Three Keys To Improve The Spheroidization Rate And Ductile Iron Graphite Roundness
There are many factors that affect the spheroidization rate and roundness of ductile cast iron. The following analyzes the factors that affect the spheroidization rate from the three aspects of chemical composition, process, and solidification control:
Chemical Composition
1. Carbon equivalent and silicon
Carbon and silicon are the basic components that affect the roundness of nodular iron graphite spheres. Under a certain cooling rate and incubation conditions, increasing the carbon equivalent can increase the roundness of the graphite sphere, increase the self-feeding capacity, and reduce carbides. Under certain carbon equivalent conditions, as the amount of silicon increases, especially large section ductile iron, fragmented graphite will be produced. Therefore, in the case of no graphite floating, the carbon equivalent should be increased as much as possible; at the same time, the silicon content should be reduced as much as possible under the guarantee of incubation conditions.
2. Magnesium
The control of the effective residual magnesium content is very important to improve the roundness of the graphite spheres. When the effective residual magnesium is less than 0.045%, increasing the amount of effective residual magnesium can improve the roundness of the graphite sphere; when the effective residual magnesium is greater than 0.045%, metamorphic graphite will be produced and the roundness of the graphite sphere will be reduced.
3. Rare earth
Rare earth has two beneficial effects in molten iron: one is desulfurization and degassing, playing the role of spheroidization and indirect spheroidization; the second is interacting with trace elements to eliminate harmful aspects and play a positive side. Both of these aspects can improve the roundness of the graphite ball. However, excessive residual rare earths, especially large-section ductile iron, will deteriorate the morphology of graphite, especially lumps. The ideal range is 0.010% to 0.019%.
4. Trace elements
A certain amount of antimony and bismuth combined with a proper amount of rare earth can improve the roundness of the graphite sphere and improve the mechanical properties. Appropriate adding range: 0.0025~0.005%.
The Process
1. Spheroidization
- Heavy rare earth magnesium spheroidizing agent can improve the roundness of graphite spheres better than light rare earth magnesium spheroidizing agent. Mainly because of its strong desulfurization ability and strong anti-decay ability.
- If the light rare earth magnesium spheroidizing agent is well controlled and supplemented with trace elements, it can also improve the roundness of graphite spheres.
- The quality of molten iron is better than the subcontracting method, so it can also improve the roundness of graphite spheres.
2. Inoculation treatment
- Intensified inoculation can improve the roundness of graphite balls.
- The use of anti-fading inoculants can improve the roundness of graphite balls.
- Using ductile iron filings as a covering agent for spheroidization can form a passivated graphite core similar to the dispersion of non-dissolved graphite, produce long-term concentration fluctuations, greatly increase the effective nucleation rate, and improve the roundness of graphite spheres. degree.
- Minimizing the pouring temperature can improve the roundness of graphite balls.
3.Coagulation Control
- Using cold iron can improve the roundness of graphite balls.
- The use of chromite sand can improve the roundness of graphite balls.
- Other measures that can speed up the cooling and shorten the time during the eutectic transformation of ductile iron can improve the roundness of graphite spheres.
Please keep the source and address of this article for reprinting: Three Keys To Improve The Spheroidization Rate And Ductile Iron Graphite Roundness
Minghe Die Casting Company are dedicated to manufacture and provide quality and high performance Casting Parts(metal die casting parts range mainly include Thin-Wall Die Casting,Hot Chamber Die Casting,Cold Chamber Die Casting),Round Service(Die Casting Service,Cnc Machining,Mold Making,Surface Treatment).Any custom Aluminum die casting, magnesium or Zamak/zinc die casting and other castings requirements are welcome to contact us.
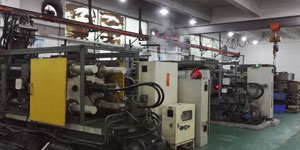
Under the control of ISO9001 and TS 16949,All processes are carried out through hundreds of advanced die casting machines, 5-axis machines, and other facilities, ranging from blasters to Ultra Sonic washing machines.Minghe not only has advanced equipment but also have professional team of experienced engineers,operators and inspectors to make the customer’s design come true.
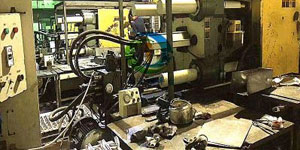
Contract manufacturer of die castings. Capabilities include cold chamber aluminum die casting parts from 0.15 lbs. to 6 lbs., quick change set up, and machining. Value-added services include polishing, vibrating, deburring, shot blasting, painting, plating, coating, assembly, and tooling. Materials worked with include alloys such as 360, 380, 383, and 413.
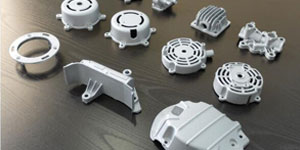
Zinc die casting design assistance/concurrent engineering services. Custom manufacturer of precision zinc die castings. Miniature castings, high pressure die castings, multi-slide mold castings, conventional mold castings, unit die and independent die castings and cavity sealed castings can be manufactured. Castings can be manufactured in lengths and widths up to 24 in. in +/-0.0005 in. tolerance.
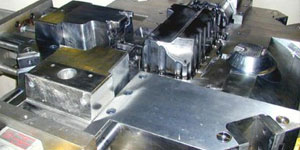
ISO 9001: 2015 certified manufacturer of die cast magnesium, Capabilities include high-pressure magnesium die casting up to 200 ton hot chamber & 3000 ton cold chamber, tooling design, polishing, molding, machining, powder & liquid painting, full QA with CMM capabilities, assembly, packaging & delivery.
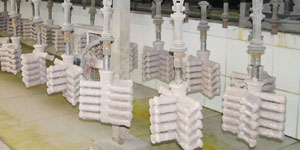
ITAF16949 certified. Additional Casting Service Include investment casting,sand casting,Gravity Casting, Lost Foam Casting,Centrifugal Casting,Vacuum Casting,Permanent Mold Casting,.Capabilities include EDI, engineering assistance, solid modeling and secondary processing.
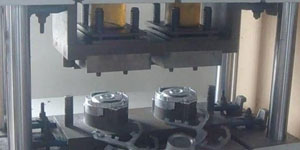
Casting Industries Parts Case Studies for: Cars, Bikes, Aircraft, Musical instruments, Watercraft, Optical devices, Sensors, Models, Electronic devices, Enclosures, Clocks, Machinery, Engines, Furniture, Jewelry, Jigs, Telecom, Lighting, Medical devices, Photographic devices, Robots, Sculptures, Sound equipment, Sporting equipment, Tooling, Toys and more.
What Can we help you do next?
∇ Go To Homepage For Die Casting China
→Casting Parts-Find out what we have done.
→Ralated Tips About Die Casting Services
By Minghe Die Casting Manufacturer |Categories: Helpful Articles |Material Tags: Aluminum Casting, Zinc Casting, Magnesium Casting, Titanium Casting, Stainless Steel Casting, Brass Casting,Bronze Casting,Casting Video,Company History,Aluminum Die Casting |Comments Off