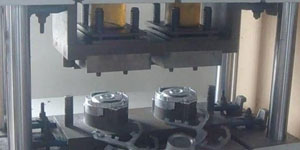
Casting Industries Parts Case Studies for: Cars, Bikes, Aircraft, Musical instruments, Watercraft, Optical devices, Sensors, Models, Electronic devices, Enclosures, Clocks, Machinery, Engines, Furniture, Jewelry, Jigs, Telecom, Lighting, Medical devices, Photographic devices, Robots, Sculptures, Sound equipment, Sporting equipment, Tooling, Toys and more.
What Can we help you do next?
∇ Go To Homepage For Die Casting China
→Casting Parts-Find out what we have done.
→Ralated Tips About Die Casting Services
By Minghe Die Casting Manufacturer |Categories: Helpful Articles |Material Tags: Aluminum Casting, Zinc Casting, Magnesium Casting, Titanium Casting, Stainless Steel Casting, Brass Casting,Bronze Casting,Casting Video,Company History,Aluminum Die Casting |Comments Off