Three Kinds Of Smelting And Pouring Schemes For Ductile Iron
Furan resin sand is generally used as the molding material for large-scale ductile iron castings produced in China. It is produced in a single piece, with heavy pouring weight and complex structure. It has high requirements on the quality and performance of castings. Some casting defects, especially shrinkage defects, often appear in the smelting process. It will cause the casting to be scrapped and cause major economic losses, especially the QT400-18AR material, which has high strength, high elongation, and impact value requirements.
While ensuring the mechanical properties of such thick and large parts, it is not easy to avoid graphite floating and shrinkage defects. Through the design of sample experiments, Elkem’s analytical equipment was used to study the effects of chemical composition and pouring temperature on the graphite floating, shrinkage and other defects of the solid sample with a wall thickness of 180mm. It is then applied to the production of ductile iron thick-walled parts to obtain good quality castings.
Equipment and materials are prepared for self-use high-purity pig iron, pure low-manganese scrap, high-magnesium spheroidizing agent, 75#FeSi inoculant; Elkem low-magnesium spheroidizing agent, inoculant; 1.5 tons of intermediate frequency melting furnace, 500kg spheroidizing bag, 500kg tundish. Elkem EPIC thermal analyzer, carbon and sulfur analyzer, spectrometer. The size of the solid sample wooden model is 600mm×400mm×180mm, and the process is trial-produced. The wall thickness of 180mm is used to cover the thick and large spheroidal graphite cast iron products produced by the company. It is quite representative. It is equipped with a riser and sprue system and adopts bottom pouring with a pouring weight of 500kg.
The smelting and pouring plan is designed to use a 1.5t smelting intermediate frequency furnace to melt 1.5t molten iron, 500kg each time spheroidizing inoculation, and pouring 1 box of small sample test pieces. A total of 3 boxes of test pieces were poured into 1 furnace. Different smelting and pouring schemes are designed as follows:
The first scheme charge ratio:
85% pig iron, 15% low-manganese steel scrap; chemical composition control: adopt spheroidizing inoculation treatment plan: firstly, 500kg iron is delivered to the tundish, and 1.3-1.5% high-magnesium spheroidizing agent, 0.3-0.4% inoculant and inoculant are embedded in the spheroidizing bag 0.8% covering agent, invert the bag for spheroidization. After the spheroidization process is completed, the inner surface of the bag is poured into the flow inoculant and completely smashed, and then the sample is analyzed and tested with the EPIC instrument. 1.2% Elkem spheroidizing agent, 0.8-1.0% covering agent, and 0.4% glass cullet are embedded in the spheroidizing bag, and iron is directly discharged into the spheroidizing bag, and 0.5% Elkem inoculant is put in at the same time. After the spheroidization is completed, the Elkem follow-up inoculant sprinkled on the surface will be sampled and analyzed using an EPIC instrument.
1.2% Elkem spheroidizing agent, 0.8-1.0% covering agent, and 0.4% glass cullet are embedded in the spheroidizing bag, and iron is directly discharged into the spheroidizing bag, and 0.5% Elkem inoculant is put in at the same time. After the spheroidization is completed, the Elkem follow-up inoculant sprinkled on the surface will be sampled and analyzed using an EPIC instrument.
The second scheme charge ratio: 65% pig iron, 35% low manganese scrap; chemical composition control:
C | Si | Mn | P | S | Cu | |
The first furnace | 3.7-3.9 | 0.6-0.75 | 0.1-0.25 | <0.05 | <0.02 |
Adopting the spheroidizing inoculation treatment plan: direct 500kg of iron to the tundish, embedded 1.2% Elkem nodulizer, 0.8-1.0% covering agent and 0.4% glass cullet in the spheroidizing bag, and direct iron to the nodularizing bag. Put in 0.5% Elkem inoculant. After the spheroidization process is completed, put Elkem's flow-through inoculant on the inner surface of the bag, smash it out completely, and use EPIC instrument for sampling for analysis and testing.
500kg of iron can be tapped directly to the tundish, and 0.95% Elkem low-magnesium spheroidizing agent, 0.65% Elkem covering agent, 0.2% steel scrap and 0.1% slag remover are embedded in the spheroidizing bag, and the iron can be tapped directly to spheroidizing package. After the spheroidization is completed, the Elkem follow-up inoculant is sprinkled on the surface, completely smashed, and the sample is analyzed and tested with an EPIC instrument. Directly tap 500kg of iron to the tundish, and the spheroidizing bag is embedded with 1.2% Elkem nodulizer, 0.3% covering agent, 0.2% Elkem inoculant, 0.5% steel scrap and 0.1% slag remover, directly out Iron into the spheroidizing bag, and at the same time put 0.35% of Elkem inoculant.
After the spheroidization is completed, the Elkem follow-up inoculant is sprinkled on the surface, completely smashed, and the sample is analyzed and tested with an EPIC instrument. The third plan is the ratio of charge: 65% of pig iron, 35% of scrap; control of chemical composition:
C | Si | Mn | P | S | Cu | |
The first furnace | 3.8-4.0 | 1.1-1.4 | 0.1-0.25 | <0.05 | <0.02 |
The spheroidization inoculation treatment plan is adopted: 500kg of iron is directly tapped to the tundish, 1.2% Elkem low-magnesium spheroidizing agent, 0.8% covering agent and 0.1% slag remover are embedded in the spheroidizing bag, and iron is tapped directly to the spheroidizing bag. At the same time, 0.55% of Elkem inoculant was put into it. After the spheroidization process was completed, Elkem's flow-through inoculant was put on the inner surface of the bag, which was completely smashed, and the samples were analyzed and tested with EPIC instrument. Directly tap 500kg of iron to the tundish, embedded 1.2% Elkem low-magnesium spheroidizing agent, 0.8% Elkem covering agent, and 0.1% slag remover in the spheroidizing bag, directly tapping iron to the spheroidizing bag, and at the same time invest 0.55% Elkem inoculant. After the spheroidization is completed, the Elkem follow-up inoculant sprinkled on the surface is completely smashed, and the sample is analyzed and tested with an EPIC instrument. Directly tap 500kg of iron to the tundish, and pre-embed 1.2% Elkem low-magnesium spheroidizing agent, 0.3% covering agent, 0.2% Elkem inoculant and 0.1% slag remover in the spheroidizing bag, directly tapping iron to spheroidizing Package, while putting in 0.35% Elkem inoculant. After the spheroidization is completed, the Elkem inoculant sprinkled on the surface is completely smashed, and the sample is analyzed and tested with an EPIC instrument. Experimental detection methods and analysis methods The carbon and sulfur content of molten iron is detected by a carbon and sulfur detector, and the content of alloys such as P, Mn, and Cu is detected by a spectrum analyzer; the cooling curve of different chemical compositions in front of the furnace is detected by Elkem EPIC equipment. For example, LET (liquid phase transition temperature), CE (actual carbon equivalent), G1, G2, and G3 have different interval values. Test results and discussion Results and discussion of the first scheme:
C | Si | Mn | P | S | Cu | |
1-1 | 3.40 | 2.51 | 0.20 | <0.05 | 0.007 | 0.14 |
1-2 | 3.45 | 1.90 | 0.18 | <0.05 | 0.010 | 0.14 |
1-3 | 3.30 | 2.61 | 0.18 | <0.05 | 0.013 | 0.14 |
According to different processing methods, the detected EPIC images are as follows:
Curve 1: The curve of the first furnace original molten iron ash mouth sample
Curve 2: The result curve of the first furnace program A
Curve 3: the result curve of the first furnace scheme B curve 4: the result curve of the first furnace scheme C
- ①From curves 1 and 2, we can see that the LET value of the first furnace scheme A increases after the spheroidization process, indicating that its liquid phase The linear temperature increases, but the G1 interval is still relatively large at 34%, and the LET-ST graphite precipitation time is 115 seconds. Combined with its chemical composition, it is known that its carbon equivalent is the highest among the three solutions in the first furnace.
- ②From curves 1 and 3, we can see that the LET value increases from 1132 to 1146°C, the G1 interval is 36%, and the precipitation time of LET-ST graphite is 129 seconds. Combined with its chemical composition, we know that its carbon equivalent is the first The lowest of the three options in one furnace.
- ③From curves 1 and 4, we can see that when the LET value increases from 1132 to 1140, the G1 interval is 32%. The precipitation time of LET-ST graphite is 139 seconds, and its chemical composition carbon equivalent is the middle value among the three schemes of the first furnace.
- ④ The higher the LET value, the higher the hot metal nucleation potential, the lower the white-mouth tendency of castings under the same conditions, and the more graphite balls; the LET-ST value is the graphite precipitation time. In the process of producing thick and large parts, this value is generally required to be higher. The larger the better, it means that graphite is precipitated during the whole solidification process, which is beneficial to use the self-expansion effect of graphite to offset partial shrinkage; the G1 interval is the austenite precipitation interval of the molten iron. The larger the G1, the greater the tendency of iron shrinkage porosity. There are two aspects that affect the G1 value. On the one hand, it is the inoculation effect and nucleation ability of the molten iron, and on the other hand, the carbon equivalent of the molten iron. When the carbon equivalent is the same, the better the inoculation effect, the lower the G1 value, and the smaller the shrinkage tendency.
- ⑤ Therefore, it seems that in the first furnace after the treatment of molten iron, option C is the best, option B is the second, and option A is the worst.
Results and discussion of the second option
C | Si | Mn | P | S | Cu | |
2-1 | 3.70 | 2.36 | 0.18 | <0.05 | 0.007 | - |
2-2 | 3.66 | 2.39 | 0.19 | <0.05 | 0.005 | - |
2-3 | 3.46 | 2.65 | 0.18 | <0.05 | 0.005 | - |
According to different processing methods, the detected EPIC images are as follows:
Curve 5: The curve of the second furnace original molten iron ash mouth sample
Curve 6: The result curve of the second furnace program A
Curve 7: The result curve of the second furnace program B
Curve 8: The result curve of the second furnace program C
- ①It can be seen from curve 5 and curve 6 that the LET value is reduced from 1149 to 1141℃, the G1 interval is 20%, and the precipitation time of LET-ST graphite is 146 seconds. Combined with its chemical composition, it is known that its carbon equivalent is the second furnace. The highest of the three programs. After analysis, the lower LET value of the original molten iron ash hole curve was due to the addition of ferrosilicon and graphitizing recarburizer, which resulted in a strong instantaneous nucleation ability of molten iron.
- ②It can be seen from curve 5 and curve 7 that the LET value is reduced from 1149 to 1139℃, the G1 interval is 24%, and the precipitation time of LET-ST graphite is 146 seconds. Combined with its chemical composition, it is known that its carbon equivalent is the second furnace. The middle of the three programs. The reason for the decrease of LET is the same as above.
- ③It can be seen from curve 5 and curve 8 that the LET value is reduced from 1149 to 1138°C, the G1 interval is 33%, and the precipitation time of LET-ST graphite is 144 seconds. Combined with its chemical composition, it is known that its carbon equivalent is the second furnace. The lowest of the three options.
- ④In general, the second furnace plan A with the strongest nucleation ability has a higher LET value, the smallest shrinkage tendency is also the second furnace plan A, and the G1 value is the smallest. It shows that the increase of CE value can reduce the tendency of contraction and enhance the ability of nucleation.
Results and discussion of the third option
C | Si | Mn | P | S | Cu | |
3-1 | 3.72 | 2.36 | 0.24 | <0.05 | 0.008 | - |
3-2 | 3.76 | 2.45 | 0.24 | <0.05 | 0.009 | - |
3-3 | 3.78 | 2.37 | 0.24 | <0.05 | 0.008 | - |
Curve 9: the curve of the third furnace original molten iron ash mouth sample
Curve 10: The result curve of the third furnace program A
Curve 11: The result curve of the third furnace plan B
Curve 12: The result curve of the third furnace plan C
- ①From curve 9 and curve 10, it can be seen that the LET value is reduced from 1147 to 1145℃, the G1 value is 6%, LET-ST graphite The precipitation time is 172.8 seconds, combined with its chemical composition, it is known that its carbon equivalent is the lowest among the three schemes of the third furnace.
- ②It can be seen from curve 9 and curve 11 that the LET value decreases from 1147 to 1146°C, the G1 value is 10%, and the precipitation time of LET-ST graphite is 182.7 seconds. Combined with its chemical composition, it is known that its carbon equivalent is the third furnace. The highest of the three programs.
- ③It can be seen from curve 9 and curve 10 that the LET value is reduced from 1147 to 1146℃, the G1 value is 9%, and the precipitation time of LET-ST graphite is 194.4 seconds. Combined with its chemical composition, it is known that its carbon equivalent is the third furnace. The middle of the three programs.
- ④The overall G1 value of the third option is relatively low, indicating that the molten iron smelted by this option has the lowest tendency to shrink. Comprehensively speaking, the difference between the three ladle molten iron is not big. Relatively speaking, the third furnace option A has the best effect. The conclusion of the sample test is to use the appropriate carbon equivalent value to adjust the charge ratio through the molten iron of the first and second furnaces.
The LET value of the original molten iron of the second furnace is higher than that of the first furnace, and the G1 value is smaller than that of the first furnace. Through adjusting the charge ratio of the second and third furnaces, replacing pure low-manganese scrap with lump steel, the LET value is close, and the G1 value is significantly reduced after the recarburization. Therefore, increasing the carbon content can improve the nucleation ability of the original molten iron and reduce.
The shrinkage tendency has little change with the type of scrap. The proper spheroidizing inoculation treatment process is obtained by comparing the first furnace A plan with the B plan and the C plan. The factory's own spheroidizing agent and inoculant adopt the existing treatment method, and the shrinkage tendency and nucleation ability of the molten iron are better. Poor; According to the second furnace plan A, plan B and plan C, when the spheroidizing agent dosage is 1.2% and the inoculant dosage is 0.5, the treatment effect is the best, and the difference between pre-embedded and tapped input is not big; passed Comparing the third furnace schemes A, B, and C, there is no obvious difference in the effects of the three treatment schemes.
The cause of the change is the CE value of the original molten iron. In short, with high CE value (C3.7-3.9, Si2.1-2.4), using Elkem nodulizer inoculant, dosage of nodulizer 1.2%, Elkem inoculant 0.5% and flow inoculant can get high shape The molten iron with nuclear capability and low shrinkage tendency makes it easier to obtain ductile iron castings that meet the quality requirements. Application conclusions for production Use sample test conclusions for the production of ductile iron thick-walled parts. The plan is as follows: melting weight 20t, charge ratio pig iron 65%, scrap steel 35%, Elkem nodulizer 1.2%, Elkem inoculant 0.5%+with Flow inoculant, the original molten iron C3.7-3.9, Si2.2-2.5, Mn≤0.3, P≤0.05, S<0.02, for production, take the casting test bar attached to the casting for testing, and dissect and observe the casting body . After the dissection, the processing surface was inspected, and there was no graphite floating and shrinkage defects after processing, and the program was successful.
To Sum Up
- 1. Thick-walled ductile iron parts are difficult to control in the production of ductile iron. They have the characteristics of large wall thickness, slow cooling, containing Mg and other elements, and high shrinkage tendency. Defects and scrap during production are easy to occur, causing economic losses . Especially for castings of QT400-18AR grade, its performance requirements: tensile performance Rm≥390; yield strength Re≥240; elongation A≥18; average impact value KV2≥14, minimum impact value KV2≥11, and higher requirements.
- 2. Through the small sample process test, the pouring small sample test piece is tested for different chemical components and different spheroidization inoculation treatment methods. The Elkem equipment EPIC detects the shrinkage tendency of the molten iron, determines the appropriate chemical composition and the proper nodularization inoculation treatment method, and can obtain the molten iron with the smallest shrinkage tendency.
- 3. Apply the data obtained from the small sample process test to actual production to form a clear and stable production plan for the production of ductile iron thick-walled parts. Through inspection of the attached casting test bar and anatomical surface observation, it is determined that the plan is effective and the casting is produced. The quality is good and meets quality requirements.
Please keep the source and address of this article for reprinting: Three Kinds Of Smelting And Pouring Schemes For Ductile Iron
Minghe Die Casting Company are dedicated to manufacture and provide quality and high performance Casting Parts(metal die casting parts range mainly include Thin-Wall Die Casting,Hot Chamber Die Casting,Cold Chamber Die Casting),Round Service(Die Casting Service,Cnc Machining,Mold Making,Surface Treatment).Any custom Aluminum die casting, magnesium or Zamak/zinc die casting and other castings requirements are welcome to contact us.
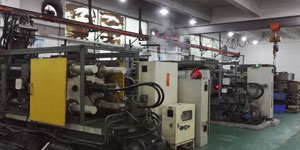
Under the control of ISO9001 and TS 16949,All processes are carried out through hundreds of advanced die casting machines, 5-axis machines, and other facilities, ranging from blasters to Ultra Sonic washing machines.Minghe not only has advanced equipment but also have professional team of experienced engineers,operators and inspectors to make the customer’s design come true.
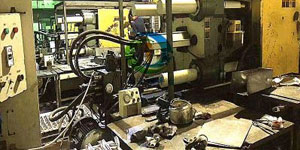
Contract manufacturer of die castings. Capabilities include cold chamber aluminum die casting parts from 0.15 lbs. to 6 lbs., quick change set up, and machining. Value-added services include polishing, vibrating, deburring, shot blasting, painting, plating, coating, assembly, and tooling. Materials worked with include alloys such as 360, 380, 383, and 413.
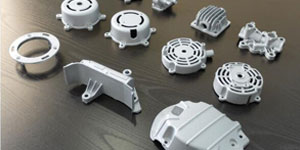
Zinc die casting design assistance/concurrent engineering services. Custom manufacturer of precision zinc die castings. Miniature castings, high pressure die castings, multi-slide mold castings, conventional mold castings, unit die and independent die castings and cavity sealed castings can be manufactured. Castings can be manufactured in lengths and widths up to 24 in. in +/-0.0005 in. tolerance.
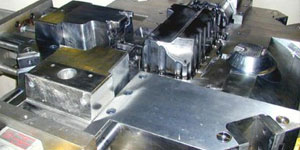
ISO 9001: 2015 certified manufacturer of die cast magnesium, Capabilities include high-pressure magnesium die casting up to 200 ton hot chamber & 3000 ton cold chamber, tooling design, polishing, molding, machining, powder & liquid painting, full QA with CMM capabilities, assembly, packaging & delivery.
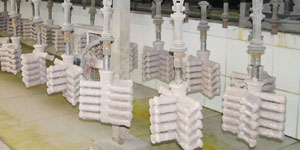
ITAF16949 certified. Additional Casting Service Include investment casting,sand casting,Gravity Casting, Lost Foam Casting,Centrifugal Casting,Vacuum Casting,Permanent Mold Casting,.Capabilities include EDI, engineering assistance, solid modeling and secondary processing.
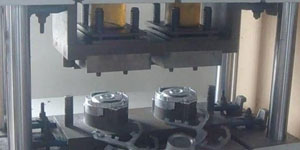
Casting Industries Parts Case Studies for: Cars, Bikes, Aircraft, Musical instruments, Watercraft, Optical devices, Sensors, Models, Electronic devices, Enclosures, Clocks, Machinery, Engines, Furniture, Jewelry, Jigs, Telecom, Lighting, Medical devices, Photographic devices, Robots, Sculptures, Sound equipment, Sporting equipment, Tooling, Toys and more.
What Can we help you do next?
∇ Go To Homepage For Die Casting China
→Casting Parts-Find out what we have done.
→Ralated Tips About Die Casting Services
By Minghe Die Casting Manufacturer |Categories: Helpful Articles |Material Tags: Aluminum Casting, Zinc Casting, Magnesium Casting, Titanium Casting, Stainless Steel Casting, Brass Casting,Bronze Casting,Casting Video,Company History,Aluminum Die Casting |Comments Off