Three Measures To Overcome Aluminum Alloy Surface Cracks
In production and life, cracks often appear on the surface of aluminum alloys. The key to this problem is to consider three main links: 1 is the control of the chemical composition of the alloy variety. 2 is the casting process of alloy varieties. 3 is the operation skills and natural conditions.
The mold of aluminum alloy is also called the condensing tank, which plays a decisive role in casting. The change of the taper of the aluminum alloy mold is not negligible for casting. When the mold cone is too large, the segregation tumors on the surface of the slab will increase. Once the operation is not good, slag inclusion will cause surface cracks. When the mold is too narrow, surface cracks will occur when the slab is cast. A good casting master will adjust the size of the mold at any time to prevent surface cracks in the slab during casting.
The surface cracks of aluminum alloy slabs are crucial to the cooling water. Whether the cooling water is evenly distributed, the strength of the large surface and the small surface, the size of the water pressure, and the water temperature have a very large impact on the solid-liquid area.
In short, the surface cracks of aluminum alloy slabs are one of the common defects in the melting and casting process. Eight kinds of analysis reasons should be paid attention to in the melting and casting process. Ignoring every detail will cause mistakes, resulting in losses and waste. Alloy composition, impurity control issues and process settings need to be studied and analyzed according to different environments, and accurate judgments can be made. For example, slag inclusion on the surface of aluminum alloy slabs is the most common cause of surface cracks in the casting operation. Most of them are caused by improper operation, such as the control of furnace temperature-water pressure-speed-whether the horn of the flow plate is flat-the level of the crystallizer liquid level-operation, etc., exist in every detail. In order to prevent the occurrence of surface cracks of aluminum alloy slabs. This is true from semi-continuous casting to fully automatic casting. For example, the internal quality defects of fully automatic casting are a new issue. For example: Feather-shaped crystals, columnar crystals, vertical tree-shaped, bright crystal columns, etc. to produce and prevent.
Please keep the source and address of this article for reprinting:Three measures to overcome aluminum alloy surface cracks
Minghe Die Casting Company are dedicated to manufacture and provide quality and high performance Casting Parts(metal die casting parts range mainly include Thin-Wall Die Casting,Hot Chamber Die Casting,Cold Chamber Die Casting),Round Service(Die Casting Service,Cnc Machining,Mold Making,Surface Treatment).Any custom Aluminum die casting, magnesium or Zamak/zinc die casting and other castings requirements are welcome to contact us.
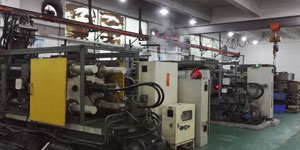
Under the control of ISO9001 and TS 16949,All processes are carried out through hundreds of advanced die casting machines, 5-axis machines, and other facilities, ranging from blasters to Ultra Sonic washing machines.Minghe not only has advanced equipment but also have professional team of experienced engineers,operators and inspectors to make the customer’s design come true.
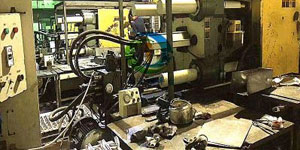
Contract manufacturer of die castings. Capabilities include cold chamber aluminum die casting parts from 0.15 lbs. to 6 lbs., quick change set up, and machining. Value-added services include polishing, vibrating, deburring, shot blasting, painting, plating, coating, assembly, and tooling. Materials worked with include alloys such as 360, 380, 383, and 413.
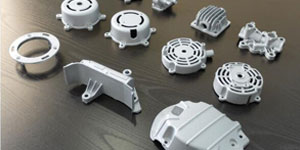
Zinc die casting design assistance/concurrent engineering services. Custom manufacturer of precision zinc die castings. Miniature castings, high pressure die castings, multi-slide mold castings, conventional mold castings, unit die and independent die castings and cavity sealed castings can be manufactured. Castings can be manufactured in lengths and widths up to 24 in. in +/-0.0005 in. tolerance.
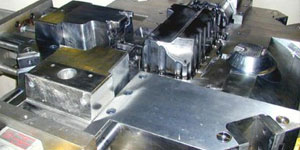
ISO 9001: 2015 certified manufacturer of die cast magnesium, Capabilities include high-pressure magnesium die casting up to 200 ton hot chamber & 3000 ton cold chamber, tooling design, polishing, molding, machining, powder & liquid painting, full QA with CMM capabilities, assembly, packaging & delivery.
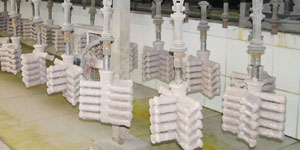
ITAF16949 certified. Additional Casting Service Include investment casting,sand casting,Gravity Casting, Lost Foam Casting,Centrifugal Casting,Vacuum Casting,Permanent Mold Casting,.Capabilities include EDI, engineering assistance, solid modeling and secondary processing.
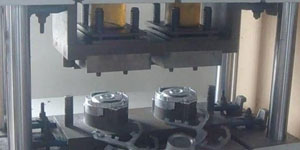
Casting Industries Parts Case Studies for: Cars, Bikes, Aircraft, Musical instruments, Watercraft, Optical devices, Sensors, Models, Electronic devices, Enclosures, Clocks, Machinery, Engines, Furniture, Jewelry, Jigs, Telecom, Lighting, Medical devices, Photographic devices, Robots, Sculptures, Sound equipment, Sporting equipment, Tooling, Toys and more.
What Can we help you do next?
∇ Go To Homepage For Die Casting China
→Casting Parts-Find out what we have done.
→Ralated Tips About Die Casting Services
By Minghe Die Casting Manufacturer |Categories: Helpful Articles |Material Tags: Aluminum Casting, Zinc Casting, Magnesium Casting, Titanium Casting, Stainless Steel Casting, Brass Casting,Bronze Casting,Casting Video,Company History,Aluminum Die Casting |Comments Off