Three Kinds Of Magnesium Alloy Injection Molding Technology
Magnesium alloy injection molding technology has become a research hotspot in the industry due to its many advantages. There are three kinds of injection molding technologies that have appeared recently: hot runner method, casting forging method and powder release agent.
The basic principle of injection molding is to melt the low melting point alloy, and then fill it into a metal mold at high speed and high pressure. The raw materials of the size of rice grains are fed from the feeding port, and then they are fed into the cylinder heated to the set temperature and transported to the front end. At this time, the shear force is increased by rotating the wire, and the alloy melt is made into a semi-molten state, and then injected into the metal mold at a high speed. The temperature of the alloy melt is maintained at 560 to 630°C, and the solid phase ratio is controlled. What Japan Steel introduces is the technology patent of American Thixomat Company, and manufactures and sells forming machines.
Compared with the die casting china method, the magnesium alloy injection molding method has a higher casting pressure, so the crystal grains near the surface are refined, so that high corrosion resistance and mechanical strength can be obtained. The reproducibility of the metal mold is also good. Because the temperature of the alloy melt is 50 to 70°C lower than that of the die-casting method, the size change of the molded product with the heat shrinkage can be controlled, thereby increasing the service life of the metal film. In addition, no melting furnace and SF6 flame-proof gas are used, explosion and dust will not occur, and it meets safety and environmental protection requirements.
The latest injection molding technology:
- Hot runner method: Frequently heat the runner in the metal mold to increase the yield of the material by maintaining the molten metal. It has the advantages of shortening the cycle time, processing multiple molds, and miniaturizing the molding machine.
- Casting forging method: Casting molded products are semi-finished products close to the shape of the finished product, and there is only one process of precision forging. It has the advantage of not producing cracks even at high speed forging.
- Powder release agent: generally spray water-soluble release agent, there is a phenomenon of release agent flying. Japan Steel Corporation has developed a method of vacuum absorption of powder release agent in a closed metal mold. It has the effect of shortening the cycle time and improving the life of the metal mold in a clean environment.
Please keep the source and address of this article for reprinting:Three Kinds Of Magnesium Alloy Injection Molding Technology
Minghe Die Casting Company are dedicated to manufacture and provide quality and high performance Casting Parts(metal die casting parts range mainly include Thin-Wall Die Casting,Hot Chamber Die Casting,Cold Chamber Die Casting),Round Service(Die Casting Service,Cnc Machining,Mold Making,Surface Treatment).Any custom Aluminum die casting, magnesium or Zamak/zinc die casting and other castings requirements are welcome to contact us.
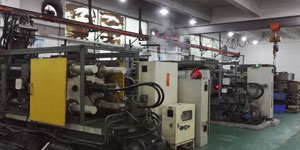
Under the control of ISO9001 and TS 16949,All processes are carried out through hundreds of advanced die casting machines, 5-axis machines, and other facilities, ranging from blasters to Ultra Sonic washing machines.Minghe not only has advanced equipment but also have professional team of experienced engineers,operators and inspectors to make the customer’s design come true.
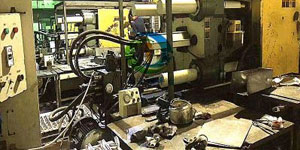
Contract manufacturer of die castings. Capabilities include cold chamber aluminum die casting parts from 0.15 lbs. to 6 lbs., quick change set up, and machining. Value-added services include polishing, vibrating, deburring, shot blasting, painting, plating, coating, assembly, and tooling. Materials worked with include alloys such as 360, 380, 383, and 413.
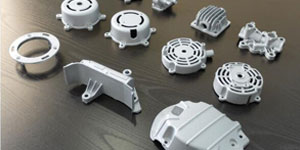
Zinc die casting design assistance/concurrent engineering services. Custom manufacturer of precision zinc die castings. Miniature castings, high pressure die castings, multi-slide mold castings, conventional mold castings, unit die and independent die castings and cavity sealed castings can be manufactured. Castings can be manufactured in lengths and widths up to 24 in. in +/-0.0005 in. tolerance.
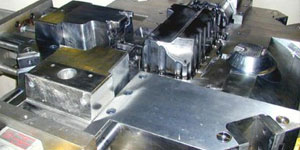
ISO 9001: 2015 certified manufacturer of die cast magnesium, Capabilities include high-pressure magnesium die casting up to 200 ton hot chamber & 3000 ton cold chamber, tooling design, polishing, molding, machining, powder & liquid painting, full QA with CMM capabilities, assembly, packaging & delivery.
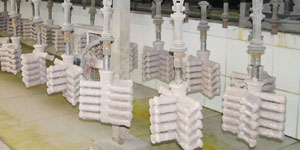
ITAF16949 certified. Additional Casting Service Include investment casting,sand casting,Gravity Casting, Lost Foam Casting,Centrifugal Casting,Vacuum Casting,Permanent Mold Casting,.Capabilities include EDI, engineering assistance, solid modeling and secondary processing.
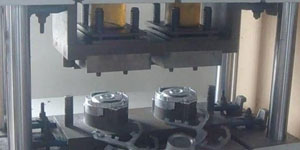
Casting Industries Parts Case Studies for: Cars, Bikes, Aircraft, Musical instruments, Watercraft, Optical devices, Sensors, Models, Electronic devices, Enclosures, Clocks, Machinery, Engines, Furniture, Jewelry, Jigs, Telecom, Lighting, Medical devices, Photographic devices, Robots, Sculptures, Sound equipment, Sporting equipment, Tooling, Toys and more.
What Can we help you do next?
∇ Go To Homepage For Die Casting China
→Casting Parts-Find out what we have done.
→Ralated Tips About Die Casting Services
By Minghe Die Casting Manufacturer |Categories: Helpful Articles |Material Tags: Aluminum Casting, Zinc Casting, Magnesium Casting, Titanium Casting, Stainless Steel Casting, Brass Casting,Bronze Casting,Casting Video,Company History,Aluminum Die Casting |Comments Off