Use And Maintenance Of Agricultural Water Pumps
Agricultural water pumps are widely used. How to properly use and maintain agricultural water pumps is essential for irrigation, drainage, and the normal operation and life of the pumps.
Installation of water pump
The installation and calibration of the water pump is the critical first step. Although the water pump unit has been calibrated before leaving the factory, it will cause varying degrees of deformation or looseness due to transportation and assembly. Therefore, the water pump must be installed while installing. Correction.
1. Installation steps
- Remove greasy and dirt on the base, and place the base on the foundation.
- Use a spirit level to check the level of the base.
- Use cement to pour the base and anchor bolt holes.
- After the cement dries up, check whether the holes of the base and anchor bolts are loose, tighten the anchor bolts appropriately, and recheck the levelness.
- Clean the support plane of the base, the plane of the feet of the water pump and the feet of the motor, and install the water pump and the motor on the base.
- Check and adjust the coincidence degree of the axis line of the water pump and the motor, check whether the axis of the water pump is consistent with the center line of the motor shaft, and the difference between the outer circle of the two couplings should not exceed 0.1 mm. The gap between the end faces of the two couplings is 2-3 mm.
2. Precautions for water pump installation
- The actual suction lift of the pump must be lower than the allowable suction lift of the pump.
- The inlet pipe of the water pump should be as short and straight as possible, and it should not bulge upward or higher than the water pump on the horizontal line to avoid the increase of cavitation and the reduction of efficiency during the operation of the water pump.
- The outlet pipe of the water pump should be appropriately enlarged and should be as close to the water surface as possible, too high or too low will increase power consumption. Larger pipe diameter should be used for long-distance transportation. The piping of the water pump should have a special bracket. The weight of the piping is not allowed to be added to the water pump to avoid crushing the water pump.
- The distance between the bottom valve of the water pump or the inlet of the water inlet pipe from the bottom of the water source and the edge of the water source shall not be less than the diameter of the inlet pipe, and the water inlet depth of the inlet pipe shall not be less than 0.5 meters. When installing more than two water pumps, the distance between the bottom valve or water inlet pipe port shall not be less than twice the outer diameter of the bottom valve or water inlet pipe port.
- The check valve of the discharge pipeline should be installed outside the gate valve, and the check valve should be installed for the pump head above 20 meters.
- The diameter of the pulley should be determined according to the calculation of the speed. When calculating the diameter of the pulley according to the formula, the factor of belt slip should be considered, and the calculated value should be adjusted appropriately.
Starting, running and stopping of the water pump
The starting, running and stopping of the water pump should be carried out in strict accordance with the operating regulations.
1. Start
- When the water pump is started, it should be determined whether the rotation direction of the motor is correct and whether the rotation of the pump is flexible before connecting the pump.
- Close the gate valve on the discharge pipeline.
- Fill the pump with water, or use a vacuum pump to divert water.
- Turn on the power supply. When the pump reaches the normal speed, gradually open the gate valve on the discharge pipeline to adjust to the required working condition. When the gate valve on the spit line is closed, the pump should not work continuously for more than 3 minutes.
2. Operation
- In the process of starting up and running, you must pay attention to observe the meter readings, whether the bearing temperature rises and heats, the filler leaks, and the pump vibration and noise are normal. If abnormal conditions are found, they should be dealt with in time.
- The bearing temperature must not exceed 80 degrees Celsius, or the ambient temperature must not exceed 40 degrees Celsius.
- The filling is normal, and the leakage should be small and even.
- When lubricating with engine oil, the bearing oil level should be kept at the normal position, not too high or too low. If it is too low, the lubricating oil should be added in time. For grease lubrication, the new water pump should be changed after 300 hours of operation, and every 1500 hours of operation thereafter. When the ambient temperature is below 0 degrees Celsius, it is suitable for oil lubrication; when the ambient temperature is above 0 degrees Celsius, it is suitable for grease lubrication.
3. Stop
Turn off the power after gradually closing the gate valve of the discharge line.
Third, the maintenance and maintenance of the water pump
In addition to using the pump strictly in accordance with the installation and operation instructions, two points should be noted: one is to avoid relying only on "experience". For example, when the bottom valve of the water pump leaks, some operators try to save trouble. Before each startup, fill some dry soil into the inlet nozzle, and then flush the soil to the bottom valve to prevent the bottom valve from leaking. This method looks simple and easy to implement, but it is not desirable. Because when the water pump starts to work, the sand and soil in the bottom valve will enter the pump with the water, which will wear the impeller, pump casing and shaft, which will seriously affect the service life. The correct method should be to overhaul the bottom valve. Replace in time. The second is to eliminate the fault in time and avoid letting the unit work "ill". For example, when the water pump shaft packing is found to be worn seriously, it is necessary to increase the packing in time, otherwise it will cause the water pump shaft packing to leak air. Leakage of the water pump shaft packing not only causes excessive energy consumption of the unit, but also causes cavitation, which accelerates the damage of the impeller and directly affects the service life of the water pump. For another example, if the water pump is found to vibrate severely, it should be shut down immediately for inspection. If the water pump shaft is bent and deformed, a safety accident is likely to occur.
After the pump unit and pipeline have been used for a period of time, the following maintenance work should be done:
- Drain the remaining water in the pump and pipeline.
- If the disassembly is convenient, the pump and pipeline can be disassembled and cleaned up.
- Check the ball bearings, if the inner and outer sleeves are worn, stray, the balls are worn, or there are spots on the surface, they must be replaced. Use gasoline or kerosene to clean the bearings and grease them for storage.
- Check whether there are cracks or small holes on the impeller, whether the fixing nut of the impeller is loose, repair or replace if damaged. Check the clearance at the wear-reducing ring of the impeller. If it exceeds the specified value, repair or replace it.
- When the pump and pipeline are not disassembled, the outlet should be sealed with a cover plate to prevent debris from entering.
- When the transmission tape is not in use, it should be removed, cleaned and dried with warm water, and stored in a place not exposed to direct sunlight, nor should it be stored in a place with oil stains, corrosives and smoke. Under no circumstances should the tape be stained with oils such as engine oil, diesel or gasoline, and do not apply rosin or other viscous materials to the tape. Before the tape is used, the white powder on the contact surface of the tape must be removed.
- Clean all screws and bolts with a steel wire brush, and coat them with engine oil or immerse them in diesel oil for storage.
Please keep the source and address of this article for reprinting:Use And Maintenance Of Agricultural Water Pumps
Minghe Die Casting Company are dedicated to manufacture and provide quality and high performance Casting Parts(metal die casting parts range mainly include Thin-Wall Die Casting,Hot Chamber Die Casting,Cold Chamber Die Casting),Round Service(Die Casting Service,Cnc Machining,Mold Making,Surface Treatment).Any custom Aluminum die casting, magnesium or Zamak/zinc die casting and other castings requirements are welcome to contact us.
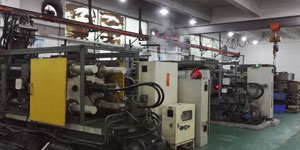
Under the control of ISO9001 and TS 16949,All processes are carried out through hundreds of advanced die casting machines, 5-axis machines, and other facilities, ranging from blasters to Ultra Sonic washing machines.Minghe not only has advanced equipment but also have professional team of experienced engineers,operators and inspectors to make the customer’s design come true.
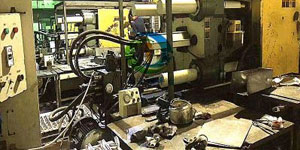
Contract manufacturer of die castings. Capabilities include cold chamber aluminum die casting parts from 0.15 lbs. to 6 lbs., quick change set up, and machining. Value-added services include polishing, vibrating, deburring, shot blasting, painting, plating, coating, assembly, and tooling. Materials worked with include alloys such as 360, 380, 383, and 413.
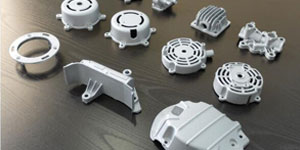
Zinc die casting design assistance/concurrent engineering services. Custom manufacturer of precision zinc die castings. Miniature castings, high pressure die castings, multi-slide mold castings, conventional mold castings, unit die and independent die castings and cavity sealed castings can be manufactured. Castings can be manufactured in lengths and widths up to 24 in. in +/-0.0005 in. tolerance.
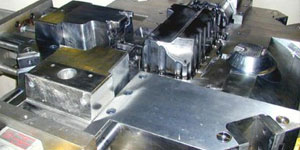
ISO 9001: 2015 certified manufacturer of die cast magnesium, Capabilities include high-pressure magnesium die casting up to 200 ton hot chamber & 3000 ton cold chamber, tooling design, polishing, molding, machining, powder & liquid painting, full QA with CMM capabilities, assembly, packaging & delivery.
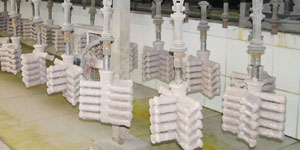
ITAF16949 certified. Additional Casting Service Include investment casting,sand casting,Gravity Casting, Lost Foam Casting,Centrifugal Casting,Vacuum Casting,Permanent Mold Casting,.Capabilities include EDI, engineering assistance, solid modeling and secondary processing.
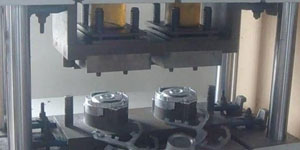
Casting Industries Parts Case Studies for: Cars, Bikes, Aircraft, Musical instruments, Watercraft, Optical devices, Sensors, Models, Electronic devices, Enclosures, Clocks, Machinery, Engines, Furniture, Jewelry, Jigs, Telecom, Lighting, Medical devices, Photographic devices, Robots, Sculptures, Sound equipment, Sporting equipment, Tooling, Toys and more.
What Can we help you do next?
∇ Go To Homepage For Die Casting China
→Casting Parts-Find out what we have done.
→Ralated Tips About Die Casting Services
By Minghe Die Casting Manufacturer |Categories: Helpful Articles |Material Tags: Aluminum Casting, Zinc Casting, Magnesium Casting, Titanium Casting, Stainless Steel Casting, Brass Casting,Bronze Casting,Casting Video,Company History,Aluminum Die Casting |Comments Off